Tarmac - The First 80
Years
The firm was named after the road
surfacing material, developed and patented by Edgar Purnell Hooley in 1902.
By the early years of the twentieth
century, mechanised road transport was becoming commonplace.
The newly developed motorcycles, steam and petrol cars
needed a good flat surface on which to run, and Tarmac
Limited came up with the solution.
Background
One of the first really suitable road
surfaces for carriage wheels was macadam, named after John McAdam. It used layers of crushed stones, with thicker ones
at the bottom, and smaller ones at the top. Most iron
carriage tyres were about four inches wide. The top layer
of stones would be around three quarters of an inch across,
so that the tyres easily travelled over them. The roads were
built above the water table, and cambered, to allow rain
water to run off into ditches on either side.
By 1834 John Henry Cassell began using
his patented ‘Lava Stone’ which consisted of a layer of tar,
covered by a layer of macadam and sealed with a mixture of
tar and sand. It could be added to an existing macadam road
after scarifying the surface.
Tarmac uses coal tar, a once commonly
available by-product from the many town gas works that
heated coal in a closed retort. Approximately 10 to 15
gallons of coal tar were produced from each ton of coal. The
tar was transported from the gas works by canal boat, or by
road in large barrels, and used to produce a wide range of
products including creosote, disinfectants, foundry pitch,
liquid fuels, naphthas, protective coatings, and solvents.
A lucky accident
In the early 1900s the search was on
for a better material for resurfacing the roads. This
problem had been worrying Mr. Edgar Purnell Hooley, the
County Surveyor of Nottinghamshire. One day in 1901 he was
passing a tar works near Denby Ironworks in Derbyshire,
where a barrel of tar had recently fallen from a dray, and
burst open, covering the road with tar. In order to prevent
the sticky black mess from spreading everywhere, a
thoughtful person covered the tar with small pieces of slag
from the ironworks. Hooley noticed that the resulting
surface was remarkably durable, dust free, and had not been
rutted by passing vehicles. |
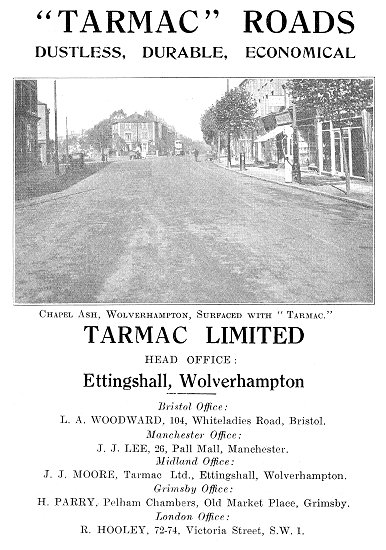
An advert from 1929. |
He realised that this material could
solve all of the road surfacing problems at the time, and
set about finding a way of producing it commercially. He
called the new material tarmac, short for tarmacadam,
meaning macadam mixed with tar. He took out a British patent
for the new material on 3rd April, 1902 (patent number
7796), and on 17th June, 1903 founded the Tar Macadam (Purnell
Hooley's Patent) Syndicate Limited.
His process consisted of mechanically
mixing tar and aggregate, which was spread over the road
surface, and compacted with a steamroller. Small amounts of
Portland cement, resin, and pitch were also added to the
mixture. Radcliffe Road in Nottingham became the first
tarmac road in the world. The new surface lived up to
expectations. It was hard wearing, and free from dust and
mud.
A factory to produce tarmac was built
at Denby, and on 26th July, 1904 Hooley obtained a US patent
for an apparatus for the preparation of tar macadam, which
improved the existing method of production. Later in 1904 he
visited the USA in order to promote the use of tarmac, but
unfortunately he was not a good businessman and had problems
selling the product. Because of lack of sales, the business
ran into financial difficulties, and in his absence
everything was put on hold. |
The story could have ended there, but luckily
Wolverhampton MP, Sir Alfred Hickman realised the potential
of the new product, which could be made from the large
quantities of waste slag that were produced at his ironworks
in Ettingshall. He purchased the ailing company and
re-launched it in 1905 as Tarmac Limited, with himself as
Chairman. |
A new Era
The new company, Tarmac Limited became
an overnight success, and orders poured in. The new
management had completely turned the business around.
