F. H. Lloyd & Company
Limited - The 1940s and Early 1950s |
During the Second World War,
castings were made for tanks, and for bomb casings. By the end of the war
James Bridge Steel Works could produce over 26,000 tons
of castings a year in 60 different grades of steel. |
The apprentice training scheme
In 1943 the company directors
approved the introduction of an apprentice training
scheme, which began in January 1944. Initially only
certain parts of the factory were involved in the
scheme, but within a few months all the departments
were involved. A carefully planned schedule of work
was planned for each apprentice, specifying the
different operations to be learnt, and the time that
would be spent on each. This ensured that the scheme
would ultimately produce skilled moulders, core
makers, pattern makers, fettlers, electricians,
mechanics and fitters. It was hoped that some of the
successful apprentices would eventually become
foremen, or senior management.
Talks were held with local
schools, and the Ministry of Labour in the hope of
attracting what was described as the 'better type of
boy'. |
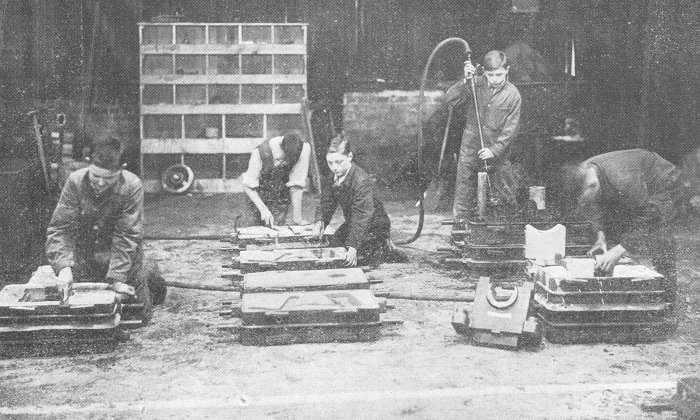
Pupils in the Foundry School
at work. From 'The Steel Casting', courtesy of Wendy
Marston. |
An important feature of the
scheme was the method of wage payment to the
apprentices. All under eighteens were paid on a
special time rate basis. Every four weeks, marks
based on timekeeping, general behaviour, progress at
work, etc. were awarded to all apprentices. The pay
rate depended upon the marks awarded. If anyone
persistently failed to achieve the required standard
of proficiency, their contract of employment was
terminated.
The scheme was divided into two
main classes, Craft Apprentices, and Engineering
Student Apprentices. Craft Apprentices were trained
to become craftsmen in one of the following
departments: the Foundry, the Pattern
Shop, the Fettling and Finishing
Departments, the Maintenance Engineering
Department, or the Machine Shops. It was intended that
all boys embarking on a craft apprenticeship course
would enter the school on joining the company and
spend from 6 to 18 months there, before passing to
other sections of the factory.
|
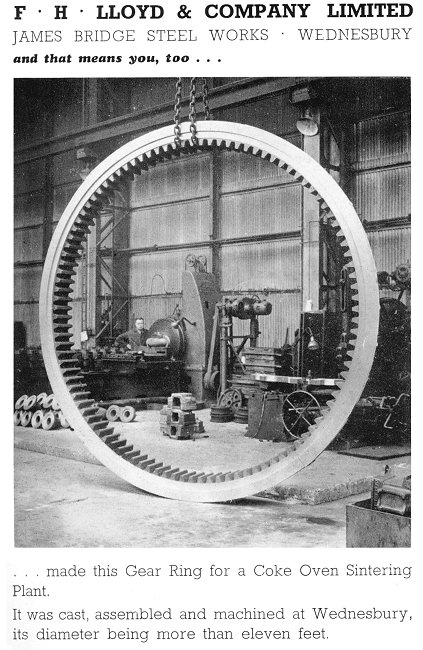
An advert from 1949. From 'The
Steel Casting', courtesy of Wendy Marston. |
Engineering Student Apprentices came from
technical and secondary schools, usually at 16 years
of age, and had to possess at least a School Leaving
Certificate. They were trained to become
draughtsmen, chemists, time study or planning
engineers. To this end a special schedule of
training was drawn up covering a wide range of
subjects. Apprentices were encouraged to
attend evening classes. All fees and expenses were
paid by the company and prizes were presented to
successful students at the end of the year.
Records
relating to all apprentices were maintained in the
Personnel Department, and on completion of the
course, all apprentices having achieved marks of 65
percent or higher received a certificate. Those who
achieved marks of 85 percent or higher, were classed
as being in the honour grade.
