The Wellman Smith
Owen Engineering Corporation Limited |
The business was founded in 1919 to acquire a major
share of the American company, Wellman-Seaver and Head,
steel works engineers and contractors; and also James
Smith Hoisting Machinery Company Limited, specialists in
dockside cranes and hoisting machinery.
The new corporation also took over the engineering
department of Rubery Owen. Mr A. E. Owen was chairman.
It became a public company in 1924, and had a number
of factories in the UK, including the one at Darlaston.
At this time the company introduced a range of coke oven
machinery including a coke charging car, and a combined
coke pusher, coal leveller, and door extracting machine,
the first of its kind in the country.
During the Second World War the company manufactured
shell forging machines, bridge laying equipment, cranes,
and shot furnaces.
The firm's shell forging machines were used in
Australia, Canada, India, and the USA. The machines
could produce in excess of 350 anti-aircraft, 3.7 inch
shell forgings an hour, and produced around 80 million
shell forgings during the war, using over two million
tons of steel.
Other war work included the production of machinery
for the Mulberry harbours, and the Pluto pipeline, and a
large number of steel smelting furnaces, and gas
producers.
|
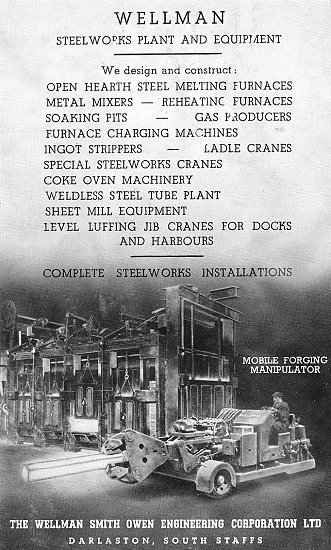
An advert from 1946. |
A highlight for the staff was the annual Whitsun
works outing, which began in 1947. Several hundred
people consisting of staff and family members would
board a special train at James Bridge Station for the
journey to seaside resorts such as Blackpool, and a
four-day stay at a holiday camp. A minimum of three
hundred people was needed in order to book the special
train.
On one occasion 550 people went on an outing to
Middleton Towers holiday camp, and greatly enjoyed their
holiday. The outing was organised by the Fitting Shop,
and linked to the Darlaston shilling-a-week football
sweep. Funds from the sweep were shared out before the
outing. Fitting Shop foreman Mr. Ernie Ramsbottom ran
the fund for many years.
In December 1955 the Falls Foundry Engineering Works
in Belfast was acquired by the Wellman Smith Owen
Engineering Corporation, Limited. The factory consisted
of machine shops, erecting shops, a foundry, and
administrative buildings. The business was acquired to
provide increased manufacturing capacity, and to take
advantage of the plentiful supply of labour in Belfast,
and the financial assistance provided by the Government.
The completely new range of heavy and medium
engineering products that the factory was called upon to
produce involved a considerable amount of retraining of
the existing labour force, which proved adaptable and
co-operative.
|
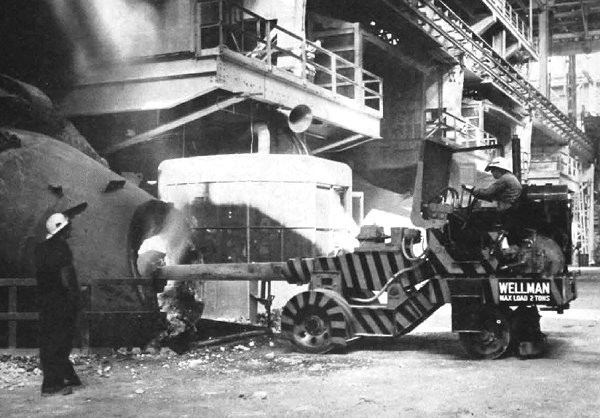
A Wellman 2 ton mobile, bar-turn,
furnace box-charging machine. |
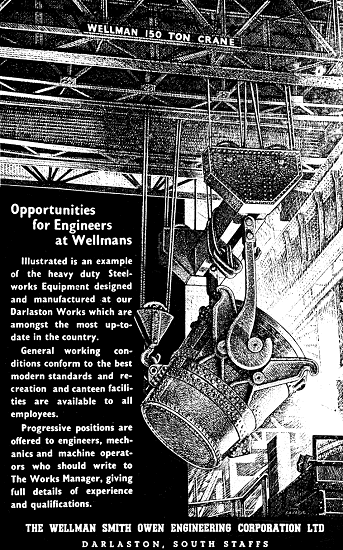
An advert from the mid 1950s. Courtesy of
Christine and John Ashmore. |
To provide for the training of future personnel, an
apprenticeship scheme was established, and in order to
provide increased efficiency, and to deal with the
expanding demands on the Belfast establishment, the
engineering shops were modernised and almost completely
re-equipped with modern machine tools.
The factory concentrated on the production of the
lighter products in the Wellman range, such as
mechanical handling and processing units for the
production of steel strip, mobile charging and handling
machines, air control valves and component parts for the
heavy steel works equipment produced at the main works
in England. Typical of this equipment is the 2-ton
mobile bar-turn furnace box-charging machine shown
above, which was supplied to the Steel Company of Wales.
This machine is driven by a diesel engine and all of its
motions are hydraulically operated.
In August 1965 the firm's name was changed to the Wellman
Engineering Corporation, which consisted of five main
subsidiaries, including Wellman Machines Limited, and
the Wellman Incandescent Furnace Company, both based at
Darlaston.
The Darlaston factory closed in the 1980s and was
acquired by Wilkins and Mitchell.