Sir Alfred died in 1910, and his son
Edward took over. The company continued to be
successful, making a profit of £4,752 at the end of his
first year as Chairman, which is nearly half a million pounds
in today’s money.
Because of increasing demand, the
manufacturing facilities had to be extended, and so in order
to raise capital, Tarmac Limited became a public company in
1913.
The factories at Ettingshall and Denby
were extended in 1914, and a new factory opened at
Middlesbrough, near to the North Eastern Steel Company. Around the same time several lucrative contracts were made
with county councils. |
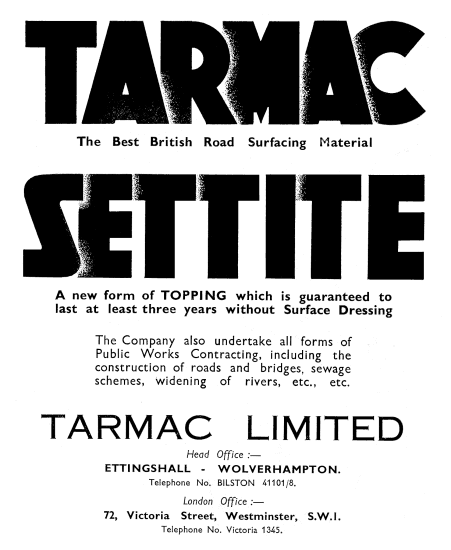
An advert from 1936. |
World War One
At the outbreak of war, the company
lost hundreds of men who joined the armed forces. This
greatly affected the road building programme and could have
led to the company’s demise. Orders rapidly decreased and
profits fell from £21,792 in 1914 to around £16,000 in 1918.
Luckily Tarmac’s Company Secretary Mr. D. G. Comyn had a
good relationship with the Head of the Road Board, Sir Henry
Maybury. This led to orders for large quantities of Tarmac,
which were despatched for military use. |
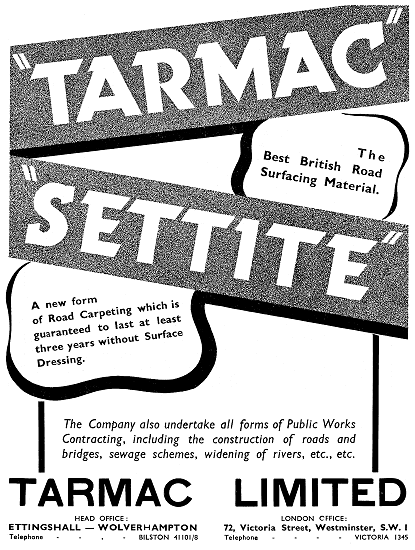
An advert from 1938. |
In September 1916 the Road Board
approached Tarmac to ask if crushed slag could be supplied
to help build urgently needed roads, to improve access to
the French battlefields. As a result large quantities of
crushed slag were shipped to the Front from Tarmac’s
Middlesbrough factory.
The shortage of labour continued to be
a problem for the company, but luckily the Road Board came
to the rescue, by supplying several hundred German prisoners
of war, who were each paid seven pence an hour. Camps were
setup to house the men at Bilston, Denby, and Middlesbrough.
By 1918, with the end of the war in
sight, Tarmac began to look forward to the future, and
expected a great increase in orders for new roads, and
resurfacing schemes.
The company leased a local slag heap from Lord
Dudley, and a steam-powered tipping waggon was acquired to
take the slag by road to the works at Ettingshall. |
The Inter-War Years
At the end of the war, orders poured in,
and Tarmac began a huge expansion programme. Sir Henry Maybury continued his relationship with the company. In
early 1919 the Board was informed that 750,000 tons of
tarmac would be needed over the next two years, for special
work alone. In order to meet the demand, Tarmac acquired
slag heaps and a roadstone quarry on the Welsh border. |
In the same year the company began to
diversify into the construction industry after acquiring the
patents for a system of construction using reinforced
Vinculum concrete, made from the company’s waste slag dust.
