Tube
Making
Crown Tube Works
The birth of one of Wednesbury’s
most famous industries took place in 1811 when John
Russell, gun barrel maker, and landlord of the Turk’s
Head Inn began to make wrought iron tubes.
|
At the time there was a shortage of
good quality tubing for use in steam engines, and more
importantly for distribution of the gas supply, thanks
to William Murdoch’s invention of gas lighting in 1792.
John Russell began to produce
tapered tubes which pushed together, but were very
difficult to make. As a result, John and his elder brother
James developed a hand-forged wrought iron socket for
joining parallel tubes together. Aaron Manby of Moxley
decided to manufacture the new invention, and offered
James employment at his new works.
In 1816 John decided to set up a
tube works on the corner of Wellcroft Street, Church
Hill, in partnership with James, who ran the business.
|
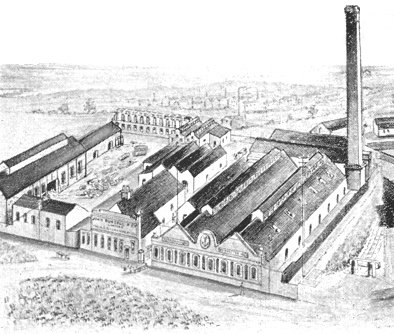
John Russell's Old Patent Tube Works at
Wednesbury. |
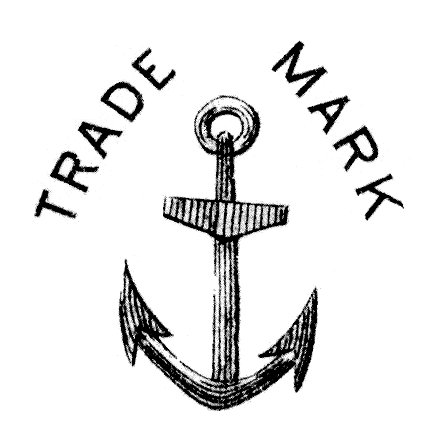
John Russell's trade mark.
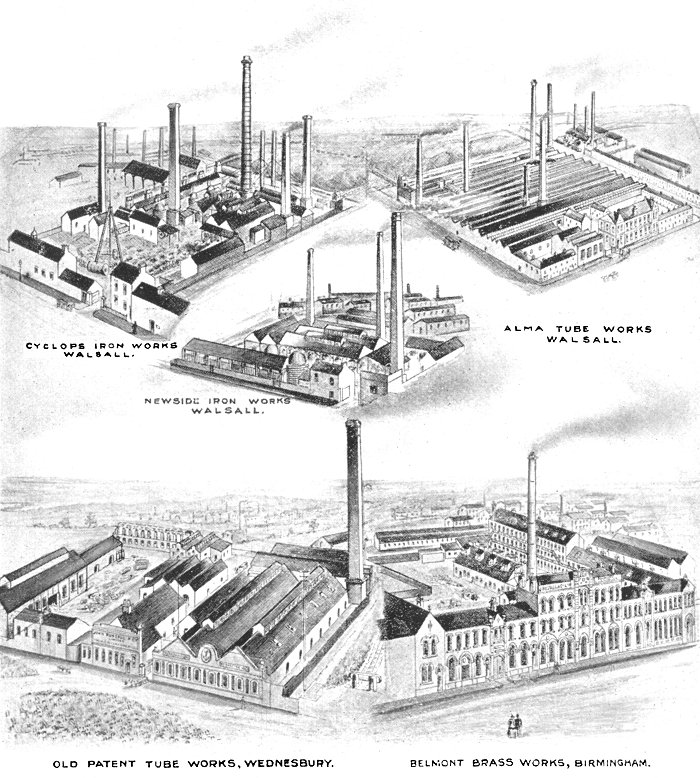
The firm's factories in 1916.
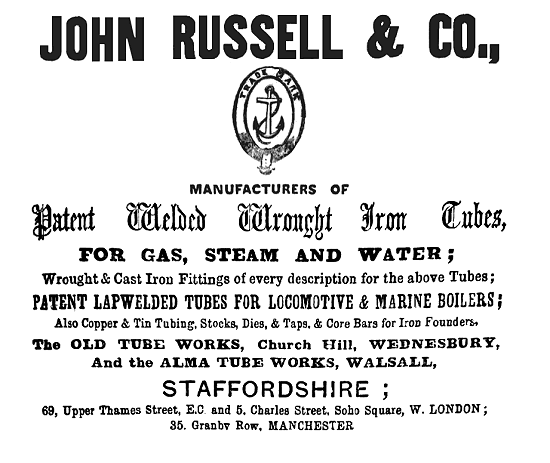
An advert from 1862.
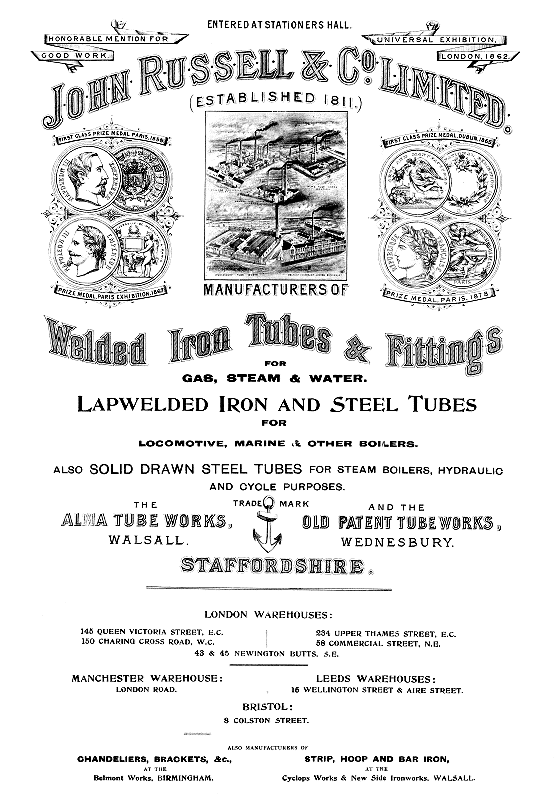
An advert from 1899.
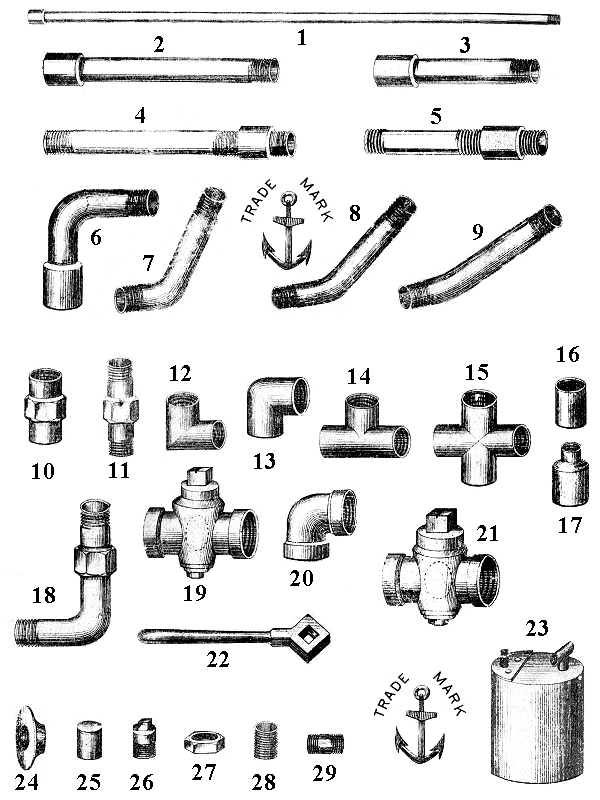
John Russell & Company Limited's tubes and
fittings on sale in 1899.
