The arrival of steam-powered machinery
greatly increased production in Victorian factories, and led
to the development of much larger and more powerful
machines. Some of the steam engines were massive, such as
the blowing and hoist operating engines used in ironworks to
provide the air blast for blast furnaces, and to power the
hoist used to raise the barrows of burden to the top of the
furnace. Sometimes engines of this type could develop 150hp.
and so large boilers were often used.
In the middle of the nineteenth
century, boilers were made from sections of rolled boiler
plate, joined by simple overlapping joints, some running
around the boiler and others along the length of the boiler.
The joints and the double thickness overlaps were stronger
and less flexible than the surrounding metal, which could
lead to internal cracks or deep pitting caused by variations
in the boiler pressure. The internal cracks could corrode,
further reducing the strength of the boiler.
Such boilers needed regular inspection
and maintenance, and constant monitoring when in use.
Something that was often not fully understood by factory
owners, and their employees. Correctly operating safety
valves were essential. Sometimes operators would screw the
safety valves down to prevent them operating properly, and
so increase boiler pressure to get more work out of their
machines. Often the dangers of high pressure steam were not
fully appreciated. The effects of a boiler explosion could
be catastrophic.
Boiler explosions were not infrequent
in the latter half of the nineteenth century, but the risks
continued to be largely ignored. The sudden failure of a
boiler could result in the total destruction of nearby
buildings, with large pieces of iron being blasted through
the air, often travelling considerable distances. Buildings
some distance away could be damaged, and windows shattered.
People were often killed, scalded, or badly injured, which
had a large impact on the local community.
Wolverhampton suffered from the
terrible affects of several such explosions, which were
often described in graphic detail in the newspapers and
magazines of the day. One of Wolverhampton’s prominent
citizens, who suffered from the after effects of a boiler
explosion that shortened his life, was local industrialist
George Benjamin Thorneycroft who owned Shrubbery Ironworks,
and a number of coal mines, including several in Willenhall.
|
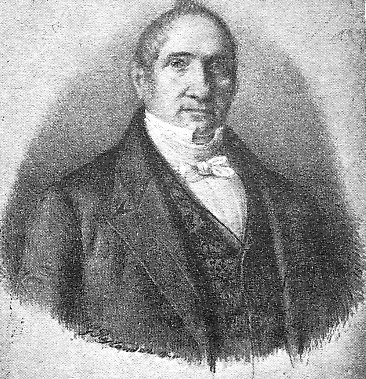
George Benjamin Thorneycroft. |
In December 1845 a new pumping engine
was being installed in one of them, and George was there to
oversee the operation. Unfortunately the safety valve was
faulty, and the boiler exploded, killing one man, and
seriously injuring sixteen others, including George. On
regaining consciousness his first words were “Praise the
Lord O my soul.” Followed by “Who else was hurt?”
One year later, with his doctor, Mr. E.
Coleman, he presented himself before lecturing staff and
students at Queen’s College, Birmingham to demonstrate how
the severe burns covering much of his body, had been healed
by the use of cotton wool freely applied to the dressings.
Unfortunately he never fully recovered
from the effects of the explosion. As time progressed he
grew weaker, eventually becoming bedridden. |
In the early part of 1851 he suffered from brain
disease, and appeared to improve, but a relapse took place,
and he died on 28th April, 1851, at the age of 60. His
funeral procession was viewed by around 20,000 people who
came to pay their last respects. George,
who had been the town’s first mayor after its incorporation
in 1848, was a wealthy and generous man who eagerly
contributed to many organisations and charities. He was a
benefactor to the South Staffordshire General Hospital, and
a Justice of the Peace for Staffordshire and Shropshire.
Another
disastrous explosion
Six years after George’s death, a
terrible explosion occurred in Walsall Street, not that far
from Shrubbery Ironworks, at Benjamin Mason’s factory where
fire irons were made. Benjamin Mason himself had retired,
and the business was being run by his son, Benjamin Mason
junior. The explosion took place at around twenty to four,
on the afternoon of Friday 24th
April, 1857, and had terrible consequences. The
ground shook, and people within a half-mile radius of
Walsall Street thought that an earthquake had shaken the
area. A dense cloud of black dust rose above the factory and
pieces of iron, timber, bricks, building rubble, a human
body, and body parts flew through the air, damaging the
roofs of buildings for a considerable distance, and
shattering the east window of St. George's Church. |
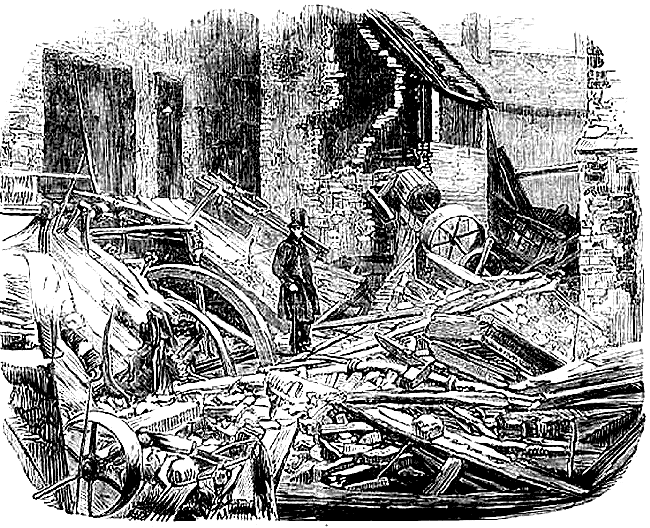
The aftermath of the explosion. From the
Illustrated London News, 2nd May, 1857.