Contracts were acquired for the building of council houses
for Wolverhampton Corporation and the City of Birmingham.
The houses were extremely successful, and another order
arrived from Wolverhampton for a further twenty houses at
£720 each.
By 1926 around 190 miles of arterial
roads had been completed, including the country’s first dual
carriageway, the Kingston By Pass. Unfortunately 1926 was a
bad year for the company due to the general strike, the
recession, and a fall in the price of tarmac. In that year
Tarmac reported a loss of £49,576. Fortunately things soon
improved. In 1927 the after-tax profit was £44,576.
The late 1920s and the 1930s were years
of steady growth thanks to a rise in demand for the
company’s products. The average after-tax profits rose to
£57,000. There were two exceptional years, 1936 and 1938
when the after-tax profit rose to £80,000. The company’s
quarries were mechanised, and excavators began to be used to
load stone into railway wagons and road vehicles. Over the
years, Tarmac had acquired a large fleet of Sentinel steam
wagons, which were now being replaced with modern lorries.
New products appeared in the form of ‘Settite’, a bitumen
macadam, introduced in 1932, and ‘Asphaltic Grittite’, a
cold asphalt, introduced in 1938. |
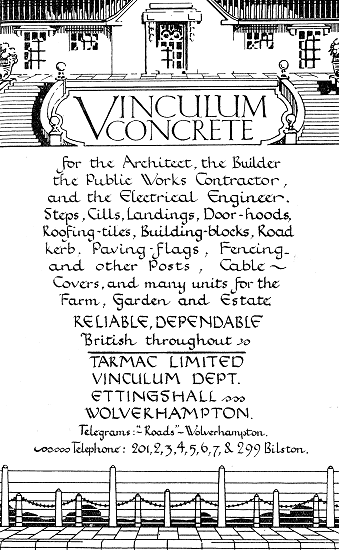
An advert from 1929. |
By this time Tarmac had become a
household name. The Roadstone Department had production
facilities at Cardiff, Corby, Deptford, Ettingshall, Irlam,
Middlesbrough, Scunthorpe, Shoreham, and Skinningrove.
In the late 1930s the company formed a
Civil Engineering Department which would not only
concentrate on road building, but also on the building of
military airports, soon to become a necessity.
The Second World War
Because aircraft played a significant
role in the Second World War, new airfields were desperately
needed, and Tarmac began a huge airfield construction
programme. |
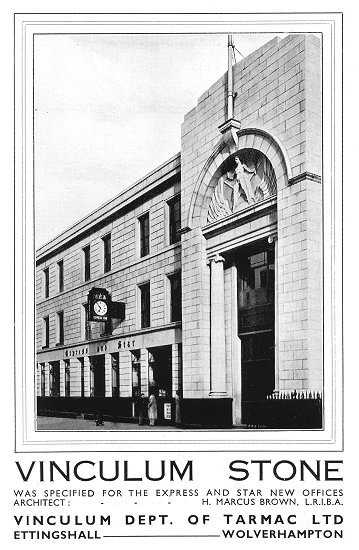
An advert from 1936. |
The company produced over five million
tons of road and runway materials, and as far as possible
introduced mechanisation to overcome labour shortages.
Nearly six million pounds worth of orders were received by
the Civil Engineering Department during the war.
The work
was often difficult and dangerous. On one occasion nearly
fifty German bombs fell on one airfield while it was being
built. Another airfield was machine-gunned by Messerschmitts
while building work was underway.
The Vinculum Department received a
large number of orders for air raid shelters. In the first
eighteen months of the war, around 50,000 precast concrete
units were produced, as well as concrete blocks for blast
walls. Building work was also carried out on gun sites, road
blocks, and defence projects.
When the end of war was in
site, Tarmac received an order for a special rush job, the
widening and strengthening of miles of roads in the south of
England, in readiness for the D-Day invasion traffic, which
travelled to the coast.
