John Harper & Company Limited, Walsall Road,
and Clarke's Lane, Willenhall.
By Bev Parker.
|
The firm was founded in 1790 in a small factory in Walsall Road, on part
of the site that was later to become Albion Works, which is believed to be
one of Willenhall's oldest established factories. It began life as the
lock-making business of William Brueton and William Harper, but little is
known about the company at that time. William Harper's son John, succeeded
his father who was described as a spring latch maker. The firm became known
as John Harper & Company. The first record of the company is an indenture
for John Harper junior, who began his apprenticeship at the factory in 1836
at the age of 15. |
When he completed his apprenticeship in 1840, John became a clerk at the
factory belonging to his uncle James Tildesley, an ironmaster, who ran
Albion Works, Somerford, Willenhall. James was greatly interested in
agriculture and financial speculation, and made a large amount of money from
the railway mania that was sweeping the country at the time. By 1844 John
was managing the factory which produced malleable and non-malleable iron.
James Tildesley suffered financially when the railway bubble burst, and in
order to settle a debt, the factory was transferred to John Harper and
Matthew Tildesley. But he retained the freehold of the land and buildings. John Harper Junior
and Matthew Tildesely then built a new factory called New Albion Works, to
distinguish it from the old Albion Works. The factory was on Walsall Road,
adjacent to John Harper & Company's premises, on the corner of what was to
become Albion Street, named after the factory. It is not known how it was
financed, but it appears that John Harper Senior criticised his son for
taking such a risk. The new business became known as John Harper Junior &
Company, to distance it from his father's firm, John Harper & Company, and
from 1846 included a foundry.
|
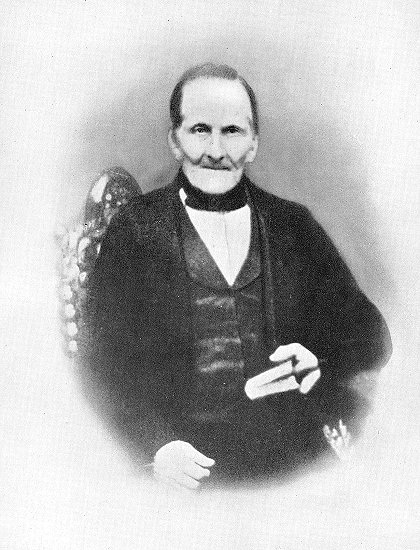
William Harper. |
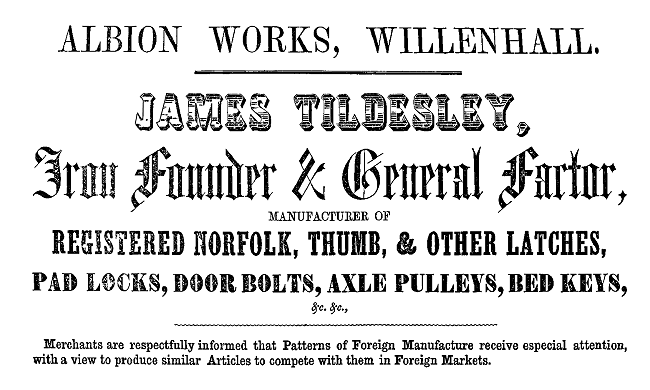
An advert from 1851. |
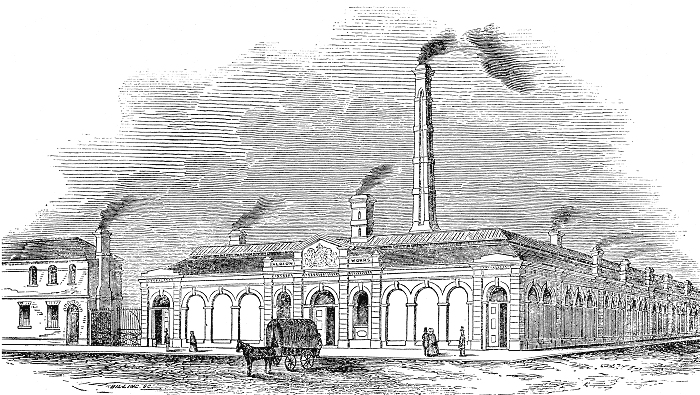
New Albion Works, later called Albion
Works. |
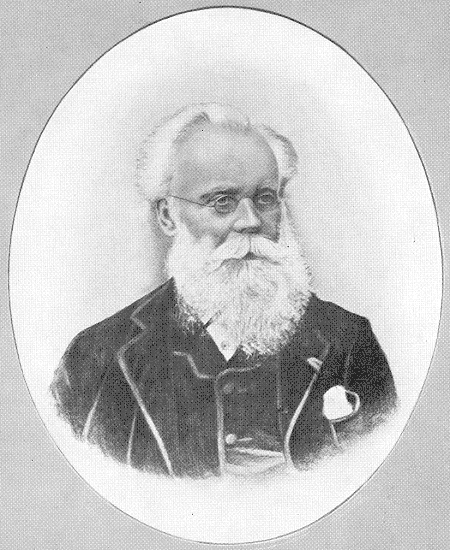
John Harper junior. |
Whilst all of this was happening, a revolution was taking place in the
casting of lock cases. A Mr. Mason of Bilston was hard at work trying to
perfect the casting of lock cases in malleable and non-malleable iron. He
was followed by Richard Tildesley, who perfected the process, and began
casting lock cases in Willenhall. By 1856 there were three ironfounders in
the town producing lock cases. They were Tildesley, Knowles, and John Harper
Junior. In 1852, Thomas Brueton's firm (William Brueton's son) had amalgamated
with John Harper & Company, Carpenter and Tildesley, John Fox and James
Lockett. By 1856 the combine had been acquired by John Harper Junior &
Company. The relationship between the various lock making firms is complex
because there were many marriages between the different lock making families,
such as the Tildesleys, the Harpers and the
Bruetons. And John Harper Junior outlived three wives and had two
families.
|
In an advert from that year, John Harper junior describes himself as
successor to Mr. James Tildesley, Mr. John Fox, Mr. John Harper senior, Mr.
J. Locket, and Mr. Thomas Brueton. He began to produce a wide range of
products including locks and latches, wood screws, plain and ornamental
light castings, to any pattern, either in malleable or common iron, and even
dog collars.
The firm began to produce general metalwork, and continued to
do so for the remainder of its life. |
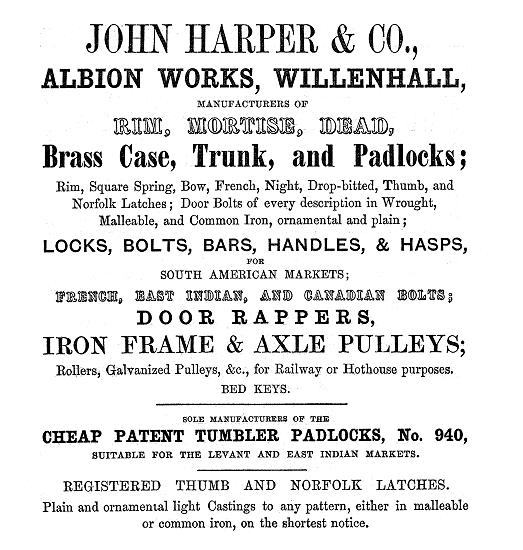
An advert from 1861. |
The firm was one of the first in the area to introduce and
develop machinery, and as a result was able to mass produce all
kinds of products, which became especially successful in export
markets. |
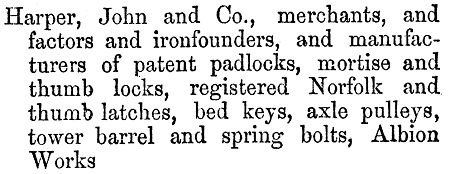
From Harrison, Harrod & Company's Directory &
Gazetteer. 1861. |
Its patented
tumbler padlock did well in the Levant and East Indies, where it sold at a retail
price equivalent to 1 penny. A visitor reported that "orders varied from 5,000
to 10,000 dozens at a time" and he watched a consignment of 1 ton, which was
equal to 40,000 iron clog sole nails being despatched. |
George Price of Cleveland Safe Works, Wolverhampton,
published "A Treatise on Fire and Thief-Proof Depositories and Locks
and Keys" in 1856.This includes the following description of John Harper's
activities at the time: |
One of the largest concerns is that of Messrs. John Harper and
Matthew Tildesley, and is called "Albion Works," where the various kinds
of locks, . . . . together with bolts, wood screws, etc., are produced
in vast quantities. We have inspected many different samples of locks,
etc., including patterns of locks, handles, bolts, and bars used in the
plantations of South America, which are made in large quantities, and
are supplied at regular periods. Messrs. Harper and Tildesley are also
the sole manufacturers of a patent tumbler pad lock which is
very saleable in the Levant and East India market, and for
simplicity and cheapness is one of the wonders of the age.
It is without exception the cheapest padlock in the world,
and it can be sold retail from one penny each. They have
been sold wholesale in quantities varying from five to ten
thousand dozen at a time. |
|
Harpers were expanding rapidly. In 1868 John Harper bought land behind
the existing works in Walsall Street and then leased it to the company, who
built factory extensions on it from time to time, extending Albion Street to
provide access. The 1868 deeds describe the land as follows: "A piece of
land bounded on the North East by a new street 10 yards wide, and diverging
in a north westerly direction out of the turn pike road leading from
Wolverhampton to Walsall, and on the west and north west by a brook course,
on the south west by land belonging to Jeremiah Hartill and on the south
east by the turn pike road leading from Wolverhampton to Walsall, or by the
stream running by the side thereof". |
The company hit hard times in the 1870s when Harper and Tildesley were
unable to meet their debts. To make matters worse, they quarrelled, which
lead to a lawsuit about some land and a bankruptcy.
