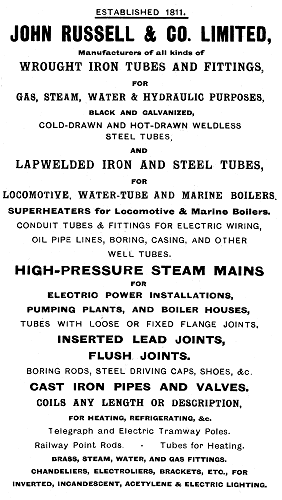
An advert from 1916. |
The largest ironworks in the Pleck area was
Edward Russell's Cyclops Ironworks in Pleck Road, which had
opened by 1873. On the site were 22 puddling furnaces and 3 rolling-mills.
Edward ran John
Russell & Company, an old Wednesbury firm that was
established in 1811. Edward was the son of John Russell and
his wife Mary. After John's death, at the age of 69 in 1853, Edward ran the
business and in 1854 founded the Alma Tube
Works. Edward died in 1875.
The firm still used the Old Patent Tube Works in
Wednesbury, and had three other factories at Pleck; the
Cyclops Tube Works, Alma Tube Works, and Newside Iron Works,
lying side by side between Pleck Road and the canal.
The
company became a Limited company in 1876, and in 1896 Newside Iron Works merged with the adjacent Cormorant
Ironworks.
In 1892 John Russell & Company Limited produced around
half the posts to carry the overhead wire for the
electrification of the South Staffordshire Tramways which
connected Darlaston, Wednesbury, West Bromwich, Handsworth,
Great Bridge, Dudley Port, Dudley, Walsall, and Bloxwich.
The other posts were made by James Russell & Sons.
|
In 1926 the firm acquired a 100 acre site at Halton, near Runcorn and built a
new tube works there. In 1930 the business was acquired by
Stewarts and Lloyds. The firm took out a patent in 1935
for improvements in water taps and exhibited brass and
gunmetal valves and pipe fittings for steam, water and
gas at the British Industries Fair in 1937. |
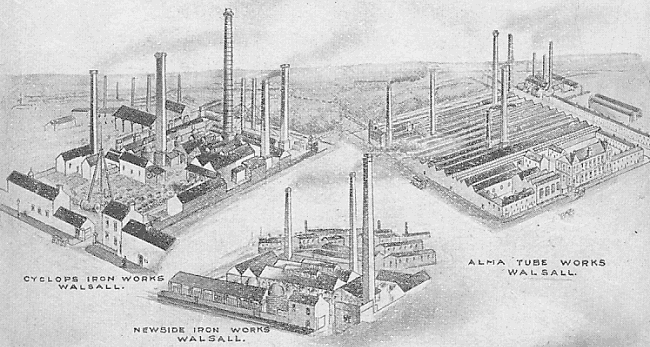
John Russell & Company Limited's Walsall
factories.
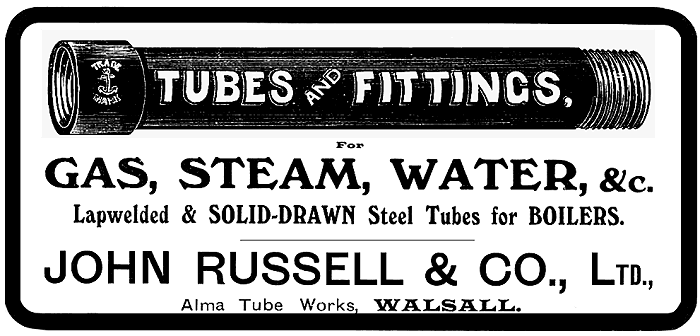
An advert from 1909.