There were many other road building
projects carried out during the war. Britain’s roads had to
be brought up to scratch. One important project was the
building of the Maidenhead Bypass for Berkshire County
Council. |
The Post War Years
Tarmac began a re-investment programme
in readiness for the expected post-war boom. Over two
million pounds was spent over eight years on the
reconstruction and mechanisation of the existing production
facilities. The company was not disappointed. In 1946 the
pre-tax profit was £207,256 which by 1953 had risen to
£680,040. By this time Tarmac was processing over 2 million
tons of slag a year, and had become one of the most
important civil engineering businesses in the country. |
Tarmac built the first stretch of
motorway in the country in 1956, the eight mile long Preston
Bypass which became part of the M6 Motorway. This was
followed by the country’s first stretch of concrete surfaced
motorway, the St. Albans Bypass, which became part of the
M1.
In 1957 Tarmac Limited became a holding
company with three main subsidiaries: Tarmac Roadstone,
Tarmac Civil Engineering, and Tarmac Vinculum. In October
1958, merger talks were held with the tar distillers Crow
Catchpole, and the Amalgamated Roadstone Corporation. |
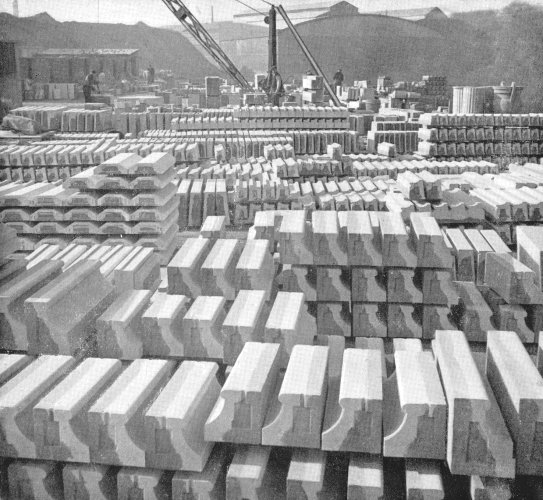
The Vinculum loading yard at
Ettingshall. |
The talks broke down and the merger was abandoned. In
1959 however, Tarmac acquired Crow Catchpole to improve its
sales capability in London and the south east. In December
of that year, Tarmac acquired Tarslag, a company based in
the north east, which moved to Wolverhampton. |
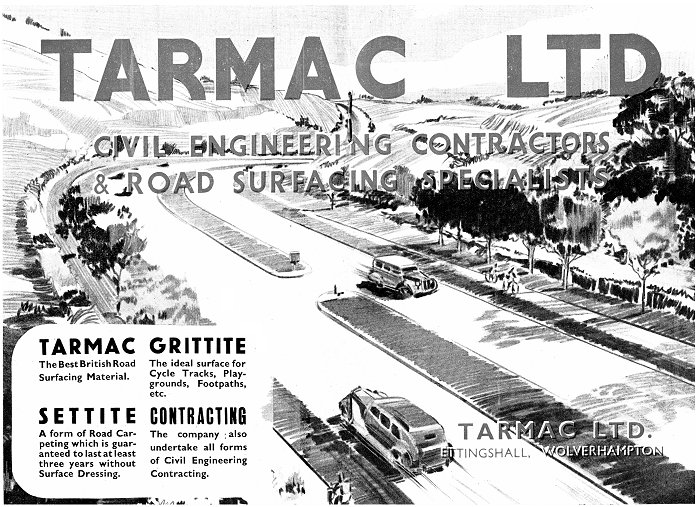
An advert from 1948. |
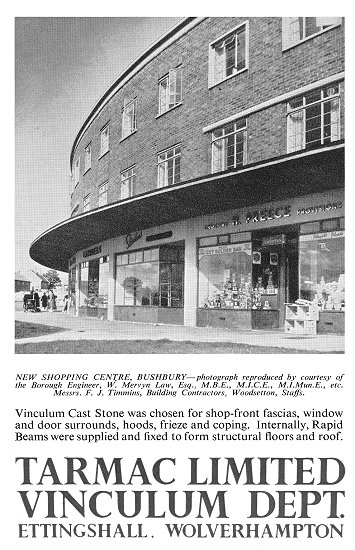
An advert from 1953. |
Tarmac also acquired Rowley Regis
Granite Quarries Limited and their massive Hailstone Quarry
at Rowley Regis. The company now had a vast supply of stone
and so was less reliant on slag. After the acquisition, the
Industrial Division was formed, to serve both private and
public industries. Local area construction teams were also
set up. They became a vital part of the company’s
operations.
