Neptune Forge, Chain, Anchor, and Engine Works |
The business was founded in 1862 by
Joseph Wright and Thomas
Tinsley, a well known Dudley nail factor. Joseph Wright
was born in Dudley on the 7th October, 1826. His father,
James Wright, was a blacksmith in Dudley. Joseph began
his working life helping his father in his business and
as an apprentice at Woodside Iron Works at Dudley. After
his apprenticeship he became an erector for Woodside
Iron Works and was involved in many projects including
the erection of a large factory in India and the
erection of Ormesby Iron Works, Middlesbrough.
He then became a partner in the
firm of Head, Wrightson and Company at Stockton-on-Tees.
During his time there he designed and built several
large blast-furnaces, developed a method of making
railway chairs cheaply, designed and improved plant for
use in foundries, and designed plant for use with blast
furnaces. In 1860 Joseph became a member of the
Institution of Mechanical Engineers. When the
partnership came to an end in 1862, Joseph returned to
Dudley and founded the chain and anchor making business
at Neptune Works, Tipton, with his future father-in-law,
Thomas Tinsley. Neptune Works stood alongside the
canal at the southern end of Sedgley Road West. In 1864
he married Thomas’s daughter, Grace Elizabeth Tinsley.
|
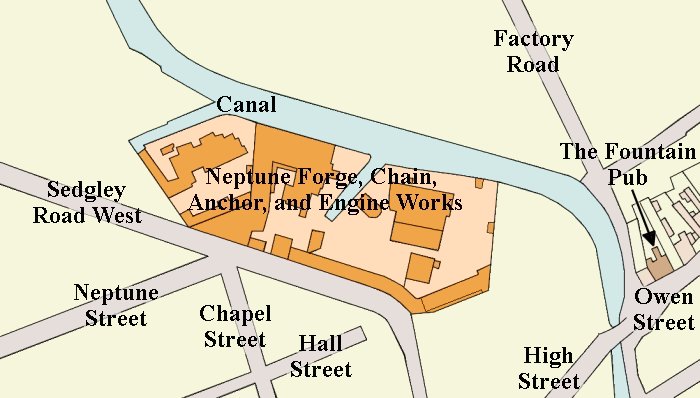
The location of Neptune Works,
based on the 1884 Ordnance Survey map. |
Neptune Works was a great success,
becoming one of the largest chain and anchor works in
the country. Its products were sold throughout the UK
and abroad, to countries including Germany, Russia, and
Turkey, where they were well appreciated. Only the
finest iron was used. It came from Bloomfield Iron Works
(B.B.H. iron) and from the Earl of Dudley’s ironworks.
Products included Martin’s self-canting anchor, which
was patented by Claude Martin, and sold in large
quantities.
The firm became Joseph Wright and
Company and the order books continued to fill. In 1881
Joseph and Grace were living at 45 Islington Row,
Edgbaston, with their four children.
|
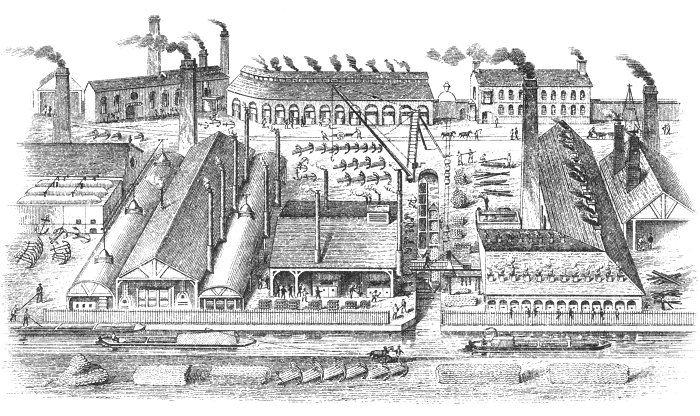
Neptune Forge, Chain, Anchor, and Engine Works. |
Samuel Griffiths includes the
following description in his Guide to the Iron Trade of
Great Britain, published in 1873:
When in the Black Country the
other day, we were particular in our enquiries in
respect to Wright's chains and cables at the Government
testing and proof establishment at Tipton, and were
there informed that the testing and proving of the
cables and chains turned out at the Neptune Forge
completely justified the celebrity for quality which Mr.
