New Works at
Wolverhampton
London has now lost practically all the large
engineering works it once had. One by one they
have been transferred to the Midlands, the North
of England, Scotland, and other parts of the
United Kingdom where better facilities for the
metal working industry are to be found. Although
this process of removal has been going on for
years, firms are still taking their departure;
but it seems that the time cannot be far distant
when none but very small works will remain. In
common with many other manufacturing firms,
Chubb and Son's Lock and Safe Company has been
compelled to consider the best means for
providing for a larger output. The company's
present chief works for safe making are in
Camberwell. S.E., but seven years ago as an
experiment, the firm opened a small branch works
alongside its lock works in Wolverhampton, the
object being to test the facilities and the
relative cost of manufacture in London and in
Wolverhampton. In addition to initiating this
practical test, they carefully considered the
relative advantages of ultimately establishing
larger works at other manufacturing centres or
in some country district.
The outcome of all the firm's inquiries and
of the practical experiment with the temporary
overflow works at Wolverhampton is that the
directors came to the conclusion that
Wolverhampton was undoubtedly the most suitable
place for carrying out the firm's manufactures.
They also believed it to be one of the most
convenient places for workmen to obtain
excellent and cheap housing. In consequence the
company has purchased a freehold plot of land,
10 acres in extent, situated on the Wednesfield
Road., just inside the borders of the borough of
Wolverhampton, and within a few minutes of the
goods stations of the London and North Western,
Great Western, and Midland railways. On this
site fine new works have been erected, and they
were formally opened by the Lord Mayor of London
yesterday. Not only are these works close to
many houses and cottages suitable for the
workmen, but within a short distance a large
garden suburb is being planned, and upon this it
will be possible for the men to obtain or lease
modern cottages of an exceptionally good type
and at a reasonable cost.
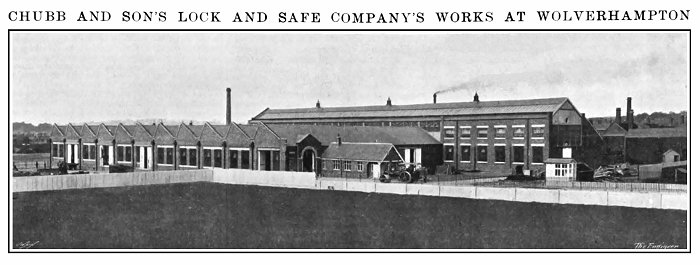
Before entering upon a description of these
new works a few remarks relating to the history
of the firm may prove of interest. The business
now carried on under the name of Chubb and Son's
Lock and Safe Company was commenced in the year
1818, when Mr. Charles Chubb, aided by his
brother, Mr. .Jeremiah Chubb, invented the Chubb
detector lock. From that date to the present
time, although alterations have been made in the
form and arrangement of the lock, the principles
remain the same, and the firm claims that no key
lock has since been invented which can
successfully compete with it for security.
After the death of Mr. Charles Chubb in 1846,
the business was carried on by his son and
partner, Mr. John Chubb, till the year 1872,
when, upon his death his sons succeeded him as
sole partners until the concern was converted
into a private limited company in the year 1882,
since which time it has been chiefly owned and
entirely managed by members of the family in
conjunction with a board of directors. When the
business was started it was confined to the
making of locks, later on the manufacture of
safes, strong rooms, and safe deposits was taken
up, and at the present time, this latter branch
of the business has grown to very large
dimensions.