Wellmans had
a London office in Victoria Station House, Victoria
Street, SW1, and offices in Australia, France, Holland,
Italy, New Zealand, South Africa, Switzerland, and
Turkey. |

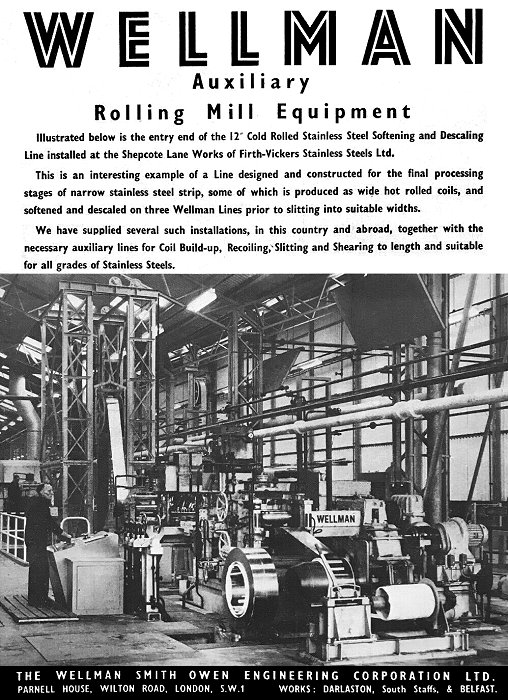
An advert from December 1960.
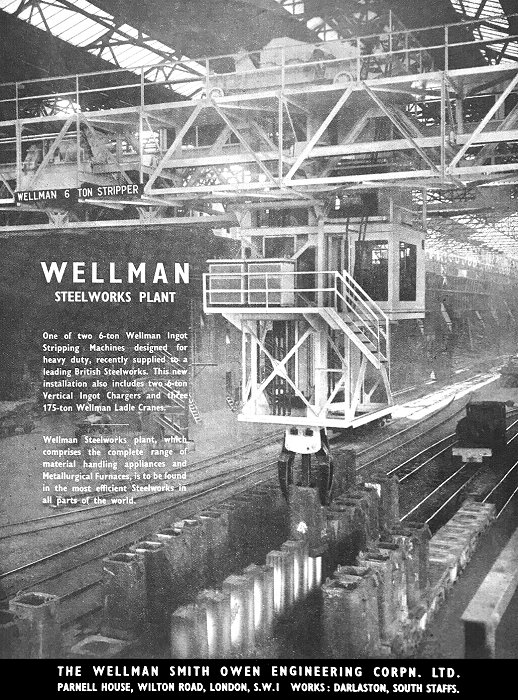
An advert from May 1953.
Some of the Company's
Products Cranes:
Docks and harbours |
The Wellman patent level luffing jib cranes were the
first British post-war dockyard cranes to be supplied to the
French Government for re-equipping ports devastated during
the war. They were supplied to the ports of Brest, Bizerta,
Cherbourg, Dakar, Le Havre, Lorient, Marseilles, Oran,
Rouen, and Toulon, and were also supplied to other countries
including Russia. |
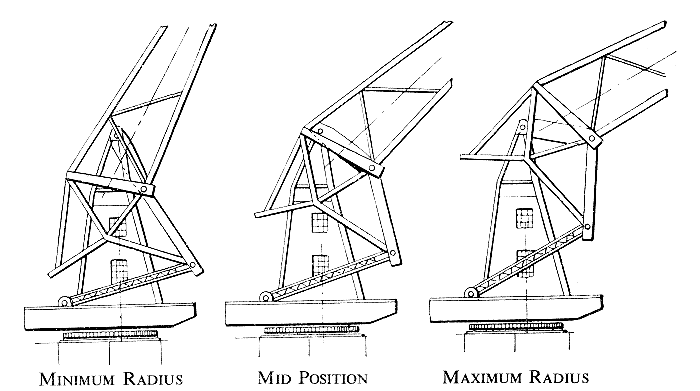
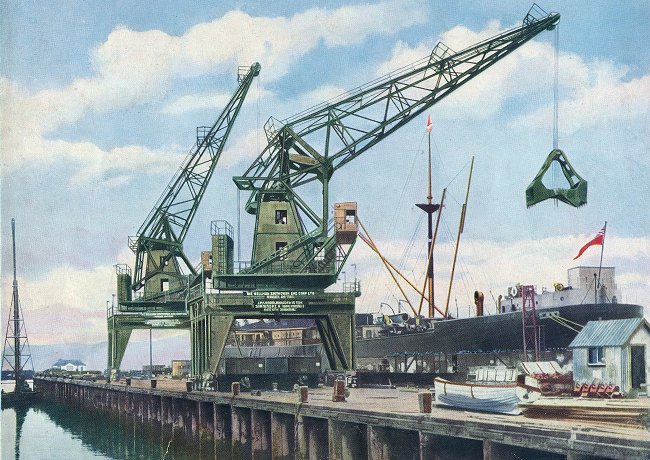
One of the cranes in action.
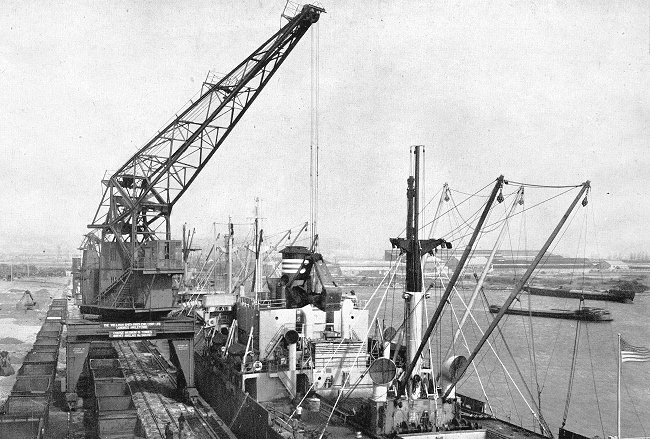
A wellman crane in use at Le Havre.
