The Wolverhampton Die Casting
Company Limited was formed in 1919 at a small factory in Great Hampton Street. The
company rapidly leapt to the forefront of the industry
to become the largest pressure die casting organisation
in Europe. By the 1950s over one hundred and fifty
million zinc and aluminium alloy pressure die castings
were produced each year, for over 700 customers in 30
different industries. Castings were produced to very
fine limits to eliminate practically all machining. |
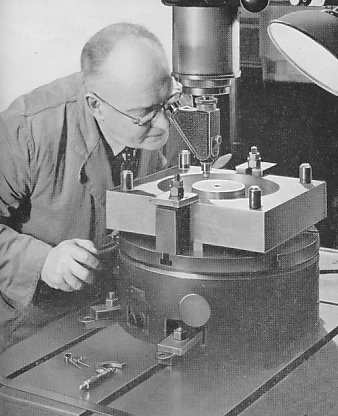 |
A diesinker at work.
The dies were constructed from
solid forged blanks of special die steel, and in much of
the work, particularly in the case of a delicate and
detailed job, the skill of the hands of the diesinker
cannot be over-estimated.
In many cases even the most
modern machinery cannot perform the intricacies
required. |
In February 1934 the company
acquired part of the A.J.S. site at Graiseley Hill, on
which to build a new factory, in order to expand
production.
Success continued, and further
expansion followed. The ‘Hollies Works’ was built on the
other side of Graiseley Hill, and a factory was acquired
at Ludlow. The total factory floor space now amounted to
nearly 400,000 square feet.
In 1950 an affiliation began with
the Precision Castings Co. Inc. of Fayetteville, New
York, the largest pressure die casting organisation in
the United States, which operated from nine separate
factories.
The association between the two
companies enabled them to keep up-to-date with the
latest technical advances in each country. |
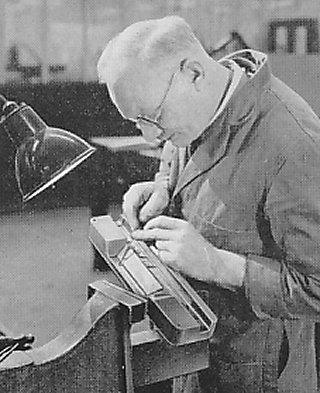
Another view of a diesinker at
work. |
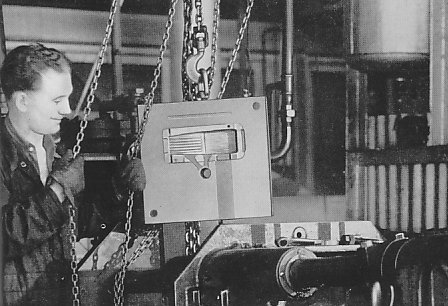 |
At work on one of the
specially designed automatic casting machines in the
foundry. |
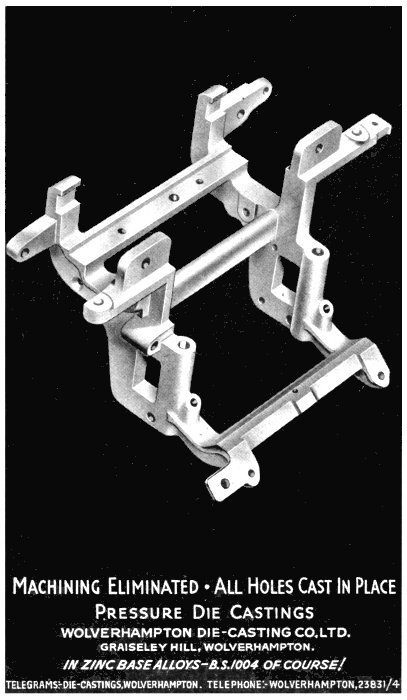
An advert from 1948. |
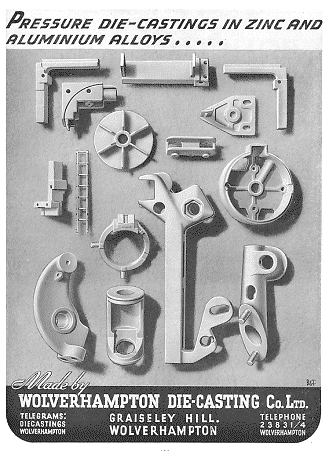 |
|
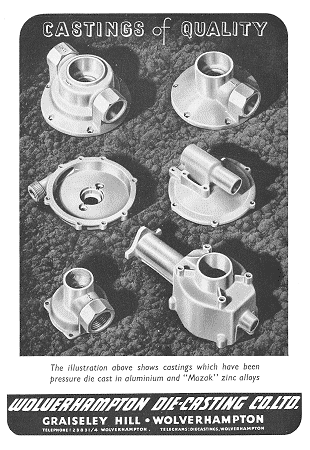 |
An
advert from 1949. |
|
An advert from 1953. |
|
In the mid 1960s the company joined
forces with British Pressure Diecasting Limited of New
Barnet, which had two factories, one at New Barnet and
another at West Chirton.