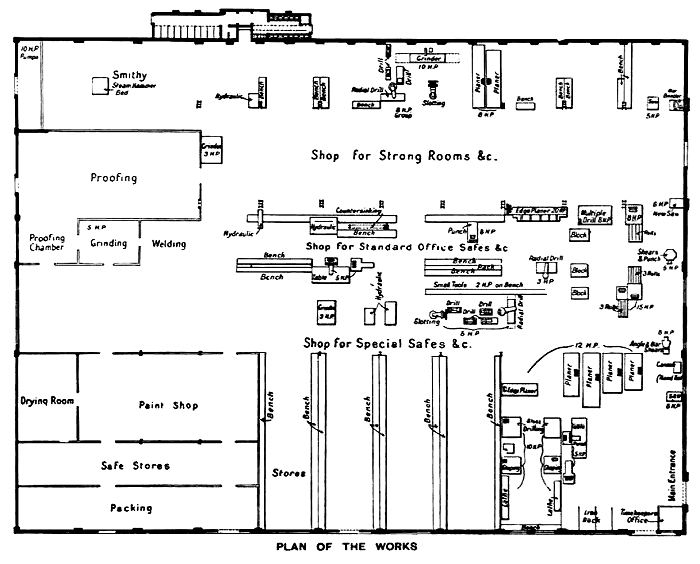
The foundation stone of the
new factory opened last Thursday was laid by Sir
George Hayter Chubb, on the 8th July, 1908. The
works, which are shown here cover an area of
63,500 square feet, and as will be gathered from
the plan, a good portion of this area is set
aside for erecting purposes. The plan, although
not quite correct as regards the arrangement of
some of the machinery, will serve to show the
general layout and the methods the firm has
adopted for turning out its manufactures. The
large erecting shop at the back of the centre
line of machine tools is set aside for the
construction of steel strong rooms, treasuries,
and safe deposits; it is 850 feet long and 40
feet wide, with a height of 38 feet clear of all
girders and roof principals. The height of the
remainder of the factory is from 16 feet to 14
feet at the lowest point. One inaccuracy in the
plan to which attention should be called is that
this large shop just referred to, has been
extended 75 feet to the right of the other part
of the works, as can be seen from the
illustration of the exterior of the works.
Nearly the whole area is undivided by parting
walls, and the general design of the buildings
gives the maximum amount of light, avoiding as
much as possible direct sun rays. Careful
consideration has also been given to the
question of sanitation and ventilation.
The centre part of the
works where the greater number of the machine
tools are situated is where the ordinary office
safes will be constructed. There are twenty five
standard sizes of these safes, and there are
also many intermediate patterns which are fitted
up to meet various requirements. The firm's
object in designing these works has been to
arrange the machines, so that as the work passes
from one tool to another, the material which
entered the door at one end gradually assumes
the form of finished articles and ultimately
leaves at the opposite end of the building,
without during the course of manufacture, having
travelled very far out of a straight line. The
part of the building shown on the lower part of
the plan has been set aside for special safe
work, and it is here where the plan is again a
little incorrect, the final arrangement being to
erect some of the machine tools shown in the
right hand bottom comer of the plan in the
spaces between the second and last row of
benches counting from the left. The benches also
run in the opposite direction to that shown in
the drawing. The group of machine tools marked 5
H.P. will also be erected in the space between
the second and last row of benches. Now, turning
to the centre row of machine tools, which are
already erected, and upon which, as previously
stated, the twenty five standard sizes of office
safes will be manufactured, the first machine
met with on the right is a plate roll by Craig
and Donald, of Johnston.
Two sets of rolls are shown
in the drawing, but up to the present only one
of these has been put down. Here the plates are
first rolled, and they are afterwards passed on
to the blocks where the flattening process is
completed by hammering. These levelling blocks,
only one of which has so far been erected, are
made of armour plate from the original and now
obsolete Dreadnought. The flattening of these
plates is an art to which safemakers attach some
importance and pride.
Having been flattened, the
plates are then passed on to a large edge planer
by J. Buckton and Company of Leeds. The work is
held down on this and other machines
hydraulically, thus saving an enormous amount of
time. Next to this edge planing machine there is
a heavy punching machine by W. Smith and Company
of Glasgow, on which the necessary holes in the
thick plates are punched. Then in the same line
of machine tools we come to a very handy machine
for counter sinking holes, which has been
supplied by John Hetherington and Sons, Limited,
of Manchester. The drill carriage can be run
along in a straight line, and the holes in the
various parts used in the construction of these
safes can consequently be countersunk with great
rapidity.