In 1874 a trustee was
appointed, and the company's debts were fully discharged, but the
partnership was dissolved. John Harper Junior became the sole proprietor.
|
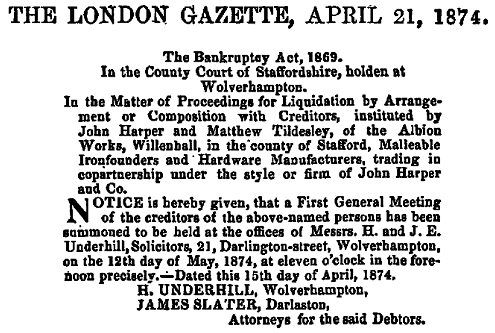 |
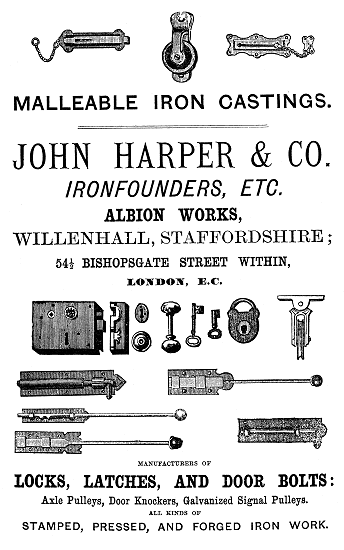 |
|
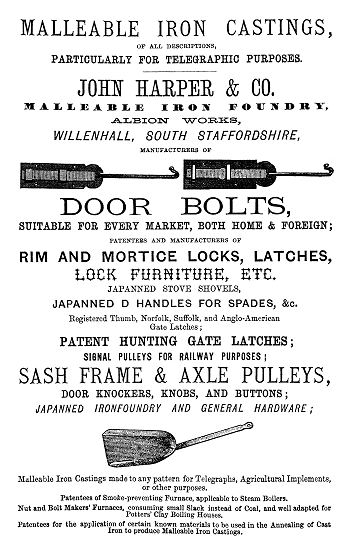 |
Two adverts
from 'Griffiths' Guide to the Iron Trade of Great Britain',
published in 1873. |
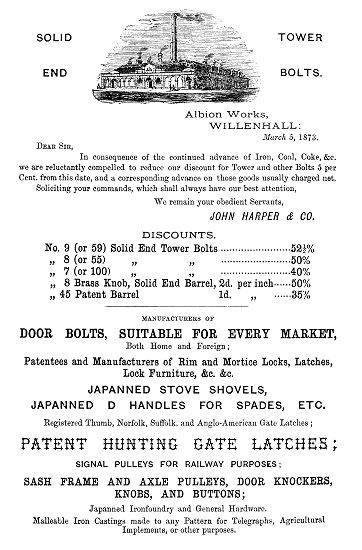
Another advert from 'Griffiths'
Guide to the Iron Trade of Great Britain'. |
The legal papers of that time describe Harpers as
Malleable Ironfounders and Hardware Merchants, no mention of common or grey
iron being made. Another deed of about the same date mentions "locks, bolts
and other articles of metal" and also "Coal Masters" which is no surprise,
because the area was extensively mined.
A wages
record in 1874 reveals the working week as of six full days, but the hours
are not stated. A good male wage was 2 shillings and six pence, with women, or more
probably girls, at 4 to 6 shillings, and boys the same. Both the boys and
girls worked the full factory hours.
In 1888 the company was re-incorporated as a private limited
company under the name of John Harper & Company Limited. The directors were
John Harper and his son, Fred. The company was, effectively, the property of
John Harper who had become a Justice of the Peace, an alderman, a great
Methodist, and a temperance campaigner.
They were joined on the board in
1894 by the successful local solicitor James
Slater J.P. who had a business in Darlaston, and lived at Bescot Hall.
He sat on the Willenhall Bench for many years, and in 1901 was succeeded on the
board by his son Maurice, also a J.P. The Slater family maintained an association with
the company until the 1960s. Slater Street in Willenhall is named after
James Slater.
|
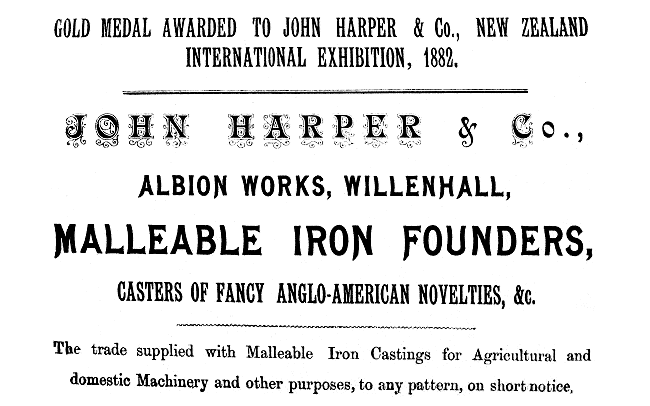
An advert from the early 1880s. |
The company expanded significantly in the late 19th
century. By the 1890s there were seven foundries, a sand blast, eleven
fitting shops, two polishing rooms, three plating shops, three lacquering
rooms, fifteen japanning shops, six warehouses, and five steam engines. In
the offices was a No. 4 caligraph typewriter, a speaking tube, and three
telephones. The works were self contained. Bricks for extensions were made
on site, and the gas to light the works came from the company's own gasometer.
Five hundred people were employed, including, from the 1870s
onwards; women. In 1888 the finished product range had widened to include
oil lamps, oil and gas stoves, and other hardware. In 1899 the company
first registered its trade mark, "Beatrice".
A description of Harper products at that time included locks, bolts, and latches; malleable castings from a
latch key size upwards; novelties and stationery goods; light and fancy
castings; lamp fittings; oil stoves; cycles and tricycles; "Beatrice" and
"Cathedral" stoves. In 1900 some 50 tons per week of castings were being
made in five more or less separate foundries, and the proportion of castings
for outside sale was growing. |
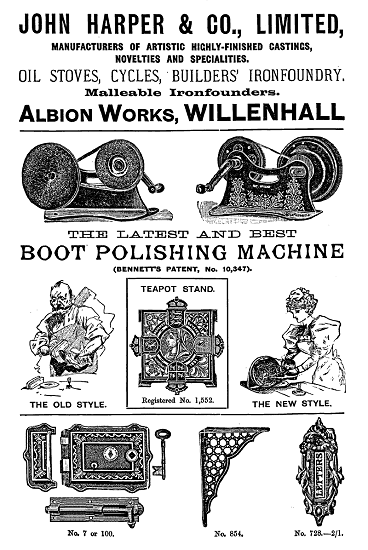
This advert is from Peck's
1896 trade directory. It includes a single lock. |
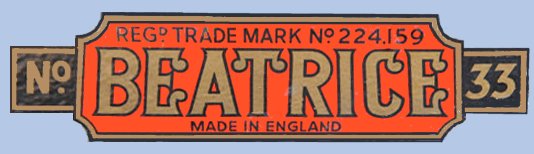
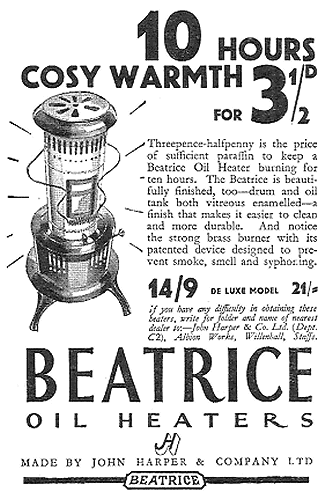 |
|
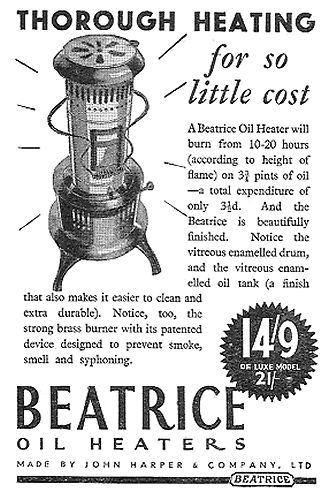 |
Two adverts from
the 1930s. |
|
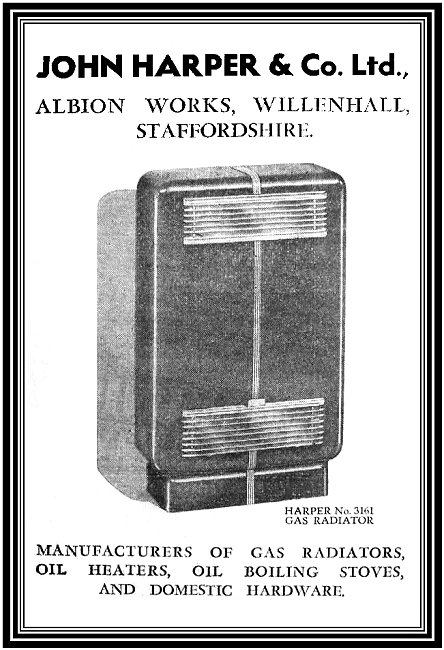
An advert from 1939.
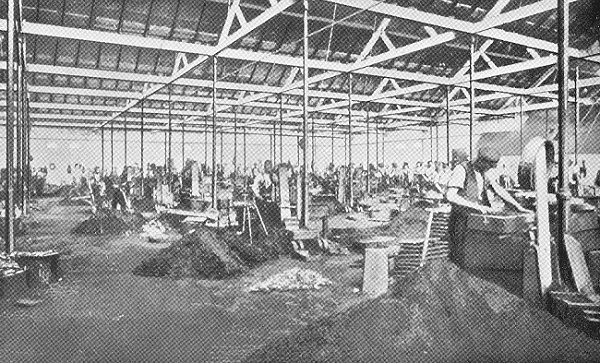
Part of Foundry No 1 in about 1900,
where general work was produced. |
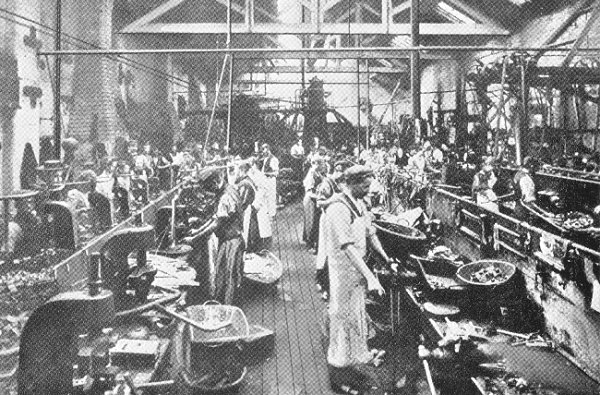
Part of 'A' shop in about 1900, where
pressing, stamping, cutting out, and fitting were carried out. |
The following is from County Biographies 1901,
Staffordshire: |
County Magistrate
Alderman John Harper, J.P.
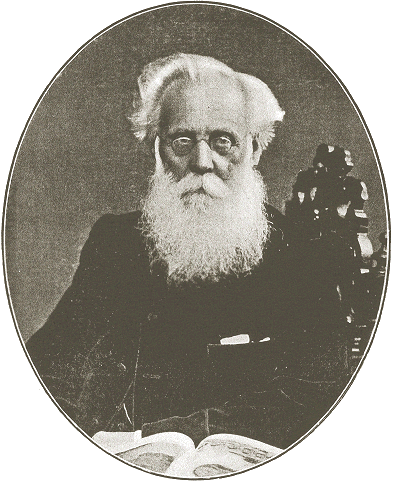
John Harper, J.P., Brueton House, Bilston; second son
of the late John Harper, hardware merchant, of
Willenhall; born May 24th, 1821. Mr. Harper is a Justice
of the Peace for the County of Stafford, and sits both
at Bilston and Willenhall Petty Sessions. He served on
the Willenhall School Board for the first six years of
its life; was returned as County Councillor for North
Bilston in 1888, and made Alderman on the same date,
which position he still holds. In politics Mr. Harper is
a staunch Liberal, and was for many years a great friend
of the late Right Hon. C. P. Villiers, M.P.; he is a
prominent Wesleyan and for sixty years has been a total
abstainer; he is also a Fellow of the Imperial
Institute. Mr. Harper's business record is a long one.
He has been in harness now for 64 years, and still takes
an active part in the works at Willenhall. This business
was founded on a small scale in 1790 by Mr. William
Harper, the grandfather of the present head of the firm;
it was subsequently carried on until 1851 by the late
Mr. John Harper, when several businesses were
amalgamated under the title of John Harper Jun. and Co.
