Wilkins and Mitchell Limited became one of
Darlaston's leading engineering companies, employing
over 1,000 people. The family business in Richards
Street produced machine tools and power presses, for
either hot or cold pressing. They can be found in factories throughout
the world. |
It all started in 1904 when two
friends, Walter Wilkins and Tom Mitchell from
Yorkshire, set
themselves up in business in a small factory in Bell
Street, called Phoenix Works, owned by nut and bolt maker Charles
Richards.
Walter, aged 29 had previously been
the head designer at Samuel Platts in Darlaston
Road, King's Hill,
and Tom aged 35, had a strong passion for
engineering, together with a great deal of technical
expertise, and the willingness to work hard for long
hours.
Walter and Tom started with a
few machines including a borer, an eight foot
planer, a milling machine, a slotting machine, a
twelve inch gap lathe, and a vertical drilling
machine.
Their first job was to
repair the steam roller belonging to Darlaston
Council.
|
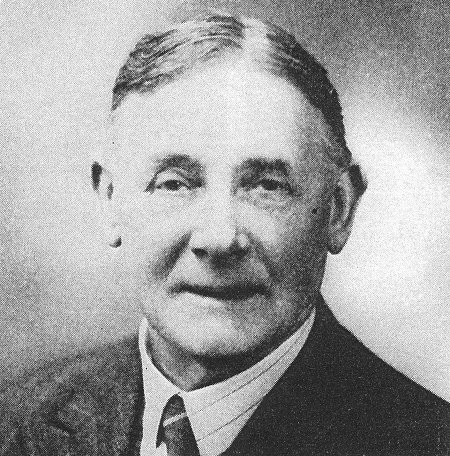
Walter Wilkins in later life. |
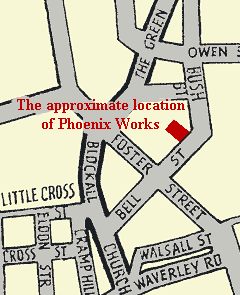 |
The map opposite shows the
approximate location of Phoenix Works in Bell Street.
Walter
Wilkins and Tom Mitchell rented the factory from Charles Richards. |
They soon received their first order for a piece
of machinery. It came from Rubery Owen and consisted
of several drilling machines. Around the same time they
received an order from Charles Richards for stripping
machines and a bolt heading machine. The bolt heading machine was the most advanced
machine of its kind, being considerably smaller than
the competition and about half the price. The two
friends soon formed a close relationship with both
companies. |
1907 proved to be a landmark year for the company, which
began when they received their first
order for machinery from a railway company. This
would become a common occurrence in
years to come, and provide the firm with a regular
income. The order, from the Birmingham Carriage
Company was for a slot milling machine.
The second
milestone was an order from Rubery Owen for a
blanking press. Walter designed the press to operate
hydraulically, with all of the hydraulic components
made in-house. As a result Wilkins and
Mitchell would go on to become one of the leading
manufacturers of power presses. They soon produced a
similar machine for Thompsons. The following year Walter and Tom built the first
British multi-head sole-bar drilling machine for the
Birmingham Carriage Company, a product that would prove
to be popular for the next 25 years.
By this time the
workforce had grown to two fitters, and an apprentice;
Tom’s son Joe.
|
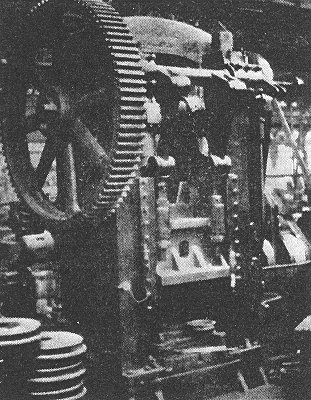
An early Wilkins and Mitchell double
action toggle press. |
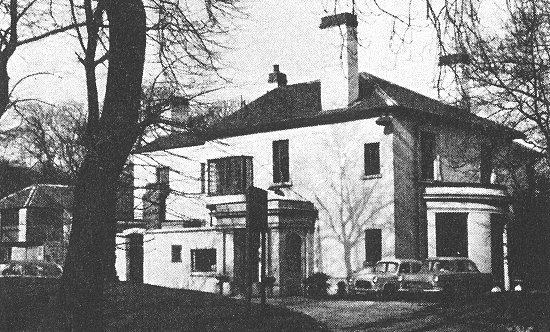
The Hollies, the Wilkins' family
home. |
1908 would be a memorable year in
another way. Walter Wilkins had become a great friend of
Charles Richards and his family, and had fallen in love
with his youngest daughter Louisa. Before the year was out they
were married, and the company’s employees were given an
hour off to attend their boss’s wedding. Walter and his
bride moved into their new home, The Hollies in Wednesbury. |
Expansion
By 1910 business was booming. There
were so many orders that they couldn’t cope in the
cramped conditions at the Bell Street factory. Luckily
the solution was at hand. Darlaston Green Works were
available at the time and so Wilkins and Mitchell
acquired the factory and renamed it “Phoenix Works”. At
the time they were receiving a lot of orders for special
machinery from railway carriage and wagon companies.
In 1911 Walter Wilkins and Alfred
Owen senior conceived the idea of a massive forming
press to cold press vehicle chassis frames, so
revolutionising production. Chassis frames were made
from around 10 gauge steel, and until that time had been
pressed hot. Although several similar presses were in
use in the U.S.A. nothing on this scale had been
attempted here. Walter’s design used a similar hydraulic
system to the one that he developed in 1907 for the
blanking press. The press, costing a mere £2,000 was
installed at Rubery Owen’s Darlaston factory in August
1913 and became an immediate success. It worked so well
that it continued in operation until 1970, and can be
seen today at the Black Country Living Museum.
Some earlier Wilkins and Mitchell’s
machines including a mechanical shear were still in use
at Rubery Owen’s factory until 1960, clearly
demonstrating the reliability of the company’s products. |
The company's first 1,500 ton "upstroking"
press that was installed at Rubery Owen's Darlaston works in
August 1913.
It ran until 1970 and cold
pressed lorry chassis by raising steel blanks that were
pressed into the correct shape. |
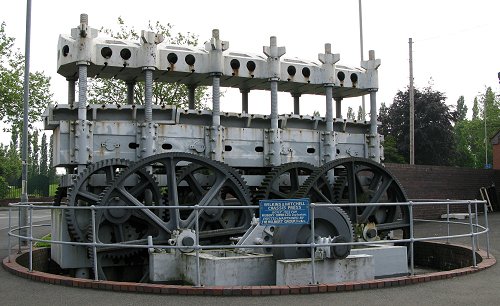
The press
at the Black Country Living Museum, Dudley. |
A
Trip to America
The success of the huge press and
the close relationship between Walter Wilkins and Alfred
Owen led them to go on a fact finding tour of the
U.S.A. to explore the latest developments in machine
tools. Walter had always been impressed with American
engineering and their seven week tour would provide them
with plentiful opportunities to examine the latest
machines.
It nearly ended in disaster because
they booked their passage on a brand new luxury ship,
RMS Titanic, but luckily last minute business
commitments forced them to delay their departure. Had
they not done so, the history of manufacturing in
Darlaston would have been very different, with the
possible loss of two of the town’s most important
manufacturers.
Thanks to the delay they sailed on
RMS Lusitania and after arriving safely visited many of
the leading American machine tool manufacturers. They
also inspected some of the factories belonging to the
largest vehicle manufacturers including Ford, General
Motors, and Studebaker. As a result of their successful
tour Alfred Owen conceived the idea of producing vehicle
chassis and other motor components for British vehicle
manufacturers at highly competitive prices. Similarly
Wilkins and Mitchell would go on to build competitively
priced, state of the art machines for the same
manufacturers.
The
War Years
For the first two years or so of
the First World War, the manufacture of special purpose machine
tools and presses continued much as before, except that
production had to be greatly increased to keep-up with
the demands of the munitions industry.
At the beginning of the war Wilkins
and Mitchell employed between 60 and 70 people who
worked flat out to supply the needs of their customers.
Unfortunately the constant pressure to keep up with the
demand for the company’s products became too much for
Tom Mitchell, who in 1916 broke down under the strain and retired
to Blackpool. He sold his interest in the firm to
Walter, who also came under a
lot of pressure.