In 1946 the company acquired a
competitor, Parker Foundry Limited of Derby and doubled
production there. Plans were made for the modernisation
of the Darlaston works, and for equipping the foundry at
Burton for the production of railway castings. |
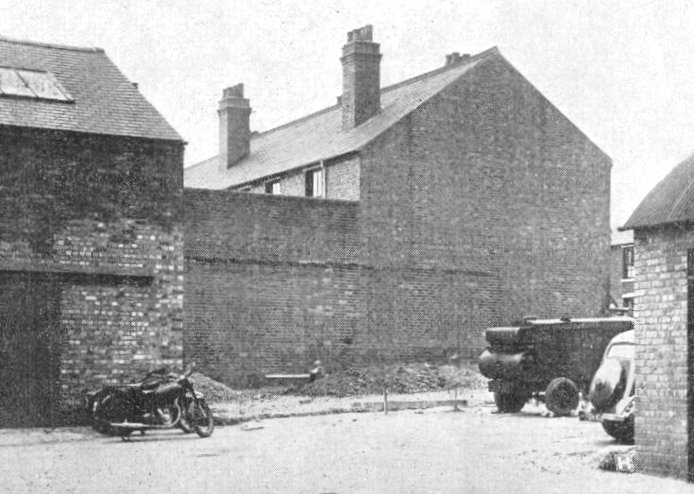
The site of the extension
to the Foundry Training School. From 'The Steel
Casting', courtesy of Wendy Marston. |

The Foundry Training
School in 1957. From 'The Steel Casting',
courtesy of Wendy Marston. |
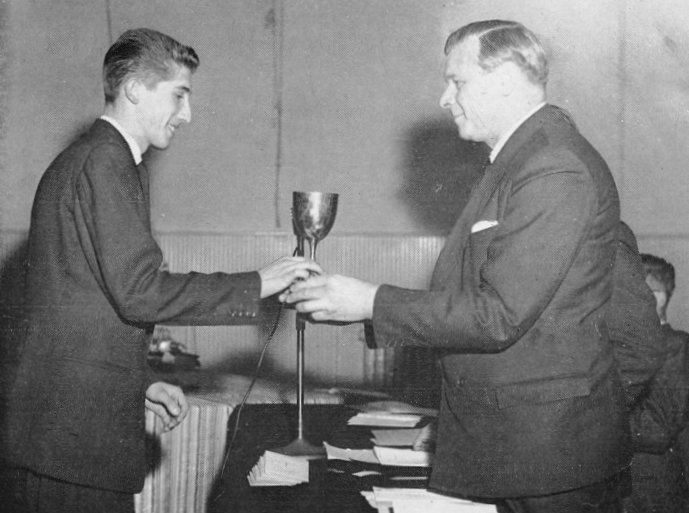
At the apprentice
prize distribution in 1959, Brian Franks
receives the Sportsman of the Year Cup
from Mr. M. C. Lloyd. From 'The Steel
Casting', courtesy of Wendy Marston. |

At the
apprentice prize distribution in
1959, Roy Degville receives the
Rosebowl Trophy from Mr. M. C.
Lloyd, on behalf of the foundry
apprentices. From 'The Steel
Casting', courtesy of Wendy Marston. |
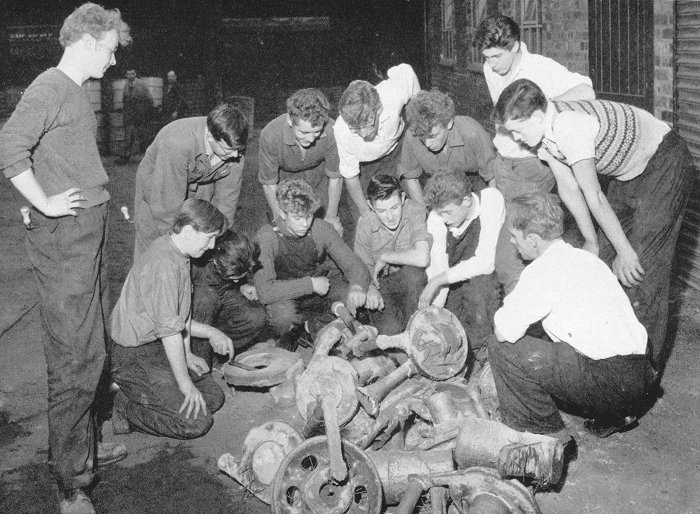
First year
foundry apprentices and their
instructor Jim Platt examine
castings produced at the Foundry
School in 1961. From 'The Steel
Casting', courtesy of Wendy