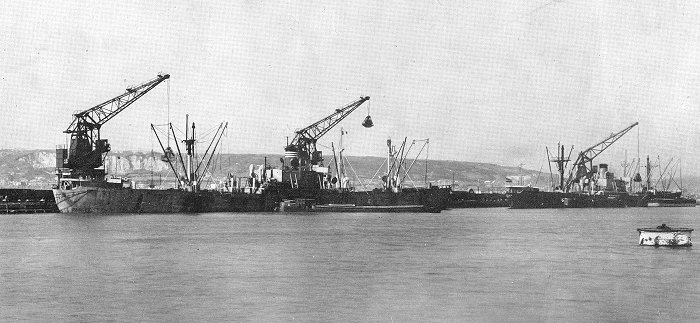
Three of the cranes working at Le Havre.
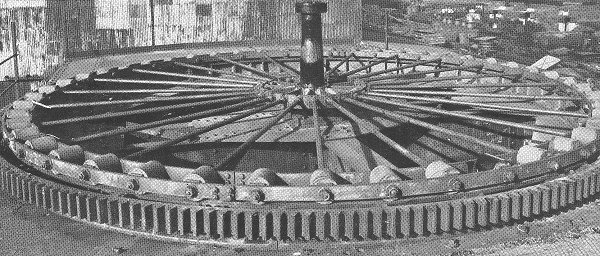
The roller path and centre pin.
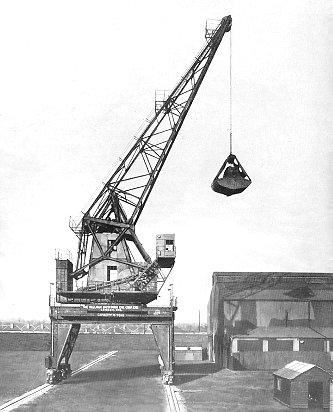
A Wellman Smith Owen level-luffing
jib crane. |
The level luffing crane opposite uses the
company's patented gear which ensures that the hook remains at the same level whilst moving
the jib up and down. This crane was designed for the handling of
coal or iron ore, and could deal with loads of up to 15
tons.
It was electrically operated and ran on 10.5
metre-wide track. With ballast it weighed around 240
tons, had a hoisting speed of 35 metres per minute, and
could travel on the track at a speed of 35 metres per
minute. There were two 75 BHP. Metrovick motors, each
of which drove a winch. One of the winches raised and
lowered the grab, the other opened and closed it.
|
The superstructure of the
crane. |
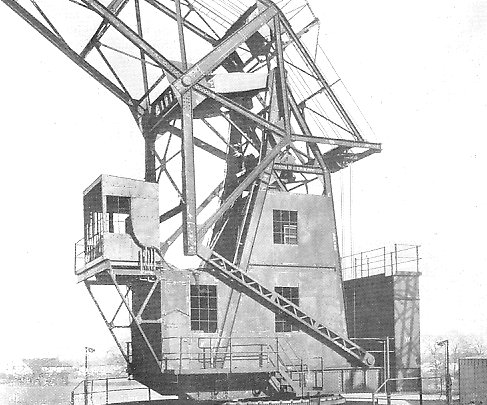 |
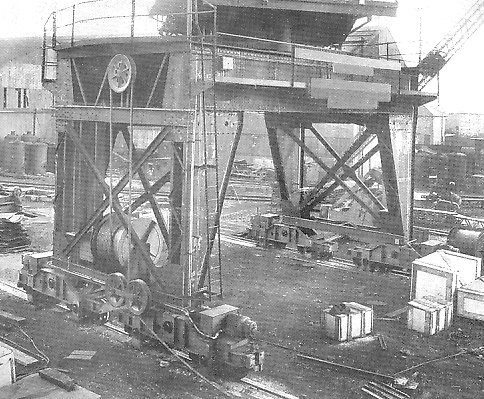 |
The crane legs and the
self-reeling drum for the power cable. |
The crane was operated from a 3-phase 380 volt, 50
hertz supply, to which it was connected via a 60 metre
length of trailing C.T.S. flexible cable. The cable was
automatically payed-out and taken-up as the crane ran
along the track, by means of a weight-operated
self-reeling drum. Five 1kW heaters were fitted so
that the cranes could work in low temperatures. Three
were in the machinery house, and two in the operator's
cabin. |
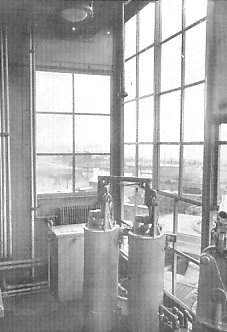
The operator's cabin. |
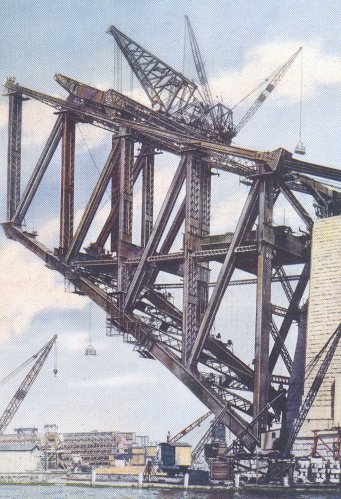 |
|
 |
One of the two
122 ton capacity Wellman creeper cranes that were
used in the construction of Sydney Harbour Bridge.
|
|
One of the two Wellman
crane assemblies used in the construction of the
Howrah Bridge at Calcutta. Each crane had a capacity
of 60 tons. |
|
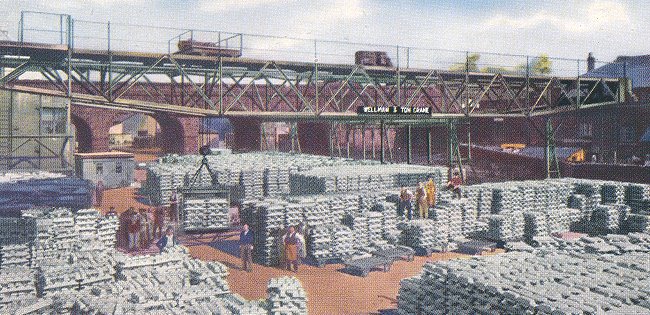
A 3 ton Wellman electric overhead travelling
crane with a 91 ft. span.