Apart from the day-to-day running of
the company, he became involved in other work. He was
asked to go to the War Office in London to assist in
vital war work. As a result he became a consulting
design engineer, assisting Dr. Frank Lanchester in the
design of a compact transmission for tanks that would
allow more room inside for the crew. As a result he
built an experimental tank at the Birmingham Carriage
Company.
He also carried out consultancy
work for other companies, which resulted in him dashing
all over the country. In 1916 his work load increased
even more when Wilkins and Mitchell designed and built
their largest press to-date. Walter was so hard pressed
that he even had 3 or 4 draughtsmen working in his
dining room at home, in order to complete the job on
time. The hydraulically operated press was delivered to
Rubery Owen in June.
By 1916 Wilkins and Mitchell were
also producing other war work including drag lines for
artillery, fuse caps, and gear trains for tanks. The
company also machined cradles for 18lb. field guns and
for naval 12lb. anti-aircraft guns for Wolsley Motors,
at the time a subsidiary of Vickers-Armstrong. Walter
revolutionised the production by making it far more
efficient. At Vickers-Armstrong one man took 120 hours
to machine a single gun cradle. Walter reduced this time
to just 12 hours by using three men to operate machines
and jigs of his own design. This meant that 10 of the
much needed gun cradles could be machined in the time
that it previously took to do just one.
Wilkins and Mitchell also began to
produce the ‘Lightening’ car jack, which Walter had
previously designed in about 1912. He originally set his
brother George up in business to manufacture the jacks
in a small factory at Moxley in partnership with John
Richards. During the war production was transferred to
Phoenix Works.
|
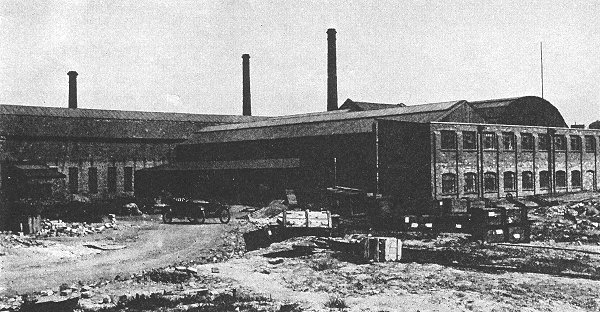
The Darlaston factory in 1917 with
Walter's Saxon car in the foreground.
After the War
The company, like many others had
greatly prospered thanks to the plentiful supply of
wartime Government contracts. Walter Wilkins realised
that the contracts would abruptly end when hostilities
ceased, and that large quantities of cheap machine tools
would be put-up for sale when they were no longer
required for war work. Something had to be found to tide
the company over until things returned to normal.
As a result he arranged to build mechanical stokers for
Vickers-Spearing, a subsidiary of Vickers-Armstrong who
had a good relationship with Wilkins and Mitchell thanks
to their work on the gun cradles. The mechanical stokers
consisted of wide endless belts that slowly revolved and
transported coal from a hopper to the furnace at one
end, then carried the burnt ash out at the other.
The contract nicely filled-in the
gap at the end of the Government orders, and provided a
smooth transition from war to peacetime work. There was an 18 month backlog of
orders to get through. At the same time new orders were
arriving, mainly for specialised drilling machines for
Railway wagon and carriage companies.
Many of the orders were for
sole-bar drilling machines, some of which were 50ft.
machines. Other orders were for hydraulic presses, used
in the production of heavy lorry chassis. |
A photograph of some of the
workers at Phoenix Works in Bell Street, in the late
1920s. The second from
the left in the middle row is John Gibbons.
Courtesy of Brian Groves. |
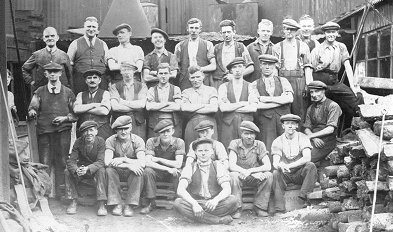 |
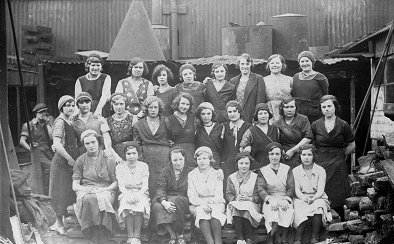 |
Another photograph taken at
Phoenix Works, possibly at the same time as the one
above.
The first lady on the left in
the middle row is Mary Gibbons.
Courtesy of Brian Groves. |
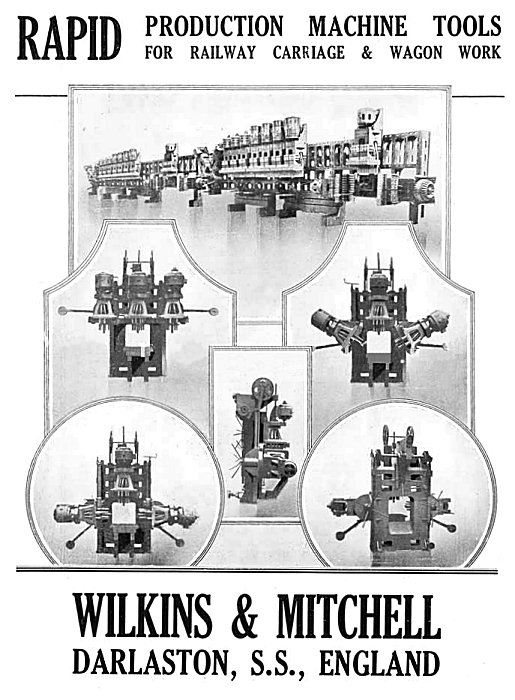
An advert from The Railway
Gazette, 22nd November, 1926. |
New
Products
Walter Wilkins was as prolific as
ever. He had a small experimental workshop at home in
which to develop new products, and even designed and
made a special drawing board for use in bed, so that if
an idea occurred to him during the night he could
instantly put it on paper. He began to develop a rotary valve
V8 petrol engine, but unfortunately never completed the
work because of lack of time. He also designed a
multi-head group drill, an early form of automated
machine tool. A number of them were sold to the
Hotchkiss Motor Company, the manufacturer of engines for
Morris.
It carried-out the complete machining of a Morris
cylinder block, and consisted of a series of
machines that were coupled together. The cylinder blocks
travelled on a track between the machines, which quickly
carried out the fifty five operations that were
necessary. The installation was one hundred and eighty
one feet long, eleven feet wide, and eleven feet high,
and powered by eighty one electric motors. It cost
around £13,500. Another of Walter's inventions was the under-drive
press.
In 1928 Walter’s eldest son, John,
joined the company as an apprentice pattern maker,
earning two pounds a week. Within a few years his three
brothers Henry, Edward, and Philip would also join the
family business. Henry
married Joyce Winn, daughter of factory owner, W. Martin Winn. Walter became interested in the
Rotarian movement and along with a few friends founded
the Rotary Centre in Wednesbury.
|
Around 1926 Walter turned his
attention to washing machines, which he considered would
be a good addition to Wilkins and Mitchell’s product
range to ensure the future growth of the company. He
founded Servis Limited in 1929 to manufacture them, and
in the
spring of 1930 took his family on a tour of the
U.S.A. While there he visited several factories
including a couple that made washing machines. When the
family returned home the Wilkins boys attempted to
perfect their prototype washing machine. They had
initial problems with the drive, but once they had
successfully tried a ‘V’ belt, they were on to a winner. The new machine was launched at the
Ideal Home Exhibition and the Preston Agricultural Show.
By that time Walters’s sons Henry and Edward had joined
the company and greatly assisted in selling the machines
at exhibitions.
During the recession in the 1930s
the washing machines helped the company to keep going.