Marston. |
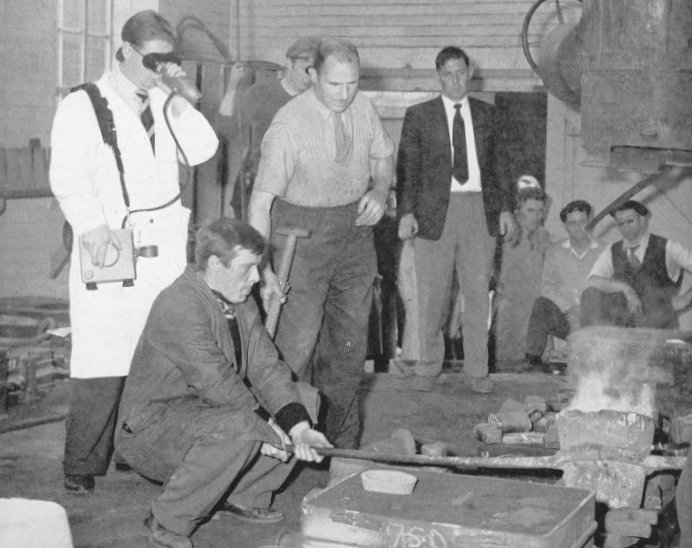
The first
of a series of experimental
heats is cast at the Foundry
School in 1961. From 'The Steel
Casting', courtesy of Wendy
Marston. |

Young
foundry apprentices listen
attentively to instructor
Geof Burns in 1964 as he
describes some of the
problems associated with
moulding. From 'The Steel
Casting', courtesy of Wendy
Marston. |
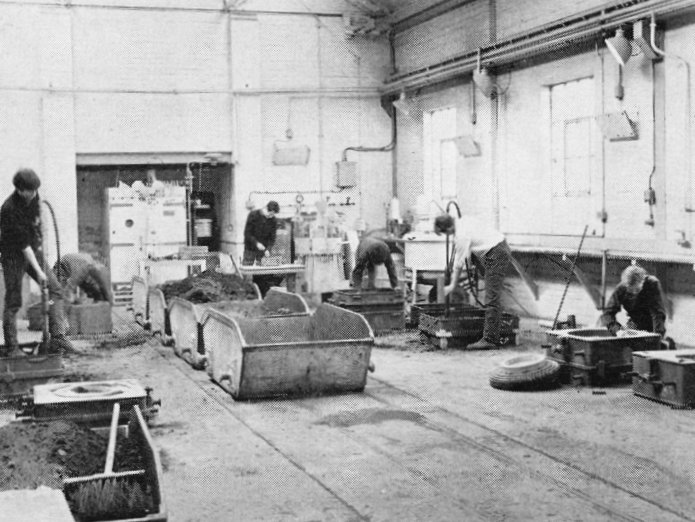
First year foundry
apprentices working in
the Foundry Training
School. From 'The Steel
Casting', courtesy of
Wendy Marston. |
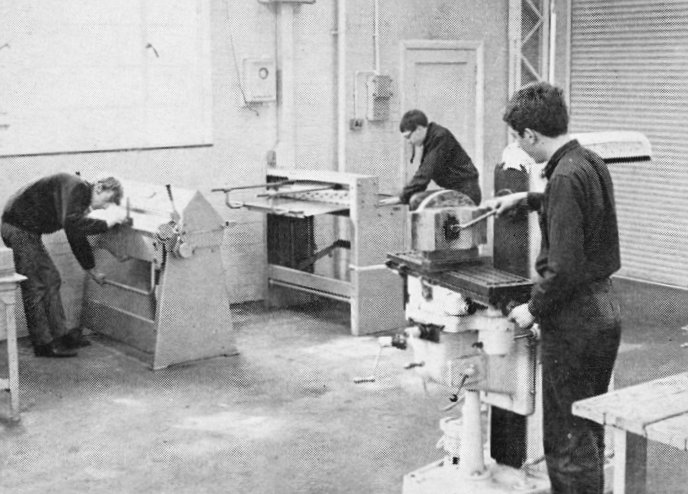
First year 'off the
job' engineering
apprentices engaged
in sheet metal work
and horizontal
milling. From 'The
Steel Casting',
courtesy of Wendy
Marston. |
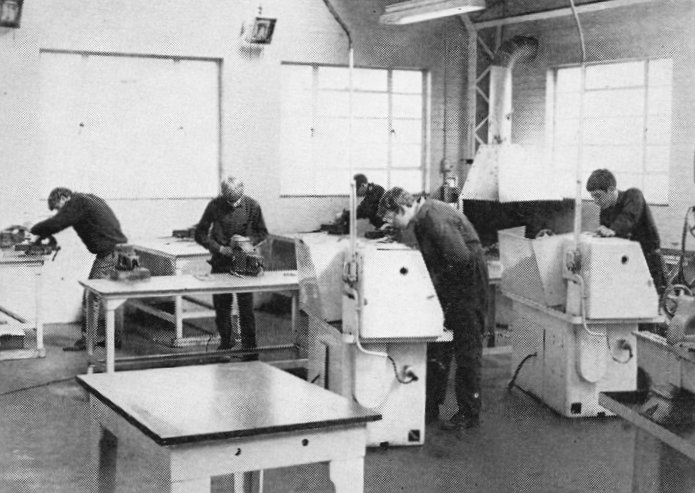
First year
machinist and
fitting
apprentices at
work on bench
fitting and
lathe practice
in the
Engineering
Training School.
From 'The Steel
Casting',
courtesy of
Wendy Marston. |
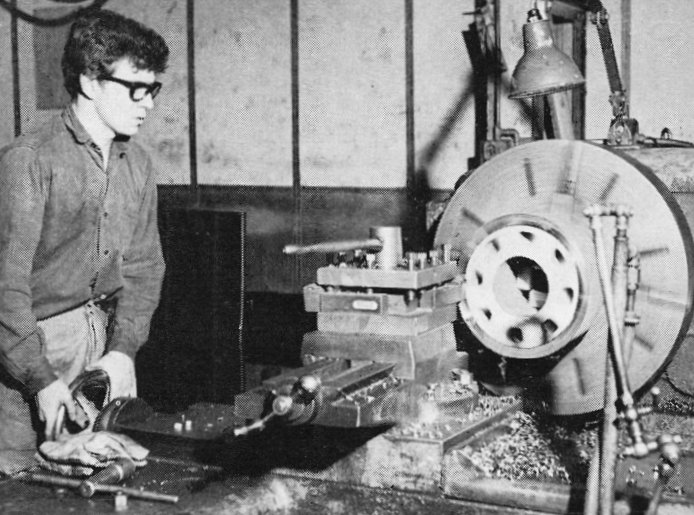
A third year
machinist
apprentice
working on
advanced
turning
practice in
the Lathe
Section of
the Machine
Shop.