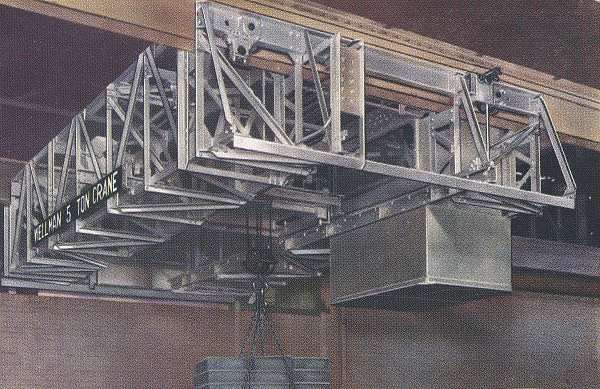
A 5 ton Wellman underslung overhead travelling
crane.
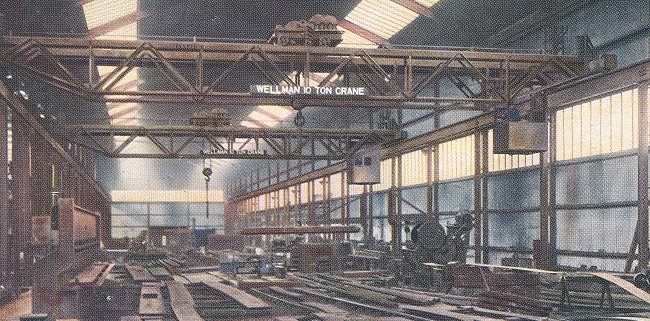
A standard Wellman 10 ton overhead travelling
crane.
Charging and discharging
machines for steelworks: |
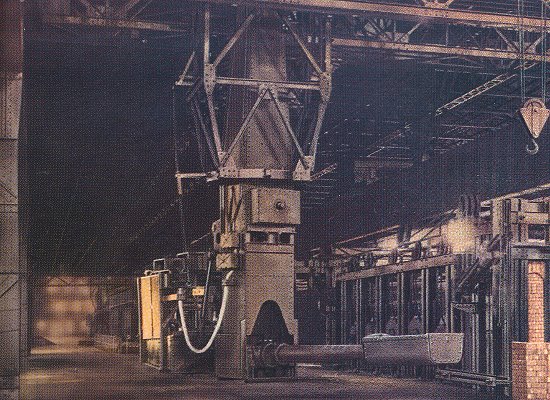
An overhead revolving charging machine for
open hearth furnaces.
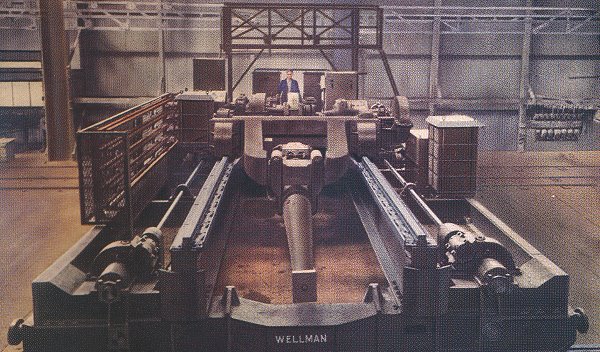
A low ground charging machine with a capacity
of 5 tons.
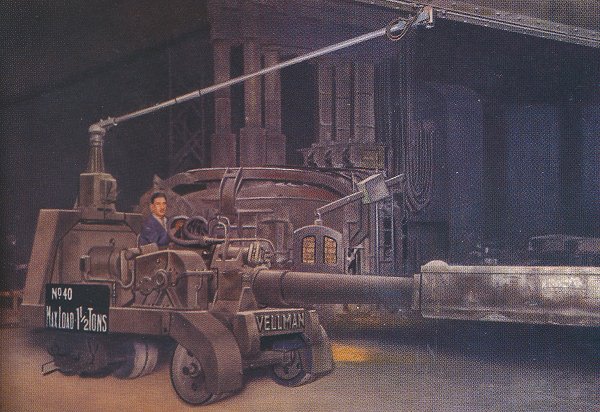
A mobile floor charging machine for electric
furnaces.
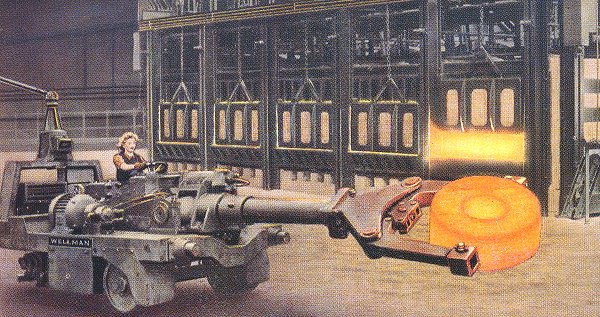
A mobile charger for handling tyre cheeses,
blooms, and billets.