The demand for machine tools fell and so workers from
that part of the business were temporarily used to
tool-up for mass production of Servis washing machines. At the
height of the recession the company made a small loss,
but still managed to keep going. |
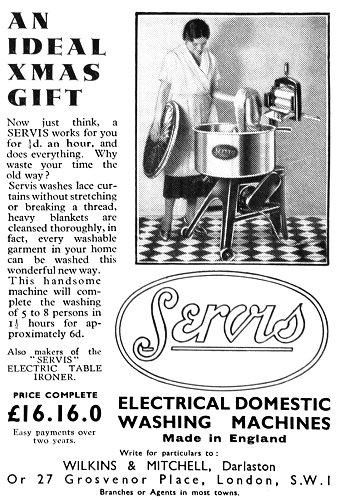
An advert from 1934. |
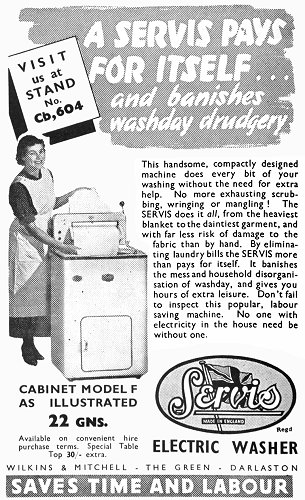
An advert from 1938. |
The first Servis machines were built using the stock
of unsold machine tools in the factory, and the Model
‘A’ soon appeared. It was quickly followed by the
improved Model ‘B’ which sold extremely well.
The first cabinet machine, the forerunner of present
day machines, was the Model ‘E’. Like its predecessors
it sold well, and assured the future of the company.
A separate department was soon set-up where the
machines were repaired by skilled mechanics who were
specially trained to work on the whole range of Servis
machines.
By the late nineteen thirties the depression had
ended, and manufacturing flourished. Heavy presses and
washing machines were produced in adjoining bays, and
newly designed blanking and drawing presses were first
tested on the Servis production line. |
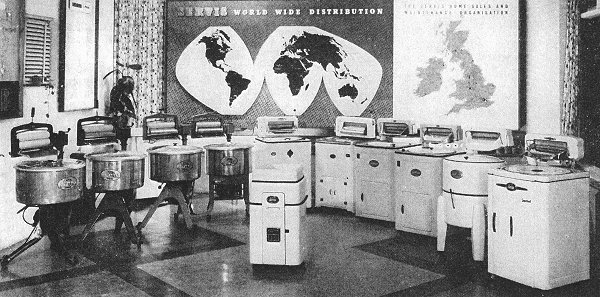
The Servis museum showing a display of
early and later machines.
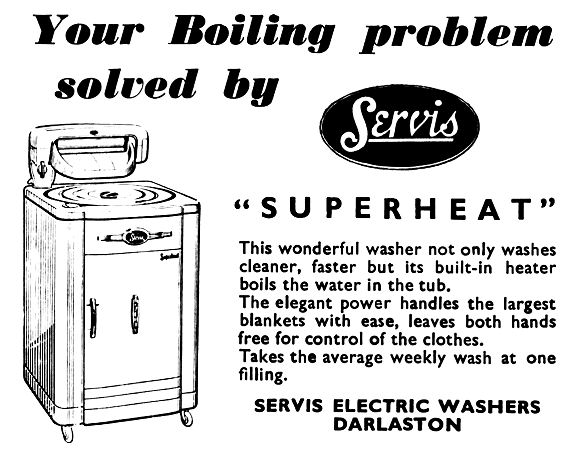
An advert from the mid 1950s. Courtesy of
Christine and John Ashmore.
At the beginning of the Second
World War washing machine production was turned-over to
the manufacture of ammunition boxes, while the heavy
tool division concentrated on building extrusion presses
for armaments, and a variety of specially designed
machines for ordnance factories.
At the end of hostilities when the
war contracts were being wound-up, and the production of
washing machines began again, Walter Wilkins was taken
ill. He was in his seventieth year, and his doctor
advised him to take things easy. Being a
workaholic made this an impossibility. He had boundless
energy and an active mind, and carried-on regardless,
working tirelessly until his death in September 1946. |
After his death, his widow Louisa Wilkins took over
the running of the company. A position she held for many
years until failing health forced her to retire.
The company was then managed by her four sons, John
C. Wilkins who became Chairman, Henry R. Wilkins and
Edward W. Wilkins who became joint Managing Directors,
and Philip A. Wilkins, Works Director.
They were joined on the Board by two non-family
members, A. F. Gadsby, Financial Director, and A. T.
Thorley, Sales Director. |
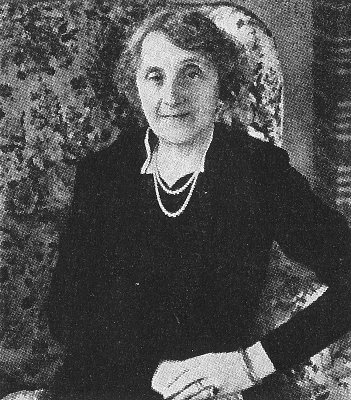
Louisa Wilkins. |
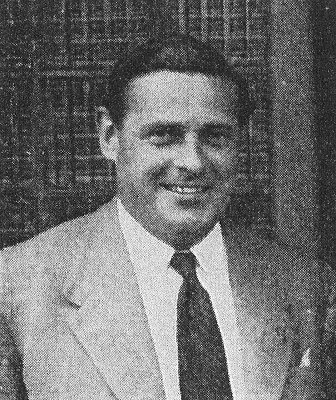 |
|
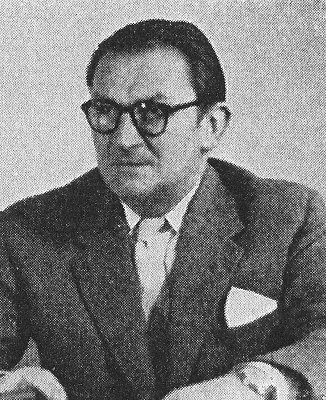 |
Mr. Edward W. Wilkins. |
|
Mr. Henry R. Wilkins. |
|
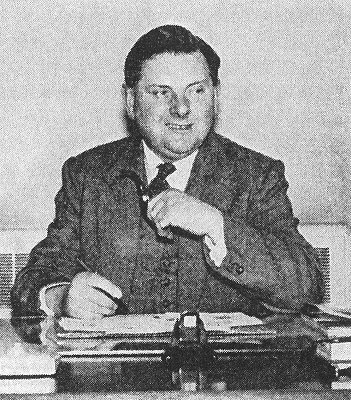 |
|
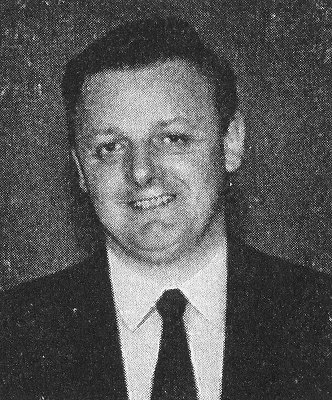 |
Mr. John C. Wilkins. |
|
Mr. Philip A. Wilkins. |
|
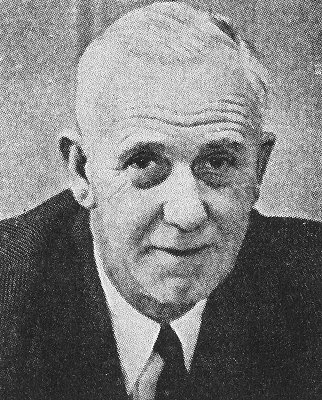 |
|
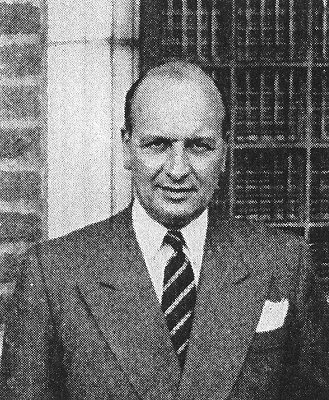 |
Mr. A. F. Gadsby, F.C.A. |
|
Mr. A. T. Thorley. |
|
Under their control the business continued to grow.