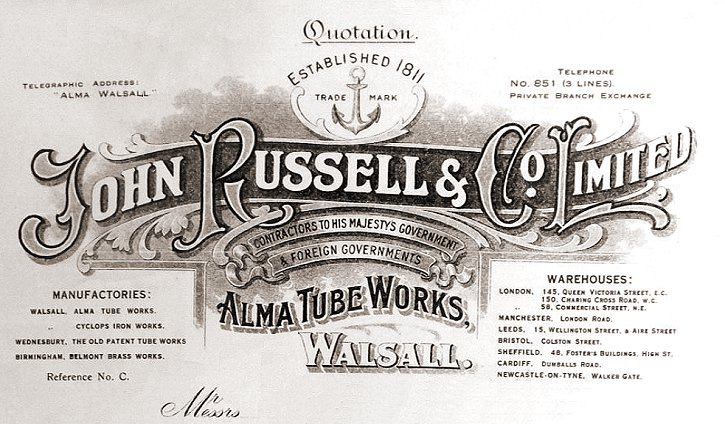
In 1897 the Institution
of Mechanical Engineers visited the tube
works:
Messrs. John Russell &
Company, Alma Tube Works and Cyclops Iron
Works, Walsall
This firm was
established in 1811, and was the first to
manufacture gas tubes by the drawing
process. The Alma Tube Works were commenced
in 1854, and are now divided into the
departments, employing altogether about 800
hands. The oldest department is the butt
weld mill, where butt welded tubes, chiefly
for high-pressure hot water, heating, and
hydraulic purposes, are made by the drawing
process. Here also are made taper telegraph
and tramway poles; railway point and signal
rods; glass blowers' tubes, etc. The
ordinary butt welded steam, water, and gas
tubes are made at the Wednesbury works, and
the process is similar to that employed in
this department. There are also fitting and
socket makers' shops and a stamping shop,
for making large sockets and flanges.
Attached to this
department also is the coil shop, where
coils of all sorts are made for heating and
refrigerating, and tuyere coils for blast
furnaces. In the lap weld department, the
mill consists of five welding and two
skelping furnaces, five out of the seven
being Siemens regenerative furnaces,
supplied with gas from a range of Wilson
producers; from these furnaces, tubes from
inch to 18 inches diameter can be welded.
The finishing shops are
fitted up with tools for cutting off,
screwing, staving, bulging, flanging, and