The Wolverhampton company employed
over 2,300 people, 60 percent of whom were men, and 40
percent women.
It was clearly a good place to
work, with a family atmosphere. It was not uncommon for
several generations of a family to be employed there,
and a considerable number of the employees were related.
Many of the draughtsmen in the
drawing office where exceptionally well qualified, and
experienced, and carried out design work on customers'
components before the dies were made. |
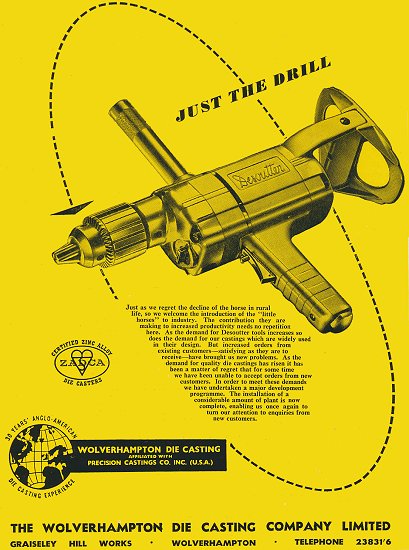
An advert from 1956 |
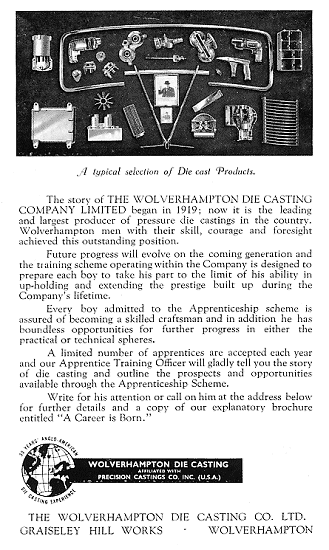
An advert from 1958.
|
In the laboratory, the
specifications of the zinc alloy and the various
aluminium alloys cast in the foundry were regularly
checked, to ensure that the high standards of purity
necessary for the production of castings, were
maintained.
Routine checks of the alloys, and
visual and photographic X-ray examinations of castings,
were regularly carried out.
Routine checks were also made in
the foundries on the quality of the surface finish, so
that a high standard was always maintained.
Inspection of castings was carried
out at various stages in the production sequence, and
more than 120 people were provided with special tooling
for this work.
By the mid 1950s the foundries
covered around 95,000 square feet, had 800 staff, and
produced approximately 3 million castings each week.
There was a separate polishing and
plating department where castings could be plated in
copper, nickel, chromium, gold, or silver. |
In order to ensure a supply of
well-trained people, an apprenticeship scheme was
developed in conjunction with Wolverhampton Technical
College.
Young men were instructed in
casting, plant maintenance, machine shop work, plating,
polishing, electrical engineering, metallurgy and die
designing.
Special technical courses were
offered to the apprentices who showed the necessary
ability and initiative, and these often led to
appointments in key positions, both in technical and
administrative fields.
The Welfare facilities for
employees included both indoor and outdoor sports, and
social activities. The sports and social club was
extremely popular.
