The firm had three local subsidiaries, Bradley
(Concrete) Limited, of Darlaston; Bradley (Darlaston)
Limited, of Capponfield, Coseley; and Arblaster &
Company Limited, of King's Hill. Darlaston Iron Works
was the largest producer of refined pig iron in the
country. The firm also manufactured special
castings that were resistant to heat, wear, and
corrosion; cast iron nuts and bolts; metallic abrasives;
heat presses and other machines; and all types of
pre-cast concrete work. The managing director, George
Lunt, started to work at the site in 1943. He began as a
foreman-manager, then became general manager, followed
by works director, before becoming managing director in
1957.
Some of the staff in 1959 were
as follows: Tom Green, from Bilston, was in charge of
transport. He had a small office beside the weighbridge
and oversaw around 200 lorries each day, when they
entered and left the works. The firm had eight long
distance lorries of its own, each of which travelled
about 1,000 miles every week, and could carry a load of
nine tons. Cyril Chambers from Walsall, the garage
foreman, looked after the fleet of lorries.
Norman Wood, who lived in Fallings Park,
Wolverhampton was the technical representative. He
travelled an average of 17,500 miles each year, visiting
customers. Valerie Smith
from Blakenall was one of the sixty women workers
in the nut and bolt department. She was a machine
operator, and her father Frank Smith was shift foreman.
Another three of the women in the nut and bolt
department were Valerie Smith, Martha Collett, and Mary
Chrimes who all put the nuts onto the bolts, a process known as
'buttoning up'.
Two of the foundry staff were
Harry Hawkes, who was in charge of foundry sales, and
Bill Greenway, a moulder. Jack Sherrard, from Darlaston,
was a metal tester, and Ken Bull, also from Darlaston, was
one of the apprentices. Another trainee was John Egan,
who wanted to become a metallurgist. The oldest member
of staff was Jack Sherrard, aged 70.
Some of the office staff were Ann Wilkes, who worked
as a shorthand typist, secretary Valerie Turner, from
Darlaston, and Joyce Walton, from Walsall, who was
secretary to the production manager. Bill Jones of Wood
Green, Wednesbury was the buyer, Harry Hawkes from
Bilston was in charge of the factory sales section, Roy
Orton from Bilston worked in the accounts department,
Assistant sales manager was William Taylor from
Essington, and George Hull from Kingswinford, a keen DIY
enthusiast, was drawing office manager. Cliff Horsfield
from Darlaston, was one of the draughtsmen, and Sam Ralph worked in the concrete department.
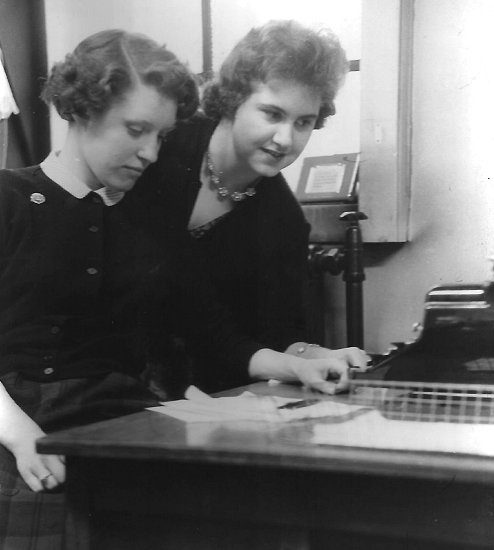 |
Shorthand typist Ann
Wilkes and a colleague.
Ann, who lived at Bentley
was a former Darlaston ladies football team
member. She retired from the game after a leg
injury.
Courtesy of Ken
Southwick, and Christine and John Ashmore. |
The Darlaston site had its own railway, and a 35 ton
steam locomotive called 'Daisy' that was driven by Bill
Mayer from Darlaston, who also used to drive the firm's steam
cranes. Ken Southwick, who also worked for the company,
remembered that at one time there were three steam
engines which were more powerful than the company's
diesel locomotives. During the Second World War, one of
the steam engines was left in gear, and the firebox was
not completely emptied. During the night the steam
pressure in the boiler built up, until it was strong
enough to start the engine moving. It ran along the
track, until it fell off, and landed on top of the works
air raid shelter, which at the time was occupied by
members of the night shift. The people inside thought it
was a bomb. Hot water from the boiler soon began to leak
into the shelter, and they thought they might drown.
Ken also mentioned that the moulders were on piece
work, so the apprentices who were learning to be
moulders were paid by the moulders themselves, and not
the company, whereas all of the other apprentices were
paid a weekly wage by the company.
Some of the Coseley Staff were as follows:
The works foreman was keen motorcyclist Jack Bonsall.
Number one furnace man was John Bull from Coseley, who
operated the furnace with his two colleagues, David
McElroy from Sedgley, and Harry Hill from Coseley.
Between them they threw eight tons of scrap metal into
the furnace during each eleven hour shift. Tom Cattell of Short Heath operated the two works diggers,
and the two works dumpers that moved the scrap metal
around the site, and Harry Turpin from Willenhall, a
keen cricket enthusiast, was weighbridge clerk,
Some members of staff at King's Hill:
William Burns of Gospel End, Sedgley was works
manager. He also worked as a part-time mathematics
lecturer at Wulfrun College. Will Arblaster, who lived
next door to the factory, which was once owned by his
father, was machine shop superintendent, and Granville
Clerk from Coseley was personnel manager. The youngest
worker in the machine shop was 15 years old Larry
Beardmore, from Darlaston.
|