 |
Other Heavy Industries
Although now thought of as an ex-nut &
bolt town, there were many other industries, some becoming
household names. One of Darlaston’s leading engineering
firms, employing over 1,000 people, was Wilkins and Mitchell
Limited, who became a well-known power press manufacturer.
Their presses were exported throughout the world, and many
are still in use today.
The business was founded in 1904 by two
friends, Walter Wilkins and Tom Mitchell who rented a small
factory in Bell Street, called Phoenix Works, from nut and
bolt maker Charles Richards. They began making all kinds of
machines including drilling machines, bolt heading machines,
and milling machines. In 1907 they built their first power
press, a hydraulically operated blanking press for Rubery
Owen, and four years later built their largest press to
date, a massive forming press, also for Rubery Owen. This
press revolutionised vehicle production in the UK because it
cold-pressed vehicle chassis frames, making mass production
possible in this country.
Because the machine was so successful,
others followed, and the company produced large numbers of
power presses, some of immense size. In 1910 the company
moved to Darlaston Green Works, and renamed it Pheonix Works
after their former factory. By 1914 the firm employed
between 60 and 70 people and continued to produce a wide
range of machinery, some of which was especially designed
for railway wagon and carriage companies
|
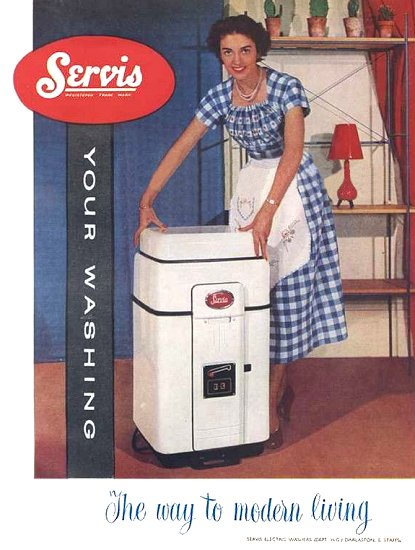 |
In his home at The Hollies, on the side
of Church Hill, Wednesbury, Walter Wilkins had a small experimental workshop
where he could work on new ideas and designs. In about 1926
he began thinking about building washing machines, and in
1929 founded Servis Limited in order to manufacture them.
Servis washing machines were a great success, and like the
power presses were sold at home and abroad.
Presses from 100 tons to 6,000 tons
were built at the Darlaston factory, and a modern London
office opened in Park Lane, where a display of Servis
washing machines could be seen. The premises also housed the
power press export section. The overseas market was
extremely important to the company.
By the early 1950s space was in short
supply at Phoenix Works and so a second factory was opened
in Darlaston Road, King’s Hill to produce washing machine
components. A few years later a large piece of land was
purchased at King’s Hill next to the existing factory, to
extend the factory, build a new office block, and
concentrate washing machine production on the site. A little
later another successful product, the Servis ‘Super Twin’
was launched. |
Extensions were added to the power
press factory, and single, and double action presses were
produced for a wide range of industries, including the motor
industry, the forging industry, the aircraft industry, and
the domestic appliance industry.
By the 1960s thousands of Servis washing machines were made each week, and a
subsidiary company called Wilkins Servis was set up to
manufacture washing machines in Australia.
In 1982 the UK manufacturing group,
Verson International, acquired Wilkins and Mitchell, and
sales continued to grow. The group built a new, larger
factory on a 15 acre site in Willenhall Road, formerly
occupied by Wellman Cranes. The new factory costing £6
million opened on 28th November, 1990 and the company’s name
was changed to Verson Wilkins. By this time the company had
come to rely on orders from UK vehicle manufacturers, but
with that industry in decline, orders fell, and the
Darlaston workforce was greatly reduced.