From 'The
Steel
Casting',
courtesy of
Wendy
Marston. |
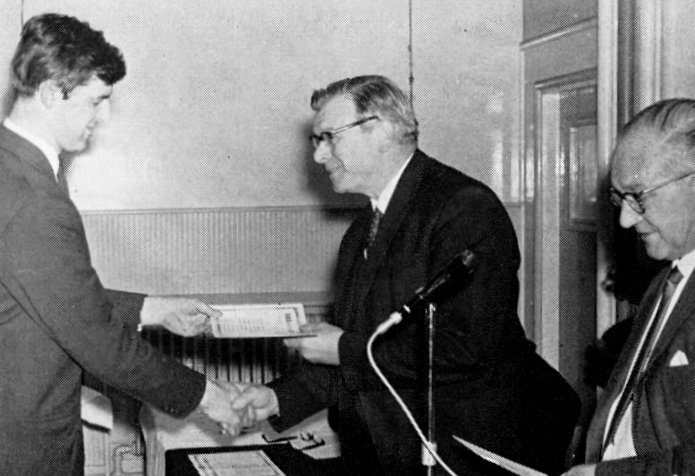
Mr. M.
C. Lloyd
presenting
his son
Mr. D.
C. Lloyd
with his
apprenticeship
certificate
on 22nd
November,
1967.
From
'The
Steel
Casting',
courtesy
of Wendy
Marston. |
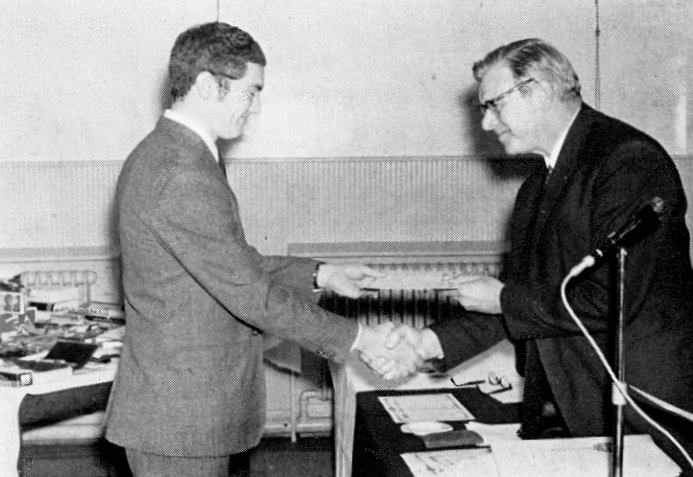
Mr. M.
C. Lloyd
presenting
Mr. G.
Mills
(Machine
Shop)
with his
apprenticeship
certificate
on 22nd
November,
1967.
From
'The
Steel
Casting',
courtesy
of Wendy
Marston. |
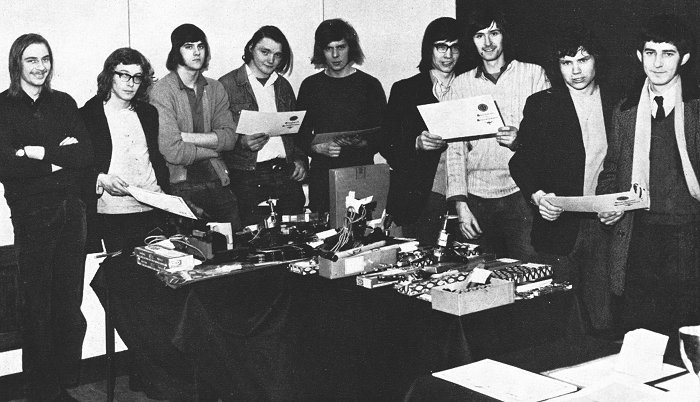
Apprentices
receiving
their
awards
in
1973.
Left
to
right:
Mick
Williams,
Peter
Jenkins,
Robert
Lee,
Stephen
Greaves,
Paul
Sheppard,
Derek
Loundes,
Dave
Nicholls,
John
Spragg,
and
Edward
Humphries.
From
'The
Steel
Casting',
courtesy
of
Wendy
Marston. |
The tiny amounts of carbon
in steel have a profound effect on its
properties, so much so that it must be
controlled to the nearest .02 percent.
In the early days of steel
making a furnace man would withdraw a small
molten sample from a turbulent bath of white-hot
steel, and pour it into a flat mould. After
cooling, it would be broken in two with a
seven-pound hammer and the bright silver-grey
fracture would be examined in the blazing light
from the furnace door.
Skilled workers could
forecast the carbon content of several tons of
molten steel from the closely knit grain of the
broken sample.
The method was unreliable,
and so in the late 1940s it was just used to
obtain a preliminary estimate of carbon content.
The furnace men at F. H.