The machine tool division no longer took orders for
special machinery, but was devoted to the design and
production of power presses. New plant was installed for
the purpose, and factory extensions were built. In 1947
the company’s products were exhibited for the first time
at the British Industries Fair, and the following year
at the Canadian Trade Fair. Many new orders came as a
result of the exhibitions, and from then on Wilkins and
Mitchell’s presses and washing machines would be seen on
display at many trade fairs, both at home and abroad. |
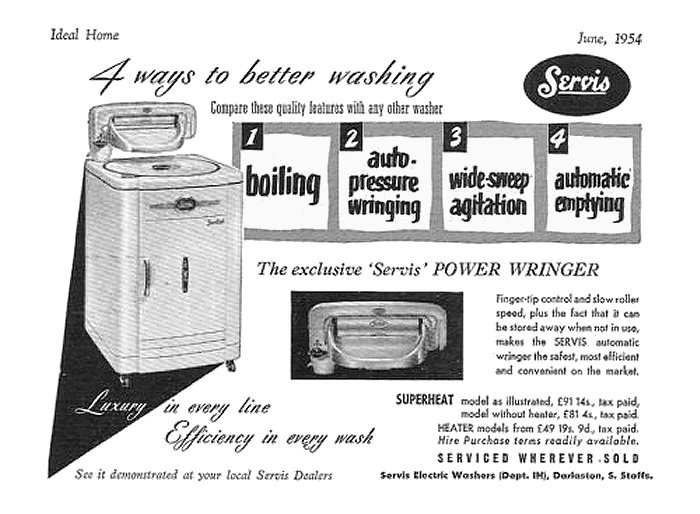
An advert from 1954. |
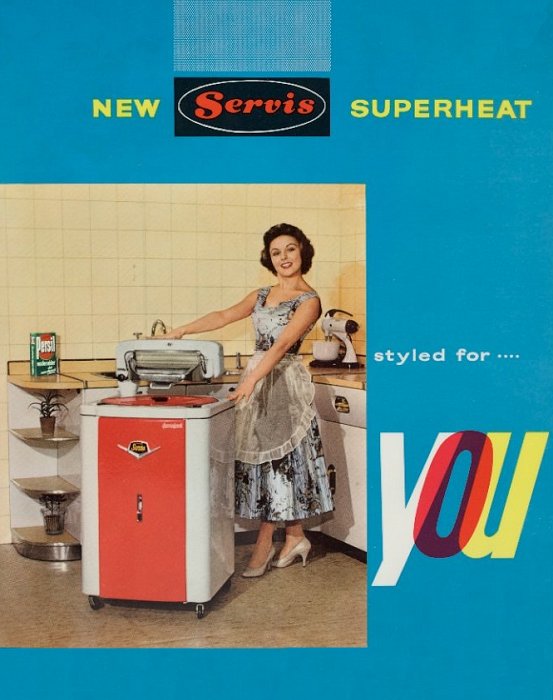
An advert from 1955. |
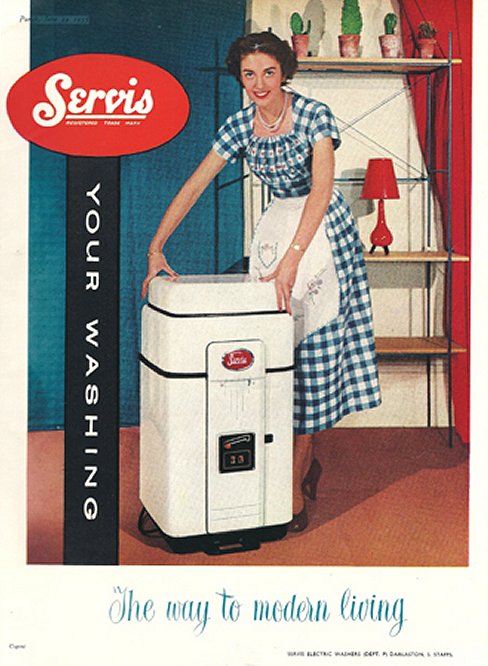
Another advert from 1955. |
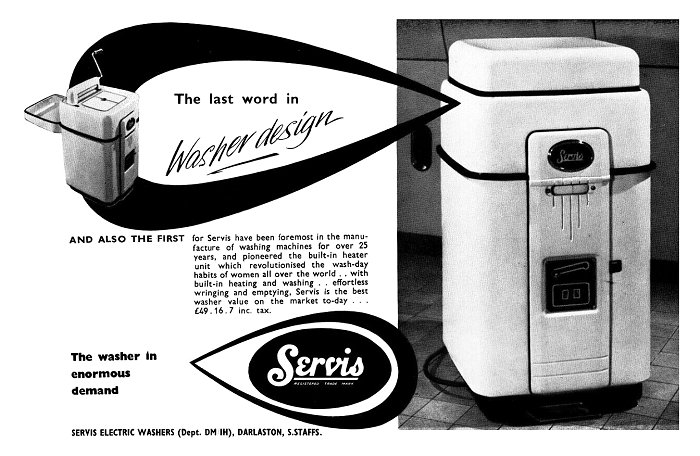
An advert from 1956. |
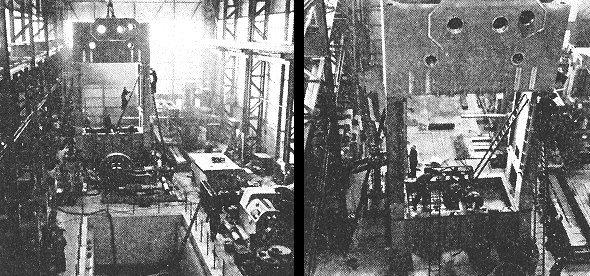
Presses under construction in the Machine
Tool Assembly Bay.
In the late nineteen forties washing machine
production suffered from the nationwide shortage of
sheet steel. In order to meet the growing demand the
company designed the Servis Model ‘R’, built from the
available steel strip. Many thousands of Model ‘R’s were
produced and sold at home and abroad. Sales were so good
that the model remained in production for many years. In
order to qualify for an increased allocation of sheet
steel, the company extended its overseas market and
designed a new machine with all the latest features,
which would appeal to foreign dealers, and compete well
in the highly competitive market. |
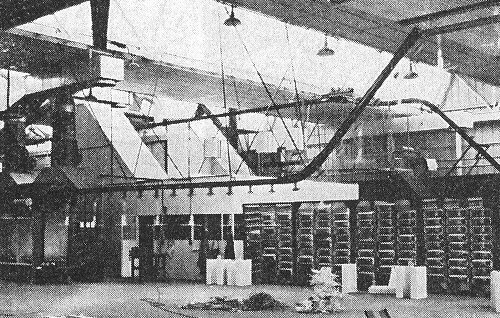
The air conditioned spray plant at
the Servis factory. |
Because of the company’s growing sales, more staff
were needed and new offices were built to accommodate
them. By the early nineteen fifties space in the
factory was in short supply. Production had rapidly
increased and so a new Servis factory was built at
Darlaston Road, King’s Hill for the production of
washing machine parts. |
The Servis Sales Training wing and the Servis
Development Department moved to a new building in the
grounds of the Hollies, in Wednesbury, the former home
of the Wilkins family.
The house itself was converted into offices for the
Servis Sales Administrations staff. |
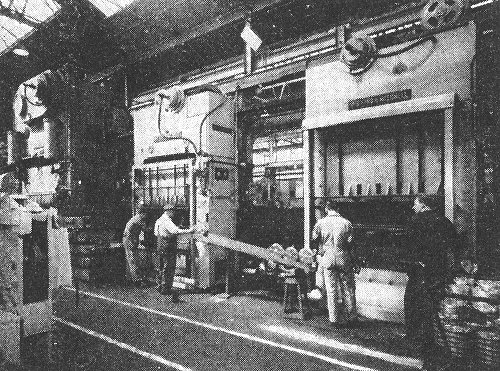
Part of the Servis Press Shop. |
Memories of Wilkins
and Mitchell Derek Thorley, who was born in October
1938 in Herberts Park Road, worked for the company.
After leaving Slater Street School in the early 1950s,
he joined Wilkins and Mitchell as an apprentice
engineer, and attended Wednesbury Technical College as
part of the company's day release scheme. He initially moved around
the factory, and worked in several departments to gain
experience.
When he joined the firm, there was no official
apprenticeship scheme. Around two years later he joined the
company's apprenticeship
scheme when it was introduced. The
scheme, run by training supervisor William E. Howells
(Billy), was based in an old electricity sub-station
building in Victoria Road, which is now occupied by the
4th Darlaston Scout Group. The building had previously
been used by Wilkes the printers, and the Wilkins and
Mitchell stationery stores. The firm installed a range of
machinery in the building, on which to train the
apprentices. William Howells arranged factory visits to
many firms including Rubery Owen, Cadburys, and Chubbs.
During his final year as an apprentice, Derek worked in
the Servis
development department at the Hollies, which was
managed by Derek's uncle, Vince Thorley, and consisted of
an engineering workshop for building prototype
machines, and a test lab for testing component
parts. He also worked in the drawing office, run by Bob
Peach, which was above the development department.
