Further Improvements
There was one other problem to be overcome
before production was fully efficient. The poor quality of the
steel meant that the tools used in the machines had to be
re-ground as often as twice a day and a setter could only look
after between 7 and 10 machines.
|
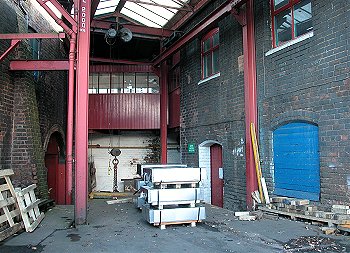
Newly arrived steel sheets about to be
taken into the Steel Shop. In the background is the crane which
enabled the one ton bundles to be lifted. |
At this time there were great improvements in
steel and Mr. Somerville decided to buy the new better quality
steel for both the tacks and tools.
Experimentation was carried out to find the best material
from which to make the tools. Several types of steel were tested
including Carbide steel, which was too brittle and shattered. In
the end cobalt chrome from Balfour Darwin of Sheffield filled
all of the requirements. It was purchased ready-forged to the
correct size, to reduce the amount of scrap. |
At the time there were many U.K. steel
manufacturers and suppliers, but most have now gone. With the
new steel the tools only had to be reground every four days and
a setter could now look after 15 machines. The choice of the new
steel for the tacks was also arrived at after a little
experimentation. Initially HR4 (blue strip mill as it was
called) was used, but the surface still had to be pickled. A
change was made to HR4 pickled (HRP), where the steel had been
treated in an acid bath to pickle off the hard surface, leave a
clean surface, and prevent flaking. Later, a cold-reduced
material was used, which being slightly softer gave rounder
heads on the tacks and formed them better. It also greatly
increased the life of the tools. |
One problem that occurred with the early batches
of the pickled steel was that it was disliked by upholsterers.
They used a magnetic hammer and would place a number of tacks in
their mouths and remove them one at a time with the hammer.
Because some of the acid from the pickling bath was still
present and the bluing process hadn’t got the tacks hot enough
to remove it, the upholsterers were left with an acid taste and
a burning sensation in their mouths. After this problem the
company had to ensure that their steel suppliers had totally
neutralised the acid during production. |
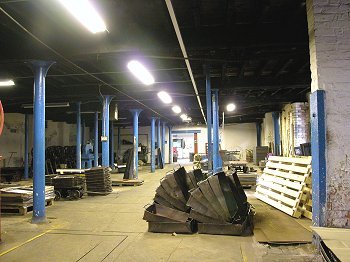
The steel shop in October 2004. It was now
an empty shadow of its former self as production was scaled
down. |
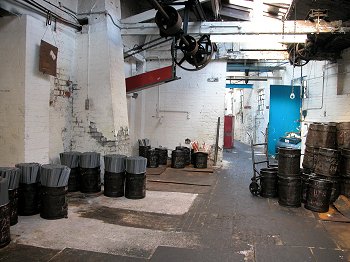
The strip store where the kegs of cut
strips were stored before being taken into the tack shop. |
Steel was purchased in one ton bundles, 26 inches
wide and 42 to 72 inches long. It was brought in various
thicknesses such as 1.8mm, 2mm and 2.3mm but commercial
tolerances could not be relied on. The thickness of each sheet
was checked under a gauging machine and sorted into stacks of
identical thickness. Thickness is related to the size of the
tack because of the diameter of the shank and the thickness of
the head. All of the stacks were marked with their actual gauge
and arranged ready for shearing. |
After all of the changes the company was finally ahead
of the competition, leading the field with the new production
techniques, which enabled the company to stay in business long
after all of the other U.K. tack manufacturers had disappeared. |
|