The photograph on which the above
illustration was based. It must be one of the earliest
industrial photos taken in the area. Courtesy of David
Clare. |
Most of the factory and some of the
tightly-packed surrounding buildings had been completely
destroyed and converted into rubble. Next to the factory
stood Benjamin Mason’s three storey malthouse, which became
a pile of rubble, even though its walls were thirteen inches
thick. The egg-shaped, vertical boiler had been mounted
against the malthouse wall. It powered a small engine used
for the fire-iron factory, and also for a grindery, and
wood-turning establishment at the rear of the factory. At
the time of the explosion most of the employees in the
establishments had been at work. All that survived in the
factory was the tall substantial chimney, to which the
boiler had been fixed. The chimney completely shielded one
of the employees who was behind it in the malthouse at the
time of the explosion, saving his life. The grindery and the
wood turning establishment had their roofs blown-off, and
were badly damaged.
A piece of the boiler weighing 2
hundredweights had been hurled about a hundred yards. At the
time of the explosion, Benjamin Mason junior, and the
engineman, Joe Cornfield had just screwed the safety valve
down because the boiler feeding pipe had burst, and the
nearly empty boiler was red hot. They attempted to cool the
boiler by adding cold water, which quickly boiled and
produced a lot of steam. The boiler instantly exploded,
killing both of them. Joe was thrown through the air and
crashed through the roof of a nearby house. His clothes had
been torn-off, leaving him naked and bleeding. Many of his
bones were broken, and he was badly scalded. He died a few
minutes later. Benjamin’s fate was even more gruesome. His
body, minus arms, and the top of his head was found amongst
the ruins. One arm was found in Bilston Street near the
cattle market.
Another employee, Tom Nightingale, who
alerted Mason and Cornfield to the damaged feed pipe, and
was with them at the time of the explosion, escaped without
injury. Several others were not so lucky. Another colleague,
Tom Holdridge received terrible injuries and died that night
in the South Staffordshire General Hospital and Dispensary,
in Cleveland Road. Two children, Matthew William Turner aged
5, who had been playing in the street, and Isabella Hall
aged 12 were also killed, both by falling debris. Isabella
had been on an errand to buy a writing book for her father,
who rushed to the scene of the explosion. He saw a policeman
carrying a body away from the scene and recognised her
frock. It must have been a terrible moment for him.
Another person was seriously injured,
and nine others received lesser injuries. A memorial service
was held on the following Sunday in front of the cattle
market, and an inquest took place at the Blue Ball Inn in
Bilston Street. At the inquest it was stated that the boiler
had been purchased second-hand, and installed six years
earlier. It had previously been enlarged, and repaired
several times. It was also stated that the water in the
boiler had been allowed to go so low that the metal was
red-hot. The explosion occurred when cold water was
poured-in.
The inquest came to the conclusion that
the deceased persons died as a result of their injuries
received by the explosion of the boiler, and that the
explosion was caused by the gross negligence of Benjamin
Mason junior.
The
explosion at Millfields Iron Works
Five years later another catastrophic
boiler explosion occurred about a mile and a half away from
Walsall Street, at Millfields Iron Works. The explosion took
place on Tuesday 15th April, 1862, at about 11.15 a.m.
The factory, previously owned by the
Birmingham Banking Company, was eleven years old. It closed
in 1858, and had been idle for four years. There had been a
previous accident on the site, which caused the death of
five workers on 5th May, 1857.
In early 1862 the factory was purchased
by Thomas Rose, who had been looking for sometime for a
suitably-equipped iron works. Having found what he wanted,
he employed around 40 men and started production, in the
hope that he would make his fortune thanks to the insatiable
demand for iron at the time.
