In 1712, a Newcomen steam
pumping engine began to operate at the Coneygree
coal mine and the first commercial steam engine
built by Boulton and Watt began pumping water from
Bentley and Company’s Bloomfield Colliery in 1776.
There was a huge demand for
coal to fuel the local iron works and so large
numbers of coal mines operated in, and around the
area. Some of the blast furnaces consumed 600 tons
of coal per week. Mine spoil heaps became a common
sight. By 1835 the annual rent for coal mining land
was around £1,000 an acre.
Beginnings
The mineral rights belonged to
the Lord of the Manor and anyone wishing to dig for
coal had to acquire a copyhold, which was a legal
document obtained via the courts. Such surviving
documents provide evidence for early mining in the
area. In 1272, a survey of the manor of Dudley,
makes reference four pits of sea coal that were
worth four pounds annually. It is thought that they
were in Woodsetton.
Many coal mines opened in the
area. By the early 17th century, licences to dig for
‘sea coal’ had been granted by the lord of the manor
to pits at Woodcross, Cinder Hill, and Woodsetton.
It seems that by that time, Cinder Hill and
Woodcross were already centres of a small mining
industry. In 1613 a licence to dig coal at Coseley,
was granted to William Persehouse, at ‘Smythie
Crofte’, ‘The Leys’, and at ‘Crosses’. Another local
resident, John Birche, obtained a licence to dig for
coal in ‘Woodcrosse’, Ettingshall. Roger Hickmans had a licence to dig for coal in
‘Ettingshall Over Field’.
In 1686, Doctor Plot wrote about
the local coal deposits in his ‘Natural History of
Staffordshire’, describing the ‘fat shining coal’
that was to be found in parts of Coseley.
Coseley’s coal mines greatly
benefited from the opening of the canal, which had
been built to enable the easy and cheap
transportation of coal to Birmingham, to supply the
many industries there. The building of local
railways in the 1850s also helped the local mining
industry, but to a lesser extent.
An early account book in Dudley
Archives has the following entry:
Coseleymoor Colliery
Trustees of the late Lord
Dudley
Saturday 28th July, 1789
Messrs. Gabb & Co. Boad No.0.
Steerer: Abraham Darby
21 Tons 8 Hundreds of Coals
To Birmingham
20 – 18 Charged
N. D. Bradley
Coseley Moor Colliery |
|
At this time, the canal had not
yet reached Coseley, so the coal must have been
loaded at Bloomfield or Bilston.
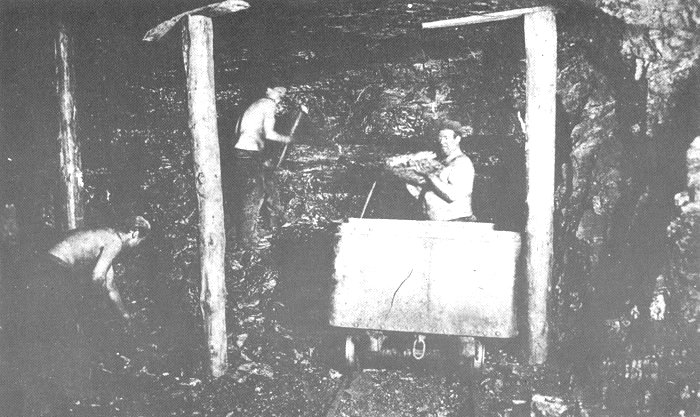
Working at the
coal face. From an old postcard. |
Later Years
In the 1870s things started to
go wrong. A depression in the iron trade led to a
fall in the price of coal, which in turn led to the
closure of many mines. A long strike took place in
the coalfield, during which labour was withdrawn.
Pumping engines were not operated, and many mines
flooded. In 1870 it was estimated that around 150
million tons of coal and 20 million tons of iron ore
were under water in South Staffordshire.
Some mine owners would not use a
pumping engine because they were also draining their
neighbour’s pit at their own expense. Pumping also
altered surface drainage, because the water was run
into streams, which percolated back into the mines.
A petition to Parliament led to
the South Staffordshire Drainage Act of 1873. Under
the terms of the act, a Board of Commissioners was
created to raise money to fund pumping operations. A
rate of one penny per ton of coal, slack, and fire
clay was levied on the mine owners, but initially
little progress was made. In 1878 greater powers
were granted to the commissioners. During the next
10 years, £100,000 was spent on pumping water out of
the deeper mines. In 1886 the levy was raised to
nine pence per ton of coal, slack and iron ore,
three pence per ton of fire clay, with an addition
of one penny per ton for surface drainage. Water
courses were straightened, and made watertight by
puddling the beds with clay.
The Mines Drainage Commission
opened a pumping station off Moat Road, Summer Hill,
on part of the Moat Colliery site. It was powered by
a large beam engine that could pump water from a
depth of 620 feet. The engine operated between 1893
and 1902 and raised over 7.3 billion gallons of
water during that time. The operation cost over
£2,500 annually, but in spite of all the efforts,
the drainage problem was never solved. The
Commission was largely ineffective.
In 1890 the Mines Drainage
Commission wanted to know if it was still worth
draining mines in the South Staffordshire Coalfield
and so contacted mine owners to ask for an estimate
of the quantity of workable coal still in the
ground. The results showed that in the local area
alone, around 43 million tons of workable coal and
ironstone were still in the ground. By that time
coal production had fallen to half of what it was in
1874, and around £75,000 would be required to
completely drain the deep pits in the area.
By 1896 most of the local
collieries had closed, although a few of the larger
ones remained, bringing the total mining workforce
to 1,332. By this time, most of the easily workable
coal had gone, and a coal strike for higher wages in
1912 resulted in the closure of many of the
remaining pits. The few that survived had all closed
by the late 1930s.
As well as coal, there were
deposits of ironstone and limestone that led to
formation of the local iron industry. There were
also numerous clay deposits that led to the
formation of many brick works. In 1851 there were
the following brick makers: James Bates, Edward
Cartwright, George Church, Job Elwell, and Benjamin
Gibbons. In 1912, Isaac Hughes made bricks at Cinder
Hill. Thanks to the local deposits of fire clay,
there were also the following makers of fire bricks:
Thomas Hinton, Benjamin Johnson, John Mellard, and
William Waterfield. In 1912 William Mobberly was
producing fire bricks in Upper Ettingshall Road.
There were also local cement
manufacturers using the local limestone deposits. In
1912 cement was being produced by the Deepfield
Company, run by James Hill.
|