Derek left the company in 1961. |
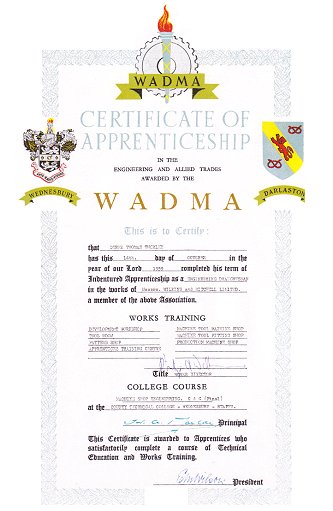 |
Derek Thorley's certificates that he obtained during
his time as an apprentice at Wilkins and Mitchell..
The one on the left was awarded when he completed his
apprenticeship as an engineering draughtsman in October
1959. He had trained in the development workshop, the
tool room, the pattern shop, the machine tool machine
shop, the machine tool fitting shop, the production
machine shop, and the apprentice training centre.
The two certificates below are his City and Guilds final
certificate in Machine Shop Engineering, and his
Ordinary National Certificate in Mechanical Engineering,
both awarded after attending courses at Wednesbury
County Technical College.
The bottom two certificates were presented at the
beginning and end of his apprenticeship.
During his apprenticeship he also helped out on the
production lines at the Kings Hill Servis factory, known
as No. 2 factory.
Derek greatly enjoyed his time as an apprentice and
has fond memories of his time there. |
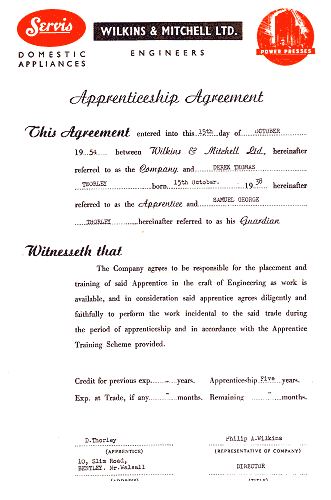 |
|
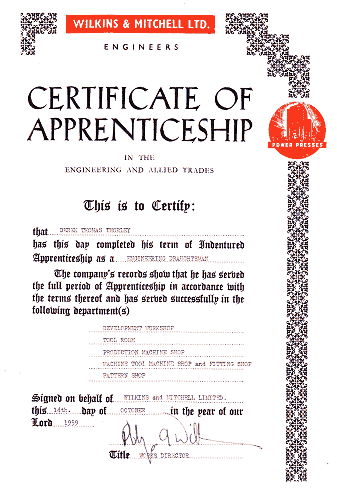 |

A group of Wilkins and Mitchell apprentices on a
day out to Cheddar Gorge in about 1955. The names
are as follows:
Back row left to right:
?, Patrick Turley.
Front row left to
right: Brian Rutter, Brian Proffit, Brian
Harrison, Graham Sheffield, Brian Jackson, Anthony
Dean, Charles Dickens, and Keith Amos.
Photo and names courtesy of Derek Thorley and
Anthony Dean.
|
Later Years
New extensions were built to the
power press factory at Darlaston including an assembly
shop with a crane capacity of one hundred tons. The
giant power presses could for the first time be entirely
built at the factory, rather than using sub-contractors
for some of the work.
Wilkins and Mitchell presses became
well known and respected throughout the world. Single
and double action presses were produced for a wide range
of industries including the motor industry, the forging
industry, the aircraft industry, and the domestic
appliance industry. The special machinery for the
forging industry included billet shears, forging rolling
machines, high speed forging presses, and clipping and
setting presses. The company’s presses also
revolutionised the hot brass stamping industry with a
specially designed sub-press, capable of producing
multi-cored components in a single operation at a much
higher production rate than had previously been
possible.
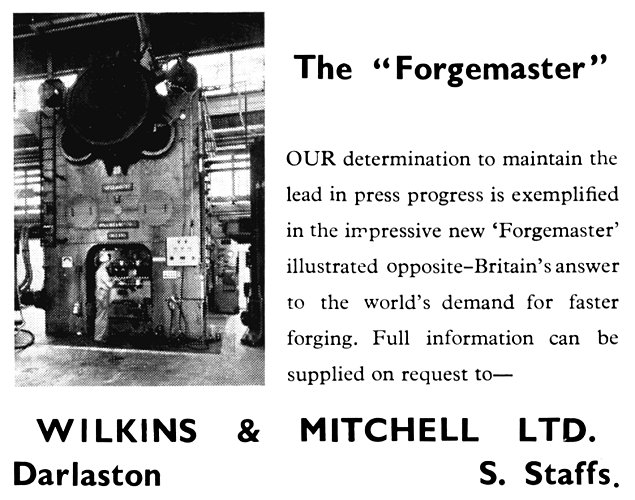
An advert from the mid 1950s.
Courtesy of Christine and John Ashmore.
Presses from 100 tons to 6,000 tons
were built at the Darlaston factory, where a team of
highly skilled mobile service engineers were based to
carry out all, except major overhauls on the company’s
presses. Wilkins and Mitchell always ensured that
“down-time” on their products was reduced to a minimum.
A modern London office was opened
in Park Lane where a display of Servis washing machines
could be seen. The premises also housed the Power Press
Export Section. The overseas market was extremely
important to the company. The Wilkins brothers regularly
visited overseas agents and kept them informed of the
latest developments. In the nineteen fifties an
agreement was made with an Australian company for the
manufacture of Wilkins and Mitchell power presses under
license. |
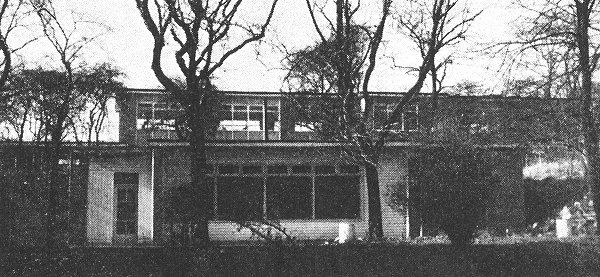
The new building in the grounds of The
Hollies.
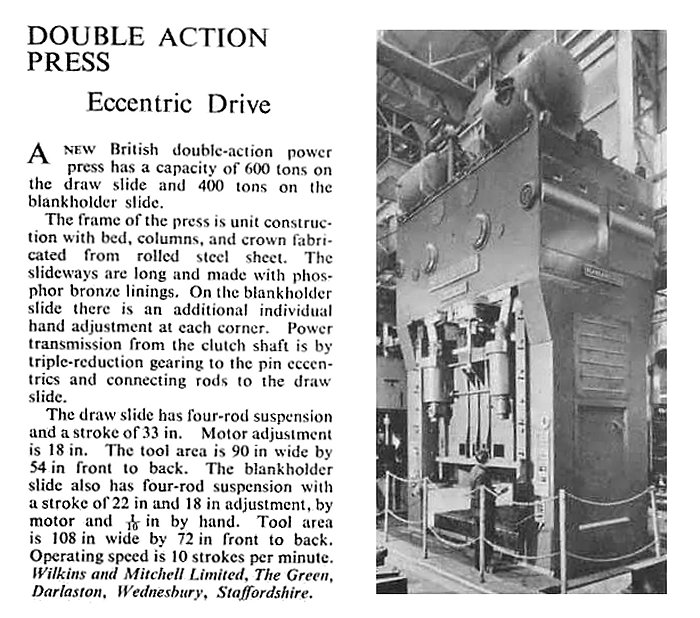
An advert from 1960.
By the 1960s thousands of Servis
washing machines were made each week. There were over
300 mobile mechanics, whose Servis vans became a common
sight on British roads. They were supplied from twenty
one regional depots throughout the country. The Servis
personnel covered over three million miles annually to
support the company’s claim that Servis washers were
serviced wherever they were sold.
A subsidiary company called Wilkins
Servis was set up to manufacture washing machines in
Australia, and there were distribution companies in
Switzerland and Belgium, and a network of agents
covering fifty overseas markets.
The long standing apprenticeship
scheme was reorganised with the opening of a fully
equipped training school. A company newspaper with a
circulation of 12,000 copies was published twice a month
and sent to all employees, dealers, and power press
customers. The company celebrated its golden jubilee in
October 1954 and became a public company with about
thirty percent of the ordinary share capital for sale.