Wright's chains have in Germany, Russia, the Levant, and
other foreign markets.
The anchors made here are well
known throughout the world, the Neptune Forge having
turned out from time to time the best and largest made.
We understand the excellency of the quality of the
chains and cables is owing in a great measure to the use
of B.B.H. and the Earl of Dudley’s bars which are
unsparingly consumed at this great factory, although the
price paid is £1 per ton to £1.12s.6d. per ton more than
any other iron of this class made in Staffordshire.
Messrs. Wright & Company are now engaged on large orders
for the Russian and Turkish Governments.
|
|
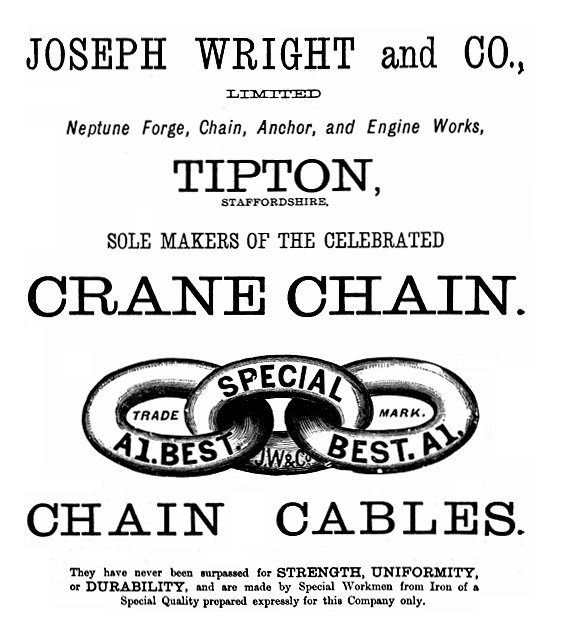
An advert from 1880. |
By 1880 Joseph Wright and Company
were sole makers and patentees of the Berryman improved
coal-saving feed-water heater that saved between 15 to
60% of coal, water and labour.
This resulted in Joseph
forming the Patent Heater Condenser Company.
In 1882 the
company manufactured anchors, chains, chain cables and
the Berryman feed-water heater and interheater. |
Other
products included all kinds of forgings in iron and
steel, housing pins and boxes, chain cables, crane
chain, lashing, sling, and coupling chains, draw bars,
hooks, rings, swivels, shackles, smith’s work of every
kind, boilers, colliery tubs, and tanks. Also Martin's
Patent Anchors. |
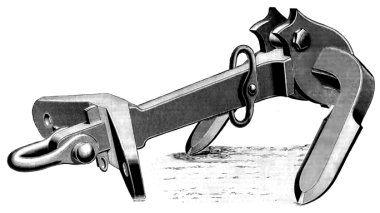
A patent anchor. |
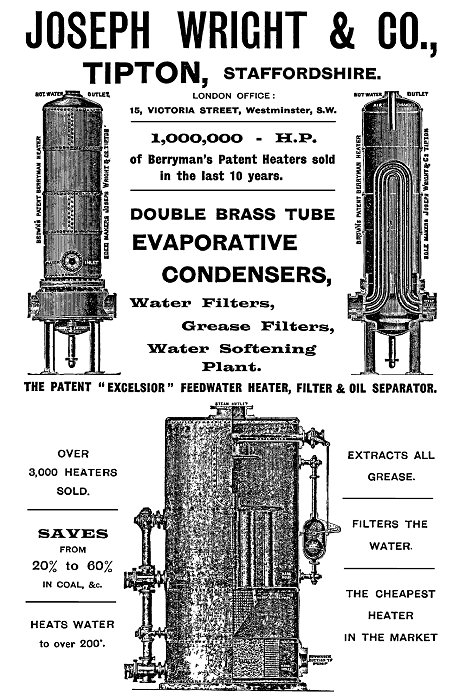
An advert from 1896.