1. |
Tubes 2 to 14ft. long |
16. |
Plain Socket |
2. |
Pieces 12 to 23½
inches long. |
17. |
Diminished Socket |
3. |
Pieces 3 to 11½
inches long. |
18. |
Union Bend |
4. |
Long Screws 12 to 23½
inches long |
19. |
Iron Main Cock |
5. |
Long Screws 3 to 11½
inches long |
20. |
Malleable Cast Elbow |
6. |
Bends |
21. |
Iron Main Cock with Brass Plug |
7. |
Springs not socketed. |
22. |
Cock Spanner |
8. |
Springs not socketed. |
23. |
Syphon Box |
9. |
Springs not socketed. |
24. |
Flange |
10. |
Socket Union |
25. |
Cap |
11. |
Pipe Union |
26. |
Plug |
12. |
Square Elbow |
27. |
Back Nut |
13. |
Round Elbow |
28. |
Nipple |
14. |
Tee |
29. |
Barrel Nipple |
15. |
Cross |
|
|
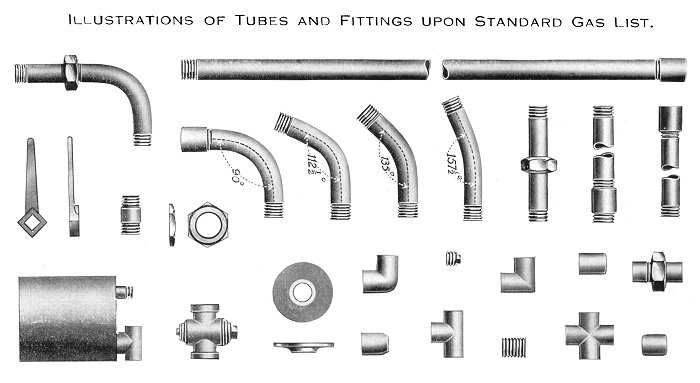
An advert from 1916.
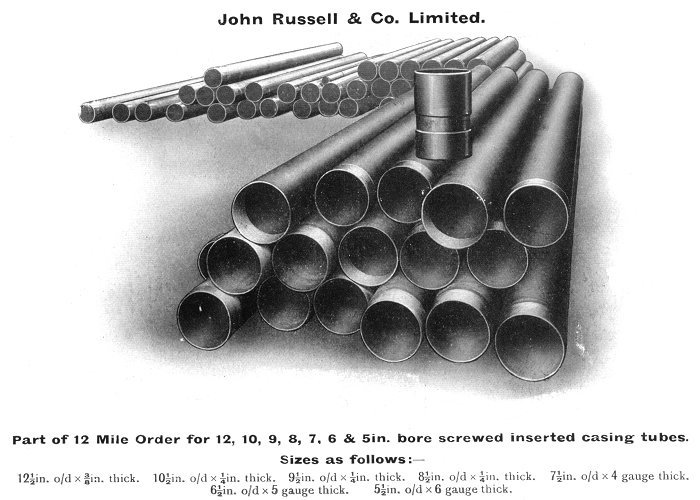
An advert from 1916.
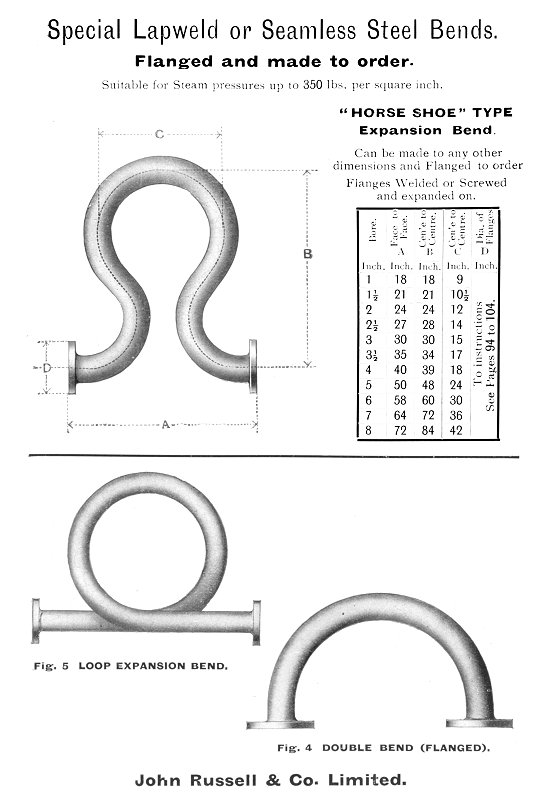
An advert from 1916.
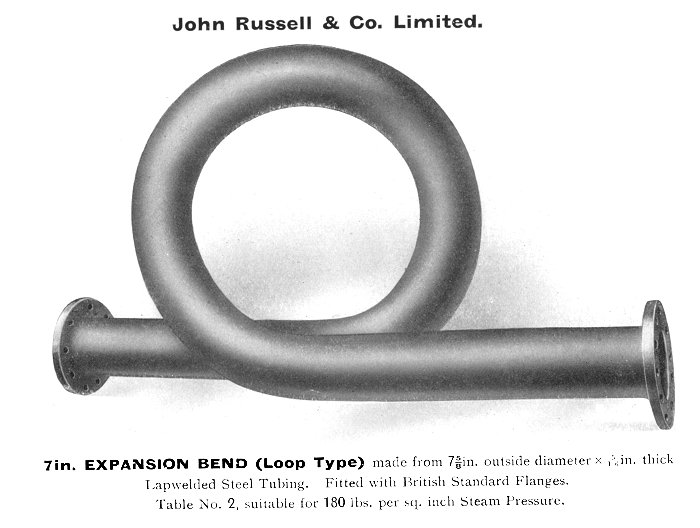
An advert from 1916.
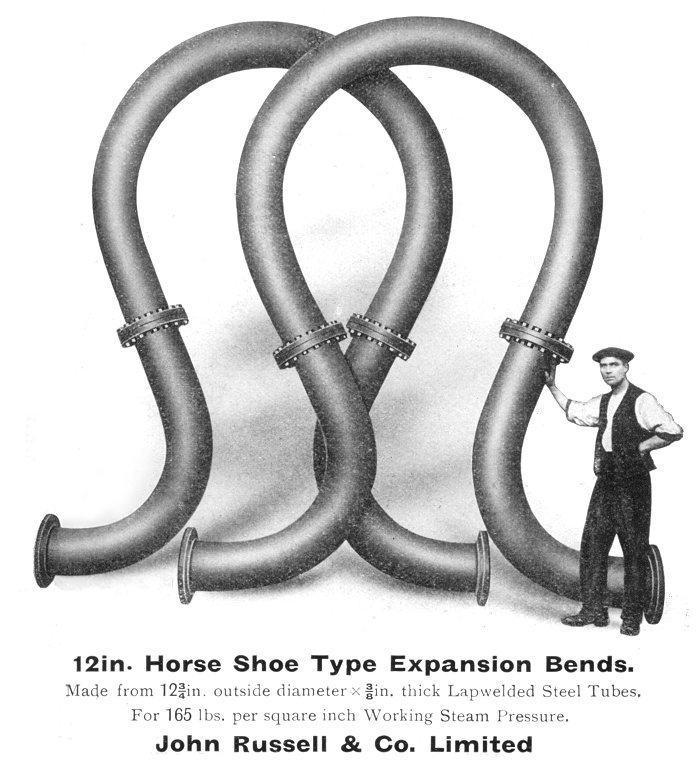
An advert from 1916.
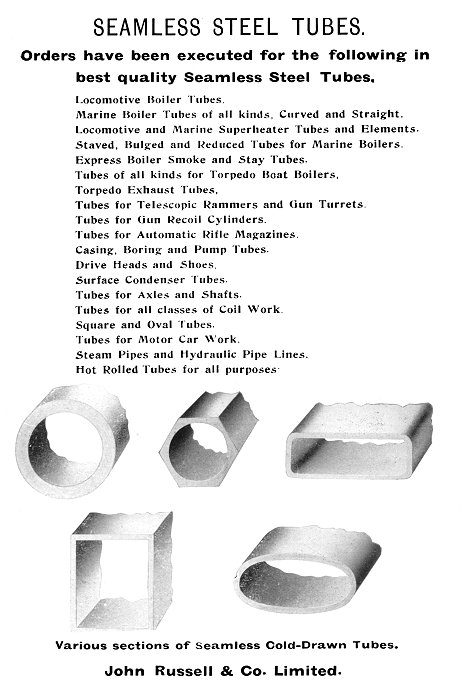
An advert from 1916.
