Camelinat and Company
Limited, Birmingham |
In 1890, twenty years old Eugene
Camelinat, started his business in Birmingham, as a
spinner to the gold and silver trade. He had been born
in France, but moved to England with his parents, in
about 1871, during the Franco-Prussian war.
His firm began to spin all metals,
and undertook copper smithing, polishing, plating and
built assemblies in sheet metal. As a result, the
business was quite successful. Eugene was among the
earliest pioneers to work in aluminium. At the time,
copper was extremely expensive, and so he pioneered a
method of copper plating zinc, which enabled the firm to
increase its production of art metal work.
By the late 1890s, cars and
motorcycles were beginning to appear. Eugene realised
their potential, and so began to produce a range of oil
and acetylene lamps, and later, electric lamps for both
cars and motorcycles. |
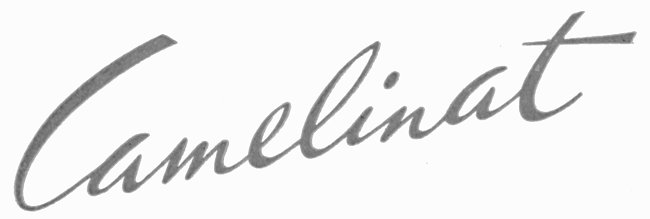 |
The First World War the firm made
engine cowlings for Handley-Page aircraft, manifold and
water fittings for aircraft engines, acetylene lighting
sets, hand grenades and petrol tanks.
By this time, Eugene’s four sons
had been working in the business, and learning the
trade. In 1922, Eugene took a back seat, and the four
brothers started to run the business.
In the Second World War the firm
produced steel helmets, smoke and signal bombs,
incendiaries, bomb tails, primers and exploders, mine
horns, gun cases, machine gun magazines, and many
pressings and assemblies for all the Government
departments.
In 1945, the firm joined the Owen
Organisation and began to specialise in the production
of metal products for the aircraft industry, for vehicle
manufacturers, and for the electrical industry,
shipbuilding industries, railways, and general
engineering. |
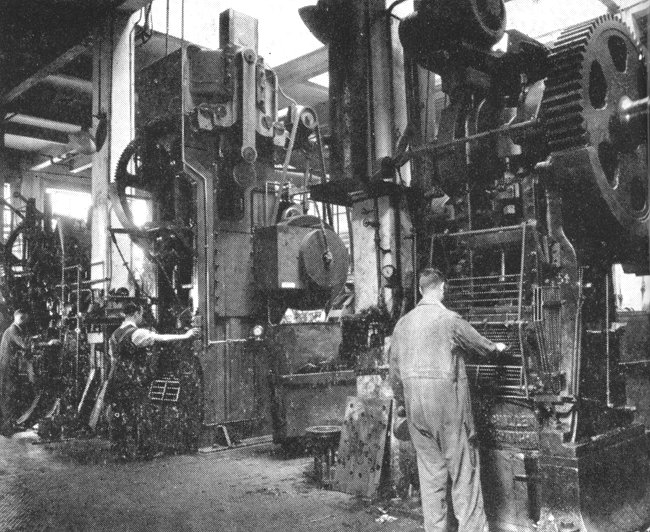
Part of the press shop. |
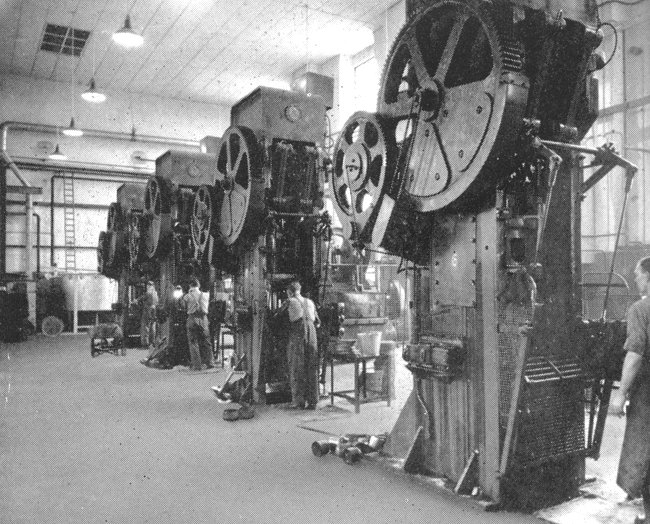
Another view of the press shop. |
The factory had the most up-to-date
machines, and could produce all types of deep drawn
pressings, light and medium pressings in steel, brass
and alloy, all using the firm's own press tools. Sheet
metal could be spun up to 50 inches in diameter, and bar
products up to 2 inches in diameter could be machined.
The press shop had over sixty presses. The single action
presses ranged from 20 to 400 tons capacity, the double
action presses could draw to a depth of 12 inches from a
33 inch diameter blank. The firm also had electric
bright annealing furnaces for the heat treatment of
pressings between operations. There were also
departments specialising in electric and acetylene
welding, spray enamelling, polishing and electroplating.
In 1950 the business expanded with
the opening of a new factory at Dowlais, Glamorgan, for
the production of deep-drawn presswork. |
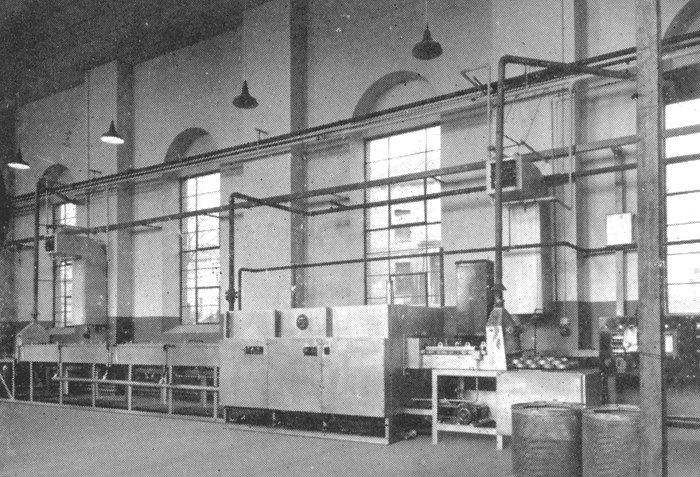
The heat treatment plant. |
 |
Return to
the
previous page |
|