Due to still
declining orders, the factory closed on 2nd April, 1999, with
the loss of 64 jobs. The Servis factory survived until
October 2008, but has since been demolished.
|
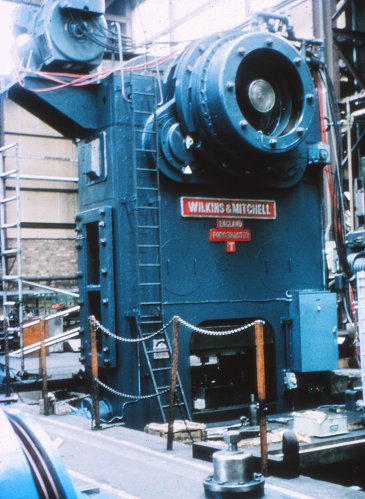
A hot forging machine. |
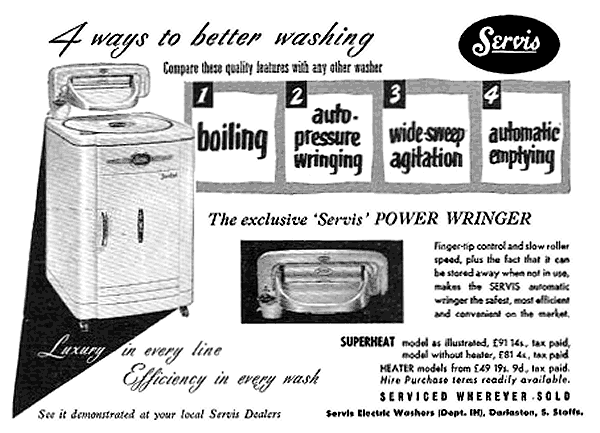
Garringtons
Another of Darlaston's once-important
factories was Garringtons, based at Albert Works in
Willenhall Road. The large forging works was once a local
landmark, with a large workforce. The firm was founded by
John Garrington who started a small stamping business at
Phoenix Works, Catherine's Cross, in 1830, to produce forged
components for the gun trade. By 1851 he also produced nuts
& bolts and bed screws.
In 1912 Albert Works was acquired by
nut and bolt manufacturer F.W. Cotterill, and seven years
later became part of G.K.N. In the late 1930s the factory
was greatly extended, and drop forgings were produced for
aircraft, ships, locomotives, railway construction,
vehicles, and machine tools. Garringtons also specialised in
heat treatment. In the 1940s over 100,000 tons of forgings
were produced annually on the site.
In 1946 Garringtons acquired Deritend
Stamping Limited of Newton Works, Bromsgrove, and also
specialised in a wide range of hand tools. The factory
closed in the recession during the 1980s.
Rubery
Owen
Another once-well known manufacturer
was Rubery Owen based at Victoria Ironworks in Booth Street,
established in 1884 by John Tunner Rubery and his two
brothers. Nine years later the two brothers left, and John
was joined by Alfred Ernest Owen, an engineer from Wrexham.
In 1903 the firm became Rubery, Owen & Company and greatly
expanded the product range to produce structural steelwork,
motor car and aircraft components, pressings and
fabrications, agricultural products, propane gas cylinders,
and nuts and bolts.
In 1910 John Tunner Rubery resigned
from the partnership, and by 1912 the works had been divided
into five departments: Aviation, Engineering, Fencing, Motor
Frames, and Roofing. On April 14th, 1920 the firm became
Rubery, Owen & Company Limited, and a Metal Aircraft
Department, and a Structural Department were formed.
Expansion continued with the opening of
the Armour Plate Department, the purchase of Easiclene
Porcelain-Enamel (1938) Limited, the formation of the
Airframe Department, and the purchase of a hydraulics
company in Warrington, that became known as Rubery Owen
Conveyancer Limited.
The company’s many products included
pressings, fabrications, general aircraft components,
precision assemblies for aircraft, gas cylinders, nuts,
bolts, studs, and motor vehicle components, such as chassis,
axles, wheels, fuel tanks, and discs. Steel structures were
designed and made for all types of single and multi-storey
buildings, and the company's Structural Department was
responsible for a number of well-known buildings including
the London Passenger Transport Offices at Westminster, the
Palace Court Hotel, Bournemouth, Rootes Securities building,
Speke aircraft factory, and the Castle Bromwich aircraft
works. Local structures include the steel frame for
Wolverhampton's Civic Hall, the old South Bank Stand at
Molineux football ground, and Birmingham Tramways and
Omnibus Department's bus garage. The company also produced
pre-fabricated houses for local authorities.