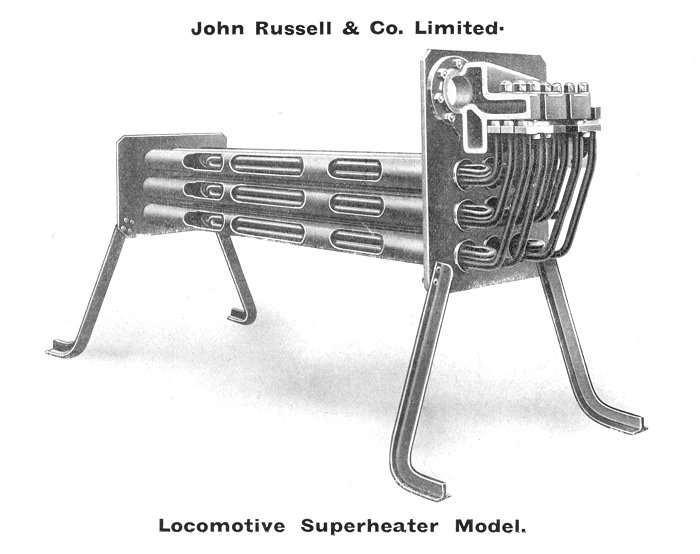
An advert from 1916.
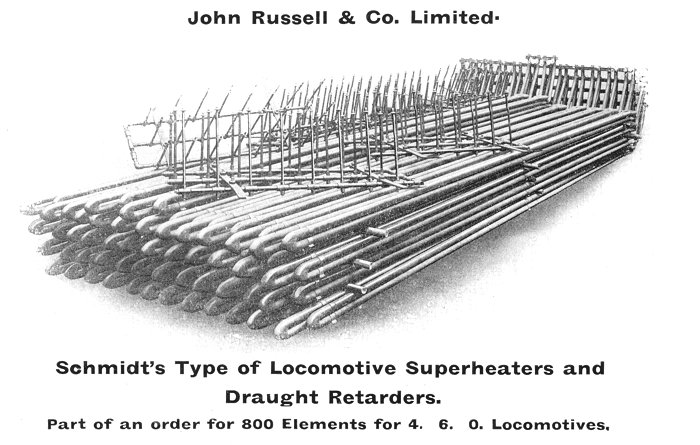
An advert from 1916.
In 1823 James left and founded
Crown Tube Works at the High Bullen, after securing a
patent for butt welded tube. John subsequently founded
John Russell & Company. After his death in 1853 much of
the manufacturing moved to the new and larger Alma Tube
Works in Walsall, but the company also continued to use
the old Wellcroft Street works.
Tubes were originally formed from
an iron strip, or skelp as it was known, which was
heated in small sections, a few inches at a time, in a
conventional blacksmith’s fire. Each section was
hammered into shape, each side of the seam being
overlapped and hammered to form a weld.
The whole
process took a long time as many heatings and hammerings
were required to form each length of tube. The process
was expensive, and labour intensive. Many tube forgers
were employed in the works, and the tubes were produced
in lengths of around 4 feet.
As a result of the primitive
manufacturing techniques then in use, the industry
couldn’t keep up with the growing demand for tubes, and
so something had to be done to both increase the supply
and reduce the manufacturing costs.
|
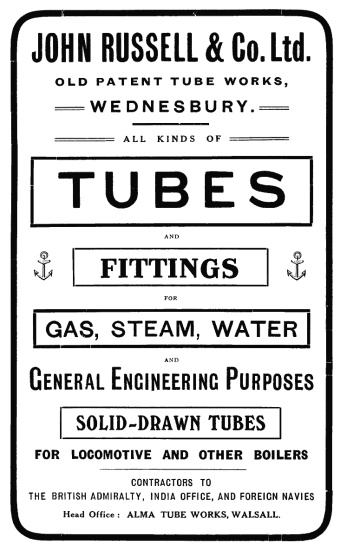
An advert from 1918. |
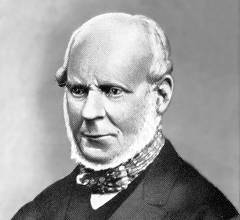
Cornelius
Whitehouse. |
The solution came in 1825 thanks
to Cornelius Whitehouse who worked for Edward Elwell at
Wednesbury Forge. He heated the whole strip in one go,
in a hollow fire of the type used by the edge tool
makers at the forge. He then shaped the strip and welded
the edges of the seam in one operation by drawing it
through a pair of semi-circular dies.
During the process the tube was butt
welded so that the edges of the seam were joined without
an overlap. The process produced an accurately shaped
tube with smooth inside and outside surfaces. Whitehouse had no need for his
invention, and on Elwell’s suggestion he took it to
James Russell who agreed to help him take out a patent
for the process. |
|
|
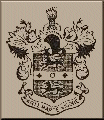 |
Read about Cornelius
Whitehouse |
|
|
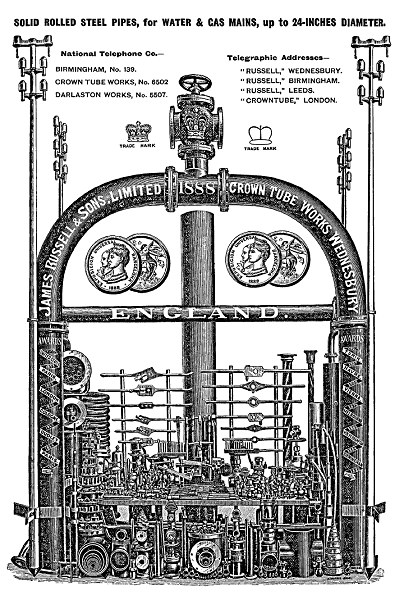
An advert from 1896. |
After the patent had been granted,
Russell purchased the rights from Cornelius on the
understanding that he would pay him the sum of £50
annually for the life of the patent. The invention
revolutionised the industry, because for the first time
tubes could be made quickly, cheaply, and in longer
lengths. Originally a man could produce around 25 four
foot lengths in a day, but now the same man could
produce 200 eight foot lengths in the same time. As a
result Crown Works now led the industry and became well
known throughout the world.
Unfortunately success came at a price. Other
manufacturers, still using the old methods, greatly
resented the company, also the tube workers who had lost
their jobs because of the introduction of the new
process, were very angry. Cornelius Whitehouse was even
fired-on by hostile demonstrators and as a consequence
always kept a loaded gun by his bedside. Russell built a
high brick wall around the works, topped with iron
spikes, to keep out the hostile crowd and prevent anyone
stealing the secrets of his process. F. W. Hackwood
mentions that some of the would-be spies even rented a
row of houses that were adjacent to the works, in the
hope of observing the process. |
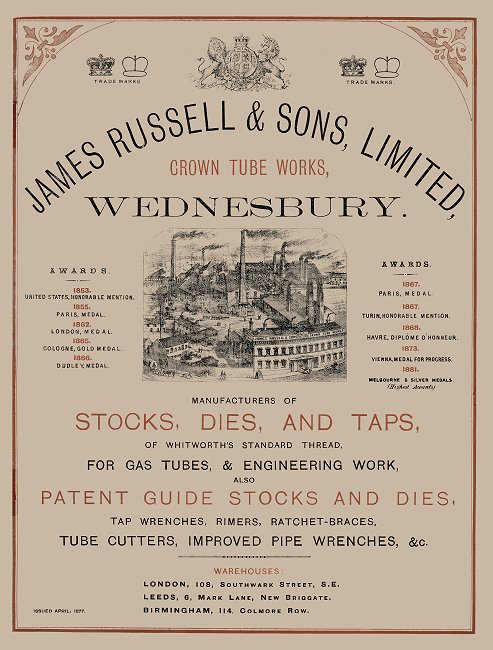 |
As well as producing tubes of all
kinds, the company also made a wide range of tools for use
with the tubes, and also for use in industry generally.