In 1888, for family reasons, the business was converted
into a private Joint Stock Company, of which Mr. Harper
is principal shareholder, Chairman of Directors, and
General Manager. In addition to this life-long
connection with the Albion Works, Willenhall, Mr. Harper
is proprietor of the Bilston Windmill Cement and Plaster
Company. He was initiated into commercial life at an
early period, and we find him, when 16 years of age,
acting as buyer and making periodical visits into the
Potteries and elsewhere on business matters. Mr. Harper
has been an extensive traveller, and has visited Russia,
Finland, Sweden, Norway, Denmark, Germany, France,
Belgium, Austria, Bavaria, Holland, The North Cape,
Rhineland, and the Danube, in addition to nearly all
parts of the British Isles. He was fortunate enough to
be present at Kiel Harbour on the occasion of the
opening of the Baltic Canal, which he has since
travelled through on his way to St. Petersburg. |
|
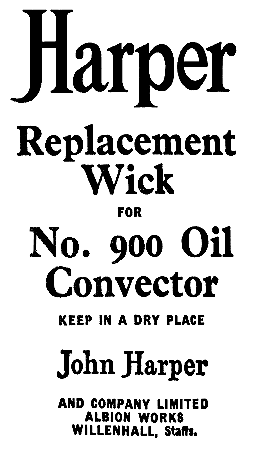 |
John Harper Junior died in 1903, after which the
company remained in the hands of his descendants and those of other
directors, the Slaters, Retallacks and Lewises. Catalogues from 1903 to 1924
show bolts, but very few locks. So lock making was probably not one of the
major activities.
An inventory from 1908 includes a horizontal compound
condensing engine, 36-in. stroke, by Victor Coates of Belfast, which seems
to have replaced the earlier steam engines.
There were dynamos, powering
electric lighting, enamel, tinning and plating shops, and a new
sand grinding mill with elevators, in the foundry. There was also a coal-dust
grinding mill and overhead travelling carriages for larger castings, and 27
moulding machines.
The stables contained six horses and eleven carts, two of
which were rubber tyred.
A chemical laboratory opened in 1913.
|

A section of the hanging lamp and
children's cycle wrapping room in about 1900. |
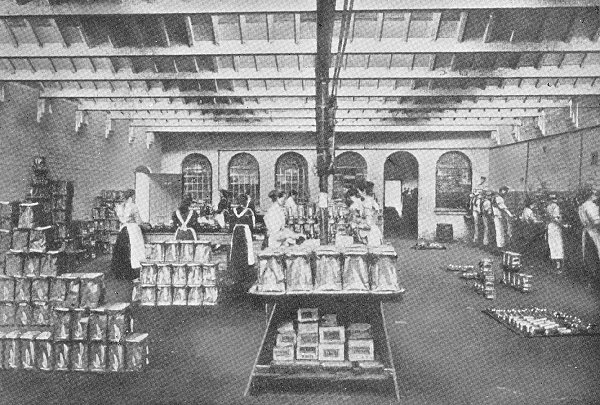
Part of the stove erection shop in about
1900. |
In
1914 the
company is listed as general and malleable ironfounders, and manufacturers
of finished hardware of all kinds, employing 764 people. In the First
World War munitions were produced.
After the war things soon returned to normal. The
product range included castings for typewriters, and electric cookers. In
the 1920s, Harper's developed equipment, unique at the time, to measure the
electromagnetic properties of iron castings, opening new markets for parts
such as resistance grids and telephone exchange components.
The old steam engine, known as the "Big Engine" broke
down and was replaced by electric power, and in 1925 Malleable iron
production ended because demand had fallen. Production then concentrated on
grey iron castings, which were in great demand. The old annealing ovens were
dismantled to allow for further foundry extensions, and a night shift
started in the foundry, which produced thousands of castings each week.
Around this time a works canteen opened. It had been built on an adjoining
piece of land.
|
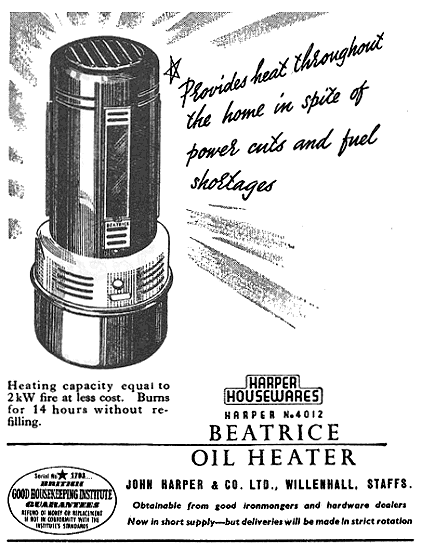 |
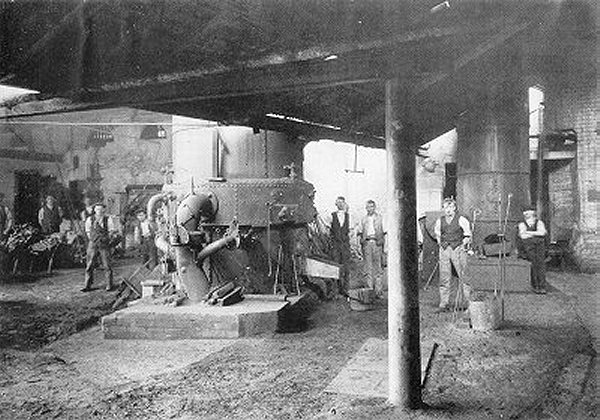
One of the cupola furnaces in 1925.
|
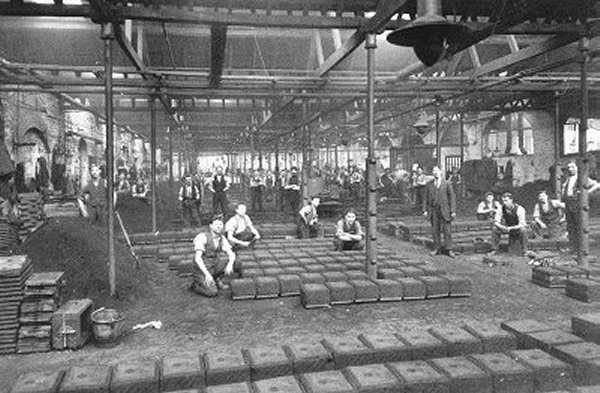
Part of the light foundry in
January 1925. |
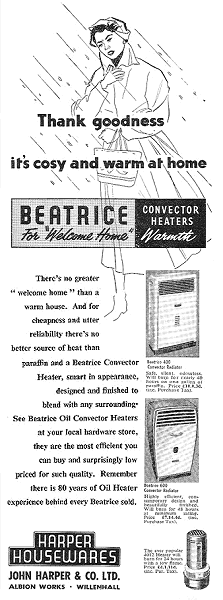 |
Although the factory had been modernised, the board
decided that it was inadequate for the future needs of the company, and a
new and larger factory was essential for future growth.
Sometime before
1897 the firm had purchased a large piece of land covering 14½
acres, which was bounded by Stringes Lane, Gough Street, Acorn Street and Clarke's Lane.
It appears to have been acquired for
possible future expansion.
The site contained large deposits of sand and
gravel which were dug-out and sold, yielding an income of about £100 per
year. By the 1920s the sand and gravel pits had been worked-out, and so the
firm used the land for tipping about 20 loads of rubbish a day, which helped
to fill-in the large holes.
In 1907 about an acre of the land, adjoining Albion
Street was sold to the education authority for the building of Albion Street
School, which opened on 4th October, 1909.
Nine years later at the end of
the First World War, the firm purchased some adjoining land from the Earl of
Lichfield, and sold the part of the land adjoining Stringes Lane and
Clarke's Lane to the local authority.
After the board's decision in 1926 to
build a new factory, the land was bought back. Because the land was so close
to the existing factory, it was felt that the development of the site would
not seriously break the continuity of either production or management.
|
Work on the new factory began in 1927 with the building
of the foundry, where the first cast was made on 3rd December of that year.
The new factory was extended over the next twenty years to fill the whole
site. As new factory units appeared, production was gradually transferred
from the old site. In 1930 capital was raised on the Stock Exchange
to extend the 1927 foundry, which had won a lot of new business in supplying
the electrical and business machine industries in particular. The new
capital diluted the family holdings and progressively ended the family's control. |
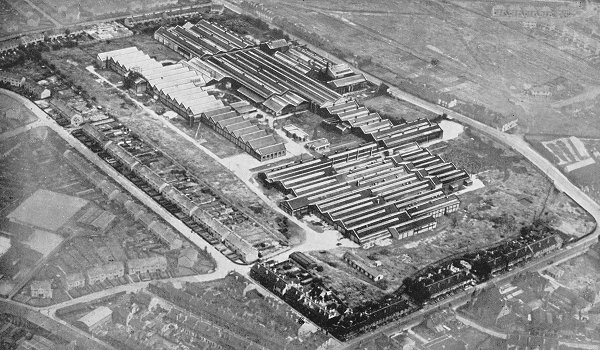
The new factory. |
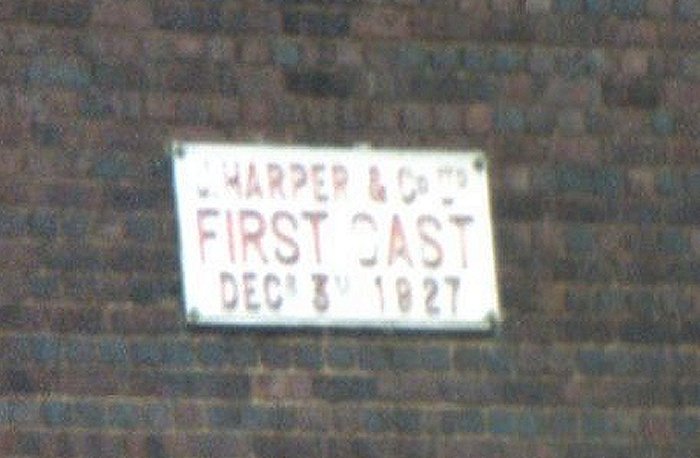
The plaque that was on the outside of
the new foundry. Courtesy of Mark Cooper and David Parsons. |
|
|
View a John Harper grey
iron castings book from 1928 |
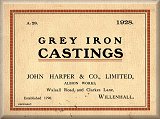 |
|
|
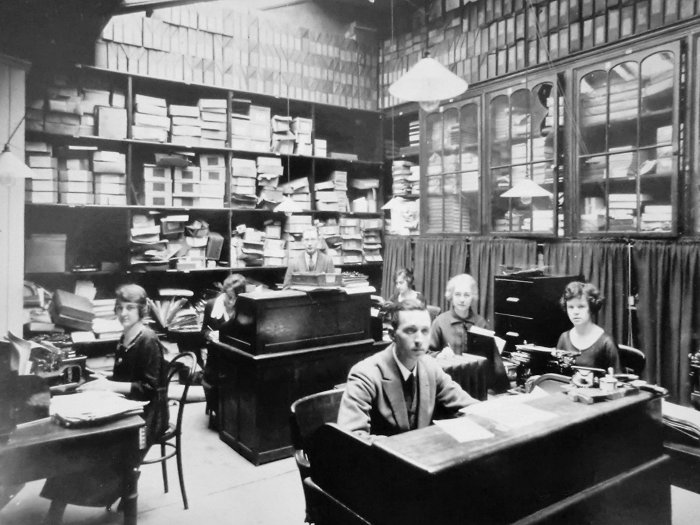
Office staff in the 1930s. Courtesy of
David Parsons. |
In order to develop new markets for castings, a 'Meehanite' licence was taken out in 1937.