Lloyds now relied on the accurate reading from a
carbometer, which provided a rapid method of
measuring carbon content, free from the vagaries of human
error. Even so, a sample had to be taken from
the furnace and used to cast a perfectly sound
test piece. |
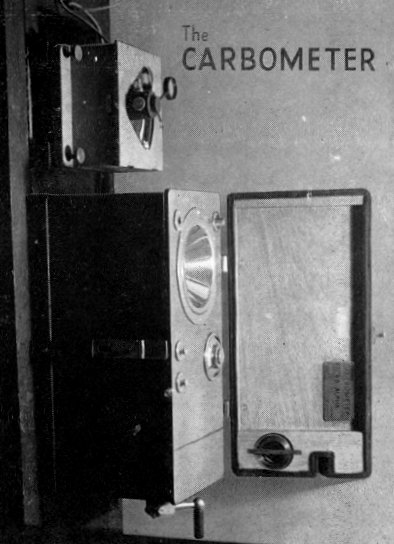 |
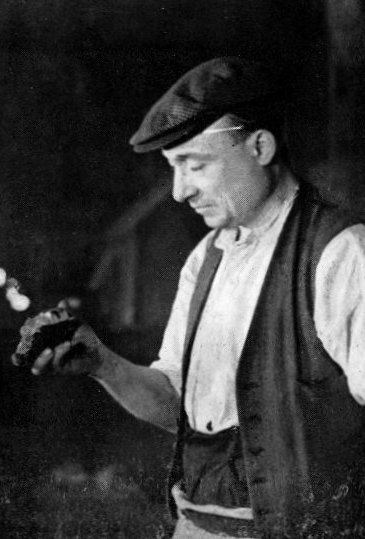 |
|
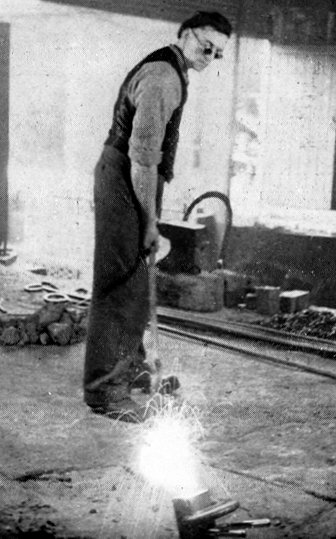 |
Thomas Hale, reading a fracture.
From 'The Steel Casting', courtesy of
Wendy Marston. |
|
V.
Blythe casting a carbometer sample.
From 'The Steel Casting', courtesy of
Wendy Marston. |
|
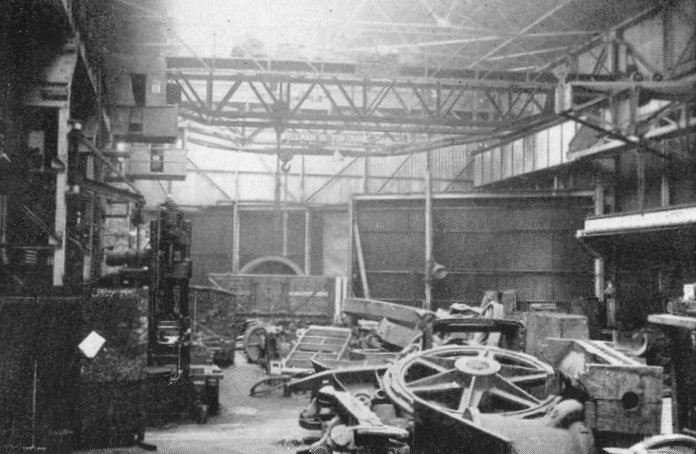
The Heavy Dressing Department.
From 'The Steel Casting', courtesy of Wendy Marston. |
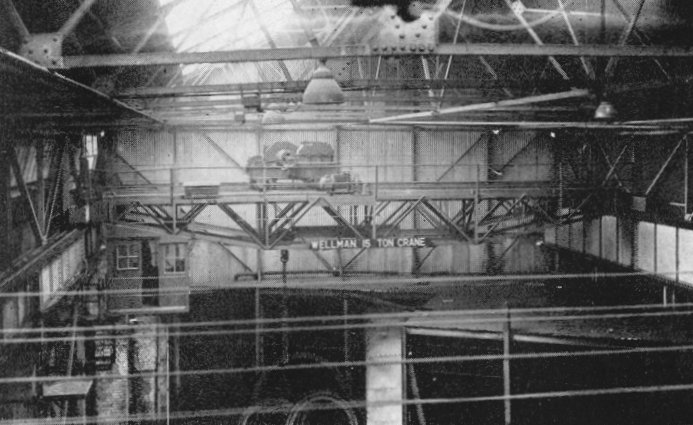
The new Wellman crane
installed in the the Heavy Dressing Department in