A point to which attention
should be directed is that a centre punch or a
foot rule are never used in the manufacture of
the company's standard safes. When a man
commences a drilling job, for example, he has
handed out to him from the stores the necessary
jigs and an instruction sheet, and in this way
marking off work is entirely dispensed with. The
last operation performed on the heavy plates, by
means of the machines in the centre of the
building, is that of bending, this being carried
out by means of two hydraulic presses shown at
the left of the row of tools which have just
been considered. The larger of these presses,
which is used for the longitudinal bending, is
by Hugh Smith and Company Limited, of Possil
Park, Glasgow, whilst the smaller is by Hollings
and Guest Limited, of Birmingham. It should be
mentioned that above all these machines, in the
centre of the building, there is a mono-rail,
and in addition, as can be seen from the plan,
there are special roller benches at the sides of
these machines, so that the operation of
conveying heavy plates from one tool to another
and placing the work in position is considerably
simplified, and this, together with the close
proximity of one tool to another, should be the
means of saving much time. The roller benches
are arranged to support the work whilst the
punching or drilling or whatever other operation
is being performed is in progress.
It will be seen from the
plan that the welding department is directly
opposite the line of machines just dealt with,
and that the safes can be lifted by a travelling
crane into this department. The welding at these
new works is to be carried out by the
oxy-acetylene method, an acetylene gas
generator, together with the other necessary
equipment having been supplied by the British
Oxygen Company, of Westminster. The gas
generator is in a well ventilated house
adjoining the main building. The ordinary system
of welding is used at Camberwell, but in this
new factory an endeavour has been made to take
full advantage of everything modem, and the
oxy-acetylene system has consequently been
adopted, and it is possible, we understand, that
this process will ultimately be employed for
cutting.
When the welding process
has been completed the next operation consists
of grinding off the rough parts so as to give
the safes a perfectly smooth surface. This
operation, as will be gathered from the plan, is
performed in the apartment next to that in which
the welding process is carried out. Here a
special grinding machine has been erected, with
which all the rough parts set up in welding are
removed. This grinding machine has been
constructed by John Holroyd and Company, of
Milnrow, near Rochdale. It consists of a long
vertical column and an overhanging arm similar
to that of a radial drilling machine. This arm
carries a revolving emery wheel mounted at an
angle, by means of which the rough places on the
safes are removed. The arm carrying the emery
wheel can be raised or lowered over a wide range
in order that work of various dimensions may be
dealt with. The machine is driven by means of a
vertical motor fixed at the top. The proofing
chamber in which the proofing material is
inserted between the inner and outer cases
adjoins the grinding department. From the
proofing shop the safes pass into the paint shop
and the drying room, and finally into the stores
or packing department, depending upon whether
they are to be dispatched or kept in stock.
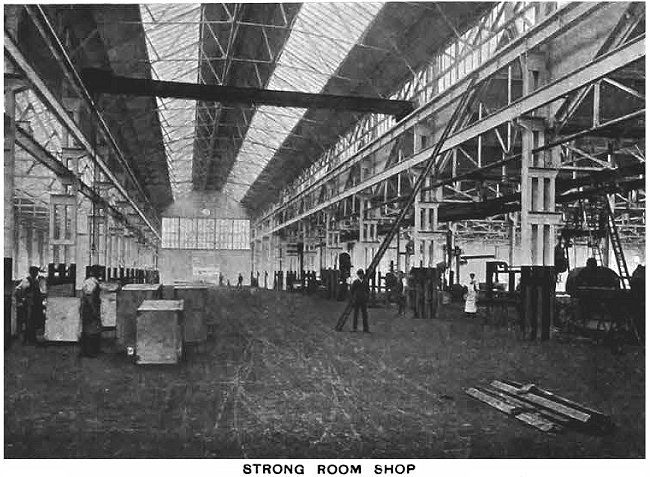
There is, of course, a
considerable amount of comparatively light work
in connection with the fittings and lining of
these safes, and for punching, drilling, and
cutting the lighter parts there is a number of
smaller machines at the side of the line of
heavy tools previously referred to and shown on
the plan. There are small drilling machines, a
punching machine by Bliss and Company, shears, a
circular saw, and a fine radial drilling
machine, the arm of which revolves on ball
bearings. This latter tool has been supplied by
W. Asquith, Limited, of Halifax. It should be
mentioned that nearly all those machines shown
on the centre of the plan are at present
erected, whilst some of those shown at the top
and bottom of the plan will be put up later. The
smiths' shop was also in a rather unfinished
condition when we visited these works a few days
ago. Ultimately it will contain five hearths,
which are all being put in by James Keith and
Blackman and Company Limited, who are also
supplying the blower.