other methods of making joints, either for
fixing in boilers or for coupling together.
Large quantities of oil line pipe, well
boring and casing tubes, both for oil and
water wells, are manufactured here, as well
as high pressure steam mains, iron and steel
boiler and stay tubes, etc. Storage heaters
for railway carriages and tramcars are also
made, and sent out ready for fixing. The
weldless tube department, which has been
recently added, is equipped with seven
double draw benches, five for cold drawing
tubes up to 2 inches diameter, and two
powerful benches for drawing Belleville
boiler tubes and tubes up to 6 inches
diameter for hydraulic purposes. The rolling
mill consists of four pairs of rolls, driven
by a tandem compound surface condensing
engine.
The Cyclops Iron Works
employ about 400 hands, and can turn out 400
to 500 tons of finished iron per week,
consisting chiefly of tube strip iron for
consumption in the tube works. There are
thirty two puddling furnaces, two of them
working with forced draught, and the others
of the ordinary kind. Three steam-hammers
and a forge train with three pairs of rolls
deal with the product of these furnaces. On
the mill side are a 16 inch and 9 inch mill,
both three high. The 16 inch mill is engaged
almost exclusively on rolling tube strip
from 4¾ to 15⅛ inches wide. The 9 inch mill
rolls 4¾ inches and narrower strip iron, as
well as bar iron. The heating furnace for
the 16 inch mill is one of the new form of
Siemens furnaces, and a second of the same
