The Return of Nail Making
Dennis Somerville was an entrepreneur, he
purchased several smaller companies and built them up. One of
these, the Birmingham Nail Company, was purchased in 1986.
|
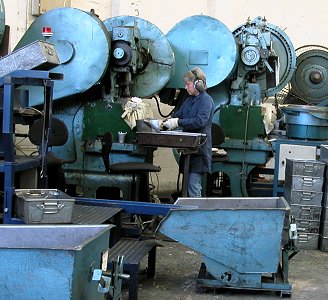
Dawn Sambrooks hand-feeding a nail
machine. |
At the time there was a reduction in the demand
for tacks and this purchase enabled the factory to keep going.
Production was moved to Commercial Road and modern presses were
used to produce the nails, which were traditionally made on nail
machines. This was the first time that nails had been made in
this way and some customers would not buy them because they
didn’t consider them to be cut nails. In reality they were a
better, more consistent and cleaner product than the traditional
variety. Many of the traditional manufacturers soon began to
distribute Crown Nail’s products in preference to their own. |
In the beginning there were 5 presses, all of
which were hand-fed. Initially there were problems with
reliability. The presses would only run for about an hour in
between breakdowns, mainly due to the poor quality of the tools.
Garry Kruczek, the Deputy Works Manager was given the job of
sorting things out. He was in charge of the fitting shop and was
responsible for all of the maintenance of the machinery.
Garry joined the company as an apprentice in 1971 and his
wife worked there for a while as a feeder on one of the
presses. |
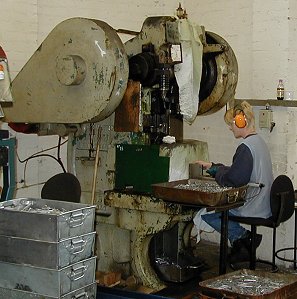
Hand-feeding one of the larger machines. |
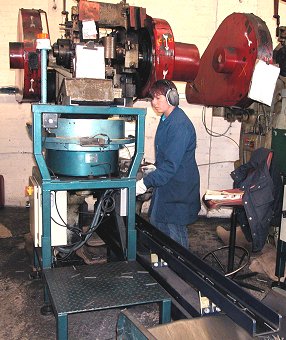
Julie Thompson operating an automatically
fed nail machine with bowl feed. |
Garry spent most of his time in the fitting shop
and when he started he worked with Bob Hawks, Johnny Winfield
and Geoffrey Weager, who occasionally came in from the tack shop
to give a helping hand.
After 18 months Bob passed away and Johnny left, and so for
several years Garry ran the fitting shop alone. In 1978 he was
joined by Shaun Thompson, a good engineer and machinist.
To overcome the problems with the presses, new tooling was
developed with the assistance of Richard Kent, from Kent
Engineering and made in-house. |
In order to reduce costs and labour it was
decided to produce automatic feeds for the machines. Garry rose
to the challenge and designed and built a very successful
pneumatically operated automatic feeding system, which remained
in use until production ended. Very clever bowl feeds were also
developed with the help of Tribal Automation. They oriented the
blanks in the right direction to be loaded into the magazine
that fed the press. |
The nails were cut from a steel strip in the same
manner as the tacks and were made to ISO 9002 and BS 1202 part
1. High quality steel was used and the company was justifiably
proud of its products. Different finishes were available for the
nails. They could be chemically blacked, galvanised, or brass
plated and were also available in a painted finish. |
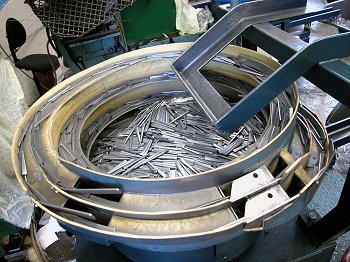
One of the clever bowl feeds in operation. |
Many types of nails were produced,
including cut floor brads and cut clasp nails. Cut nails have
more holding power than traditional wire nails and are used in
floorboards, breezeblock and the renovation of old buildings.
One of the company’s later products was rosehead nails for the
building industry, which if needed could be coloured.
At the beginning about one ton of nails was produced
each week and this eventually rose to about 15 tons a week. The
nails varied in size from 25mm clasp nails to 150mm long nails
for a Swedish customer. The nails were packed into 25 kilo
cartons. |
|
|
 |
|
|
Return to
Improvements |
|
Return to
the Contents |
|
Proceed to
The
Later Years |
|