For the jubilee celebration, the company hired the Civic
and Wulfrun halls in Wolverhampton, and laid-on coaches
to get the employees there. There were staff from all
over the country who enjoyed a dance with a live dance
band, and entertainment featuring Tommy Cooper and a
roller skating duo. In the late
1950s a large piece of land was purchased at
King’s Hill next to the existing factory, for an
extension to the factory and the building of a new
office block. At the same time development of what was
to be another successful product, the Servis ‘Super
Twin’ began. The Servis machines were at the expensive
end of the market along with such names as Bosch, and
gained a high reputation for reliability. |
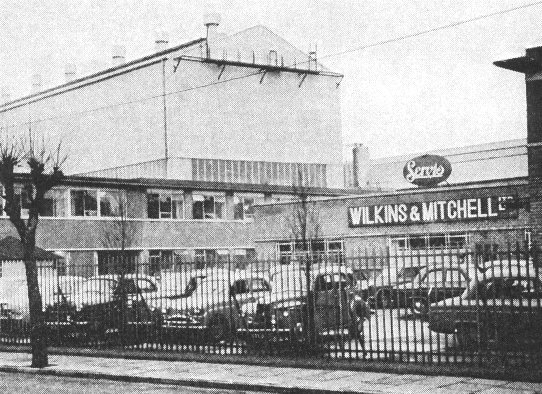
The front of the factory with the
large press shop assembly bay in the background. |
The 1960s were good years for the company, sales
remained high, and new products were developed.
Unfortunately things started to go wrong in the
recession during the late 1970s.
Orders were few and far between, which resulted in
the business going into receivership in the early 1980s. |
In 1982 the
newly formed UK manufacturing group, Verson
International run by American businessman Tim Kelleher
acquired Wilkins and Mitchell from the receiver.
The group’s main companies were Wilkins and Mitchell,
and Bronx Engineering of Lye, who were acquired in 1986.
By the late
1980s group sales were approaching £40 million and a
good future seemed ensured. In 1987 profits were
£750,000, compared with £176,000 in 1986, and this
steady growth continued for some time.
Tim Kelleher
removed the barriers between the shop floor and the
management team. He believed that the company’s main
asset was the skilled workforce. Director’s dining rooms
were closed, their privileges were removed, and all
non-essential company cars were sold. A manager could
loose his job if he didn’t know every employee by his or
her first name. |
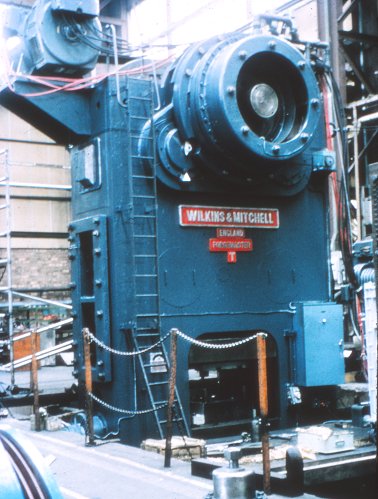
A hot forging machine. |
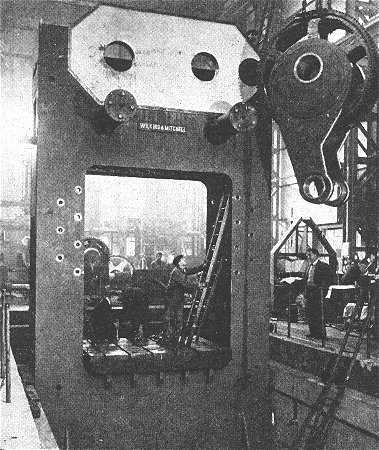
The bull gear and eccentric being
fitted to a 1,500 ton press. |
At Darlaston the
group planned to build a new larger factory for Wilkins
and Mitchell on a 15 acre site in Willenhall Road,
formerly occupied by Wellman Cranes. The existing
Richards Street works would house a new specialised
fabrications company.
The new factory
with a workforce of nearly 300, cost £6 million and was
opened on 28th November, 1990 by John Major. The company’s Managing Director
was George Paxton, who previously ran Verson AI in
Inverness.
The company name
changed to Verson Wilkins, and by the end of 1990 orders
for power presses reached nearly £7 million. The orders
included a huge 2,650 tonne trimming press for a forge
in Lincoln, the largest power press built by the company
at that time. Many of the orders that followed were for
vehicle manufacturers, including Nissan at Tyne & Wear;
A.C. Rochester who were part of General Motors; and a
huge 3,000 tonne “try out” press for Toyota. |
Unfortunately
the fortunes of UK car manufacturers were on the wane
and orders fell. By the middle of 1993 Verson
International was £3.5 million in the red, not helped by
a very significant loss at Verson Wilkins. As a result
the group merged with Clearing UK and reduced its
product range. The Darlaston subsidiary now became known
as Clearing International. In November, 1994 about 70
jobs were shed at Darlaston and the future looked very
uncertain. Quite a stir was caused in the works in
December of that year when the factory became the
location for the American film crew who were shooting a
film about the Iraqi super gun entitled “The Doomsday
Gun”.
In 1995 about
half the employees lost their jobs at the Darlaston
factory when the workforce was greatly reduced. At the
time they were producing presses from 300 to 1,500
tonnes as standard, and up to 2,500 tonnes to special
order. The company also refurbished their old products.
By 1996 the deficit amounted to £5.8 million and the
group decided to sell Darlaston based Clearing
International. The Darlaston company then formed a
partnership with Scarborough based Bootham Engineering,
but the downturn in the motor manufacturing industry
continued and the decision was taken to close the
Darlaston factory.
|
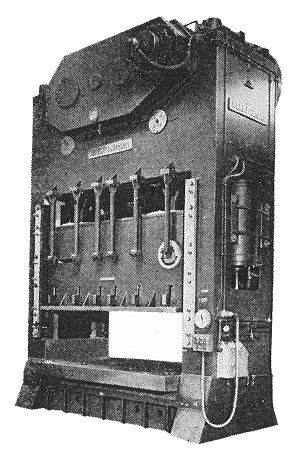
A T.R. Series blanking and drawing
press. |
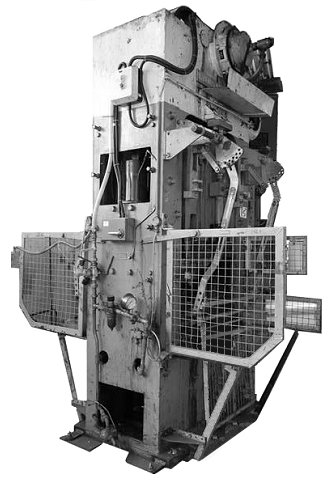
A 300 ton double sided power press. |
As a result the factory closed,
with the loss of 64 jobs, on 2nd April, 1999. Another nail in the coffin
for Darlaston’s manufacturers, who were once known
throughout the world for their quality products. The story doesn't quite end there. After the closure of
the Darlaston works, Bootham
Engineering moved its offices to Bloxwich.
In
2003 the company was taken over by Muller Weingarten UK
Limited, and in October 2005 the company moved to
Quayside Drive in Walsall.