We may remark here that an
entirely new departure in the construction of
safes is being undertaken which embodies all the
best known principles, such as heavy 12 bend
bodies with welded corners, asbestos inner
doors, and inner and outer doors of new design
built on the external lock case principle.
A vertical boiler has been erected in the
smiths' shop for supplying steam for heating the
drying room. The hydraulic pumps and accumulator
are also erected in this shop. The pumps have
been supplied by Hugh Smith and Company of
Glasgow. There is also an electro pneumatic
hammer by B. and S. Massey, of Manchester. It is
in this shop that the hardening is to be carried
out. A double furnace for hardening two large
plates at once for strong- rooms will be
provided, and electric instruments for measuring
the temperature so as to ensure the plates are
not being overheated. The plates are heated to a
cherry red and then plunged into a tank of water
through which a continuous supply of cold water
flows. Although it may appear from the
illustration showing the exterior of the works
that a power plant has been put down for driving
the machinery owing to the presence of the tall
shaft in the background, this is nevertheless
not the case, the shaft in question belonging to
the works of J. Evans and Son, which are in
close proximity.
The whole of the machinery
in Chubb's new works is driven by three phase
induction motors, all of which are of the
squirrel cage type. Three phase current is taken
from the Corporation mains at a pressure of
5,000 volts. It is transformed down to 400
volts, and the current at this pressure is
supplied to thirty motors of various sizes
ranging from 2½ to 20 horsepower. Naturally,
each large machine has its own motor, whilst the
smaller tools derive their power from shafting,
one motor thus supplying power to a number of
the smaller tools. The whole of the motors have
been supplied and erected by the British
Westinghouse Company, of Trafford Park,
Manchester. They are all of the open type, and
many are mounted direct on the machines which
they drive, the power being transmitted direct
without the use of chains or belts. Many of the
starting switches are mounted on the walls, and
in the case of the large motors the starting
current is limited by means of the star to mesh
connection. In the case of the small motors,
however, simple resistances are used for
starting. The type of switchgear used is simple
and strong, and admirably adapted for workshop
use. In many instances ammeters are fixed to the
starting switch, and enable the operator to see
how much current the motor is taking, and so to
judge when the change from the star to mesh
connection should be made. The wiring is also
admirably suitable for workshop use, armoured
cables being employed. Usually, where electric
power is available, workshops are lighted by
means of arc lamps, but in this instance Osram
lamps have taken their place. Lamps of 100
candle power are used, and are suspended by
flexible wires in the usual manner. Additional
lamps, we understand, are to be provided on
those machines where a good local light is
needed. The periodicity at Wolverhampton is 50.
For lifting the plates in
the large shop where the strong rooms are to be
manufactured, a travelling magnetic crane is to
be erected. Alternating current for a magnetic
crane is, of course, quite unsuitable, and to
overcome this difficulty a continuous current
dynamo is to be driven from the shafting. This
will charge a storage battery so that continuous
current for use on the crane will always be
available.
A small block of temporary
offices has been provided, adjoining the main
factory, and a foreman's cottage is in course of
construction. The protecting fences and walls
enclose an area of about 20,300 square yards.
The approach from the Wednesfield Road is by a
wide private cart road. A large piece of land is
retained at the back of the factory for future
extensions, to which additional access has been
provided from the Woden Road. In the meantime it
has been placed at the disposal of workmen and
others for sports. A bowling green has also been
laid down.
The whole of the factory
buildings have been designed on lines carefully
thought out by the present directors and
successfully carried out by their architect, Mr.
G. Gordon Stranham, of Bush Lane, Cannon Street,
London, E.C. Mr. C. H. M. Mileham, of Lincoln's
Inn Fields, has acted with him as consulting
architect, and Mr. F. T. Beck, of Wolverhampton,
as local superintending architect. Mr. F.
Simpson was the general clerk of the works. The
contract for the buildings was placed in the
hands of Henry Lovatt, Limited, of
Wolverhampton. The steel construction is by
Drew, Bear, Perks and Company, of London. The
consulting electrical engineers were the British
Engine, Boiler and Electrical Insurance Company,
Limited, of Manchester. |