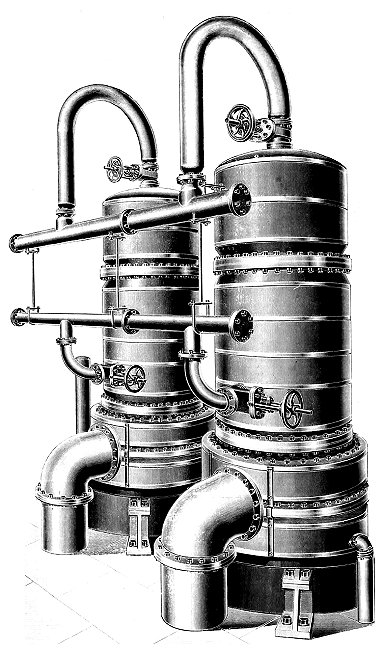
Berryman improved
coal-saving feed-water heaters. From 'The
Engineer', 1898. |
In 1887 he retired from the firm,
and practised as a consulting engineer in Westminster,
at the same time carrying on the manufacture of heaters,
evaporators, condensers, water softeners, and other
appliances connected with the purification of water.
His
last invention, completed only a few days before his
death, was a high-speed engine for electric lighting
installations.
During the last eight years of his
life, Joseph suffered from terminal throat cancer and
died on 20th October 1893, at the age of sixty-seven.
In 1903 the company received an order from the
Wath-upon-Dearne Main Colliery Company for a heater
detarteriser, to heat and soften about 18,000 gallons of
water per hour. The device was the largest of its kind
ever made, being around 35ft. high, 8ft. diameter and
weighing around 40 tons.
The firm founded Wright's Forge and Engineering
Company in 1913 and in 1922 - 1923 the business was
acquired by N. Hingley and Sons of Netherton. In the
1960s, N. Hingley and Sons became part of F. H. Lloyd &
Company of Wednesbury.
|
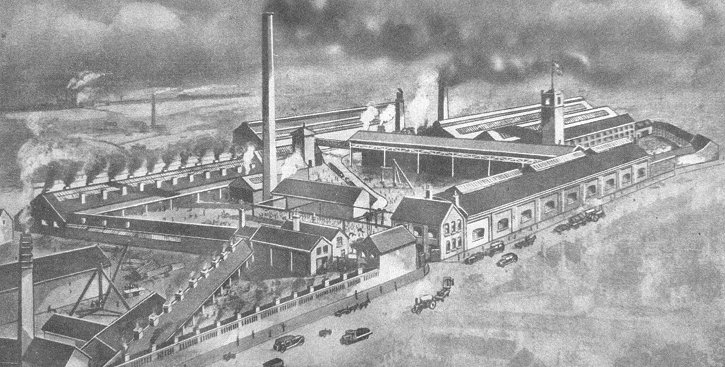
Wright's factory. From
a 1920s advertising brochure. |
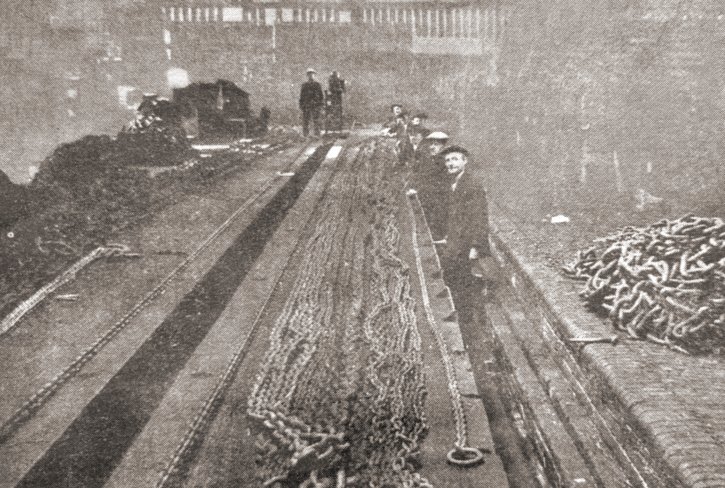
Testing chains at
Wright's works. From a 1920s advertising
brochure. |
F. H. Lloyd's
Tipton Factory
On 4th November, 1963 a team of men from James Bridge
works moved into the two empty bays of Wright's Forge in
Tipton. Lloyds acquired the site in order
to fettle large turbine castings which were occupying
valuable space at James Bridge. Heading the team of ten
was George Wilkinson who had the task of setting up the
operation there. Initially there was no shotblast or
heat treatment facilities, just hard work.