'Meehanite' was a production process
which produced a high quality iron product with 'semi-steel' qualities.
Harper's set up a separate foundry and a separate company, John Harper (Meehanite)
& Company Limited, which remained in existence until 1961 when it was re-integrated
into the parent company. |
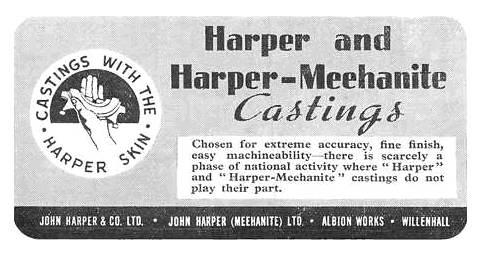 |
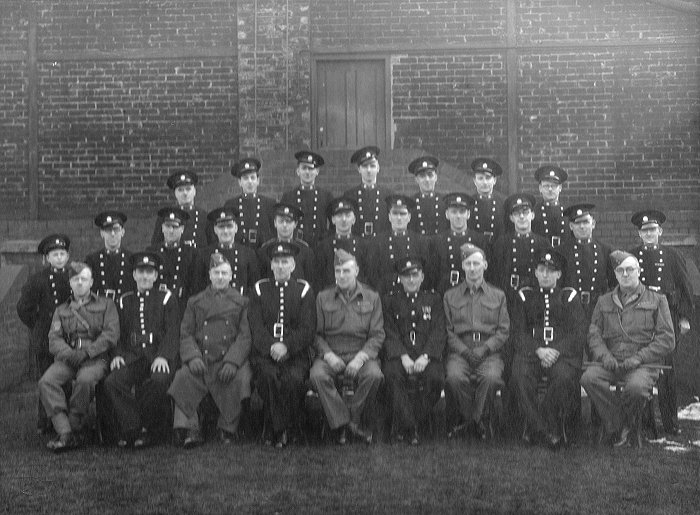
Harper's fire brigade in about 1939.
Courtesy of David Parsons, whose father is second from the right
on the back row. |
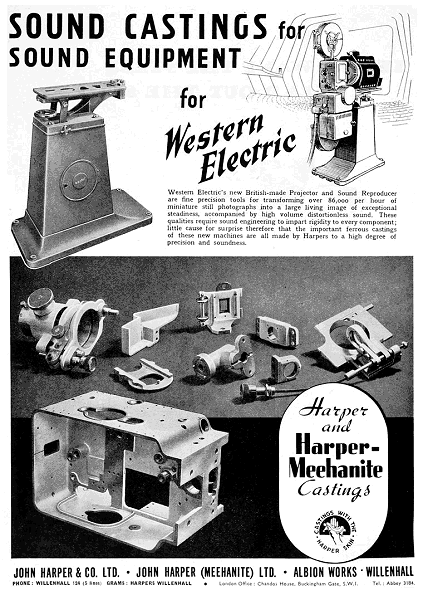
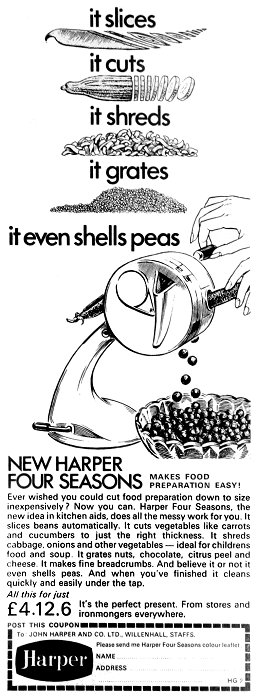
Courtesy of David Parsons. |
By 1939 only the warehouse, and the office in the old
factory were still in use. When war began in September 1939, production was
turned over to the war effort, and the production of munitions.
Parts of the
old works were given a new lease of life, and were occupied by a variety of
other manufacturers whose premises had been destroyed by the enemy.
After the war, building work started again on the new
site. In 1949, a new office block was built which enabled the company
to transfer everything to the new factory
and to sell-off most of the old works, although a garage, carpenter's
shop, social club and dining room were retained until the 1970s.
Much of the
old site was acquired by H. & J. Hill Limited, ironfounders. They had a
foundry on the site until the 1980s when the business closed. The site is now
occupied by housing.
In 1952 Harpers bought a foundry in Poole, largely to
make high phosphorus content grey iron castings. It became extremely
efficient, producing 600 to 700 tons of castings a year,
mostly for Harper's own finished goods, but also for outside sale, including
the complex water-cooled cylinder bodies for British Seagull outboard
motors.
|
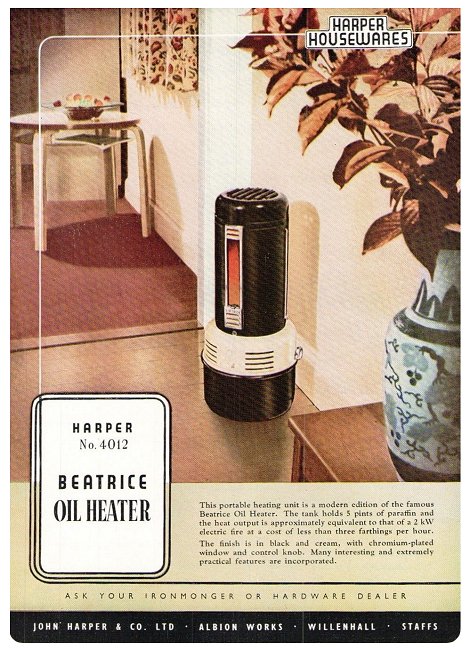
An advert from 1951.
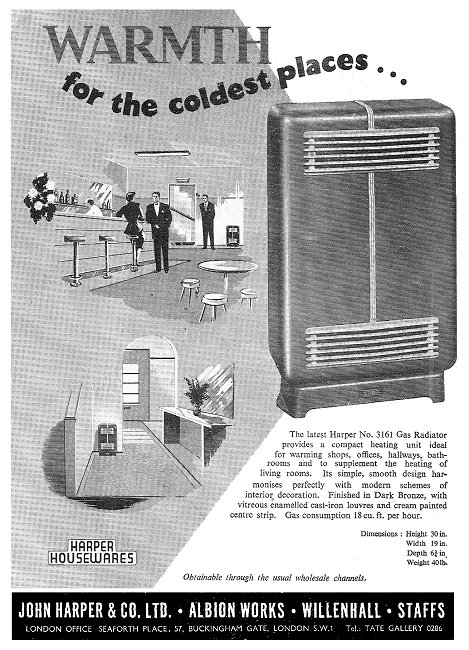
An advert from 1953.
In 1953 the company produced a couple of castings to
celebrate the coronation. There is a throne and a crown, both of
which are money boxes. The throne is 8 inches high, 4.5 inches
wide and 2.5 inches deep.
The crown is 2.5 inches wide and 3 inches high. |
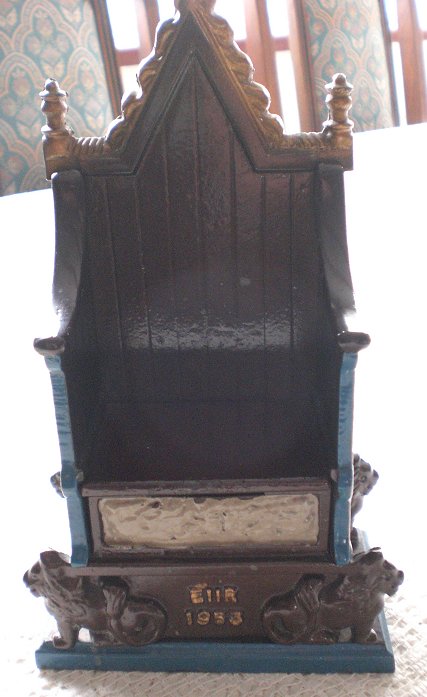
The throne money box. Courtesy of David
Parsons. |
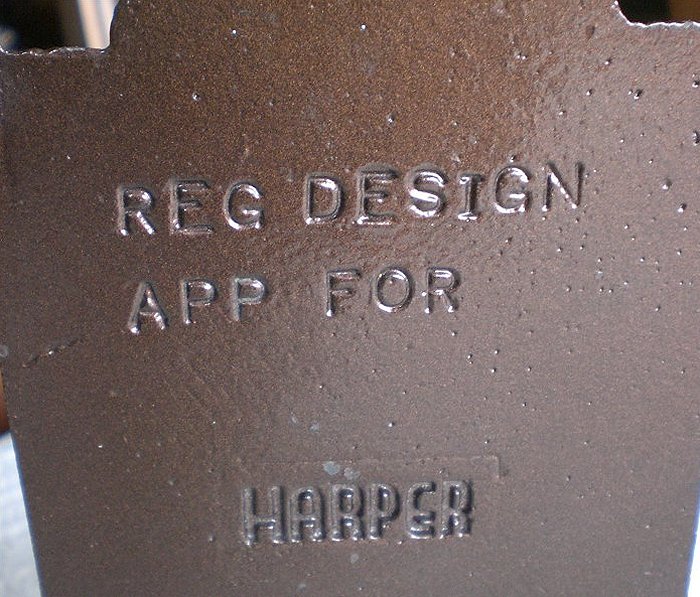
The back of the throne. Courtesy of
David Parsons. |
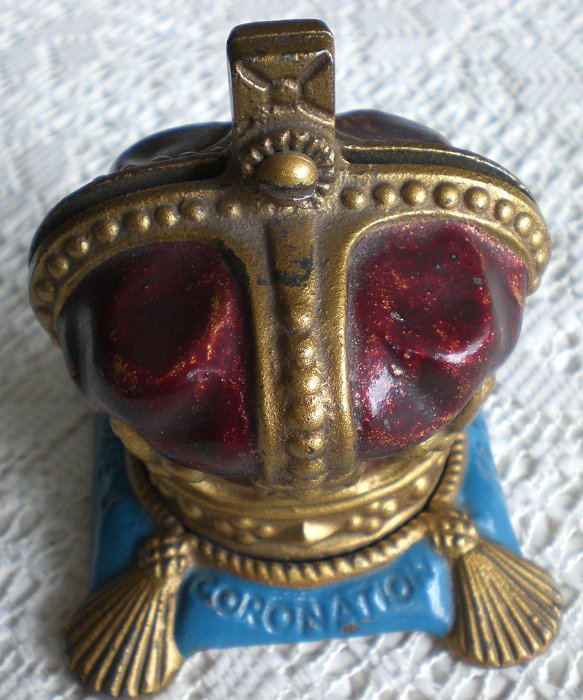
The crown money box. Courtesy of
David Parsons. |
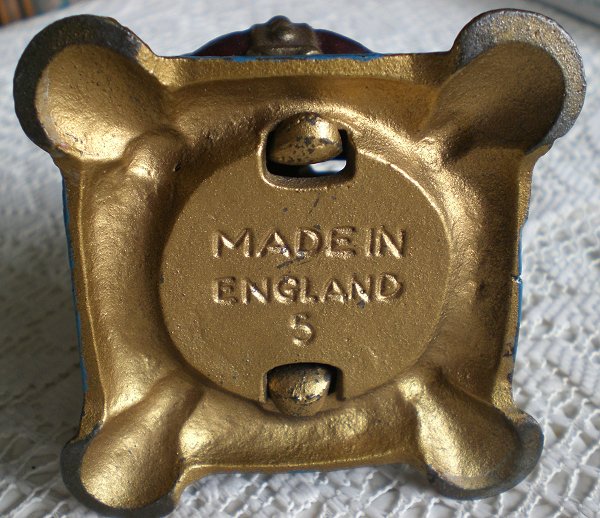
The underside of the crown
money box. Courtesy of David Parsons. |
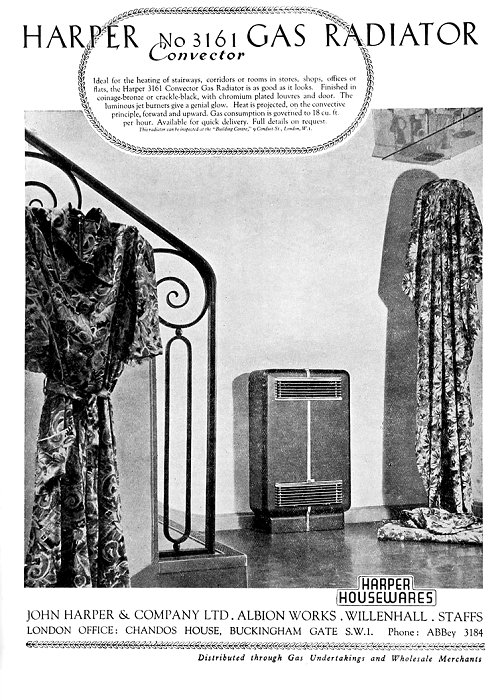
An advert from 1949. Courtesy of David Parsons.