The image on the left shows the front
cover of Russell's April 1877 tool catalogue. |
A lovely image of Crown Tube Works
from the April 1877 tool catalogue, as seen above. |
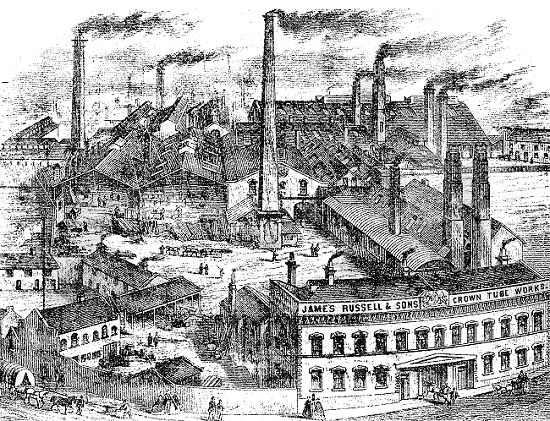 |
Some of the tools from
the 1877 catalogue: |
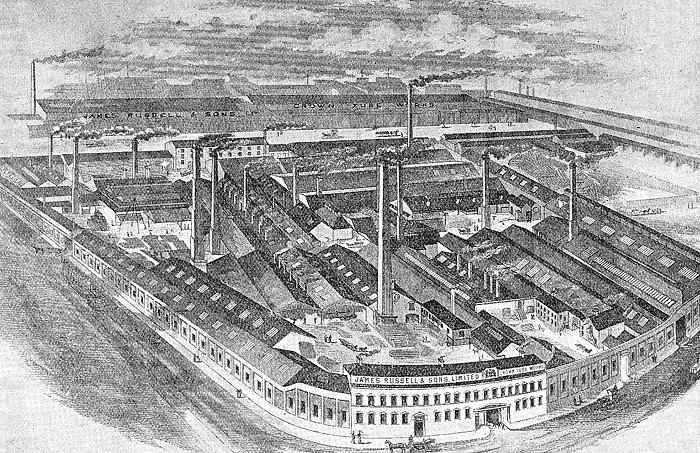
Crown Tube Works in 1905.
Russell had to
spend large sums of money towards legal proceedings to
protect his patent from infringement. In 1838 he
obtained a 6 year extension for the patent on the
understanding that he would pay Whitehouse £500 annually
during that time.
Crown Works became one of the town’s
most important employers and the extension of the patent
was celebrated in the town. By James Russell’s death in
1849 the works employed around 200 men who were
producing well over 4 million feet of tubing a year.
After his death the works were run by his son John James
Russell and by 1865 were producing over 5,300,000 feet
of tubing a year. John added a foundry to the works to
make tube fittings and built a mechanic’s institute for
the workers, complete with a library, classrooms and
lecture hall.
In 1866 John
found himself in financial difficulties through no fault
of his own. The company’s London agent had been
embezzling large sums of money, which resulted in the
business being transferred to a limited company; James
Russell & Sons Limited. John became chairman and most of
the shares were purchased by the company’s employees.
|
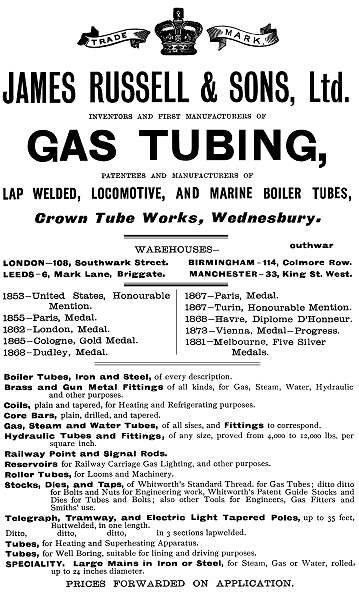
An advert from 1905. |
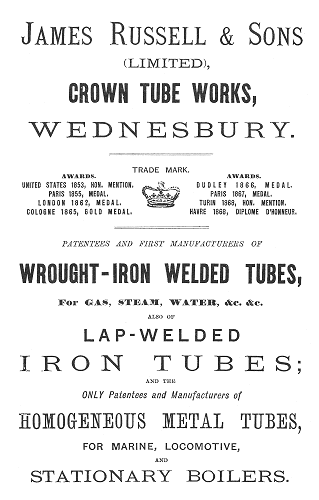
An advert from 1873. |
Crown Works retained its dominant
place in the industry in spite of other large UK
manufacturers, and exported its products to many
countries including France, Germany and Russia.
By 1889 nearly 1,100 people were employed at the works,
and before the turn of the century the company opened a
galvanizing plant at Darlaston.
The 1880s saw
the introduction of steel making in Wednesbury using the
Siemens open hearth furnace, and as a result Crown Tube
Works began to produce seamless steel tubing, but their
main products were still made from wrought iron, which
continued to be popular because it didn’t corrode when
used for water or gas.
By the turn of
the century the Crown Tube Works began to suffer from
lack of investment, which would eventually lead to its
downfall. |
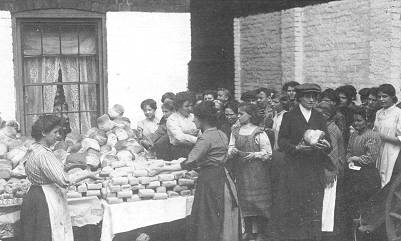
Striker's wives and children
queuing for bread. |
In 1913 a large strike began in Wednesbury, which
effected many of the local companies.
It started on 9th May when 200 workers from Crown
Works demanded higher wages. Large numbers of strikers
gathered in the Market Place |
The strike had a great impact on the local companies
and was a time of great hardship for the strikers. The
strike eventually ended after the employers agreed on a
minimum wage of 22 shillings a week for unskilled
labourers.
They also agreed to allow their workers to join
trades unions. |
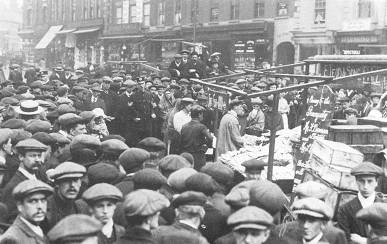
Strikers gathering in the Market
Place for handouts of free food. |
The works still
relied heavily on man power. During World War One the
wages bill amounted to 27% of their sales. A proposal to
modernise the works and install the latest machinery led
to a disagreement between the directors, which got
completely out of hand. Things were so bad that the
business could not continue to operate, and as a result
87% of the capital was acquired by John Russell &
Company who set about the task of sorting things out.
The new owners
found that the factory was “a rabbit warren of small
shops impossible to supervise”. Many of the antiquated
machines were only suitable for scrap, the men were
obstructive and the foremen had no control over them.
They were very critical of the management, who had no
accurate means of stocktaking or analysis of sales, and
hardly ever visited their depots.
Crown Tube Works was bombed in
World War One during a Zeppelin raid. On 31st January,
1916, nine German Zeppelin airships left their bases to
carry out bombing raids over England. The target was
Liverpool, but two of them got lost and ended-up over
Wednesbury. One of them, L21, captained by 45 years old
Max Dietrich dropped bombs on Tipton, Bradley,
Wednesbury and Walsall before returning home. As it
neared Wednesbury, the airship flew across the
relatively dark area of Lea Brook, heading for the
brightly lit town centre. As it travelled towards the
High Bullen, bombs were dropped around King Street and
on the Crown Tube Works, setting the huge factory
alight.