kind is in course of construction. |
|
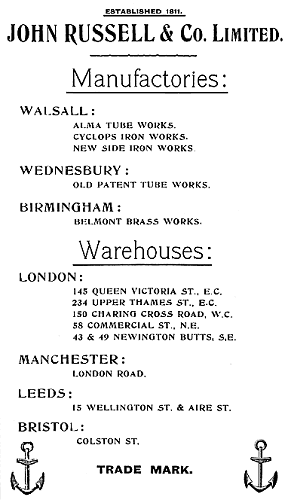
Factories and sites in 1916. |
|
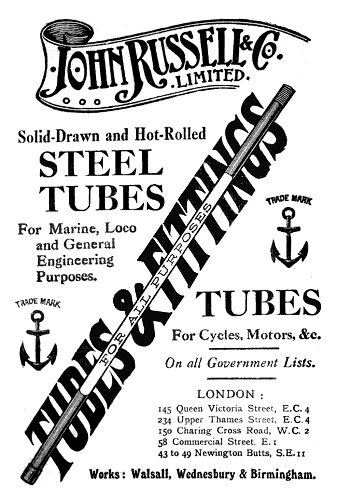
An advert from 1918. |
|
Some products from the 1916 catalogue |
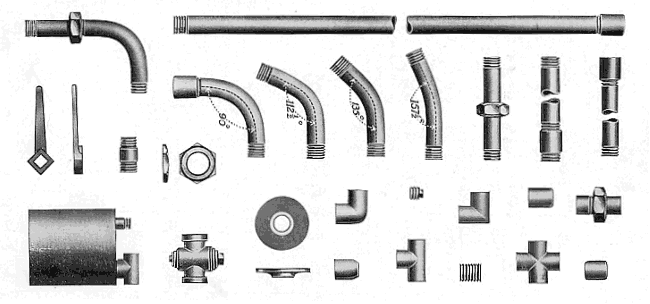
Standard gas fittings.
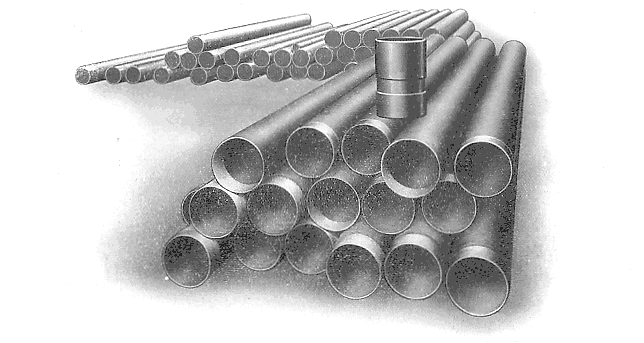
Screwed inserted casing tubes with a 5 inch to
12 inch bore.
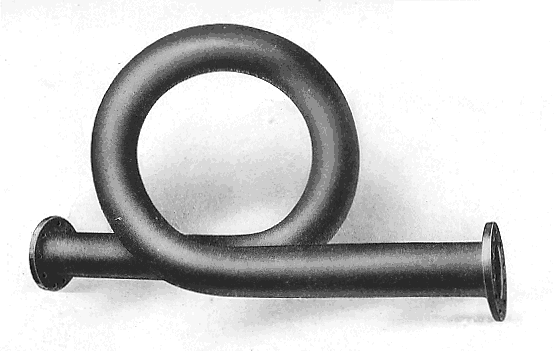 |
A loop type expansion bend with a
7 inch bore suitable for 180 psi steam pressure. |
12 inch horseshoe type expansion
beds for 165 psi steam pressure. |
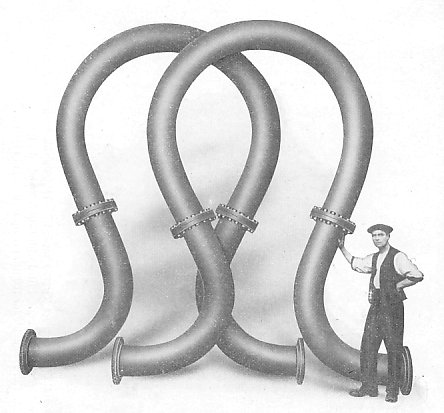 |
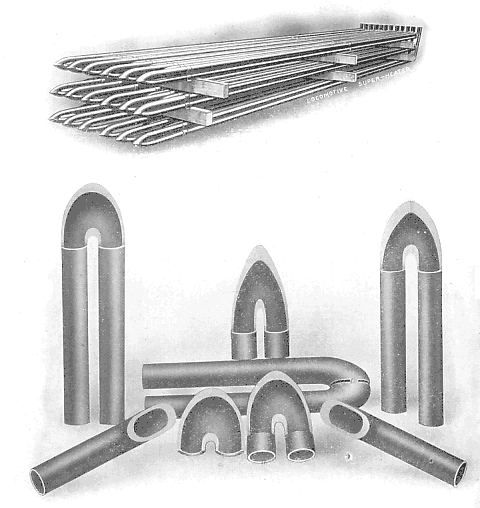 |
Seamless superheaters with special
welded ends for locomotives and boilers. |
Locomotive superheater elements. |
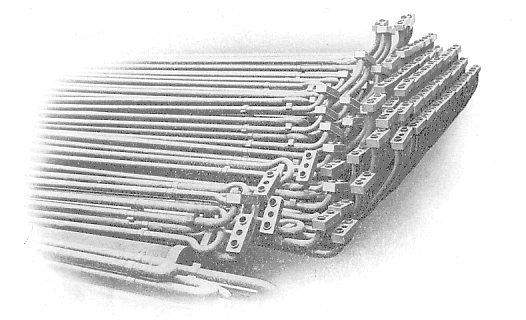 |
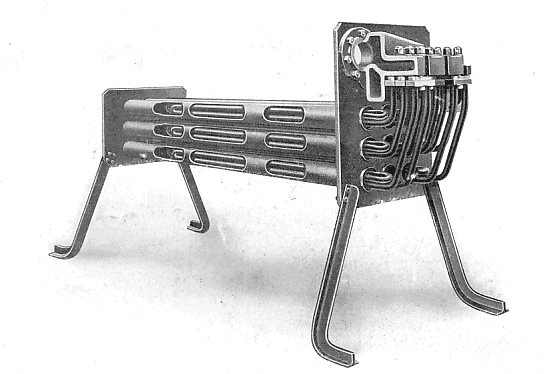 |
Locomotive superheater model. |
Schmidt type locomotive
superheaters and draught retarders. |
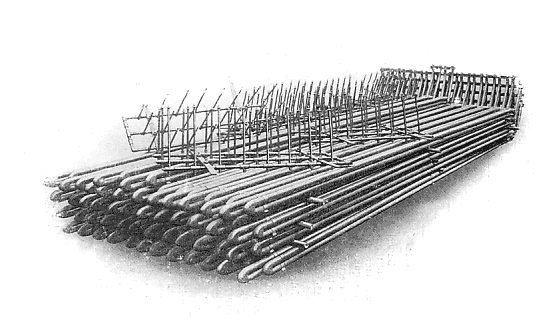 |
Boiler flue and stay tubes,
lapweld quality. Made from iron, steel, or charcoal iron as
requested. |
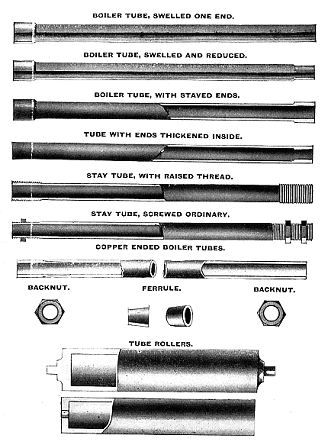 |
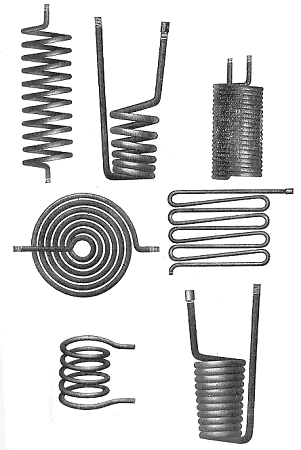 |
|
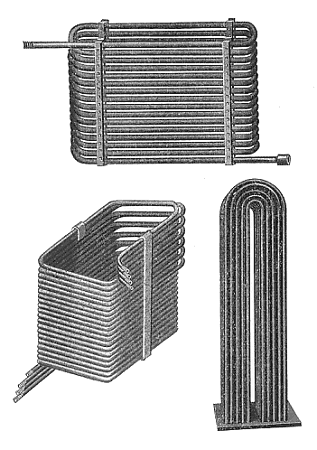 |
Coils were
available in round, square, or rectangular tube,
galvanised or black. They were suitable for
condensing, heating or cooling, in high or low
pressure heating plants. |
|
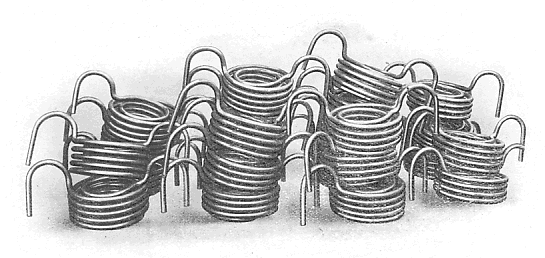
Seamless superheater coils.
