Materials and Methods of Manufacture
Steel can take, and was given, a very high polish, so that it
reflected and shone as much as silver. The surface could, of
course, be decorated by techniques such as engraving. But perhaps
the most characteristic use of steel in jewellery is steel studs. These
are small pieces of steel cut to shape, and then given a high polish.
The commonest shape was a faceted stud, similar to a cut gemstone.
But in addition almost any other shape might be used, including
rectangular faceted bars, frustra of cones, crescents and vesica.
In addition steel beads were made which could be used on steel jewellery
or sewn into dresses, woven into purses or used in any other way that
took the fancy of an artisan or a lady genteelly engaged in
needlework. A shoe buckle, or other piece of jewellery, was made by
cutting a base plate, usually from steel, brass or even a low grade of
silver alloy, into the shape of the final article. The studs were then
rivetted or screwed onto these base plates. Small base plates could be
linked together to make larger pieces or flexible pieces such as
bracelets. (Note that marcasites, which are iron pyrites cut and
polished as if it were stone, sometimes look not dissimilar to steel
studs. But they are always mounted in claws or coronets, [or, in modern
cases, simply stuck into small depressions] as if they were stones.
Steel studs were always rivetted or screwed, probably because steel
jewellery sprang from a metal working tradition not from the jewellers'
tradition.)
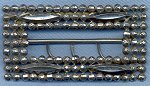 |
A buckle, complete with chape, showing faceted studs
and four vesica studs. |
A buckle, for sewing to the tongue, with a myriad of
close packed studs - or, possibly beads. The
back is heavily black laquered, possibly to protect the
stringing. |
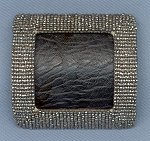 |
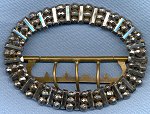 |
A buckle, complete with chape, showing
faceted bars
and studs. These faceted bars seem to be
relatively uncommon. |
A buckle for sewing on to the tongue of
the shoe, with frustra - the truncated cone shape.
|
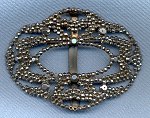 |
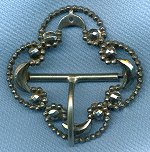 |
A buckle, complete with chape
showing crescent shaped studs. |
These are not the whole range of studs - which could,
of course, be in almost any shape. The faceted stud is the
most characteristic shape. And they could be combined
according to the notions of the designer. This
heavily decorated buckle shows faceted studs, frustra and
crescents. |
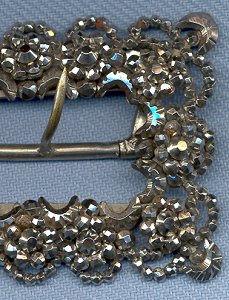 |
1. The materials
Clifford says that the best steel to use was said to be old horse shoe
nails, melted down and reformed into small bars from which the studs
were cut. On the face of it this does not seem very likely as such nails
were made of very soft steel but, if horse shoes nails, which were usual
made of a good quality of iron, are melted down correctly and re-forged,
what you get is a form of steel, which, especially when case hardened,
would serve for these purposes. But Hughes says that steel jewellery was
made out of Swedish wrought iron. Swedish iron was, at the time, the
best quality available. Angerstein notes, in a list of iron prices
at Wolverhampton, that "Swedish clair iron for candle snuffers and other
polished work, costs 21s per ton" and that "Swedish iron comes from
Bridgnorth, ten miles away by road". The learned translators of
Angerstien note that "clair iron" has not been come across before - and
that the price must be per cwt not per ton.
According to Gill' s Technological and Micropscopic Repository, 1830,
(cited in Bury, op.cit., p.702) they were cut from "either of well
annealed sheet or hoop iron; or, which is better, of cast steel
decarbonated and which is therefore reduced to the state of the softest
and purest iron".
If anything is clear from all this it is that steel toys were made
out of the best steel that could be got or afforded, and that this might
be Swedish steel or it might be steel made locally from local iron. It
was probably initially worked in a soft form and then case hardened to
produce a polishable and durable finish.
2. The methods
Steel jewellery normally consists of a back plate, cut to the shape
desired for the final piece, and then drilled with holes for receiving
the studs.
Angerstein - the only known eighteenth century observer, whose work,
not having been translated until 2001, was not practically available to
Shirley Bury and other writers - gives a detailed account of the
process, anyway as he saw it being carried out in Woodstock in 1753.
This process may not have been used in all places at all times.
His account is as follows:
Most of the work on articles of this type is carried out when the
material is still in the form of soft iron. Subsequently it is
packed in paste and case hardened. After that the parts of
finally assembled and polished. Parts that are very thin and
minute, for example the smallest links and screws for watch chains,
are made of steel from the start and are generally not hardened or,
if they should be, they are tempered to restore the strength and
toughness.