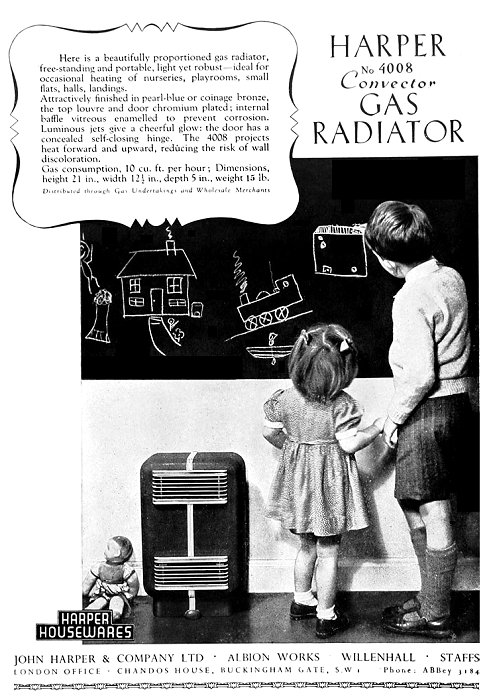
An advert from 1949. Courtesy of David Parsons.
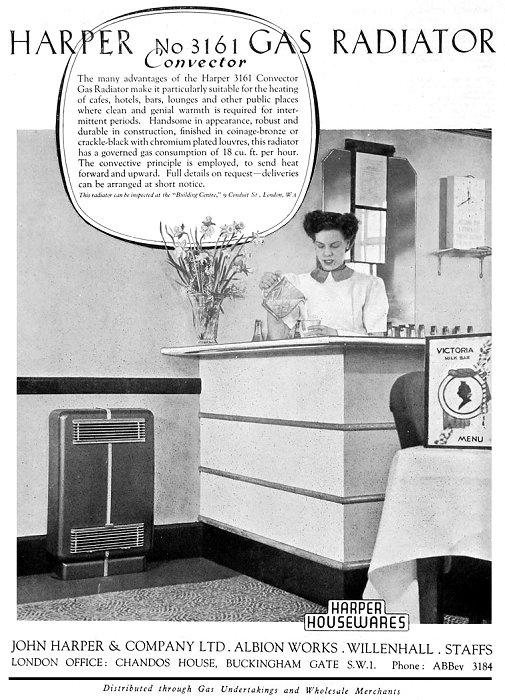
An advert from 1949. Courtesy of David Parsons.
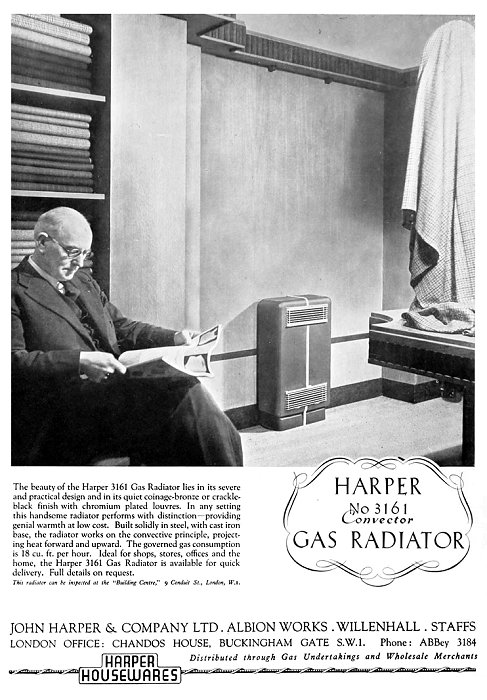
An advert from 1949. Courtesy of David Parsons.

An apprenticeship certificate. Courtesy of David
Parsons.
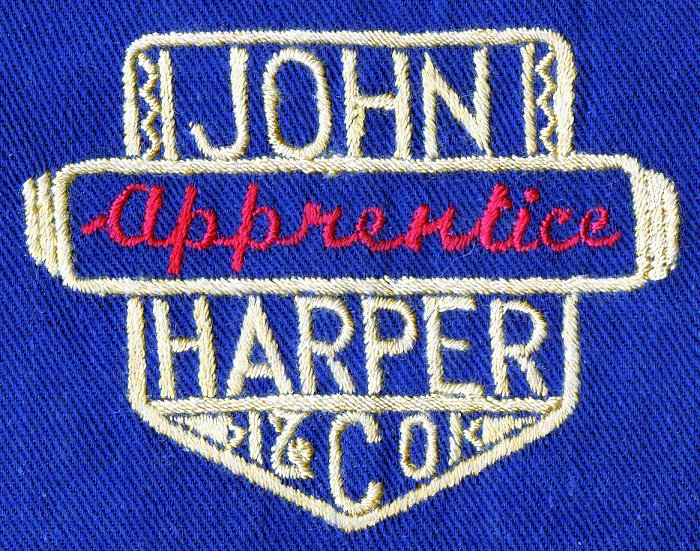
A badge from a John Harper boiler suit.
Courtesy of David Parsons. |
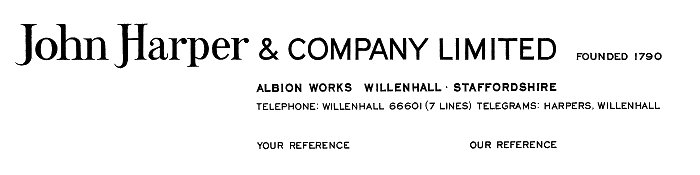
A letterhead from 1963. Courtesy of
David Parsons. |
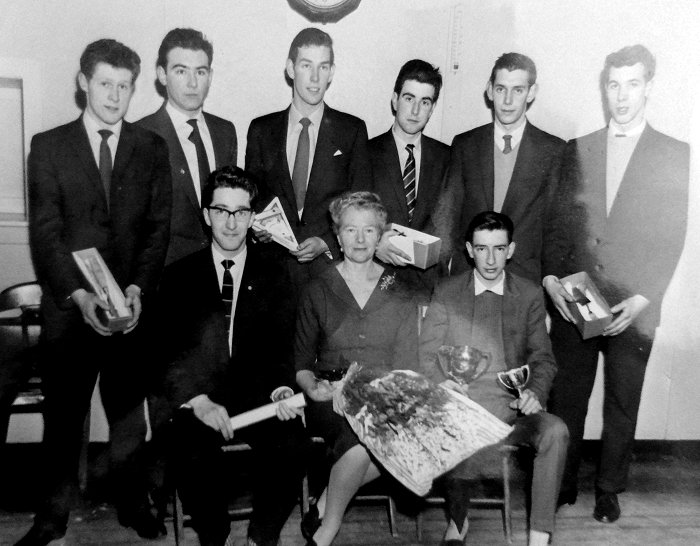
A group of John Harper employees at a
prize giving day in the 1960s. Courtesy of Mark Cooper and David
Parsons. |
By 1960 the company had two divisions, Finished Goods
Division and the Foundry Division. The Finished Goods Division produced oil
stoves and heaters under the 'Beatrice' brand, and domestic hardware under
the 'Harper Housewares' brand.
The Foundry Division had 3 foundries working
in cast iron, 'Meehanite', and ductile iron. They employed around 1,400
people.
The Finished Goods Division closed in 1970 after falling sales,
despite a diversification into electric heaters.