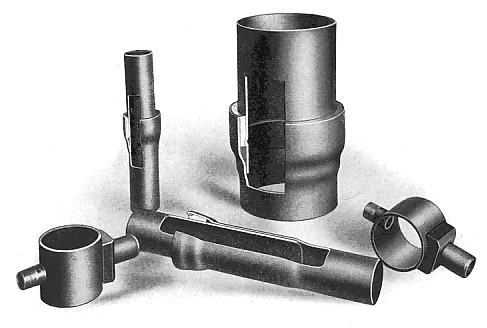 |
Joints for steel steam mains. |
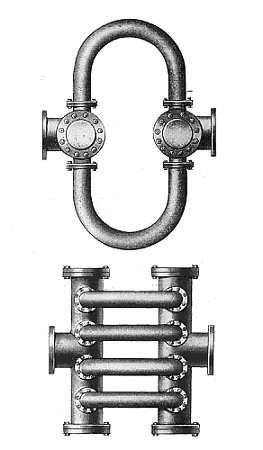
Expansion pipes for gas,
water, or steam. |
|
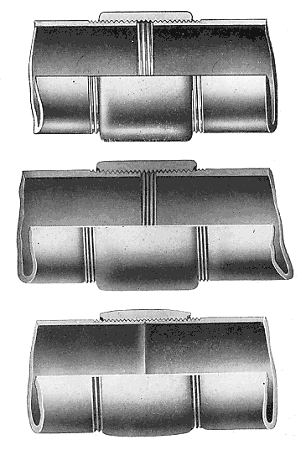
Standard sockets, screwed to
order. |
|
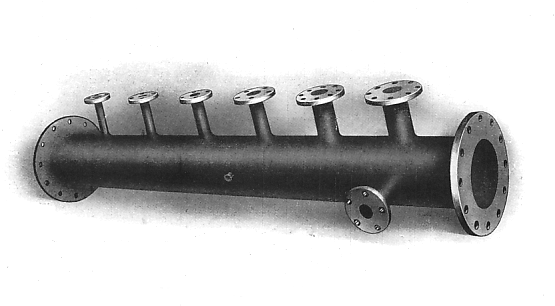
Steam drum for superheated steam at 300 psi.
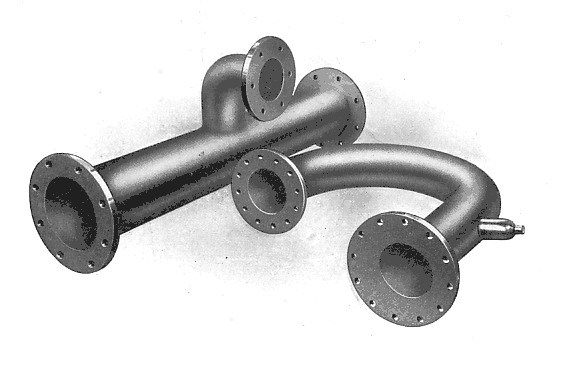
12 inch steam pipe with 8 inch outlet, and the
companion 8 inch bend.