Rubery Owen became one of the major
employers in the area, employing around 14,000 people by the
1960s. Unfortunately things started to go wrong during the
recession in the late 1970s. In June 1979 the company shed
400 employees at Darlaston, and 950 more in 1981. Sadly
things didn’t improve, and the Darlaston factory closed in
the same year.
|
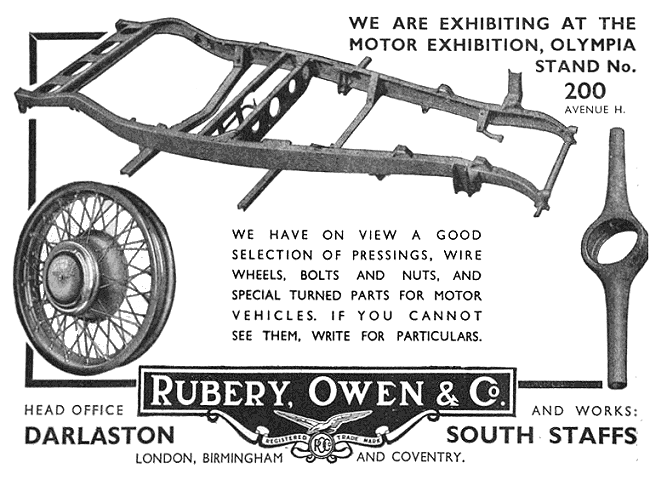
An advert from 1931.
E. C. &
J. Keay Limited
Another well known company, E. C. & J.
Keay Limited was founded in 1879 at New Street, Birmingham.
They were builders and ironmongers. In 1884 they moved to
Cyclops Works, West Bromwich and began to manufacture
fencing, fittings, and steel fabrications.
In 1887 the company moved to "Bridge
Yard", James Bridge where they produced many products and
specialised in structural steelwork for all types of
buildings, such as schools, hospitals, factories, offices,
and warehouses. They also built bridges, hoppers, bunkers,
riveted platework, welded fabrications, and railway
signalling equipment.
In 1957 they became part of the Hingley
Group and were absorbed into F.H. Lloyds in 1960. Sadly they
were another victim of the 1980s’ recession. The F.H. Lloyd
group collapsed in 1982.
|
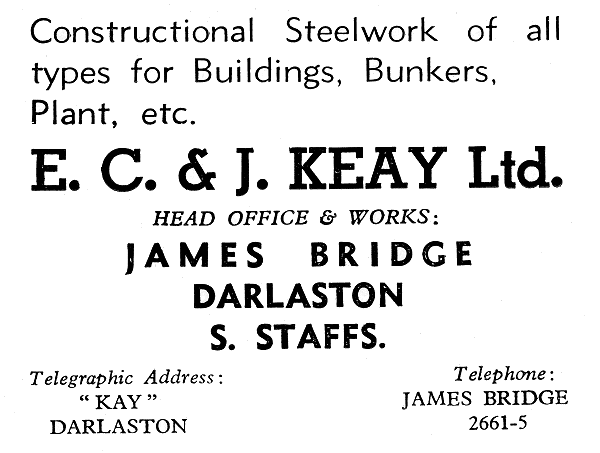
An advert from 1963.
Samuel Platt Limited
Samuel Platt Limited was based at Kings Hill Foundry, and
produced a wide range of products including machinery for
tube making, machines for nut and bolt making, drop hammers, stripping
presses, reeling and straightening machines, stamping
machines, and drop hammers. Other products included lathe
chucks, pulleys, mill gearing, shafting, shaft fittings, and
pressings. |
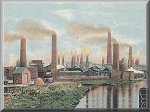 |
|
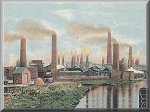 |
|
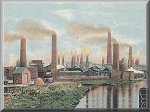 |
Return to
Nuts & Bolts |
|
Return to
contents |
|
Proceed to
Lighter Industries |
|