Sadly one of the bombs destroyed
the house at number 13 King Street and badly damaged
number 14 next door, killing four members of the Smith
family. They were Joseph Horton Smith, aged 37, Nellie
Smith, aged 13, Thomas Smith, aged 11, and Ina Smith,
aged 7, whose body had been blown onto the roof of the
tube factory. |
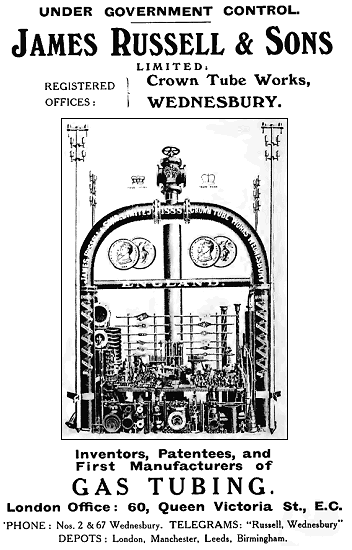 |
The advert opposite and the
text below were taken from the 1918 Wednesbury Official
Handbook. |
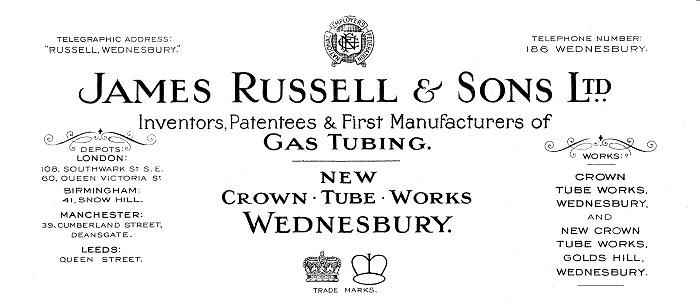
A letterhead from 1929.
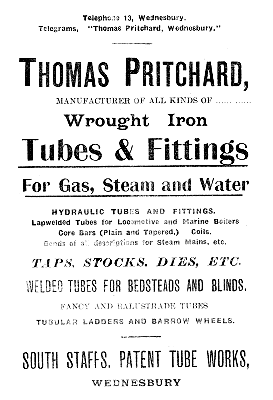
An advert from 1922. |
The decision was
taken to close and demolish Crown Works and temporarily
transfer the business to their Walsall factory and the
old Wellcroft Street works at Wednesbury. They
also opened a new tube works at Runcorn and built a new
Crown Tube Works at Hill Top, near the railway and the
Tame Valley Canal. Unfortunately both ventures were
unsuccessful and the company sold out to Stewarts and
Lloyds in 1929.
In 1928 Stewarts and Lloyds also
acquired another tube works in Wednesbury, the Prothero
Steel Tube Company Limited, founded in 1926. They
manufactured hot rolled and cold drawn weldless tubes.
Just before the outbreak of war in 1939 the Crown Works
were equipped with shell making equipment to produce
shell forgings as part of the war effort.
One remnant of the old Crown Tube
Works at the High Bullen remained until 1989, that was
George Croft's Bright Drawn Steels.
|
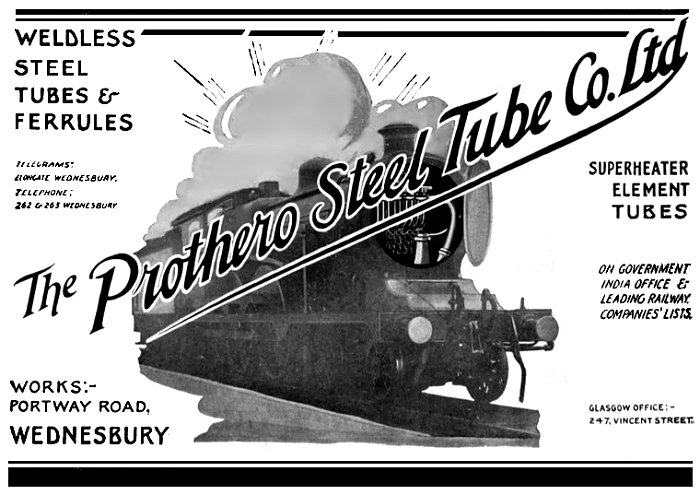
An advert from 1927. The
Prothero Steel Tube Company Limited, Portway Road,
Wednesbury manufactured hot rolled and cold drawn
weldless tubes. |
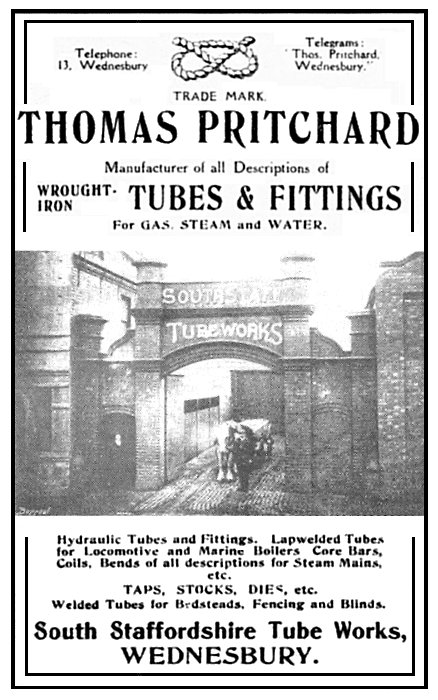
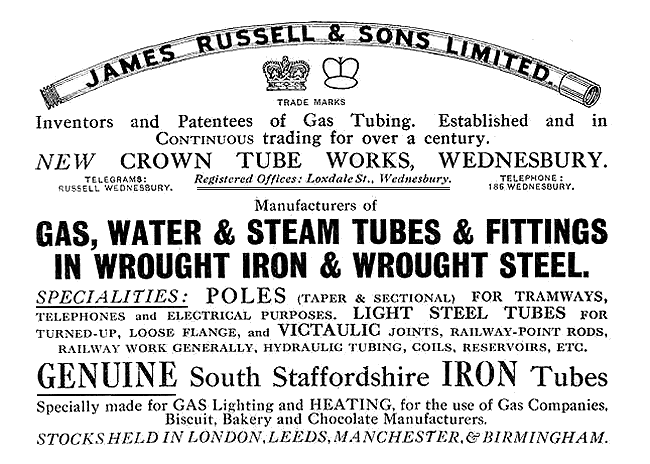
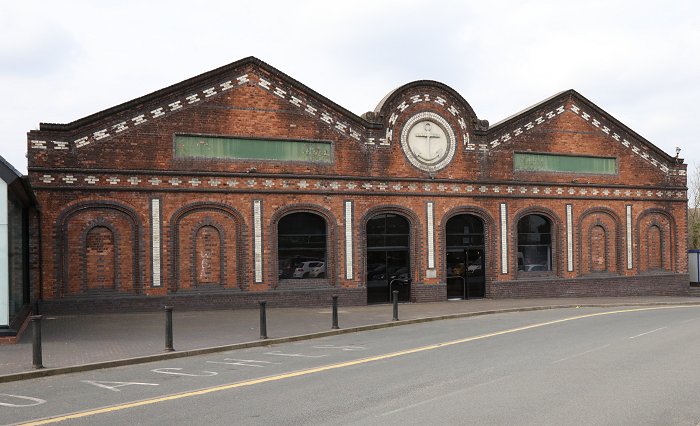
The frontage of John Russell's Old Patent
Tube Works can now be seen at the Black Country Living Museum.
Globe Tube Works
In 1849
Cornelius Whitehouse founded the Globe Tube Works at
Holloway Bank, the first joint stock limited company in
the town. Unfortunately he was no businessman and the
company failed in the 1875-1886 depression, the only
tube works to do so. He died in poverty in 1883. The
works reopened in 1882 after being acquired by John
Spencer. The factory remained in business until 1935
when John Spencer Limited was taken over and closed by
Stewarts and Lloyds.
|
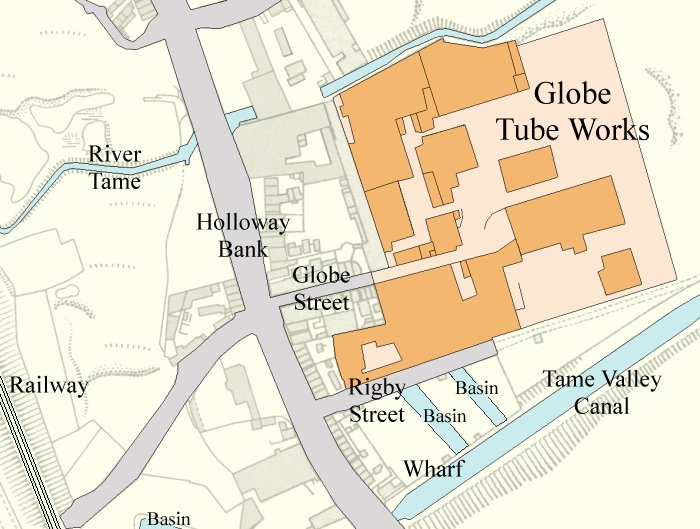
The location of Globe Tube Works.