The Foundry Division
continued to grew, especially in the production of high strength special "S.G." iron engineering castings. |
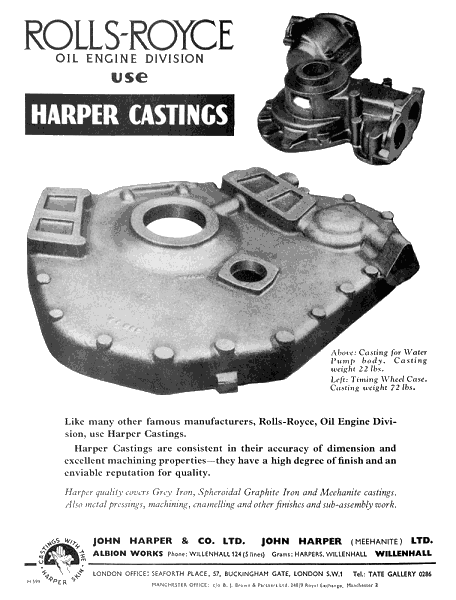 |
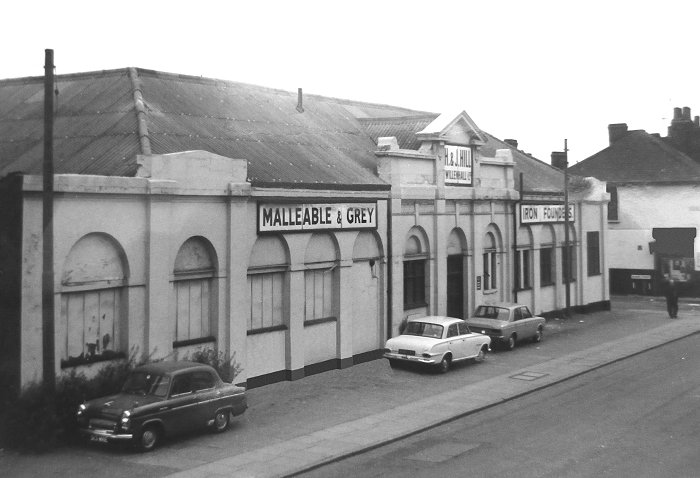
Albion Works when it was occupied by H. &
J. Hill Limited. Courtesy of Mark Cooper and David Parsons. |
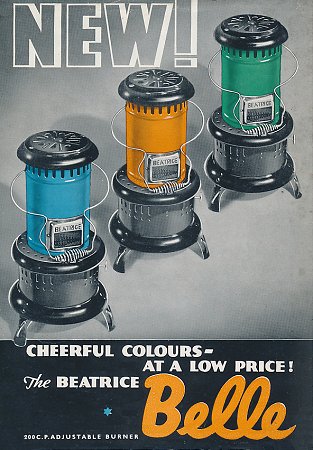 |
|
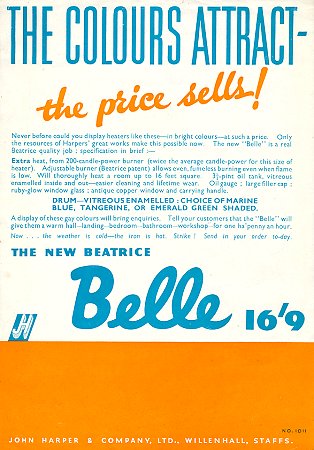 |
An advert for
John Harper's Beatrice Belle
paraffin heaters. |
|
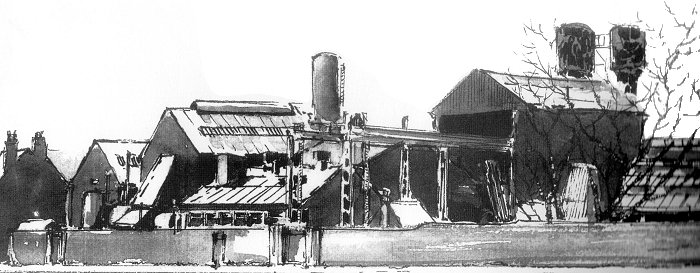
A drawing of part of the factory. A
once familiar Willenhall landmark. Courtesy of David
Parsons. |
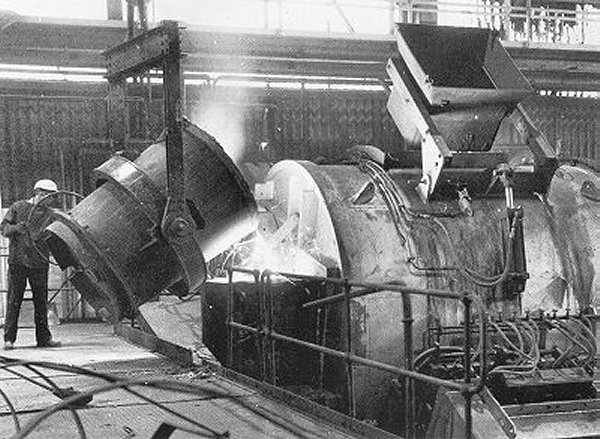
The melting plant for the high strength
special "S.G." iron in 1972. |
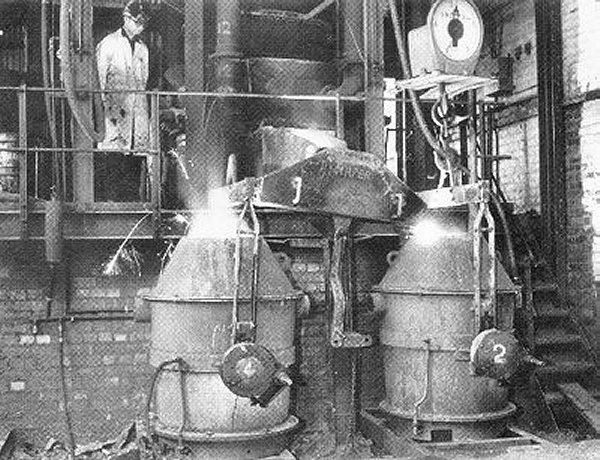
Some of the melting plant in 1965 showing
a continuous tapping cupola spout, with tilting launder, filling
porous plug ladles in which the metal is treated with calcium
carbide and graphite, before being transferred to an electric
furnace. |
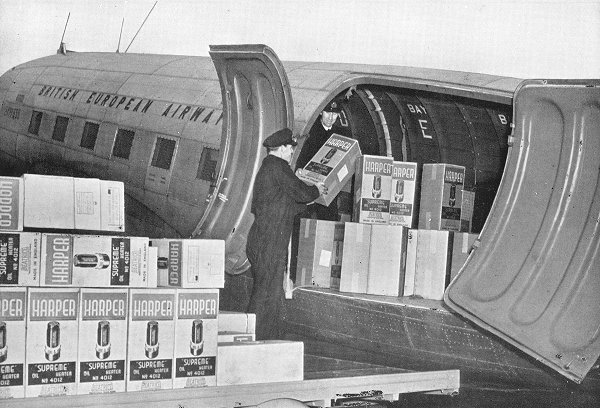
Oil heaters being loaded onto a British
European Airways aircraft for transportation to Turkey. They are
standard 'Beatrice' oil heaters that were sold in Turkey under
the 'Supreme' name because 'Beatrice' is difficult to pronounce
in Turkish. |
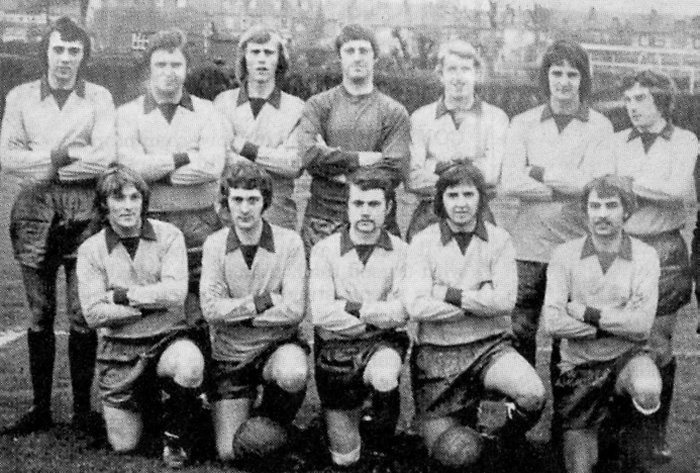
A John Harper football team from 1973.
Courtesy of David Parsons. |
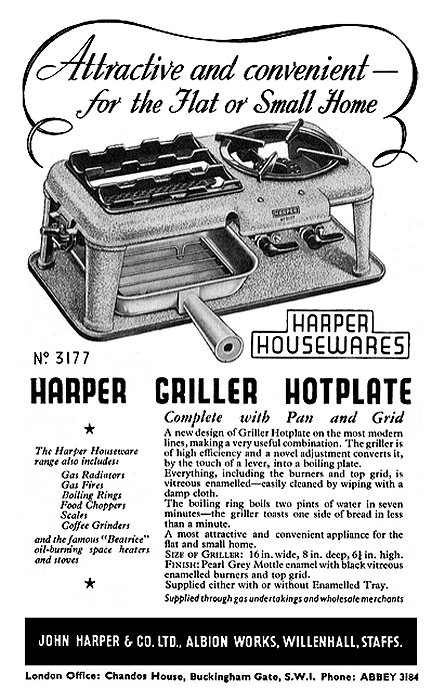
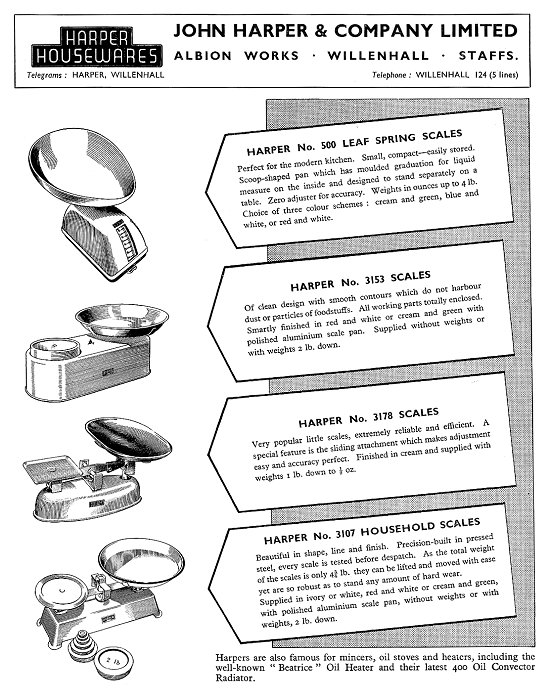
An advert from 1956.
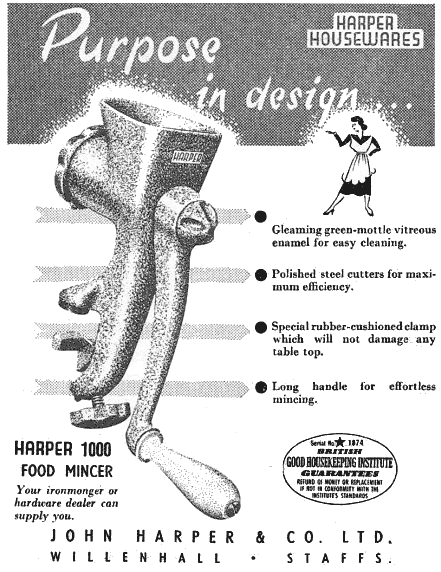 |
In 1972 Newman Industries acquired interest in John
Harper and Company, which was taken over by Duport, in 1974.
In 1982 Duport decided to combine several
of its foundries into a single site at Tipton.
As a result the
Willenhall factory closed, and John Harper and Company Limited ceased
to trade as a separate business.
A few years later Duport itself closed,
but the business survived in Tipton as Duport-Harper.
It was taken over by
the American Company Grede Foundries UK Limited, and still operates in
Tipton as Duport Harper Foundries. |
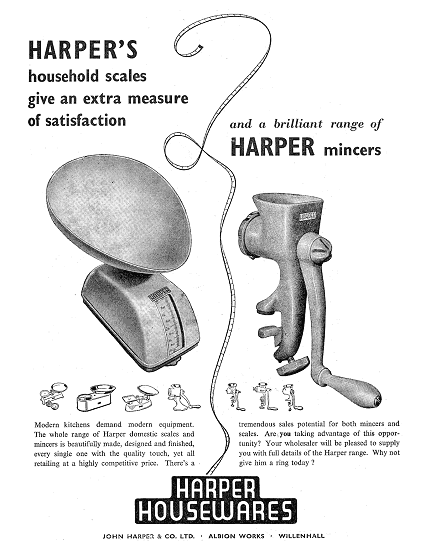
An advert from
1958. |
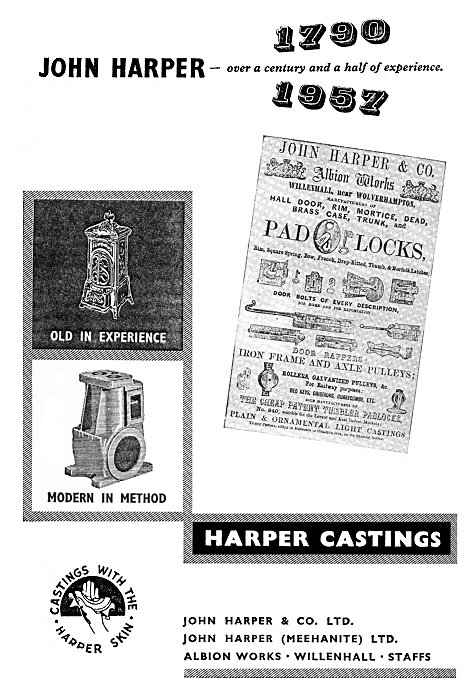
An advert from
1957.