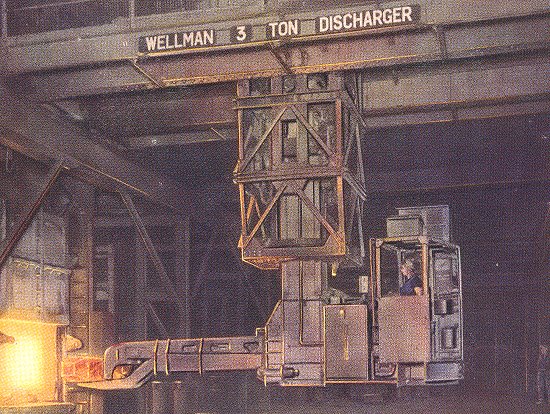
An ingot discharging machine.
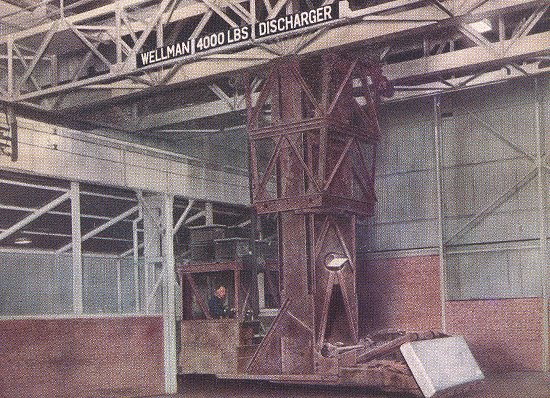
An overhead billet and slab discharger.
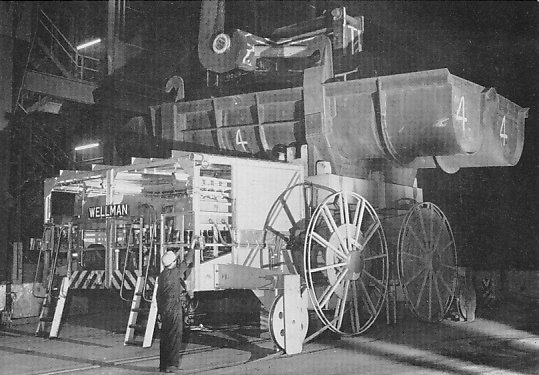
A Wellman 85 ton scrap charger in
use at Richard Thomas & Baldwins Limited, Spencer Works,
Llanwern, near Newport, South Wales. The 2 charging
boxes are being lowered onto the scrap charger. |
The company's many products included an
85 ton scrap charger. This was ideally suited for use
with LD convertors, a German designed refinement of the
Bessemer convertor, that blows pure oxygen instead of
air through the molten metal.. |
One charging box is in the
tilted position to charge an LD convertor.
After charging, the box will be
lowered, and the electrically powered scrap charger,
which runs on rails, will be moved forward to position
the second charging box over the mouth of the convertor.
|
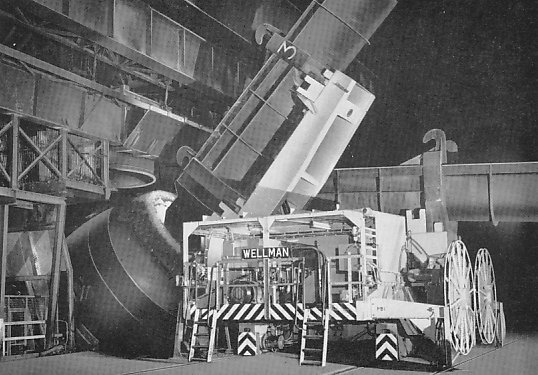 |
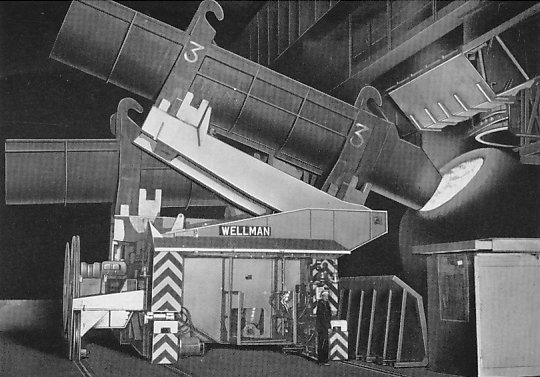 |
A final view of the scrap
charger, showing an empty charging box returning to the
horizontal position. |
More machines for use
in steelworks: |
Ingot stripping
machines and vertical charging machines serving
a large battery of soaking pits. |
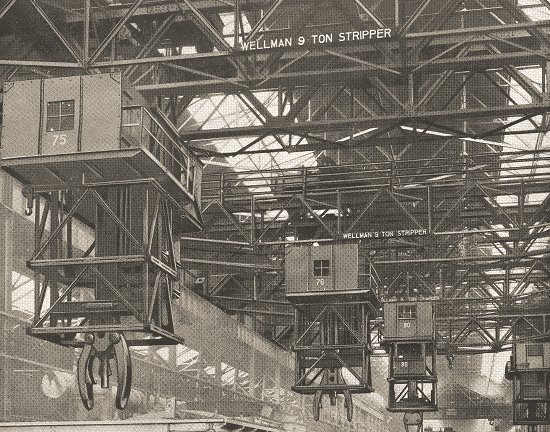 |
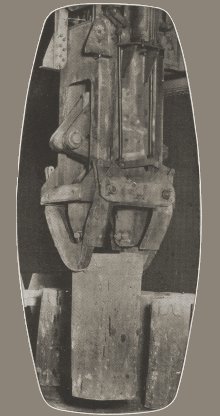 |
The Wellman patent
ingot stripping and mould handling machine to
strip hot top ingots, and to handle ingot
moulds. After an
ingot has been stripped, the apparatus retained
the mould to prevent it falling back onto the
casting car. The operation of the mould tongs
was independent of the movement of the stripping
tongs. |
A stationary ingot
stripper with an operational pressure of 100
tons. |
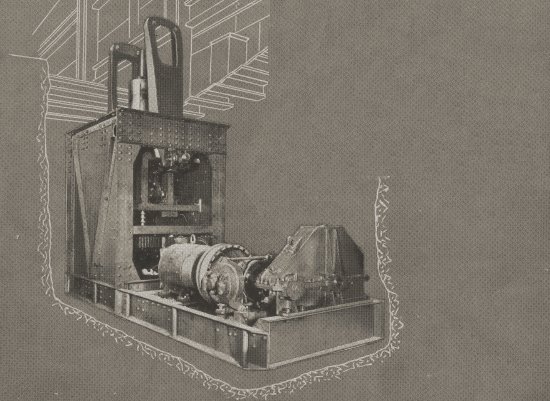 |
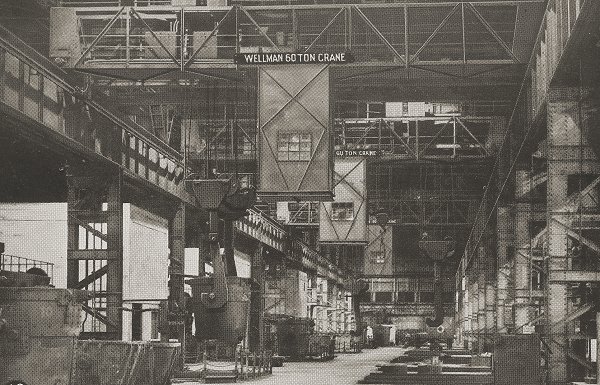
Three 60 ton ladle cranes.