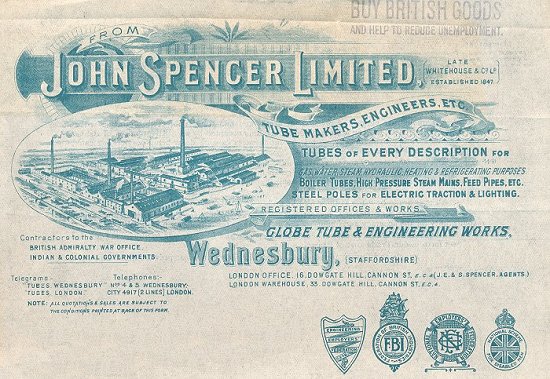
A letterhead from 1927.
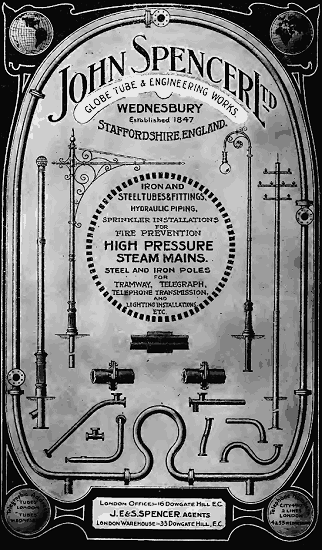 |
The advert opposite and the
text below were taken from the 1918 Wednesbury Official
Handbook. |
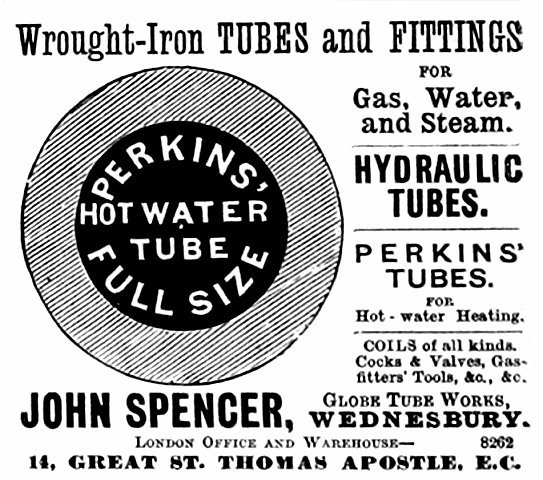
An advert from 1889.
Other Early Tube Works
In the 1850s and
1860s a number of ex-Crown Works employees set
themselves up in business making hand-forged tube
fittings. Such enterprises required little start-up
capital and mainly relied on the skill of the workers.
One of them, John Knowles, who founded Walsall Street
Works in 1850 went on to become the main producer of
tube fittings. Others tube manufacturers were Job
Edwards’ Junction Works founded in 1863, and Eagle Works
founded in 1880. The business was eventually taken over
by Wellington Tube Works.
James McDougall
founded the highly successful Hope Patent Tube Works in
1869 which became the first factory in the area to
produce weldless tubes. Sales of the tubes were
extremely high thanks to their many and diverse uses
including bicycle frames and bedsteads. In 1913
McDougall purchased the Imperial Tube Works from Isaac
Griffiths & Sons Limited.
|
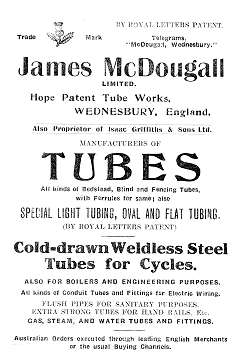
An advert from 1922. |
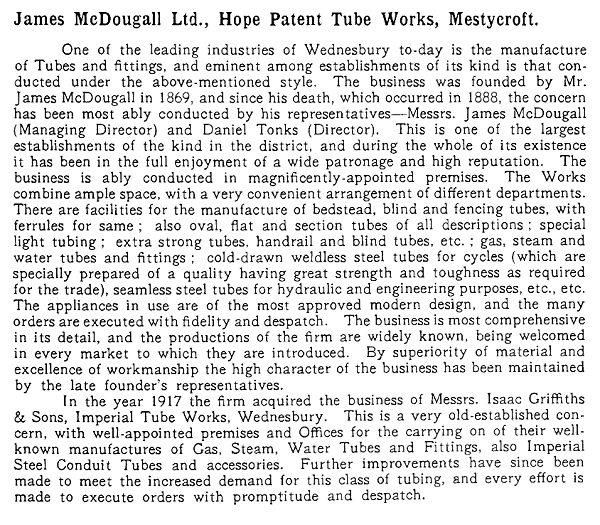
The text above and the advert
below were taken from the 1918 Wednesbury Official
Handbook. |
Hope Patent Tube Works produced a
wide range of products including:
bedstead, blind, and
fencing tubes, and ferrules; special light
tubing; oval and flat tubing; cold-drawn
weldless tubes for cycles; boiler tubes;
electricity conduit tube; electrical
fittings; sanitary flush pipes; strong tubes
for hand rails etc; gas, steam, and water
tubes, and appropriate fittings |
The company was eventually taken
over by Helliwell's Aircraft.
|
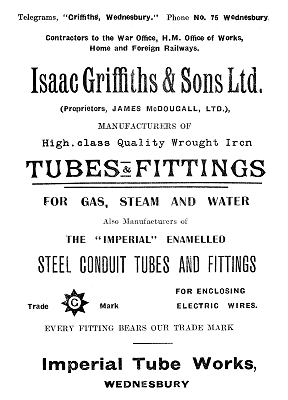
An advert from 1922. |
|
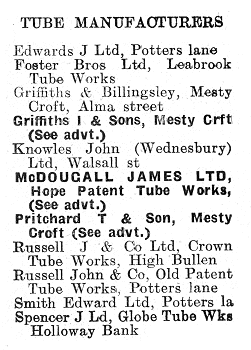
The list of tube makers in Cope's
Wednesbury & Darlaston Blue Book of 1922. |
|
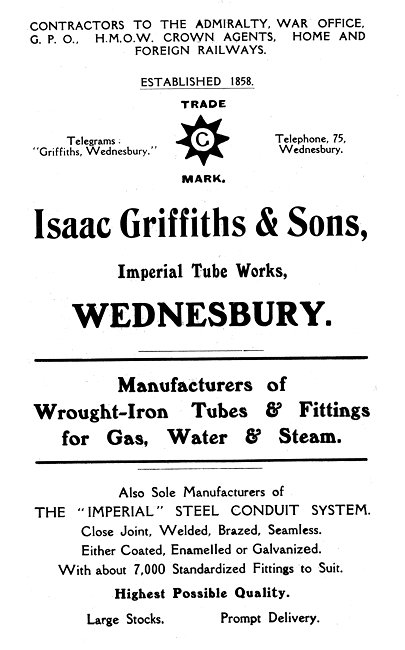 |
An advert from 1908. |
From the 1918 Wednesbury Official
Handbook.