Within twelve months, a shotblast plant and a heat
treatment furnace had been installed, and by the end of
1964 there were 13 welders, 17 finishers, 3 burners, 3
shotblasters, 2 heat treatment furnace men, 2 crane
drivers, and 1 labourer. By the 1970s the building had
grown to four bays covering 100,000 square feet. Around
3,000 tons of fabrications were produced annually under
the control of George Roberts, Production
Superintendent.
|
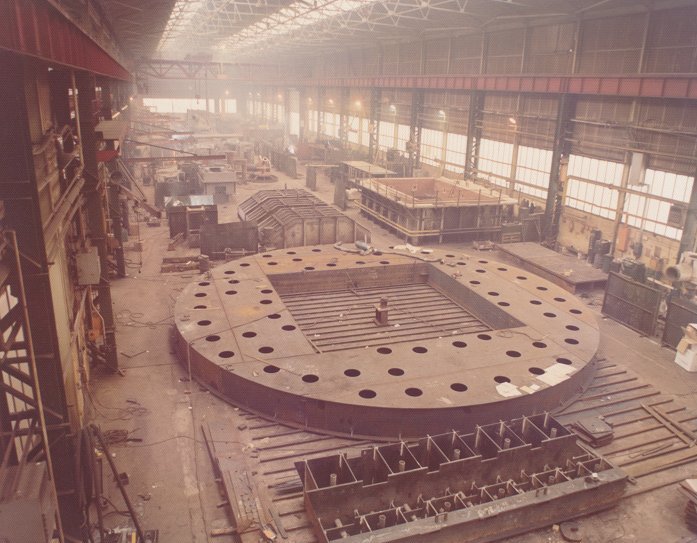
A view inside F. H. Lloyd's
Tipton factory. Courtesy of Wendy Marston. |
Machinery in the factory included a 700 ton twin 'C'
frame hydraulic press, designed and built at the James
Bridge factory. It could handle steel plate up to 16
feet wide and ¾ inch thick. There were 4 automatic gas
profile cutters and fully automatic welding machines. The Fabrications Section moved to Tipton in 1966, and
became a separate division of F. H. Lloyd and Company
Limited in 1967. Lloyds Steel Fabrications became one of
the country’s leading manufacturers of welded steel
fabrications. It was a great success.
Dick Howett was general manager, in
charge of sales, estimating and process planning,
costing, buying and production. The production
superintendent was George Roberts who was responsible
for all production and work schedules. He maintained
liaison with customers on delivery and ensured that the
right materials were in stock for the job.
|
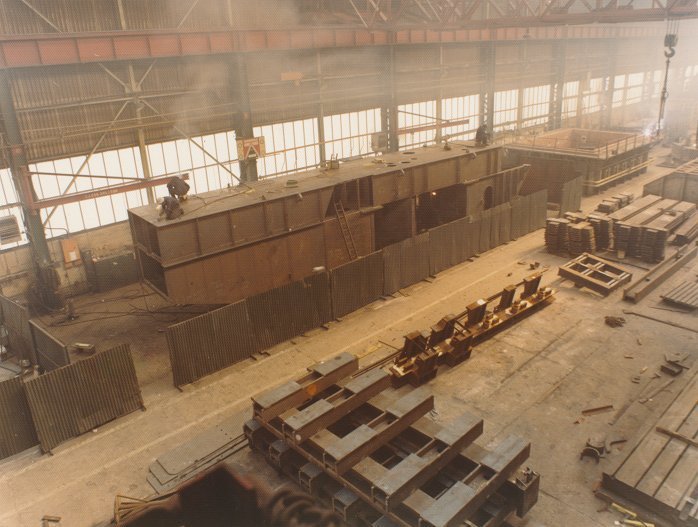
A large fabrication nears
completion in the Tipton factory. Courtesy of Wendy
Marston. |
Colin Hammond was chief planning
engineer at Tipton. His department prepared estimates
against enquiries, from which quotations were submitted.
The department also translated orders and drawings into
detailed working instructions for manufacture. George
Arnold oversaw quality control, which included checks on
raw materials, work in progress, and completed
fabrications, using special test equipment.
