Shearing and
Bluing
As well as producing the new tack machines,
the Lloyd brothers also commissioned a new shearing machine,
purchased in 1934 from Rhodes of Birmingham. They also installed
the tack bluing machine.
|
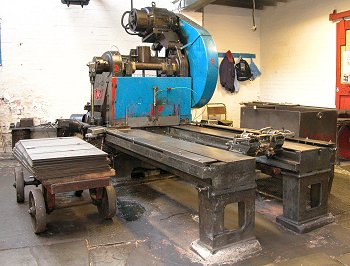
One of the two automatic shearing
machines. |
In the Lloyd’s day the sheet steel was purchased
in what were called “randoms”. Individual pieces of steel were
of different shapes and sizes, inaccurate thicknesses and of
spurious quality. The steel was delivered from the railway
station by a three wheeled Scammell “Scarab” lorry. Every piece
had to be unloaded by hand, placed onto a large hand truck and
taken into the store. Each piece had to be hand trimmed to
suitable sizes that would fit the shearing machine. For many
years this was carried out by warehouseman, Arthur Johnson. |
He didn’t measure the sheets with a ruler for
trimming he just used a 26 inch long piece of steel.
The metal was placed in one of the shearing machines and cut
into the strips that were later fed into the tack and nail
machines. The width of each strip was equal to the length of the
tack or nail, plus the length of the material required to form
the head. A half inch tack needs an extra one eighth of an inch
for the head and so the strip would be five eighths of an inch
wide. |
When the steel was cut, the width of each strip
was governed by a “rack”, a length of steel that had grooves cut
into it. The grooves were separated by the width of the strip
being cut. They were used as a guide to advance the steel sheet
before each cut was made.
The width of the strips varied from about three eighths of
an inch to two inches, in increments of one sixteenth of an
inch, as governed by the American Market.
The racks were clearly marked and stored in a holder that was
mounted on the wall and could rapidly be changed. |
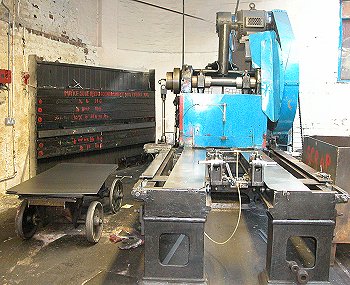
Steel sheets ready to be loaded onto the
second shearing machine. On the left is the holder for the
racks. |
After cutting, the strips were loaded into kegs
which weighed between 150 and 200 kilos. These would be loaded
on a truck and taken to the operator as required. |
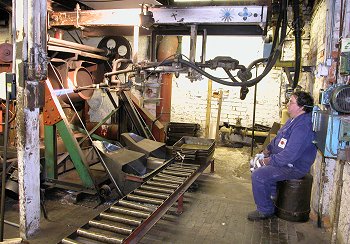
Kevin Farrington operating the tack bluing
machine. |
After the tacks were made they went to be blued.
Bluing of the tacks was necessary because when the head was
cold formed in the machine, it would sometimes crystallise. When
such a tack is knocked into wood the head will sometimes break
off. To eliminate this the tacks were originally annealed in a
furnace by heating to a dull red. When they came out they were
blue in colour, hence the name. |
Today with modern materials crystallisation does
not occur and so the bluing process is purely cosmetic, although
it does help to prevent rust.
People expect to buy blued tacks and so that’s how they are
provided. Because it is no longer necessary to anneal the tacks
they are simply tipped into a rotating barrel and heated with a
gas flame.
The bluing machine that was used until the end of production
was designed by Cyril Haydon. Cyril was a good engineer and
extremely devoted to the company. He often took work home with
him in the evenings where he would work out new designs and
solve problems.
|
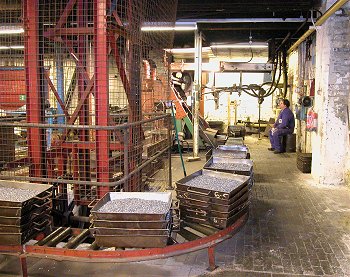
Another view of the bluing machine. On the
left is the elevator that carries pans of blued tacks to the
warehouse to be cooled, weighed and packed. In the foreground
are pans full of tacks ready to be blued. |
After bluing, the tacks were put into pans
to cool, after which they were weighed and packed. Today
cardboard cartons and boxes are used, but originally they were
put into hessian sacks, each one weighing 28lbs. These were
extremely dangerous to handle because some of the tacks would
inevitably stick out of the sides. As the tacks were extremely
sharp, great care was needed when carrying them.
Until the second world war the canal was still used to
transport tacks. Many were loaded onto barges and taken down to
London. This practice was overtaken by road transport and the
canal basin was eventually filled-in, around 1960. |
|
|
 |
|
|
Return to
Early Years |
|
Return to
the Contents |
|
Proceed to
Rationalisation |
|