In March 2008, Muller
Weingarten UK Ltd and Schuler UK merged to form the new
company Schuler Presses UK Limited. The company services
and supports Wilkins and Mitchell presses. |
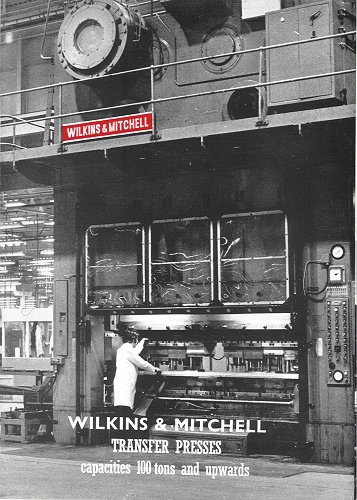 |
|
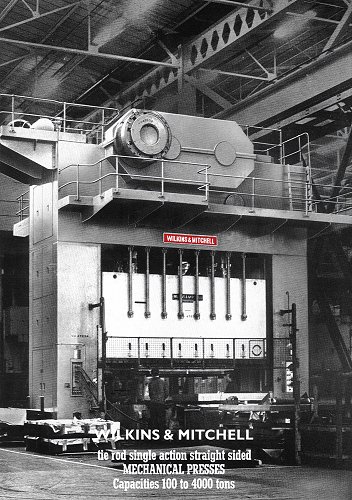 |
Courtesy of Mark Foster. |
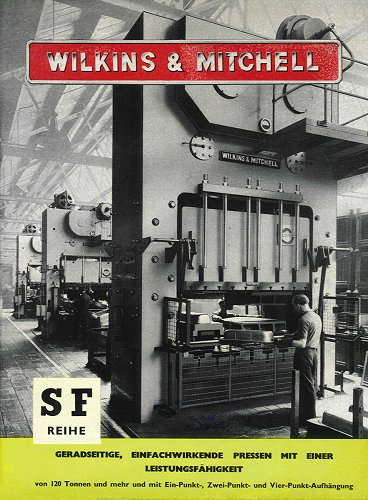 |
|
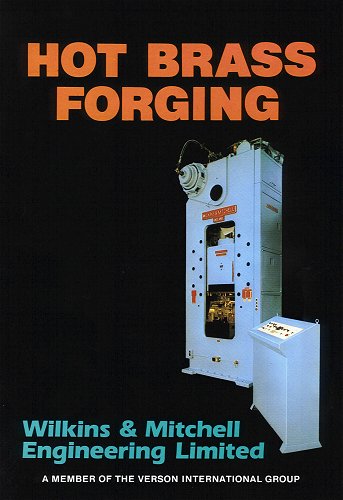 |
Courtesy of Mark Foster. |
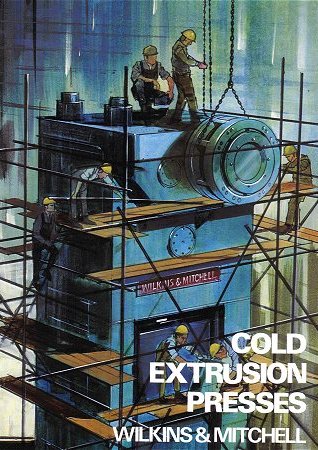 |
|
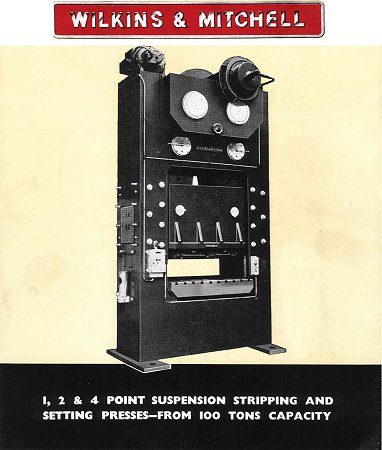 |
Courtesy of Mark Foster. |
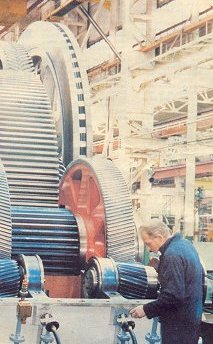
Assembling a gearbox for the Cable
Belt Company in the 1980s. |
|
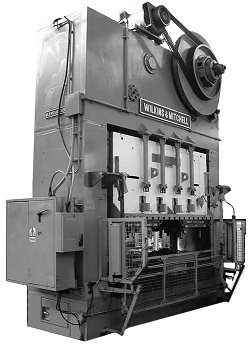
A Wilkins and Mitchell large power press. |
|
Wilkins and Mitchell's other factory, Servis at
Darlaston Road, King's Hill had been extremely
successful until the early
1980s.
In the early 1980s they produced the first
washing machines in the world to use microprocessor
control, in the successful "Quartz" range.
The company
got into difficulties during the recession and went into
receivership. In July 1982 it was acquired by Centreway
Industries, which saved over 1200 jobs. In 1983 there
was a huge fire on part of the King's Hill site that
caused much damage.
The company went into receivership a second time in
1985 and was purchased by the Gooding Group in April
1985, with
assistance from the West Midlands Enterprise Board,
which provided £750,000 towards the purchase. 400
of the 600 workers at the factory were then able to return to
their jobs.
In December 1987, the Gooding Group decided to sell
the business, which had failed to rise to expectations
and acquire a large enough share of the British market,
even though there were annual sales amounting to £30m. |
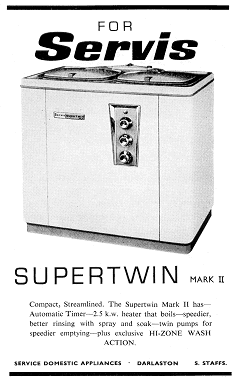
An advert from 1963. |
There was a management buyout led by Graham
young and Kevin Moat, each owning 44.5 percent of
the company. Graham young was Managing Director and
Kevin Moat was Sales Director. They hoped to expand
their sales in Germany and Belgium. Unfortunately
things didn't work out as planned and in March 1989
the business again went into liquidation.
A new
company, Servis UK was formed in November 1990 and
purchased by Antonio Merloni in 1991. Manufacturing ceased at the
King's Hill factory, which became a spare parts centre,
and dealt with repairs.
In 1995, the workforce was greatly reduced, and
about half the employees lost their jobs. The
factory closed in October 2008, by which time there were only 50
members of staff. Sadly, the factory was demolished in
2011, and by
April of that year it had completely disappeared. It was
a tragic end for a Darlaston company that was once the largest local
employer, producing high quality products that were well
respected and well known, almost everywhere. |
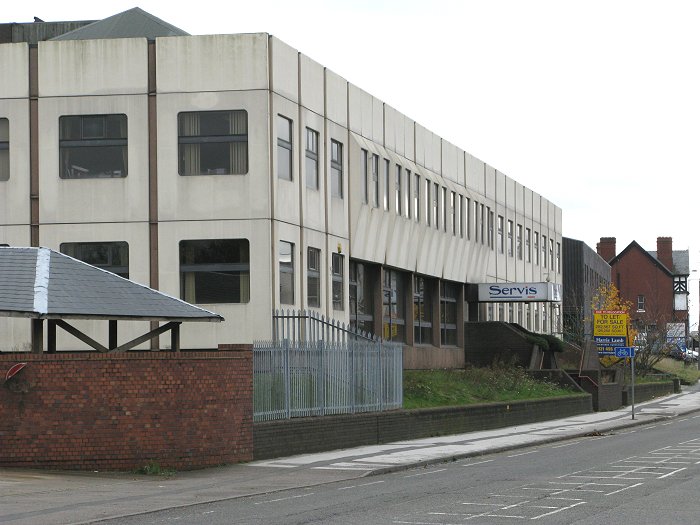
The empty Servis factory in November 2008.