Profits continued to increase. By 1959
the annual profit amounted to £1,047,000, and the equity
capital had soared to £3,592,000. Tarmac’s new Managing
Director, Robin Martin, who was appointed in 1963,
instigated a massive expansion programme, which led to vastly increased
profits. By 1970 the annual profit was £3.8 million.
In the mid 1960s one of Tarmac’s major
projects was the building of the M5 Motorway.
Because of the decline in the availability of slag,
Tarmac acquired more quarries and several slag processors,
including: Taylors (Crook) Limited, slag processors in the
north east; William Prestwich & Sons, slag processors and
quarry owners, surfacing contractors, and foundry owners in
Sheffield; New Northern Quarries in the north west; Cliffe
Hill Granite in Leicestershire; and Hillhead Hughes, a
quarrying company with quarries in Derbyshire, Lancashire,
and North Wales. |
Tarmac also secured its supply of bitumen by acquiring a
bitumen refinery at Ellesmere Port, jointly owned with
Phillips Petroleum of Oklahoma. A reliable bitumen supply
became essential by the late 1960s when town gas was replaced
by natural gas, so that coal tar was no longer available.
The first natural gas arrived from the North
Sea in 1967. |
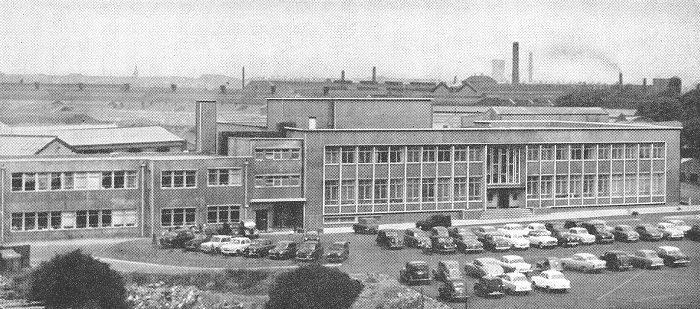
The company's head office at
Ettingshall. |
In August 1968 Tarmac merged with two
rivals, Derbyshire Stone, and William Briggs, a company
based at Dundee, specialising in bitumen, building
materials, and building contracts. Tarmac also acquired
Amasco which then became known as Briggs Amasco. The new
group, the country’s largest roadstone and construction
group was initially named Tarmac Derby, but in 1970 the word
Derby was dropped.
1971 Tarmac acquired Limmer and
Trinidad, a London based quarry products firm, with an
asphalt lake in Trinidad. Tarmac then became the largest
road surfacing contractor and blacktop producer in UK. The
acquisition included the firm of
Fitzpatrick & Son, which for many years held all of the
paving contracts for the City of London and the City of
Westminster.