A contributory pension scheme was
in operation, and employees automatically became members
of a non-contributory pension scheme after ten years
with the company. |
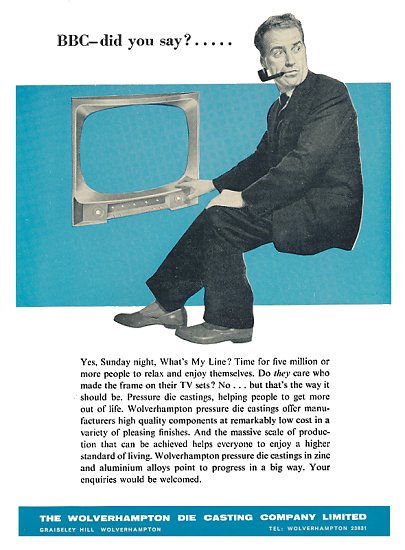
An advert from 1965. |
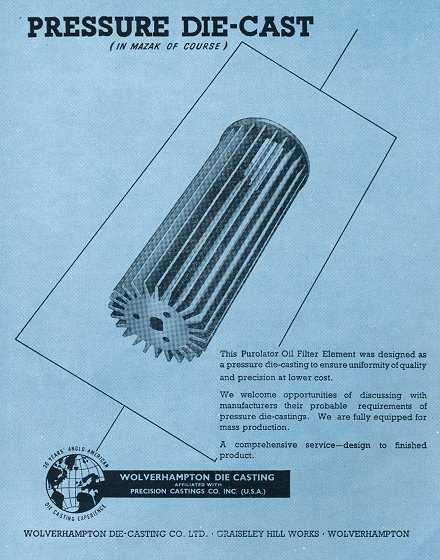 |
An advert from 1954. |
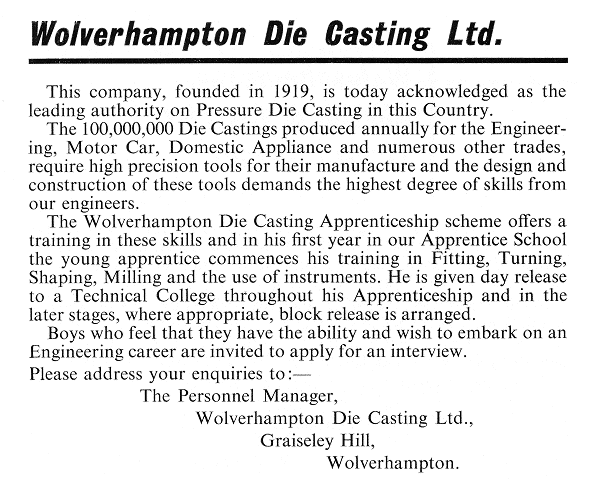
Advertising for apprentices in 1967.
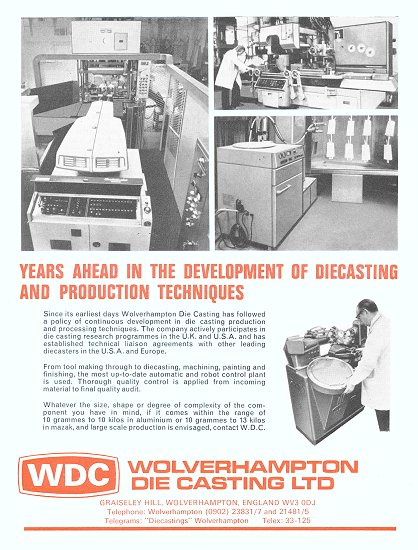
An advert from 1974.
|
In 1977 the business was acquired
by Worcestershire based Mitchell Somers.
Things started to go wrong in the
recession in the late 1970s when orders declined. The
company began to make a loss, and was sold to Cookson in
1985.
The business became Metal Castings
Limited, but sadly closed on the 16th December, 2004.
All traces of the Graiseley Hill
factory have now disappeared, the site will soon become
a shopping centre. |
An example of the up-to-date
machinery that was used on the site. Industrial robots
were very new at the time. |
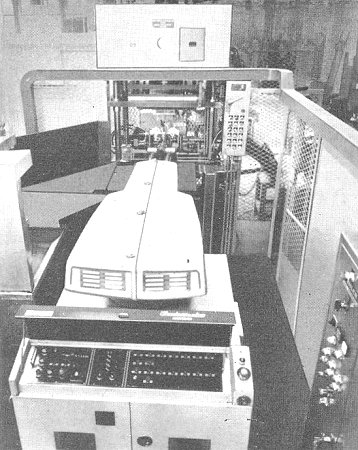 |
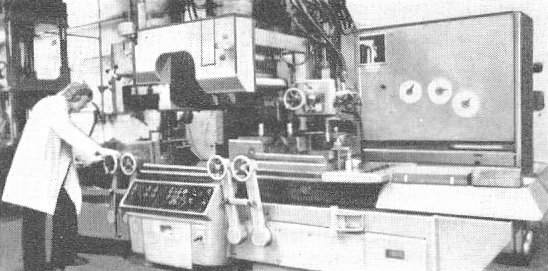 |
Another example of the modern
manufacturing facilities at Graiseley Hill, and the
investment that was put into the factory. |
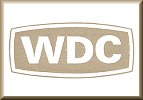 |
Return to
the
engineering hall |
|