During the process care is taken to complete all the work as far
as possible before the case hardening takes place and that includes
much of the polishing, which makes the final polishing operation so
much easier. When making 'diamante' items, the steel diamonds
are screwed into place and the whole object completed before being
taken apart again for case hardening and polishing, after which it
is finally assembled.
To make it possible to polish small pieces, they are screwed into
a pin, mounted on a handle which, when in use, is supported by a
wooden beam. The paste used for the case hardening is made by
charring old leather until it can be pulverised in a mortar,
after which it is mixed with brine or urine. The following is
another and better mixture: 'Cows or horse hoofs and sheeps horn
burnt til thy will, pound in a mortar, mix with a little salt or
urine or brine makes the best hardening'. [Angerstein's
learned translators note that this quotation is in English in the
original and was probably (mis)copied from a manuscript in
Angerstein's possession]. When the articles are ready for case
hardening, they are placed in an iron box and covered with the
paste. The packed box is covered with an iron lid and placed
in the hearth, in which the fire has been blown up to a high
temperature. The lid is made with a little handle so that it
can be lifted up for checking the heat inside. The temperature
has reached it proper level when the black material of the paste is
white all over. The box is then removed from the fire and the
contents thrown into a cauldron full of water. A sample piece,
dimensioned in accordance with the articles in the bath, is also
placed in the box and subsequently fractured to show how far the
hardening has penetrated, if it has gone too far or not far
enough.
Small screws and other similar items that might warp are placed
on top of the hot box for tempering and then thrown into oil, which
gives them toughness. For the polishing, white whetstone from
the Levant and oil is first used, then emery mixed with oil
and finally, tin oxide with good spirits. The emery and the
tin oxide are applied with special wooden sticks but the last
polishing is carried out by rubbing with the palm of the hand and
fine tin oxide. I was told that it requires two weeks' work
for one person to make a pair of buckles costing 2 guineas.
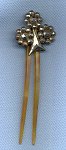 |
That is Angerstein's account. We can try to break
it down into further detail. Note that Angerstein does
not mention the making of the back plate which would have
been a first step. This back plate was, originally,
made from rolled steel sheet but later on was often made of
brass or copper, usually silvered. Bury suggests that
this development dates from the time of the Paris Exhibition
of 1867. Back plates, in whatever metal, could have
been stamped out of the sheets or hand cut with tin snips. |
The studs and beads then had to be made.
For this step we can turn to Gill, who was reporting on the
methods used in Birmingham in 1833. Studs were cut in
a fly press, and their centres were then slit to receive a
length of iron wire, which was brazed into the slit to
provide shank. Small beads were punched out of sheets
and then made into spheres with steel tools on a filing
block, and then had holes punched in them. Large hollow
beads were stamped out, then shaped in dies and punches. |
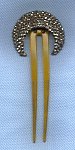 |
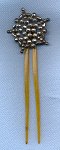 |
According to Gill it was at this stage that
the pieces were case hardened. As Angerstein has it,
each piece is assembled (presumably for checking) and then
disassembled and the pieces case hardened. It may be
that Angerstein was describing the process by which
individual pieces were made, one at a time in Woodstock; and
that Gill was describing a kind of mass production, in
Birmingham, where large numbers of standard studs and beads
would be produced for use in pieces which would be designed
and assembled later. |
One would only add that, particularly in the Birmingham
case, it seems that the studs could be stamped so well that
they needed no filing or fettling to trim them; and that the
case hardening would penetrate so deeply that the amount of
polishing that might be required could be accommodated.
According to Gill (as described by Bury) the pieces were
case hardened "by being placed in layers in shallow iron
trays, with bone dust in between them and then "subjected to
fire". |
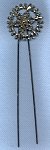 |
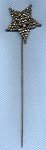 |
The recipe Angerstein gives for the case hardening paste
is similar to that given by Plot in 1686. He says that
iron "for some of the finest work, they commonly harden in
order to their receiving a better polish". This was
"formerly done" with hoofs and horns of cattle, sand and
salt, which were mixed and put, with the iron to be treated,
in a "coffin of clay" and then heated. But when he
wrote he said that "it is being done at Wolverhampton with
burnt hoofs and hornes, fountain and bay salt, sublimat,
urin, old burnt leather, and tartar, all mix't together and
reduced to powder". As Plot was the Professor of
Chemistry at Oxford he presumably got this recipe reasonably
right. He noted that this process produced case
hardening, as he comments that the hardening was "only on
the outside about the thickness of a shilling at most, which
is highly sufficient to receive a polish". |
Neither Plot nor Angerstein comments on how the pieces
were shaped. Hunt and Holland make a brief reference
to a lapidary's mill being used. Gill gives more
detail, He says (as paraphrased from Bury's account of
Gill) that the beads and studs were faceted in groups
on a horizontal lap wheel. It seems that Gill is
saying is that at least some of the shaping was done in the
stamping out stage. This may well have been the case
in Gill's time and place but one suspects it was not the
case at Woodstock or in the earlier days in Wolverhampton or
elsewhere, when stamping was not so well carried out or
widely available. Indeed Bury says that stamping our
pieces was a technique imported from France in the early
decades of the nineteenth century. |
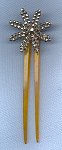 |
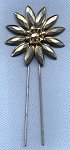 |
Once the pieces were shaped and case hardened, then had
to be polished.