Tarmac’s expansion
continued. In February 1973 the company acquired Mitchell
Construction Holdings, and its subsidiaries including
Kinnear Moodie, an expert tunnelling company. This led to
contracts for parts of the Fleet Line underground network in
London, the first tunnel under the Suez Canal in Egypt, and
the Brighton sewer outfall. The company also carried out
construction work on parts of the Majes Project in Peru,
which included the building of tunnels, canals, and
reservoirs to transport water from the Andes to irrigate the
Majes Plain. Other projects included concrete oil production
platforms, and civil engineering work on the Thames Barrier. |
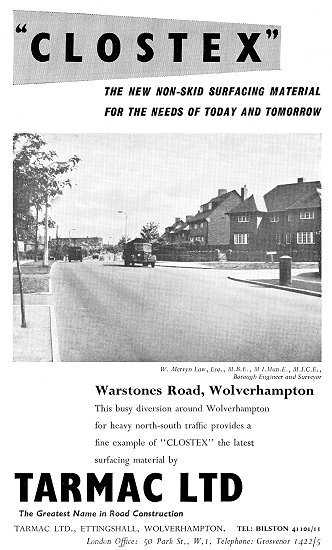
An advert from 1956. |
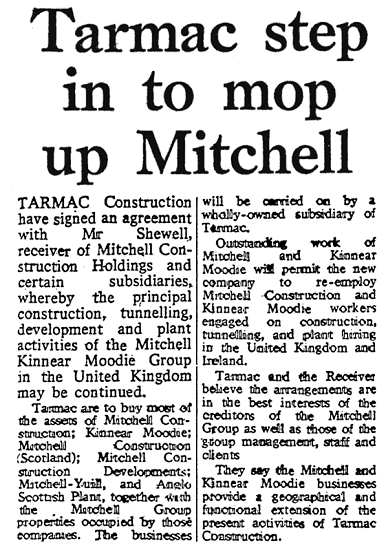 |
From the Glasgow Herald. 14th
February, 1973. |
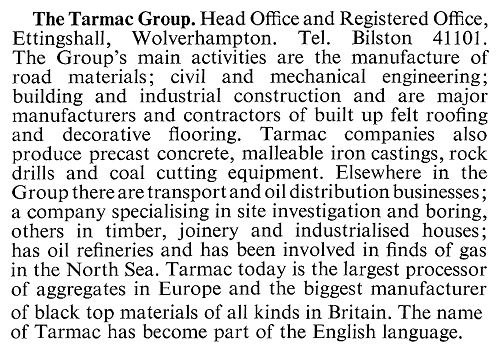
From the 1972 Wolverhampton Handbook. |
By this time the company had vast stone reserves. Tarmac
owned over a hundred quarries, and could potentially remove
over 3,300 million tons of rock, enough to supply the
country for about thirty years. The stone was mainly
quarried for concrete, building and road foundations, rail
ballast, sewage filter beds, sea and river defences, and
road surfacing.
There were also sand and gravel pits, and a dwindling
supply of furnace slag. |
The company’s limestone quarries supplied ground
limestone for use as a soil neutraliser, and stone for
cement, iron and steel production, fillers, and for the
sugar, glass, rubber, and plastics industries. Tarmac also
mined natural rock asphalt in France and Switzerland, which
is a naturally occurring mixture of limestone and bituminous
crude oil. |
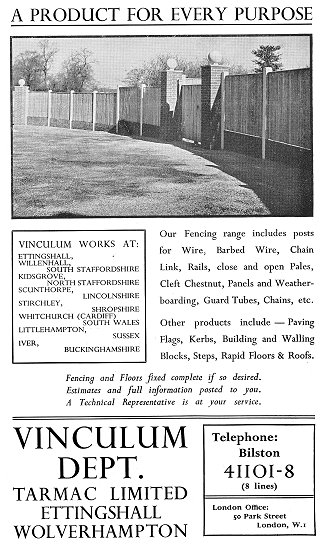
An advert from 1951. |
|
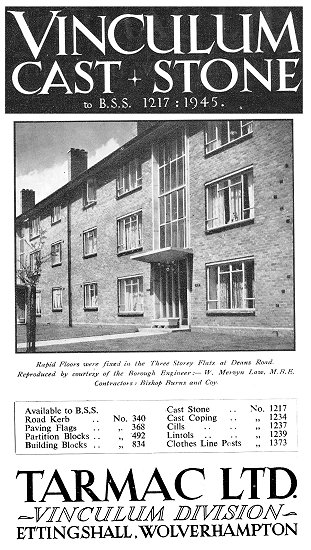
An advert from 1956. |
The road building and resurfacing part of the business
continued to thrive. Products were available with a wide
range of characteristics. There were skid resistant
surfaces, heat resistant surfaces, airport runway surfaces,
and many more. The company also had a large involvement in
the country’s motorway building programme, and built roads
throughout the world, in all kinds of terrain, from
mountains to deserts. |
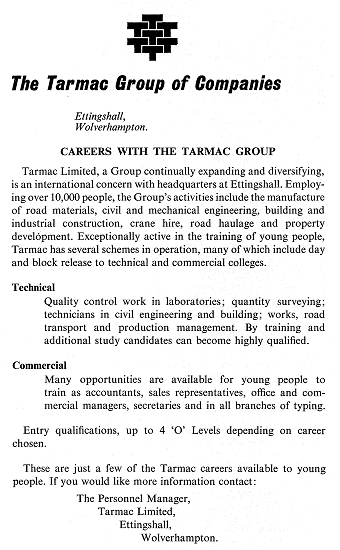
Careers at Tarmac in 1967. |
The home building side of the company
expanded dramatically in early 1974 when Tarmac acquired
McLean Homes. Up until then, Tarmac Homes, the original
private house building company, had been a mediocre
performer, but that soon changed.