1949. From 'The Steel Casting', courtesy of Wendy
Marston. |
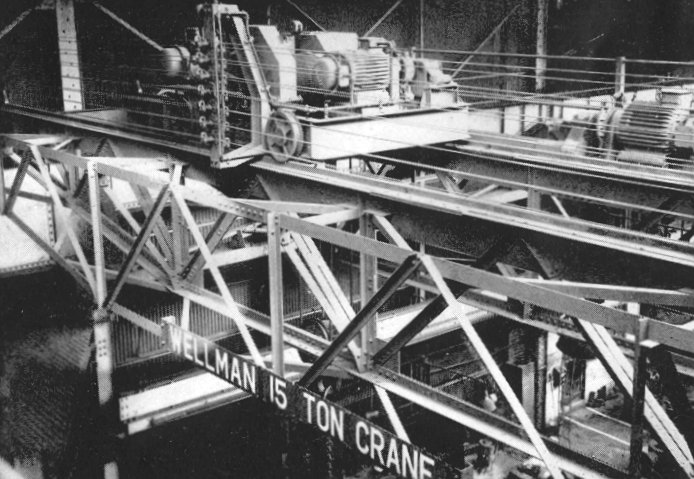
A close-up view of the new
crane. From 'The Steel Casting', courtesy of
Wendy Marston. |
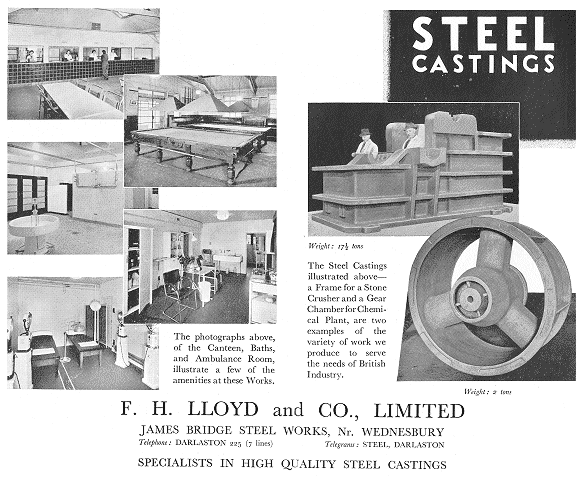
An advert from 1949. |
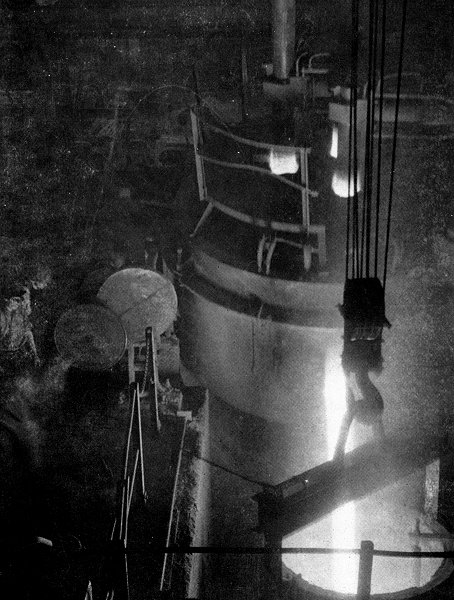 |
Tapping an electric arc
furnace. From 'The
Steel Casting', courtesy of Wendy Marston. |
An advert from 1950.
From 'The Steel Casting',
courtesy of Wendy Marston. |
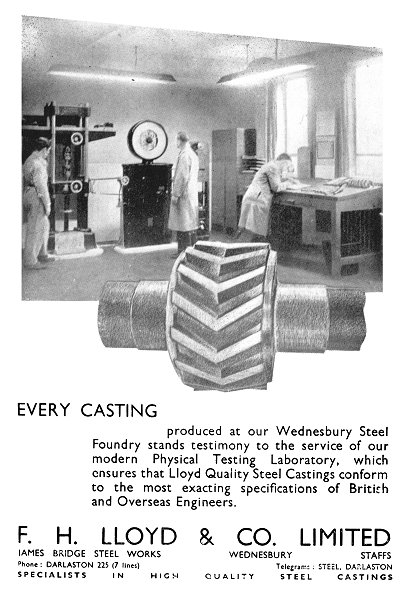 |
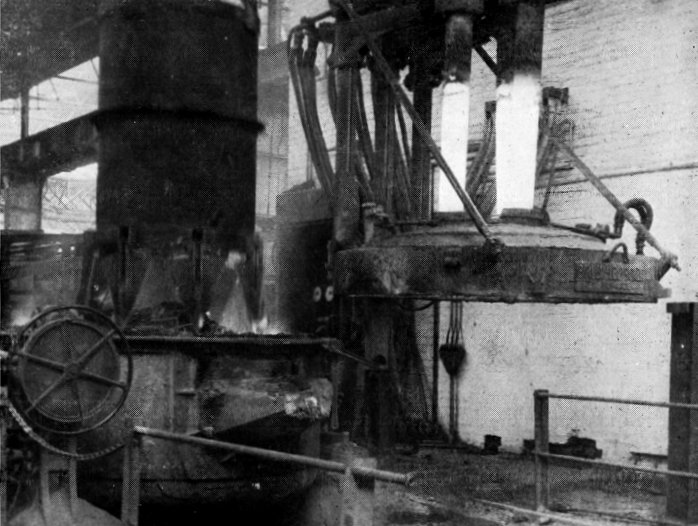
Charging an electric furnace
with steel scrap. From 'The Steel Casting', courtesy
of Wendy Marston. |
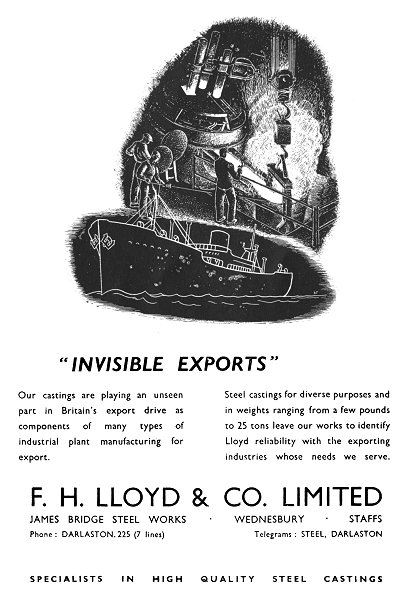 |
An advert from 1950.
From 'The Steel Casting',
courtesy of Wendy Marston. |
An advert from 1950.