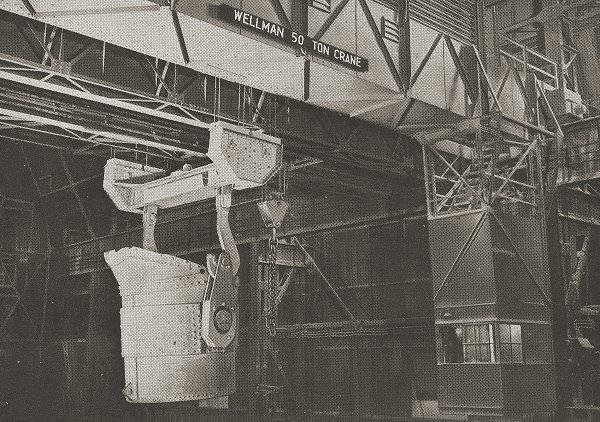
A 50 ton ladle crane.
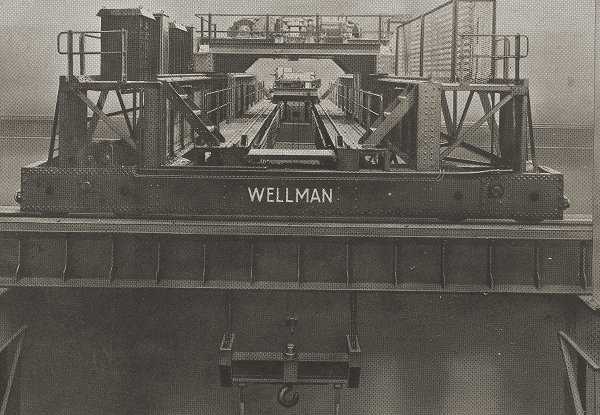
The main and auxiliary trolleys on
an overhead crane. |
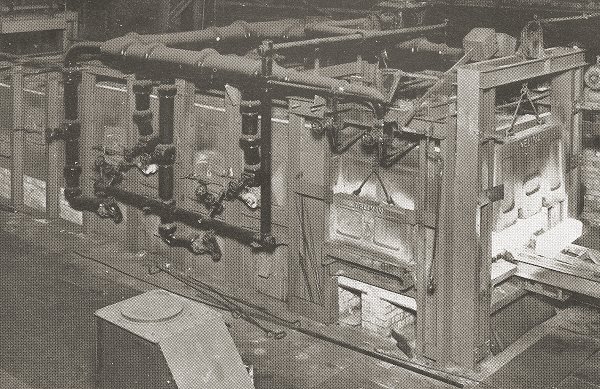
A continuous reheating furnace, fired from
town gas.
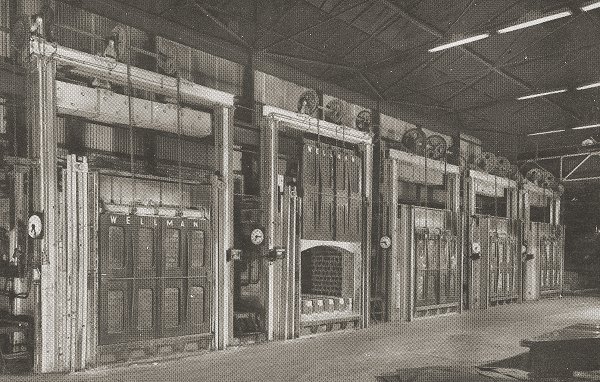
A battery of annealing furnaces for brass and
copper sheets.
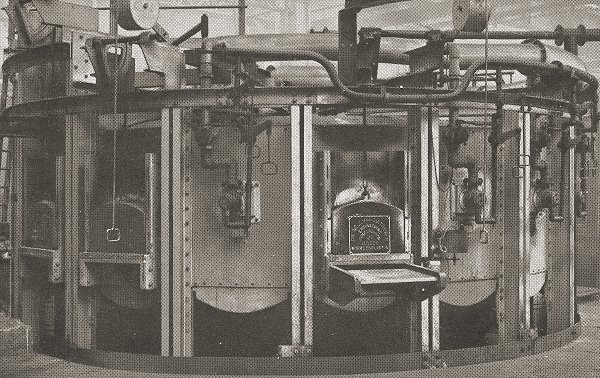
A Wellman rotary hearth furnace, fired with
coke oven gas.