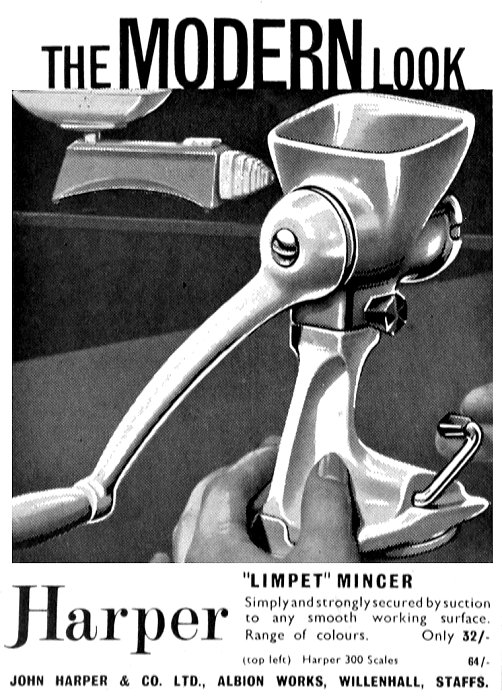
An advert from 1962. Courtesy of David Parsons.
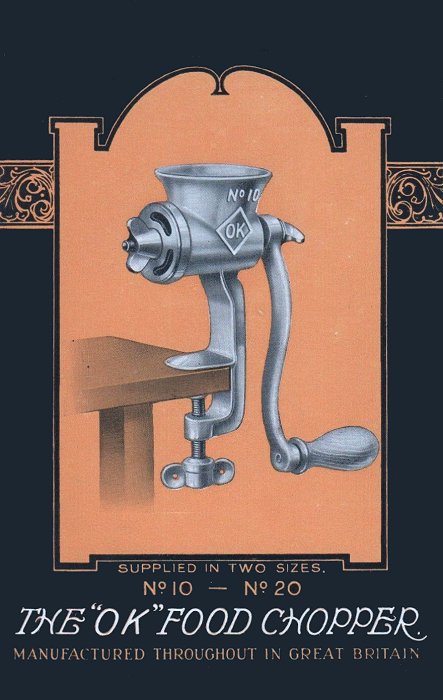
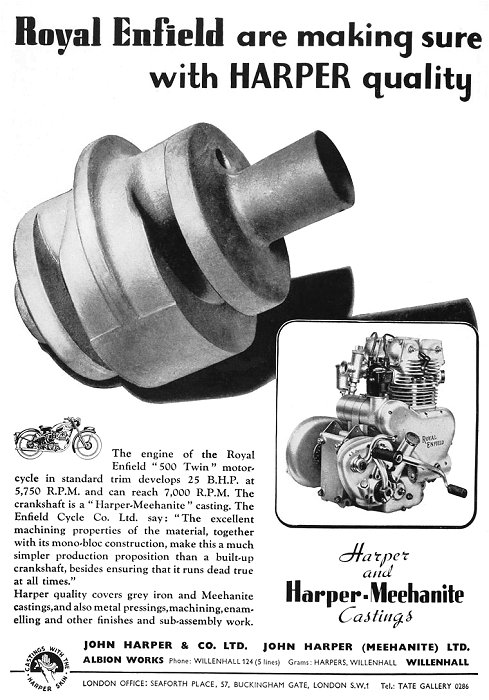
An advert from 1952. Courtesy of David Parsons.
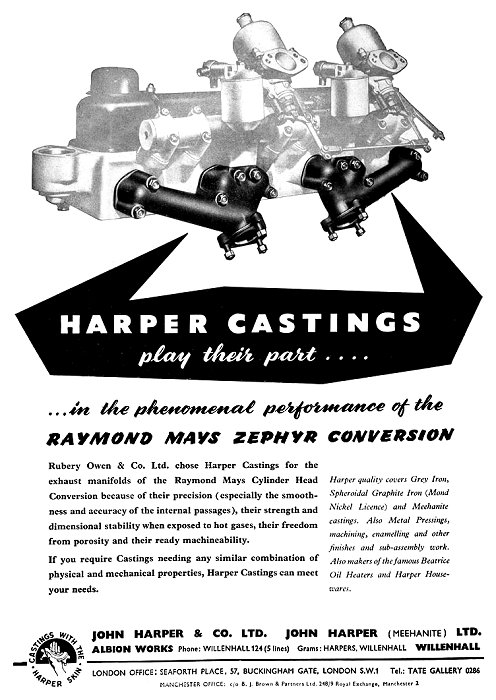
An advert from 1958. Courtesy of David Parsons.
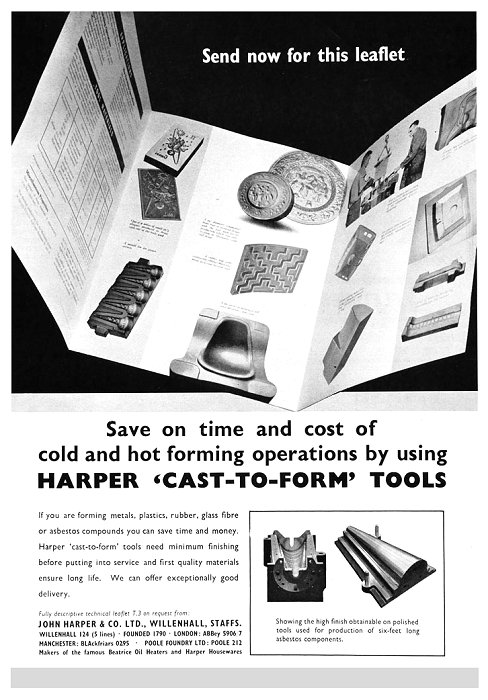
An advert from 1961. Courtesy of David Parsons.
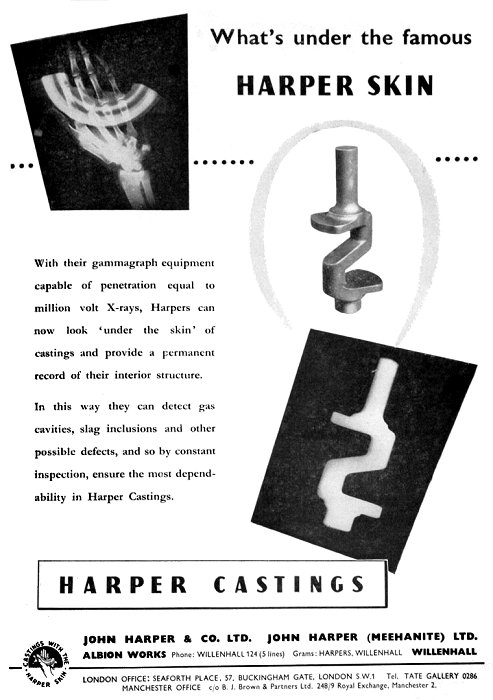
An advert from 1954. Courtesy of David Parsons.
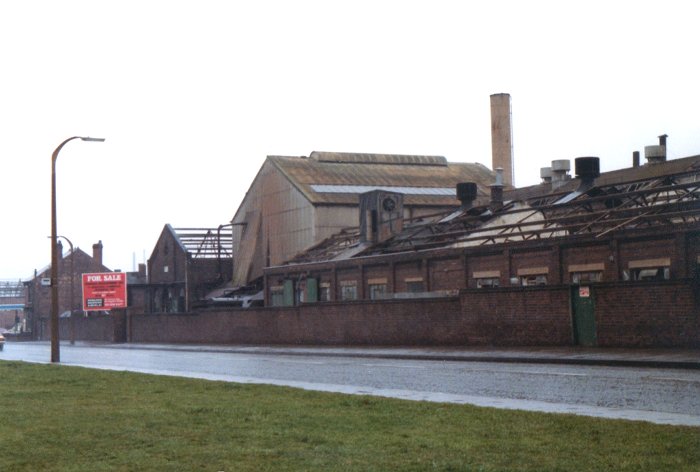
Demolition of the Clarke's Lane site.
Courtesy of Mark Cooper and David Parsons. |
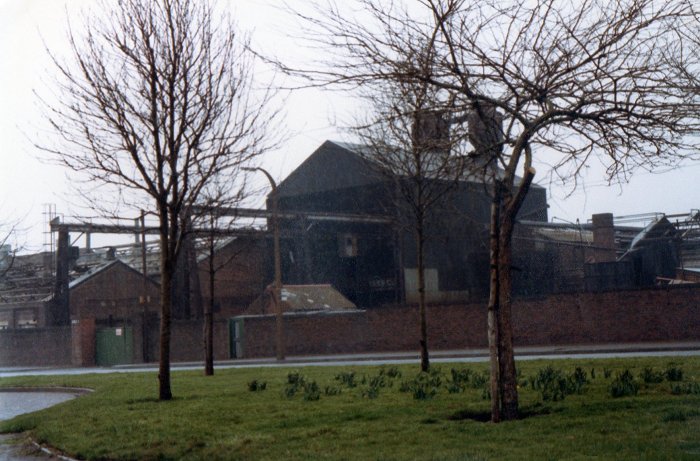
The two cupola furnaces.
Courtesy of Mark Cooper and David Parsons. |
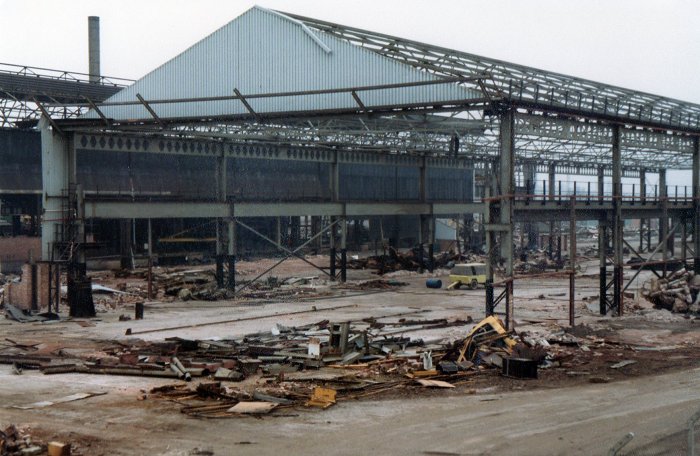
Demolition quickly got underway.