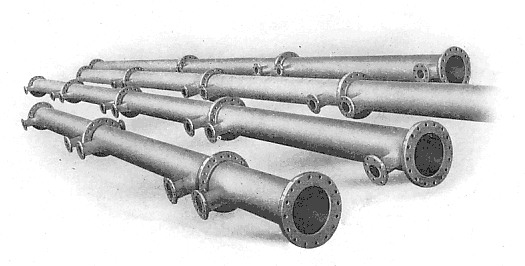
12 inch steam main, 160 psi.
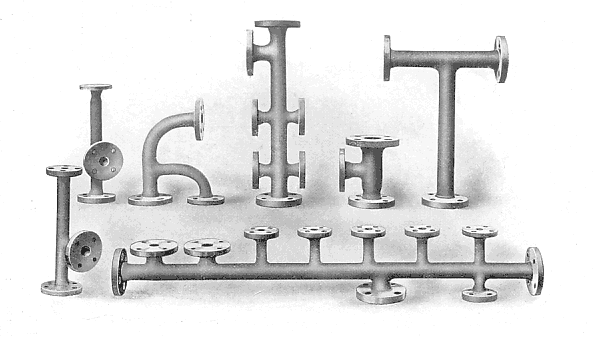
Steel tubes with welded outlets and welded-on
steel flanges.
Flanged tubes with
outlets welded-on. |
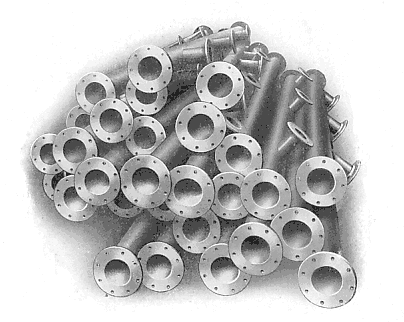 |
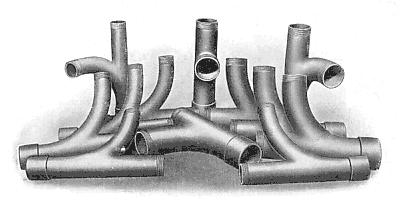 |
Special solid forged
sweep tees. |
Flanged fittings for 180 psi steam
pressure. |
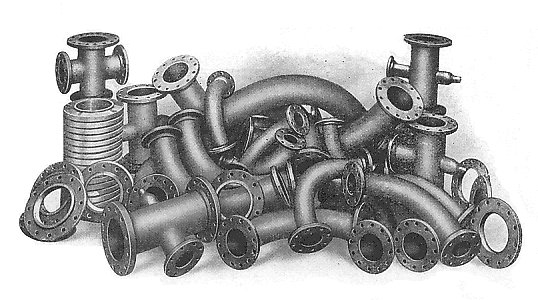 |
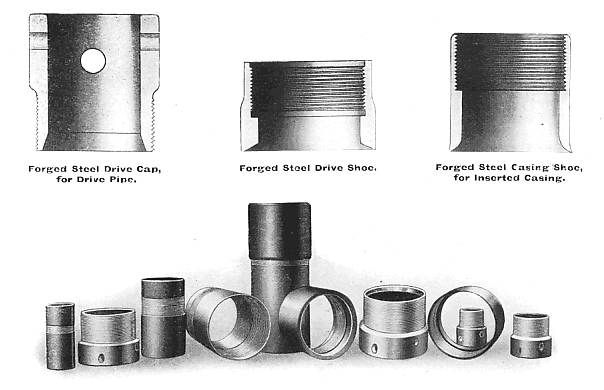
Driving heads and shoes for socketed well
casing tubes.
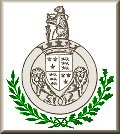 |
Return to
the
previous page |
|