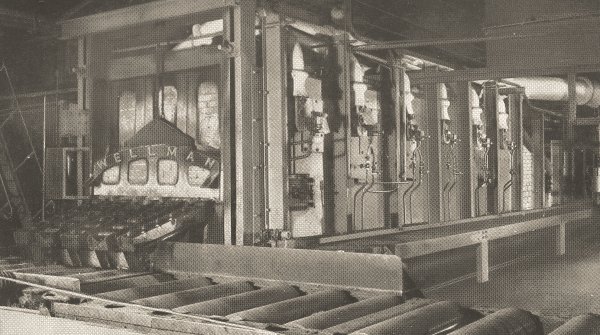
A continuous slab heating furnace.
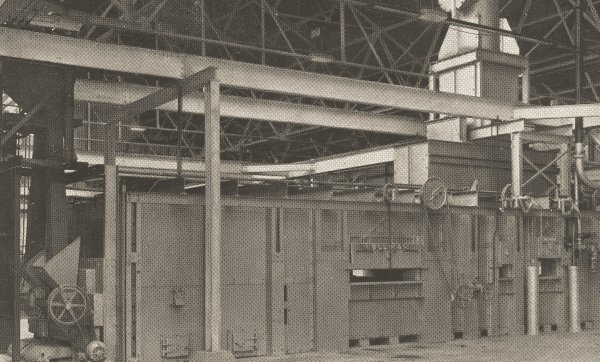
An aluminium melting furnace with a chain
grate stoker.
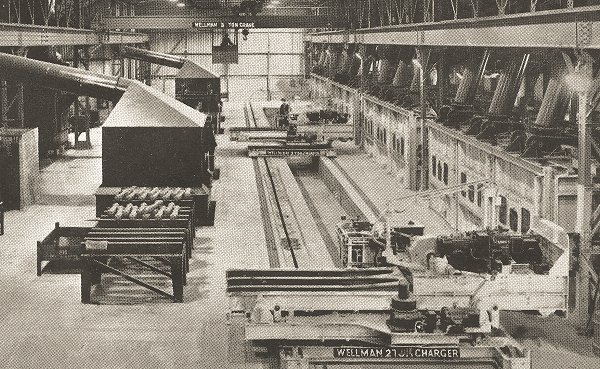
A complete heat treatment plant.
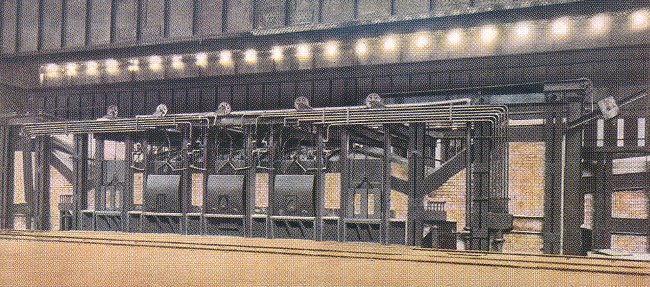
The charging side of a Wellman 'Venturi' open
hearth furnace.
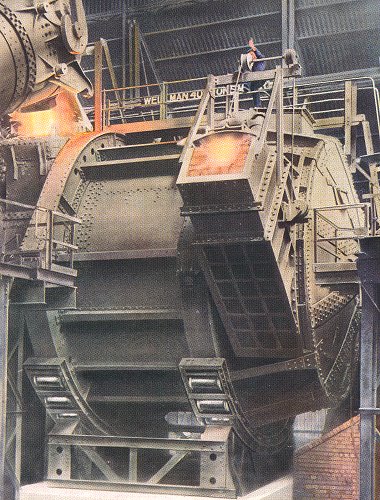 |
A 400 ton Wellman inactive metal
mixer that is fired with blast furnace gas through three
special burners. It
electrically tilts and rests on a roller track between the
rockers and the bearer girders. |
A 300 ton tilting open hearth
furnace. It is electrically
tilted, water cooled, and has an electrical door lifting
mechanism. |
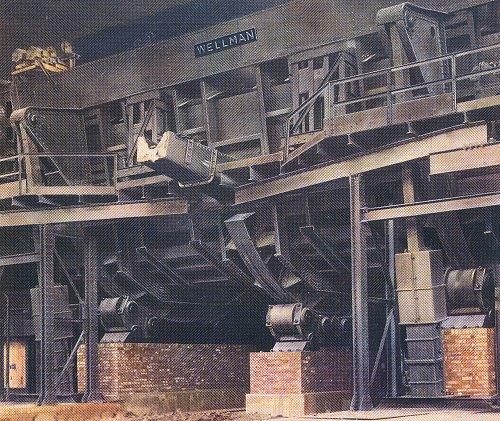 |
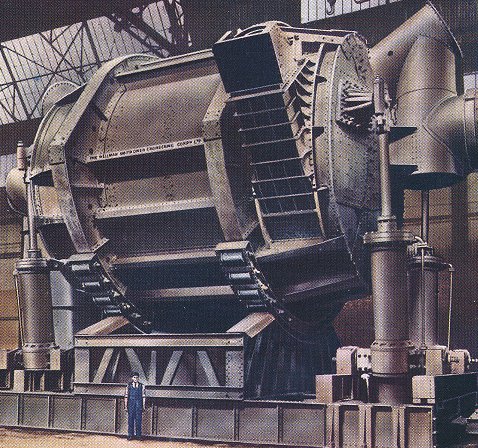 |
A Wellman 1,000 ton metal mixer
designed for use in a confined space.