When Angerstein was in Derbyshire, he remarks:
"Bakewell is situated nearby and here a stone known as
'Rottenstone' is quarried, used for metal polishing
and at Wolverhampton for steel polishing". A quotation
from "The Technical Repository" given by Hunt, provides more
detail: |
"the hardened steel is either polished fiat, like glass, or cut into
facets, like a diamond, consequently the lapidary's mill is used. The
workmen commence by smoothing the work with rather coarse emery, then
with finer emery, and finish with the finest. The smoothing being
perfected, they polish it with English rouge, trit‑oxide of iron, and
oil, and finally finish it with putty of tin (peroxide of tin) and
water. When the steel articles consist of raised and hollow work, they
are smoothed and polished with the same substance; but the instruments
are, as in the case of less harder [sic] metals, pieces of wood,
properly shaped, and employed in the same manner: sometimes also the
circular brush is used."
It seems reasonable to say that the lapidary's mill was normally used
but that does not exclude the possibility that filing was also used.
Bury gives Gill as saying that studs were polished in
groups fixed to a block and brushed with emery powder and
water, the brushes often being attached to a lathe.
The remaining marks were then removed by a preparation of
ironstone and water and a polish given with a putty formed
of metallic oxides. Beads were polished by stringing
them on a wire and holding them against a brush on a lathe. |
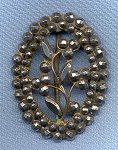 |
At what must be a later period the French (and may be others) adopted
a polishing method of tumbling the pieces in emery powder and water,a
process which was, Bury says, cheap and easy though slightly burring the
sharpness of the facet edges.
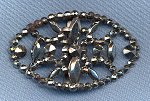 |
The studs were then either screwed or rivetted into
position. Bury says: "The screw method seems to have
been abandoned soon after Queen Victoria came to the throne,
it being easier and cheaper to rivet the studs to the back
plates by means of their wire shanks. They were then
trimmed and hammered down on the reverse side of the plate."
In later times it appeared that the studs could be set in
the back plate by machinery but details of this development
are lacking. |
I might as well comment here, as anywhere, that however brightly
polished the studs, and whatever the quality of the steel used, the
studs do not, unlike gemstones, reflect light from within. So a diamond
laid next to a steel stud would seem brighter and more sparkling. Some
items of steel jewellery try to obtain an equivalent brilliance by using
a large number of studs, closely packed, to catch and reflect as much
light as possible. Some pieces which seem to be covered with a myriad of
very small studs are likely in fact to be covered with steel beads. At
the height of steel jewellery's popularity the lighting would be by
candles and their flickering light would play on the studs far more than
would the steady light of a modern electric bulb. Of course movement by
the wearer causes the studs to flash. And very bright lighting
directly on displayed pieces greatly enhances their appearance.
In due course, with the improvement of stamping and
pressing of metal, it became possible to make passable
imitations of cut steel jewellery (especially buckles) and
to do so very cheaply. Bury attributes these
productions to Germany in the latter half of the 19th
century. These items do not usually have anything like
the polish of the real things - nor, of course, their
weight. They are usually easily identifiable by
examining the back where their hollowed form and lack of
backing plate and rivets gives them away. |
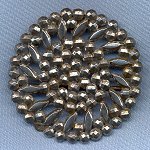 |
However, such items were sometimes made with a backing plate and,
even, with one or two real studs added. If the number of studs on
the front of the piece does not correspond with the number of rivets on
the back, that usually indicates these mixed method items.
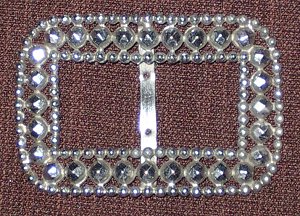 |
A buckle stamped out of white metal, possibly
plated. Probably late Victorian. Possibly German made.
One of a pair.
|
The back of the buckle above, showing that there
are no rivets and the studs are not real studs. |
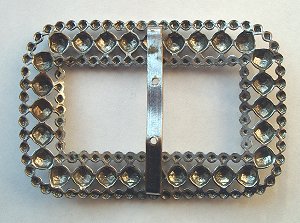 |
|