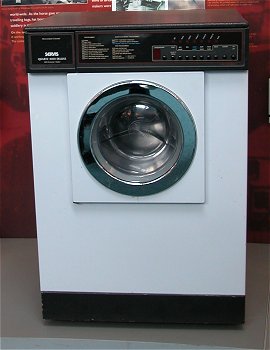 |
The Servis Quartz 1000 Deluxe
microprocessor controlled machine that's on display at
the Black Country Living Museum, Dudley. |
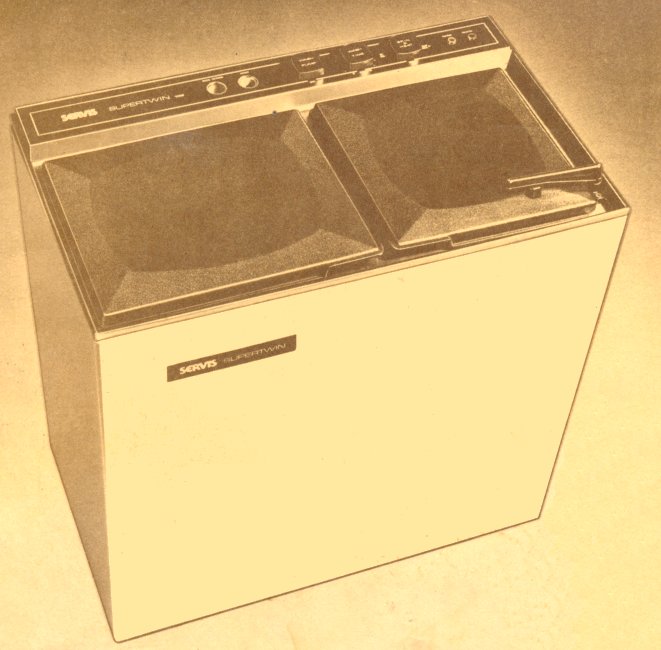
The Servis Supertwin 108. |
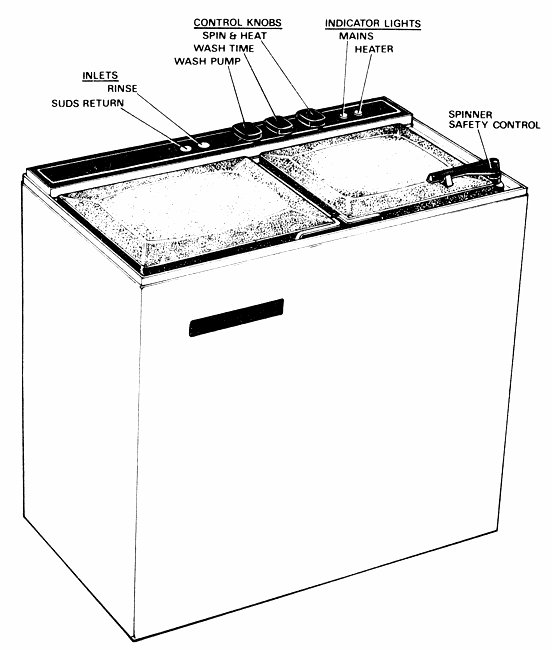
Another view of a Servis Supertwin
108 showing the controls. |
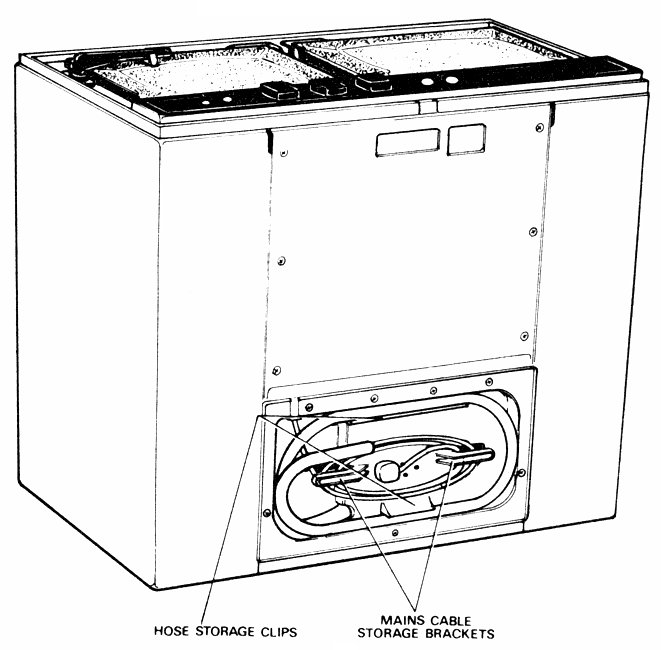
A rear view of a Servis Supertwin
108. |
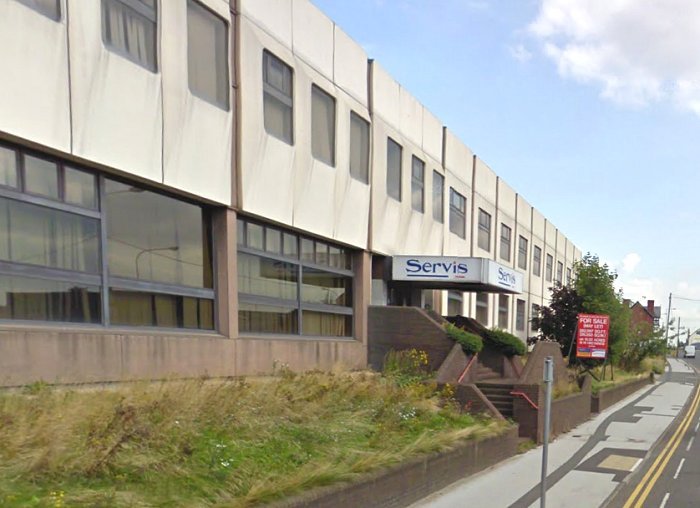
The empty factory in 2009.
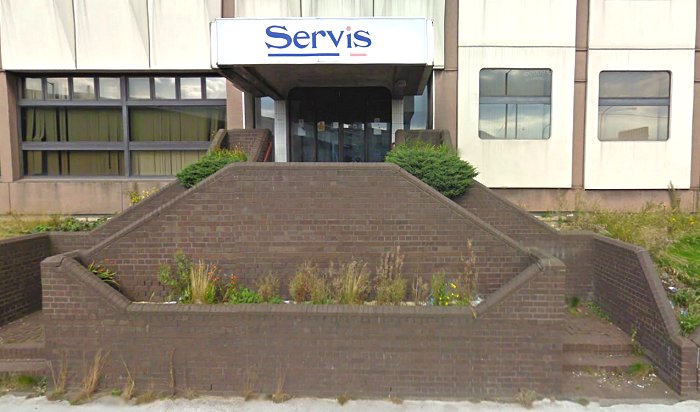
The main entrance in 2009.
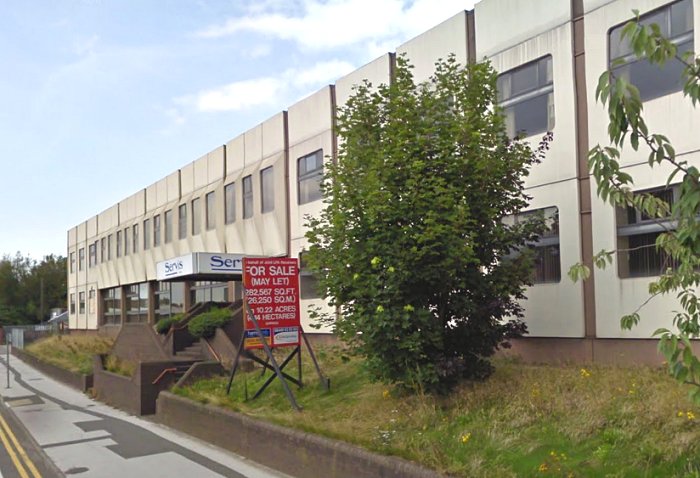
Another view from 2009.
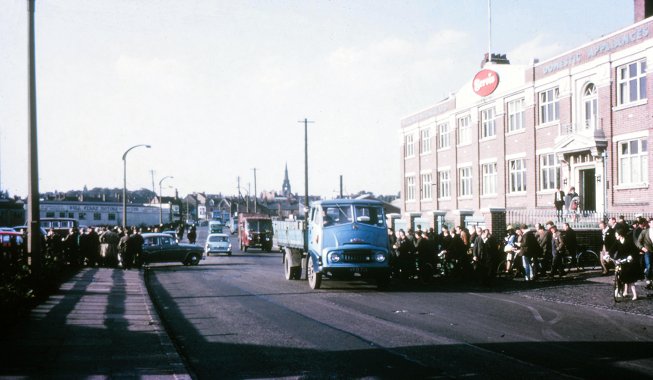
The Servis factory in the 1960s.
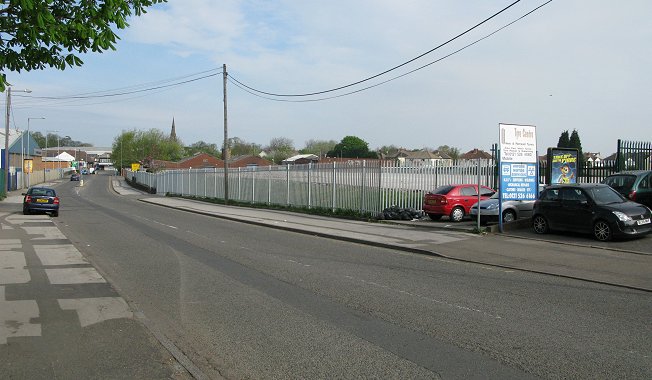
The same view in April 2011.
All that remained of the Servis factory in
April 2011.
I would like to thank Mark Foster of Schuler Presses UK Limited for
his help in telling this story. He kindly provided the information
about the company up to the Second World War, and many of the
illustrations. I would also like to thank Bill Rayson who worked at
the company for 36 years,
who also worked there, and Peter Richards who supplied a lot of
information.
 |
Return to
the
previous page |
|