The firm made metal mixers with
capacities of 150 to 1,000 tons. |
General lifting and
handling equipment: |
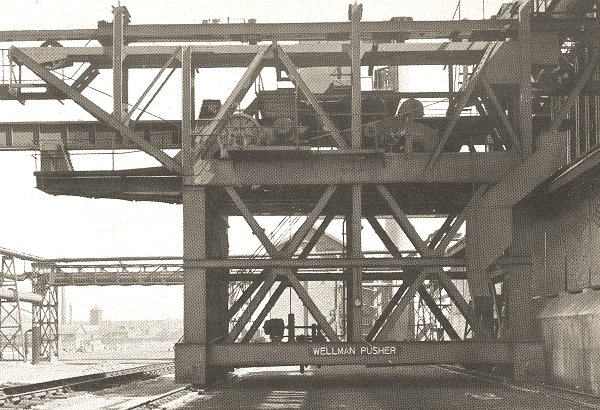
A combined coke pushing, coal levelling, and
door extracting machine.
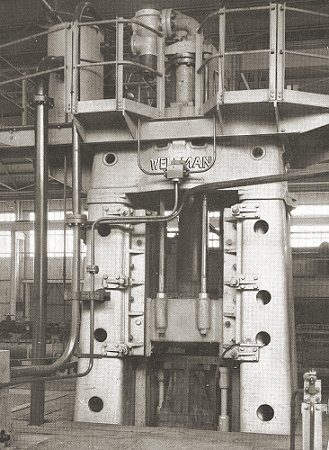 |
|
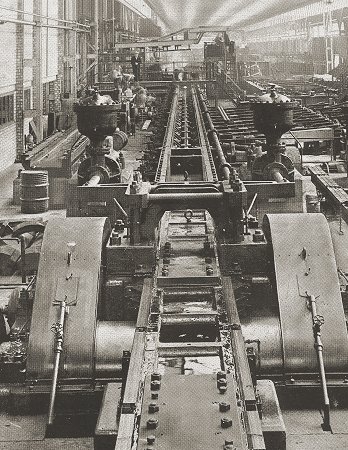 |
A 1,500 ton
piercing press. |
|
A complete
Wellman seamless tube plant. |
|
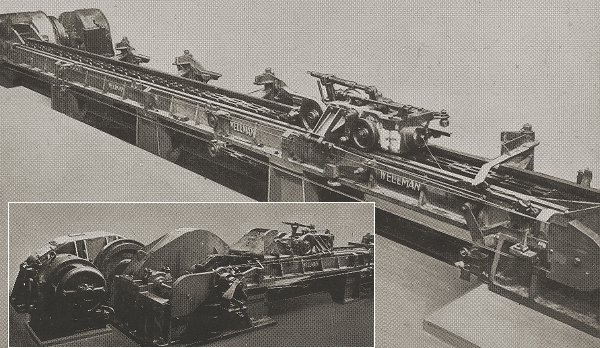
A 40 ton variable speed cold draw bench for
tubes.
Wellman-Galusha gas
producers: |
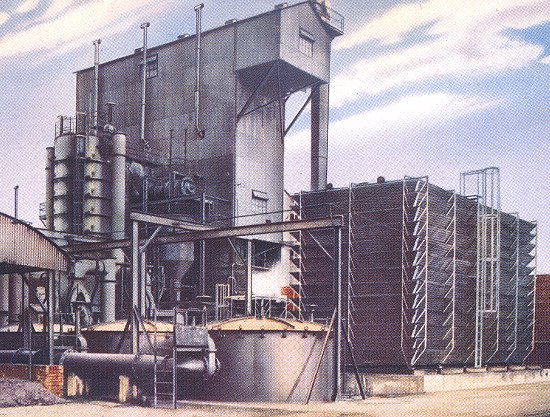
A Wellman-Galusha gas producing plant with
producers and a cleaning plant.
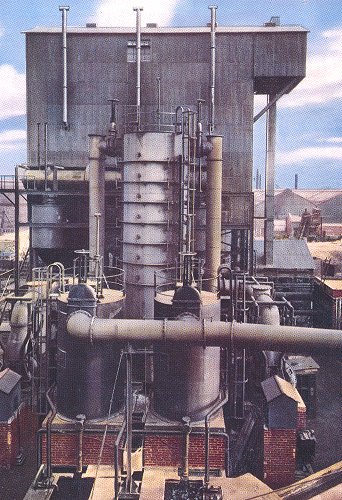 |
|
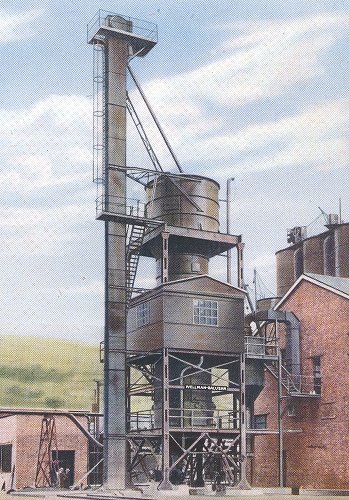 |
A Wellman-Galusha
gas producing plant. |
|
A single
unit for the production of hot gas. |
|
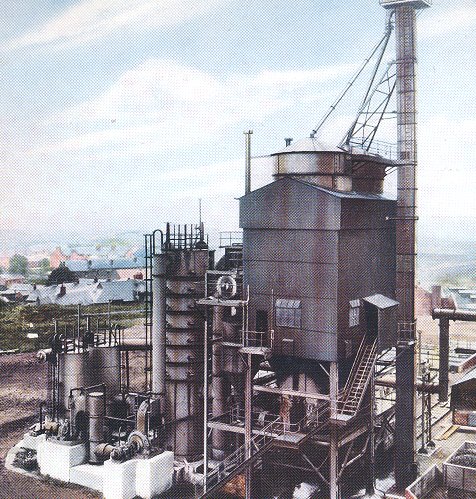 |
Two Wellman-Galusha gas producers
with auxiliary equipment. |

 |
Return to
the
previous page |
|