The factory consisted of two forges and
three mills. At the time only one forge was in operation. It
consisted of twenty puddling furnaces, a shingling hammer, a
rolling mill, and an 80 hp. steam engine that worked the
massive shingling hammer. Steam for the engine was provided
by two cylindrical boilers with hemispheric ends, both about
twenty feet long, and nine feet in diameter. The boilers
were heated by the hot gases from the flues of some of the
puddling furnaces. One boiler was heated by four flues, the
other by two. They were made by John Elwell & Company, at
Priestfields.
When the explosion occurred, the puddlers from the four furnaces attached to boiler number
one, were taking their red-hot balls of puddled iron to the
shingling hammer to produce puddled bars, which were cut-up,
reheated, and rolled into merchantable iron in the rolling
mill. About forty people were at work at the time. |
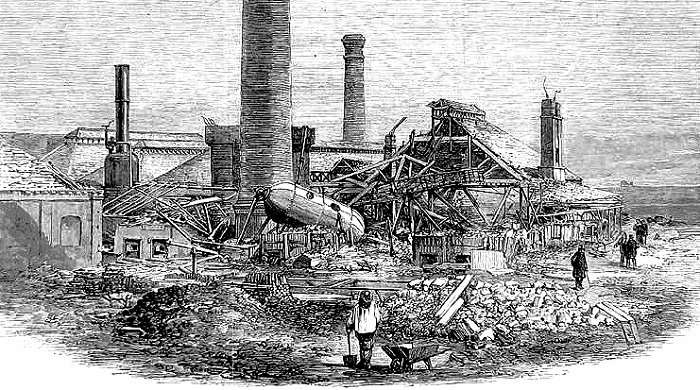
The scene of the boiler explosion at
Millfields Ironworks. From the Illustrated London News 26th April,
1862.
Everything seemed to be going well,
until without warning, an excruciatingly loud noise, like a
clap of thunder, shook the building. The roof blew off, the
walls collapsed, and the building was totally destroyed.
Boiler number one had exploded and been torn apart. Three
quarters of it, weighing around eight tons was tossed 200 or
300 feet into the air and landed on the other side of the
railway line, over three hundred yards away. The other
quarter, torn into three parts, had been blown through the
forge, each part travelling in a different direction,
tearing down the roof supporting pillars, and ripping the
massive roof timbers apart. The furnaces were also torn
apart, sending their contents, consisting of the molten
metal and the burning fires, throughout the factory, to
complete the appalling catastrophe.
There were bodies and seriously injured
people everywhere. Some were buried beneath the molten iron,
or beneath fragments of the fires, or red-hot brickwork.
Some people were badly injured by the falling fragments,
many of which fell on the boats on the adjacent canal.
Within an hour fourteen bodies had been recovered, all of
them shockingly mutilated. One person lost his head, which
was never recovered, and another had been cut in two. The
bodies were so badly damaged that few could be positively
identified, something that was not helped by the fact that
some of the workers had only been taken-on that morning.
Fifteen of the injured were taken to
the South Staffordshire General Hospital, and six to their
homes. Three died on the way to hospital, and another died
whilst on his way home.
The damage to the works was estimated
at between £2,000 and £3,000. The area around where the
boiler stood was showered with scalding hot water from the
boiler, which indicated that the boiler was full at the time
of the explosion. Below the water line was a seam, and a row
of rivets with the heads burnt off, which suggested that the
explosion was caused by poor quality joints in the boiler
barrel. The night before the explosion, the engineer on duty
had noticed a loose rivet, which should have started alarm
bells ringing.
The explosion, which had been heard for
miles around, demolished everything within a hundred yards
of the factory. One lucky survivor, 12 years old Billy
Williams, was on his second day at work, and standing near
to the boiler when it exploded. He was blown more than 200
yards, and ended-up with little more than a few bruises.
The rescuers who quickly attended the
scene, were faced with a huge pile of twisted metal, broken
smouldering masonry, and the desperate cries of injured and
dying men. Throughout the day they searched for bodies,
often only finding limbs, or a head. Three victims who were
killed by falling debris were on a canal boat over a hundred
yards away. Twenty men died at the scene, and another eight
from their injuries.
It was discovered that the boiler had
not been properly inspected or maintained. It had not even
been inspected since Thomas Rose reopened the factory, even
though it had been idle for four years. Yet again the
factory owner and his employees had failed to appreciate the
dangers of high pressure steam.
There were other boiler explosions in
the area. One on 5th November, 1884 at Spring Vale killed
three workmen, and a second at Tupper & Company’s ironworks
at Bradley on 20th January, 1903 killed four workmen and
injured another eleven. It took a long time before boilers
were treated with the respect they deserve, and were
properly maintained, and monitored. |
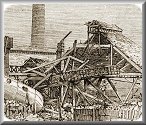 |
Return to
the
previous page |
|