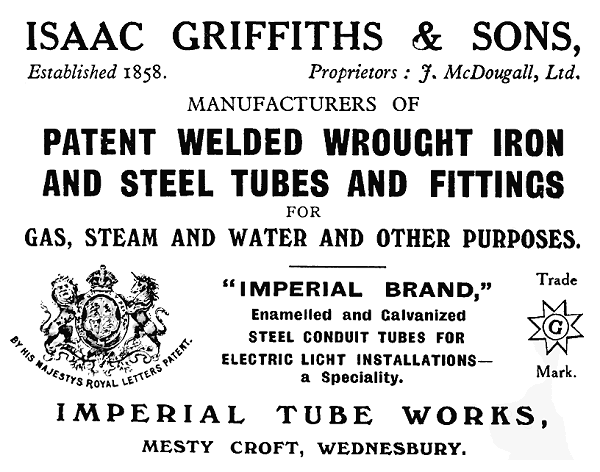
An advert from 1918. |
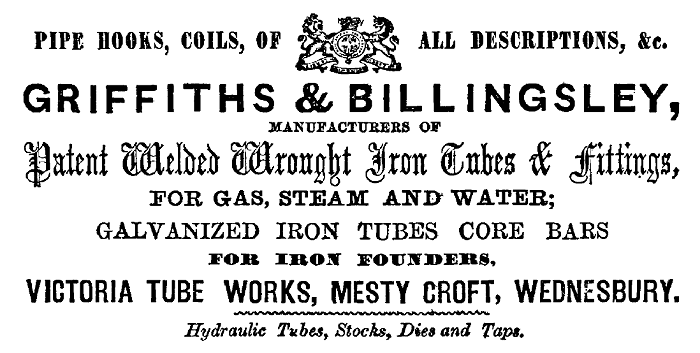
An advert from 1851. |
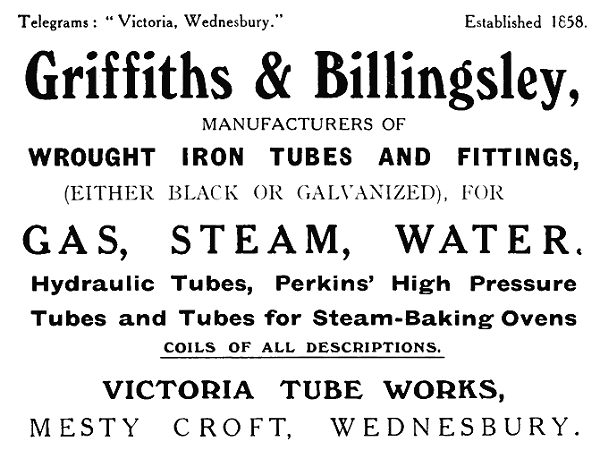
An advert from 1918. |
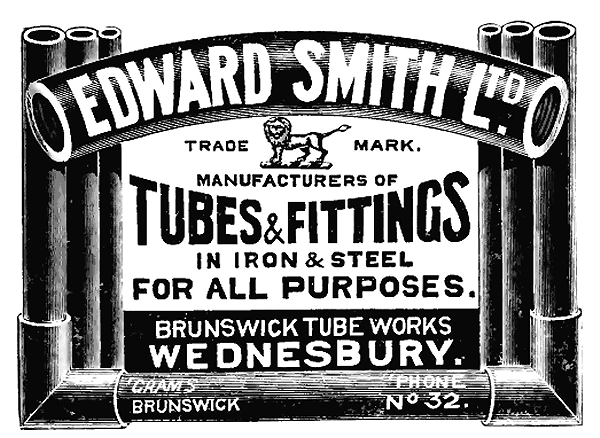
An advert from 1918. |
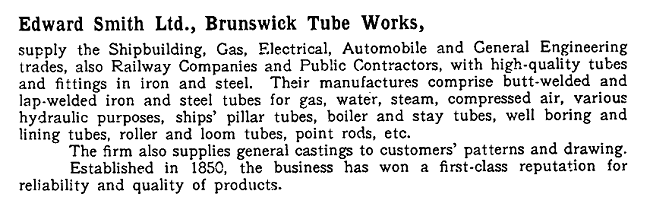
From the 1918 Wednesbury Official
Handbook. |
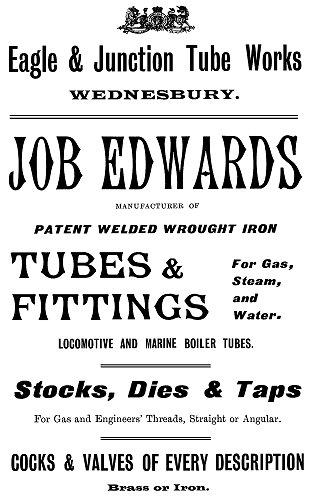
An advert from 1905. |
|
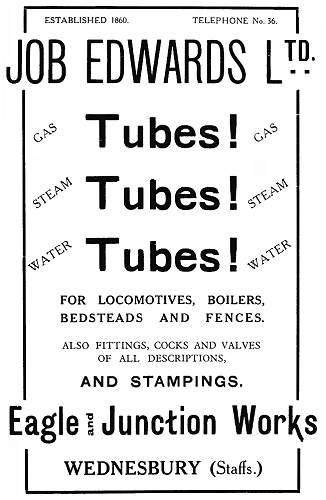
An advert from 1918. |
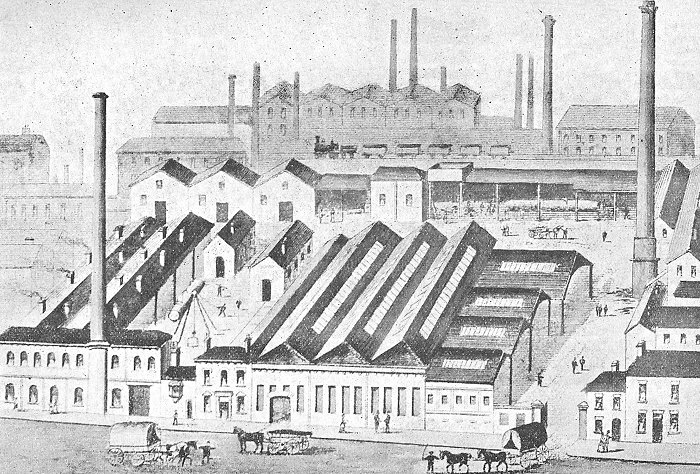
Eagle and Junction Tube Works.
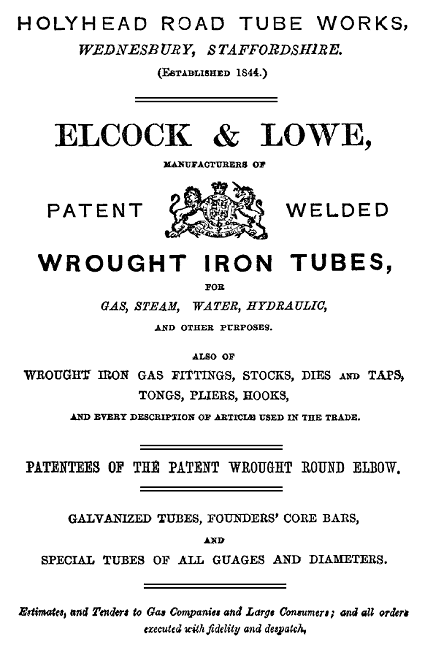
An advert from 1865.
Foster Brothers
Thomas Foster was an ex-Crown Works employee, who
later worked at Globe Works, Wednesbury and Ridgacre
Lane Tube Works in West Bromwich. In 1887 his two
sons, Thomas and Humphrey founded Ratcliffe and
Foster with Mr. Ratcliffe, an experienced
businessman. The business was set up at the site of
the old Lea Brook Iron Works, alongside the Walsall
Canal in Leabrook Road, where their first batch of
tubes was produced in 1888.
In 1893 Thomas Foster senior,
helped his sons to buy-out Mr. Ratcliffe and the
firm was incorporated as Foster Brothers Limited.
Unfortunately before the transaction was completed,
Thomas junior died, leaving Humphrey in charge. A
few years later, Thomas senior died. He had been
running the tube works in Ridgacre Lane, West
Bromwich, with another of his sons, John Foster. The
West Bromwich site was sold and John joined his
brother Humphrey at Leabrook Road, bringing much of
the better machinery from Ridgacre Lane with him.
By this time, Foster Brothers
was very successful, producing tubes, wrought-iron
fittings, cocks and valves, both in iron and brass.