After the take-over, Eric Pountain,
McLean’s Managing Director, ran the house building division.
Under his leadership it went from strength to strength,
producing around 2,000 houses a year. By the end of the
1970s McLean was building 4,000 houses a year, and
substantially contributed to the group’s profits. It soon
became the country’s biggest house builder, and in 1979 Eric
Pountain took over as Managing Director for the whole Tarmac
Group.
There were other take-overs in the
1970s. In 1976 the civil engineering part of the company
expanded with the acquisition of the building company
Holland Hannen and Cubitts which had been involved in many
important building projects.
Tarmac set up a number of teams to work
as local contractors, both at home and abroad. The expansion
continued with the acquisition of Thomas Lowe & Sons,
followed by the acquisition of Alexander Turner of Scotland
in 1977. |
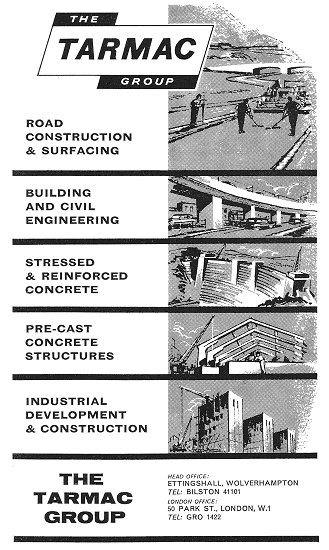
An advert from 1965. |
|

An advert from 1968. |
The company became one of the largest
waterproofing businesses in the country after taking over
Permanite, Britain’s biggest roofing felt manufacturer.
Under Tarmac’s wing, the firm’s products included bituminous
roofing felts, mastic asphalts, and bitumen polymer based
sheeting. Another member of the group, Coolag, enabled
Tarmac to produce a variety of thermal insulation products
including rigid polyurethane, and polyisocyanurate foam,
ideal for roof and wall insulation.
Expansion continued in 1980 when Tarmac
acquired Briggs' Dundee oil refinery and greatly increased
its output.
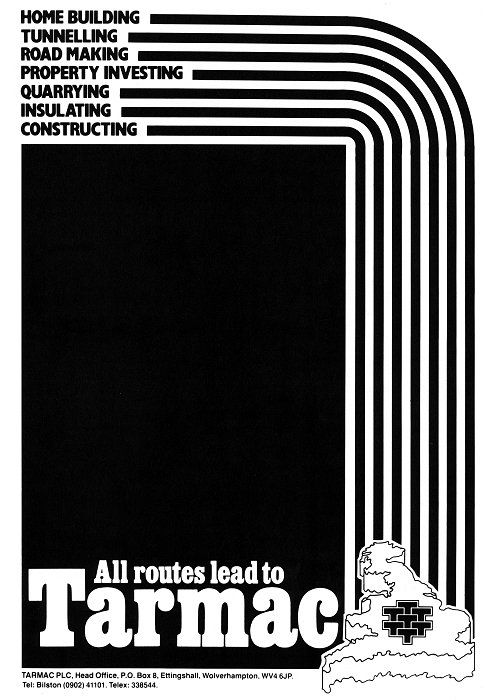
An advert from 1985.
The company grew from small beginnings
into a vast group, and since the 1980s has continued to
expand. In recent times it has itself been taken over, to become
part of one of the largest construction companies in the
world. |
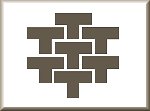 |
Return to
the
Entrance Hall |
|