From 'The Steel Casting',
courtesy of Wendy Marston.
|
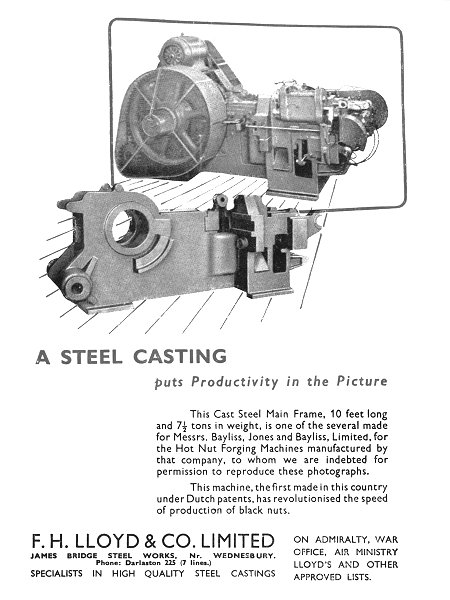 |
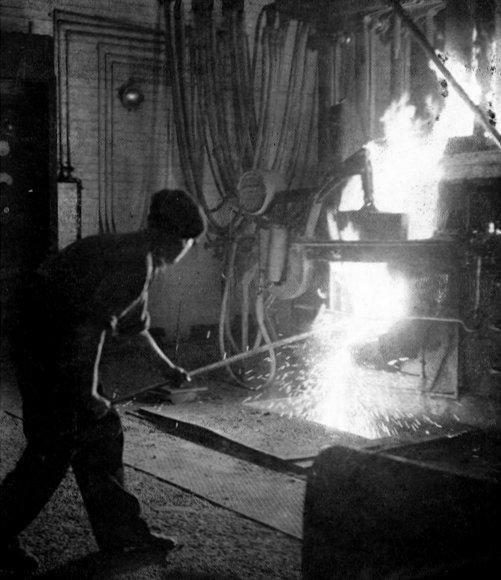 |
Removing the oxidising
slag in the course of a basic electric heat.
From 'The Steel Casting',
courtesy of Wendy Marston. |
An advert from 1950.
From 'The Steel Casting',
courtesy of Wendy Marston.
|
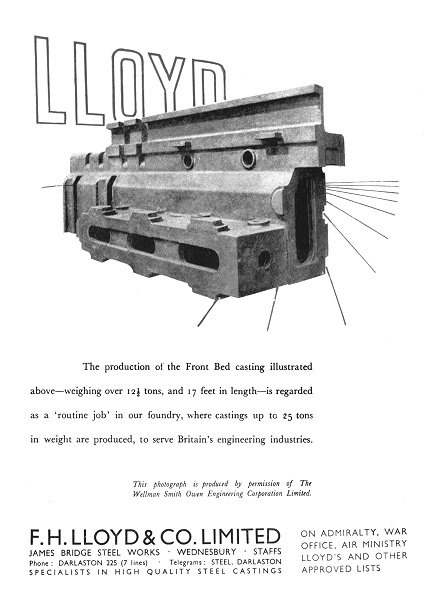 |
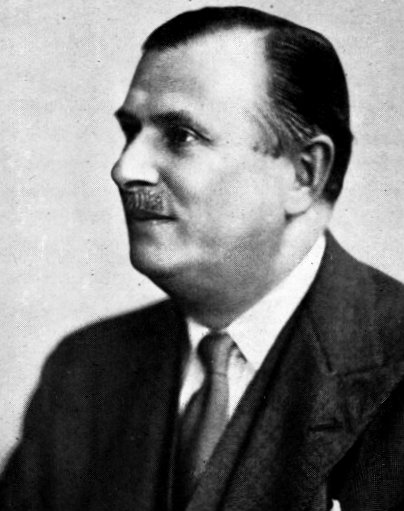 |
Mr. Victor William Bone
who was a Director of the company until 1949, and
Chairman from 1941 until 1949.
He died on 12th October, 1951
and was buried at Lincoln.
From 'The Steel Casting',
courtesy of Wendy Marston. |
Radio Outside Broadcast
On 9th September, 1952 a BBC
radio outside broadcast team came to the James
Bridge site to record part of a programme about the
manufacturing of Centurion tanks. At the time the
turrets were cast at the factory, in one piece, in
armour steel. The programme included a section about
the heat treatment process, and the quenching
necessary to produce a turret from steel with the
required strength and toughness.
An interview took place in the
Heavy Heat Treatment Department beside the water
quenching tank, during which the well known radio
presenter Mr. "Jim" Pestridge talked to Mr. F. N.
Lloyd, Horace Taylor, supervisor of the Heavy
Foundry, and Arthur Reynolds, supervisor of Heavy
Heat Treatment Department. |
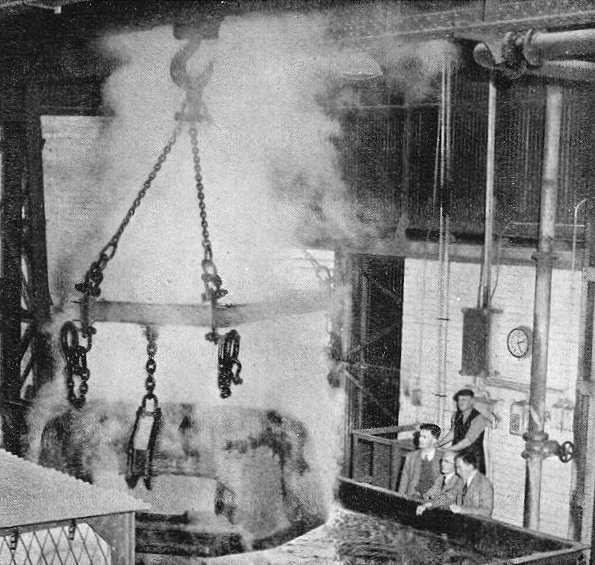
The interview in the Heavy
Heat Treatment Department as a turret is quenched.