Many of the products were exported throughout the
world. In 1902, Humphrey junior joined the firm, as
did his younger brother Kenneth in 1918. The firm
also manufactured tubes for the railway companies
and specialised in high pressure tubes and fittings.
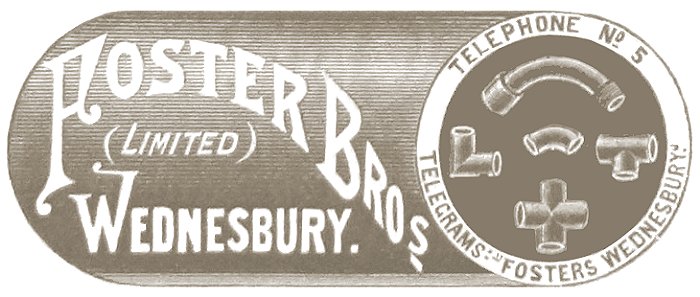
By the 1960s the firm had
expanded with the formation of two subsidiary
companies, Foster Brothers (London) Limited, based
at Clapham and Foster Brothers Plastics Limited at
Wednesbury.
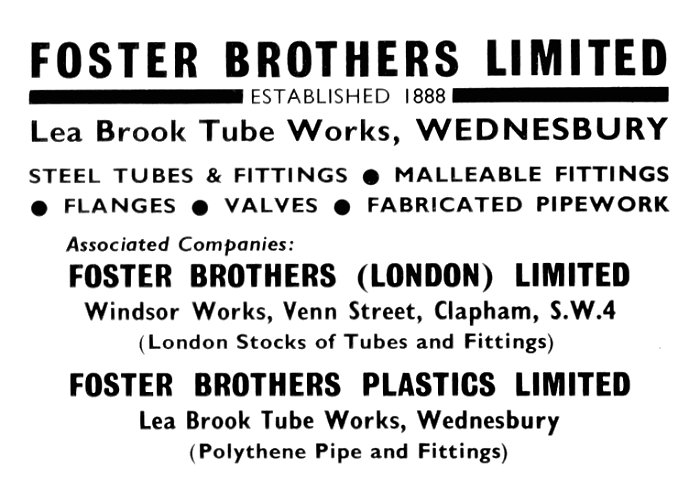
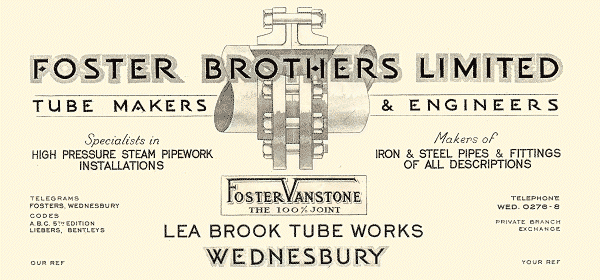
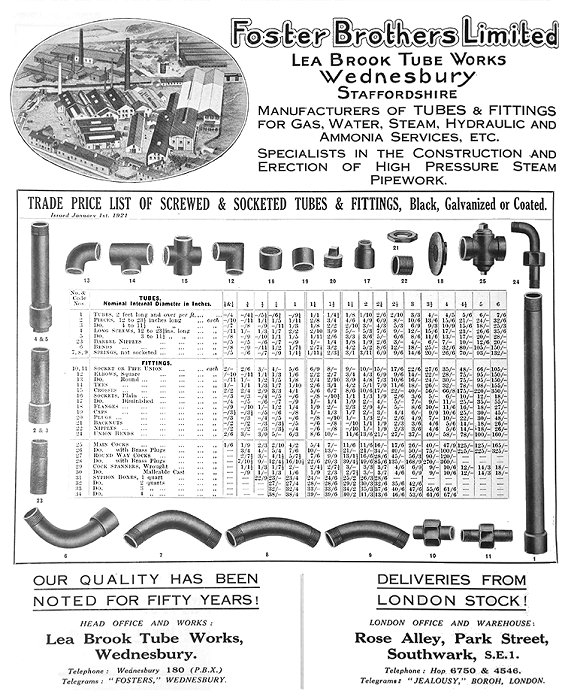
Sadly the business went into
liquidation in 1985, when liquidators were
appointed, as can be seen from the following notice
in the London Gazette.
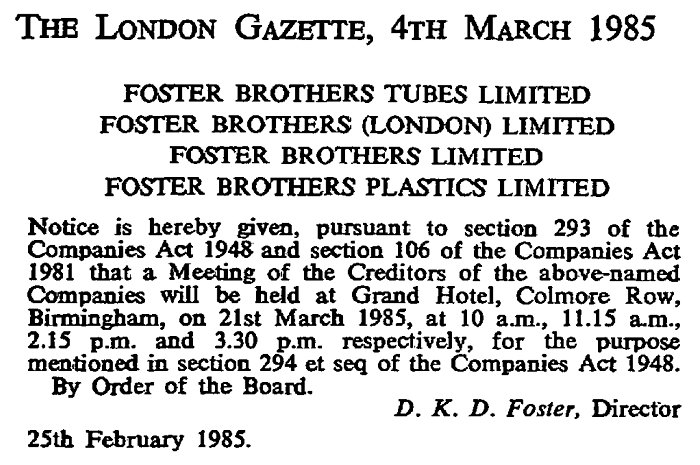 |
Decline of the Industry
In the 1850s and 1860s competition
from the new tube works at Halesowen, Birmingham, and
Wolverhampton began to have an effect on Wednesbury's
tube industry.
In 1900 the town still had a monopoly on
tapered tubes that were mainly used for telegraph poles
and electric tramways. The two main suppliers were Crown
Tube Works and Globe Tube Works. |
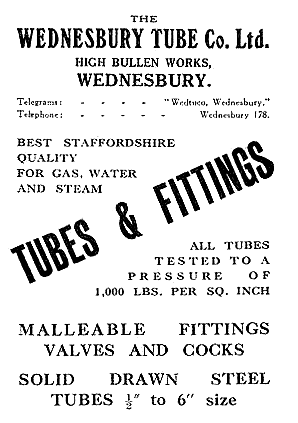 |
America and Germany increased their import duty on
imported tubes to protect their own manufacturers, who
by 1914 were exporting large quantities of tubes to the
UK.
By World War One Wednesbury had lost its dominant
position in the industry. The largest manufacturer at
the time, Stewarts and Lloyds, of Halesowen easily
exceeded Wednesbury's total annual production.
Wednesbury's older factories were suffering from a
general lack of much needed investment. Much of the
machinery was old-fashioned and by 1906 the wages bill
amounted to 84% of the total production cost.
The town
continued to concentrate on iron tubes and by the 1930s
many of the factories had closed. |
In 1924 Griffiths & Billingsley
Limited, of Alma Street was purchased and closed by the
British Tube Association. In 1935 it was the turn of
Edward Smith Limited, who were purchased and closed by
the Wellington Tube Works.
Other companies survived for much
longer. John Knowles Limited of Walsall Street was
purchased by Tipper Brothers. It was still going in the
1960s as were Thomas Pritchard & Company, and Foster
Brothers.
In 1937 a new company, founded by
Percy Newman appeared, and
built a large up-to-date factory. This was Newman Tubes
Limited in Holyhead Road who began to produce cold drawn weldless steel tubes.
In 1947 a new automatic mill was installed for
the production of electrically welded tubes.
The business became Newman-Monmore
Tubes of Western Way, one of Wednesbury's main
tube producers.
|
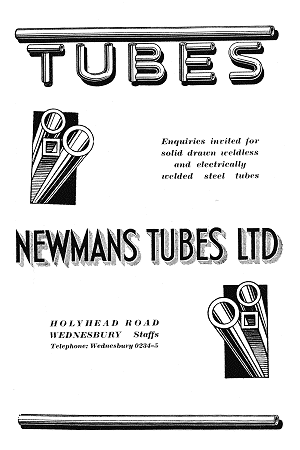
An advert from 1949. |
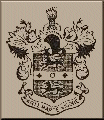 |
Return to
industries |
|