Muriel Simmons was secretary to Mr.
Howett, and the young lady, known as the voice of the
division, Barbara Potter, was the telephonist.
|
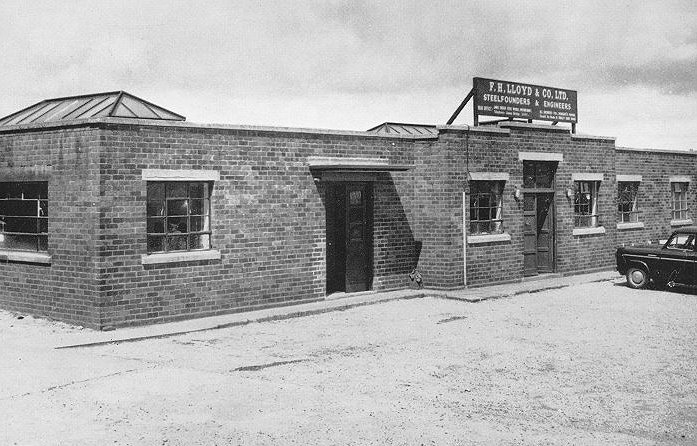
In the autumn of 1965 a new
canteen opened on the Tipton site. It became known
as the 'Wilkeyville' canteen, named after the boss,
George Wilkinson. Courtesy of Wendy Marston. |
Plate preparation equipment in the
factory included four automatic gas profile cutters, a
Hancoline HL.3 and HL.4, a Hanco-ordinate c.90 and BOC
Bison, which were giant pantographs to exactly reproduce
on a sheet of steel a design or profile which was read
from a specially prepared drawing by an optical sensor.
There were also a number of straight-line cutting
machines, and twin C-frame hydraulic presses, designed
and built by Lloyds.
Four welding processes were used:
manual arc, cored wire CO2, submerged arc and electra-slag,
the last two being fully automatic. The electroslag
machine is a prototype and the only one of its kind in
this country, manufact:ured by ESAB of Sweden. It could
butt weld plates up to 15 inches thick.
There was a North Sea gas fired heat treatment furnace with a
capacity of 24 ft. x 16 ft. x 11 ft. where fabrications were heated
to a temperature of 650°C to relieve any stresses set up by welding.
The shot blast plant was in a heavily shielded room measuring 27 ft.
x 24 ft. x 18 ft. high with an opening top to permit the craning in
and out of fabrications. Steel pellets were 'shot' from a nozzle by
compressed air at high speed to scour the surface scale from the
fabrication and reveal the pristine grey metal that is steel.
On 12th August 1969 F. H. Lloyds became part of F. H. Lloyd Holdings
Limited which was created to oversee the various companies in the
Lloyd group. The Tipton factory closed in the late 1980s and the
site is now occupied by Neptune Park apartments and Neptune Health
Park medical practice.
|
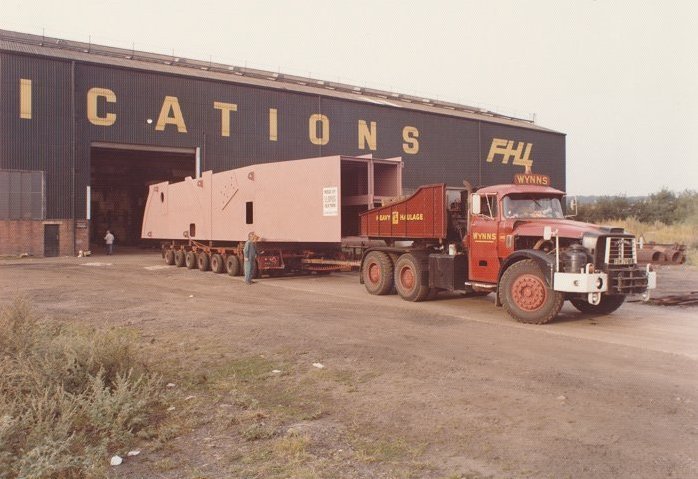
A large fabrication leaves the
Tipton factory. Courtesy of Wendy Marston.
|
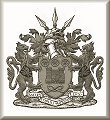 |
Return to
the
previous page |
|