Courtesy of Mark Cooper and David Parsons. |
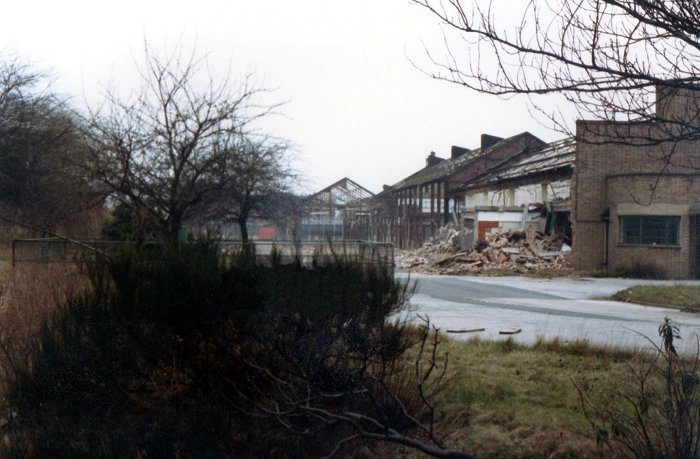
The factory is soon turned into a pile
of rubble. Courtesy of Mark Cooper and David Parsons. |
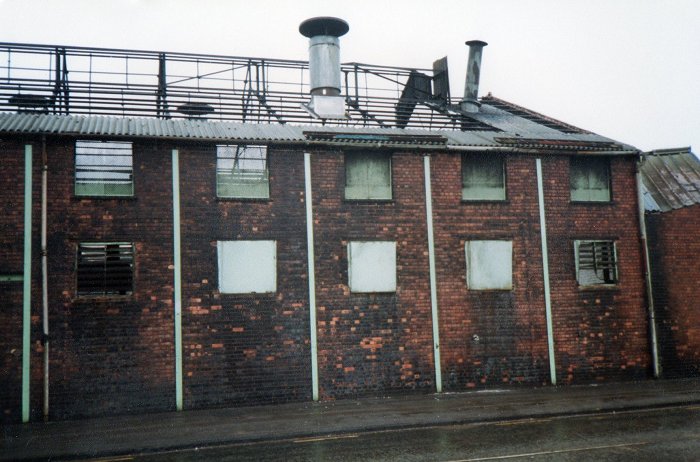
Another of the once-important
buildings meets its end. Courtesy of Mark Cooper and
David Parsons. |
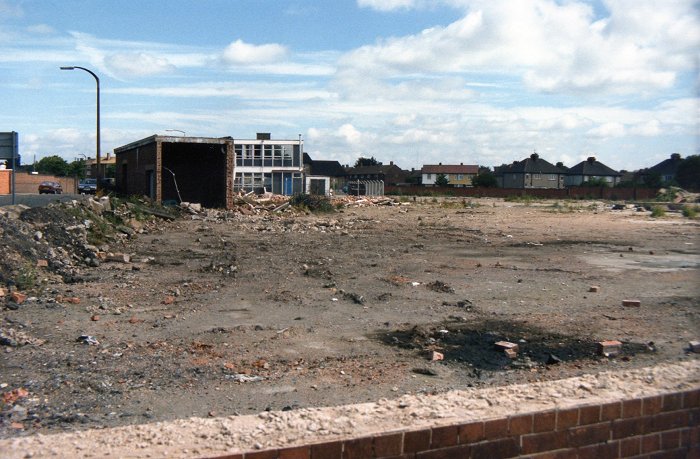
The southern end of the site looking
across to Lincoln Avenue. A sad end to one of Willenhall's
largest factories. Courtesy of Mark Cooper and David
Parsons. |
An advert from 1947.
Courtesy of David Parsons. |
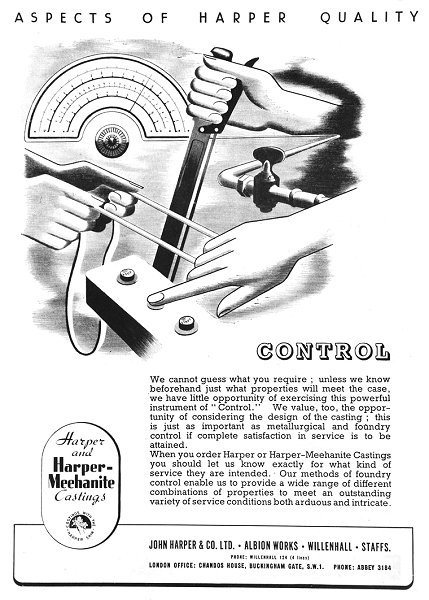 |
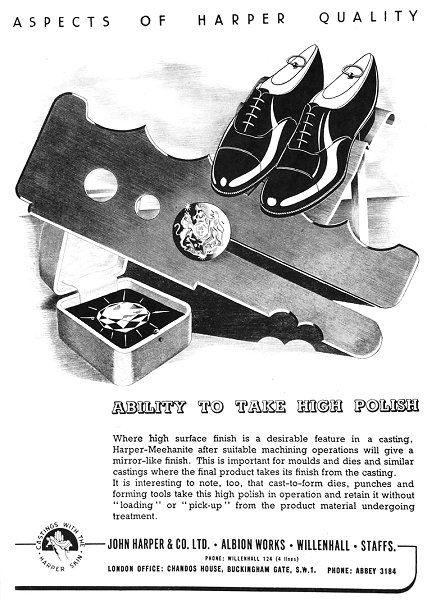 |
An advert from 1948.
Courtesy of David Parsons. |
An advert from 1948.
Courtesy of David Parsons. |
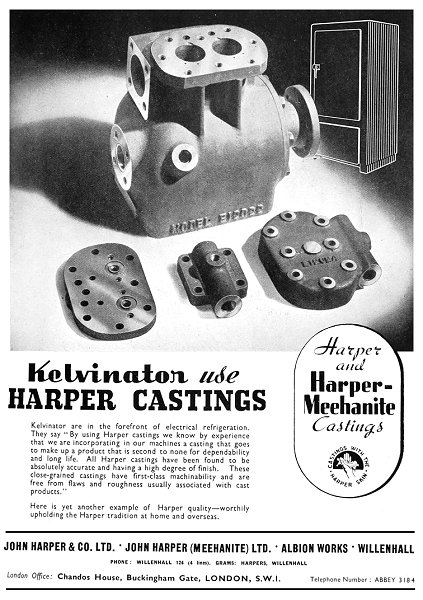 |
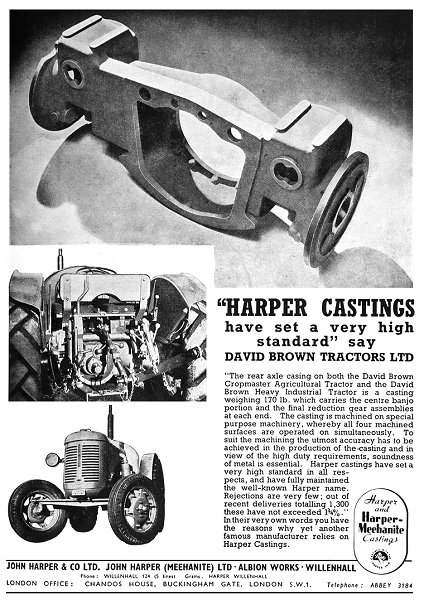 |
An advert from 1948.
Courtesy of David Parsons. |
An advert from
1950.
Courtesy of David Parsons. |
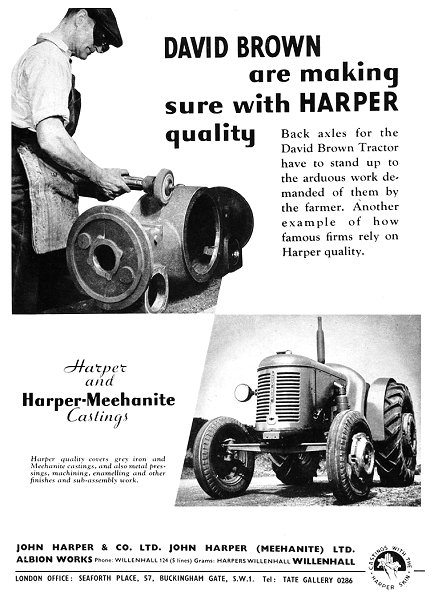 |
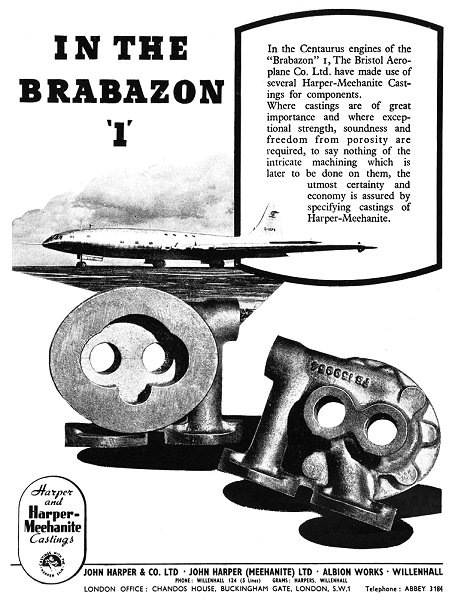 |
An advert from 1952.
Courtesy of David Parsons. |
An advert from 1952.
Courtesy of David Parsons. |
 |
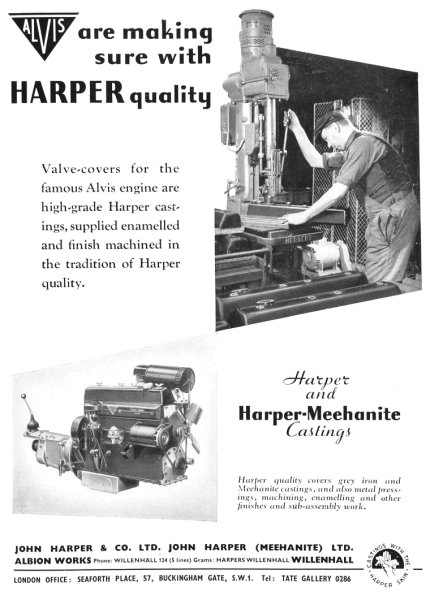 |
An advert from
1952. Courtesy of David
Parsons. |
An advert from 1957.
Courtesy of David Parsons. |
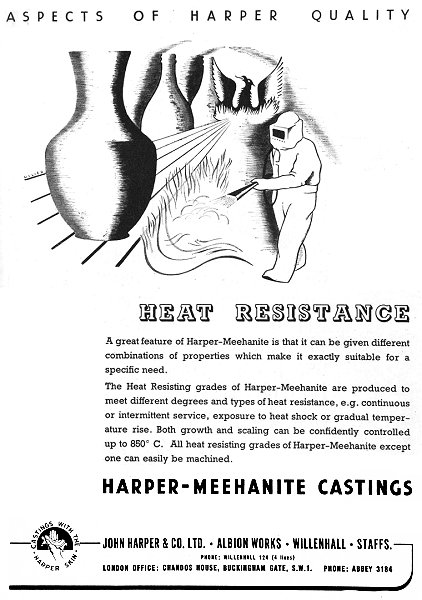 |
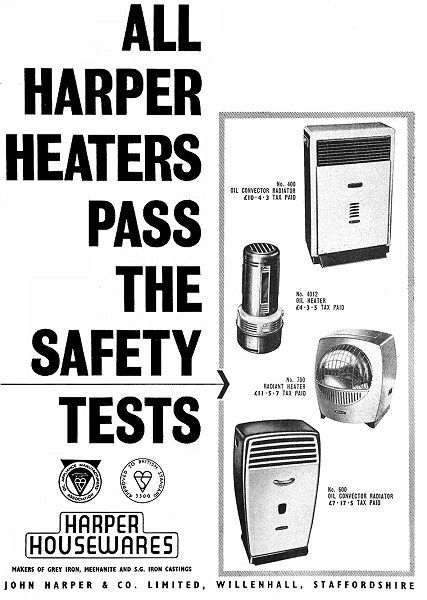 |
An advert from 1961.
Courtesy of David Parsons. |
 |
|
 |
Return to
Willenhall History |
|
Return to
the gazetteer |
|