From 'The Steel Casting', courtesy of Wendy Marston. |
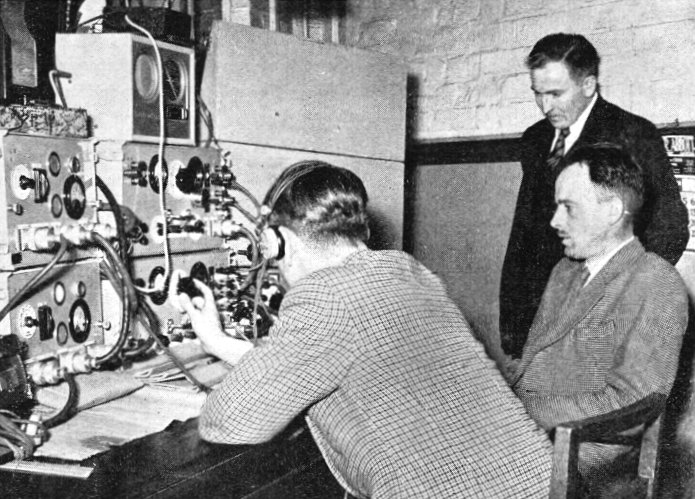
Members of the BBC team adjust
their equipment. From 'The Steel Casting', courtesy
of Wendy Marston. |
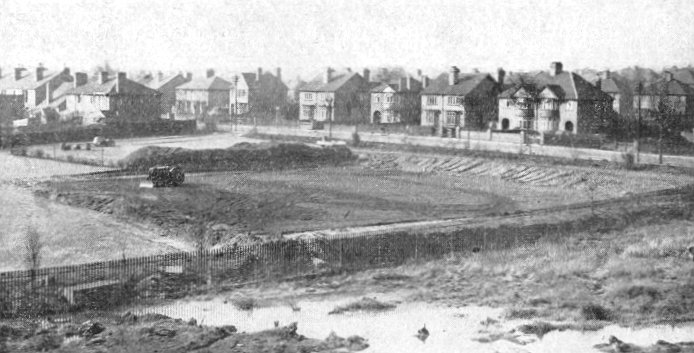
Work gets underway on the new
bowling green alongside Park Lane in the spring of
1952. From 'The Steel Casting', courtesy of Wendy
Marston. |
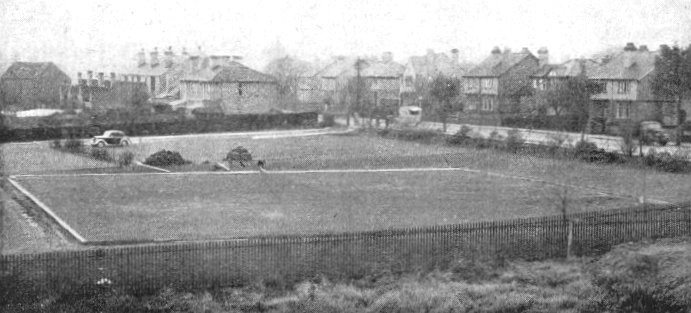
The new bowling green, just
after completion. From 'The Steel Casting', courtesy
of Wendy Marston. |
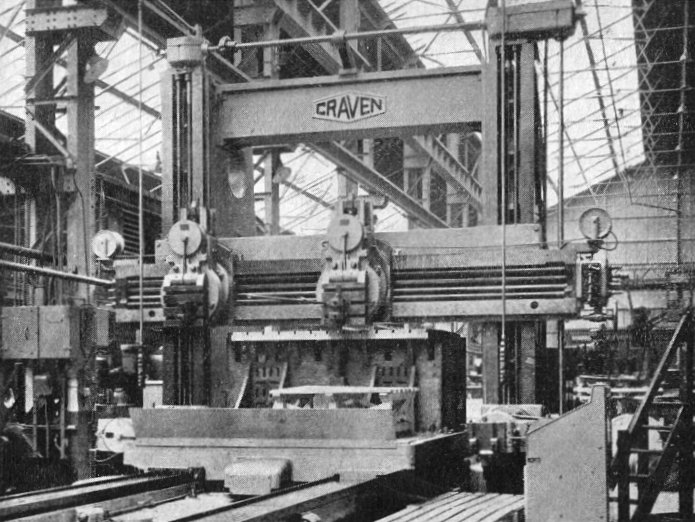
The new Craven planing machine
that was installed in the Machine Shop in 1952.
From 'The Steel Casting', courtesy of Wendy Marston. |
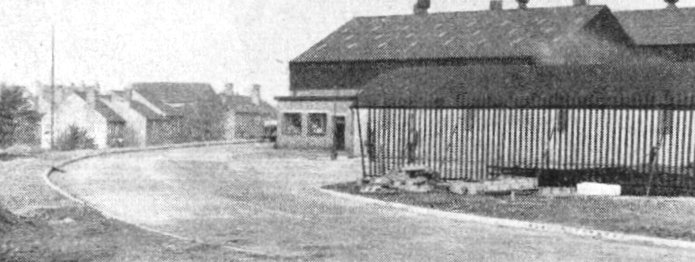
The new factory road, built in
1952. From 'The Steel Casting', courtesy of Wendy
Marston. |
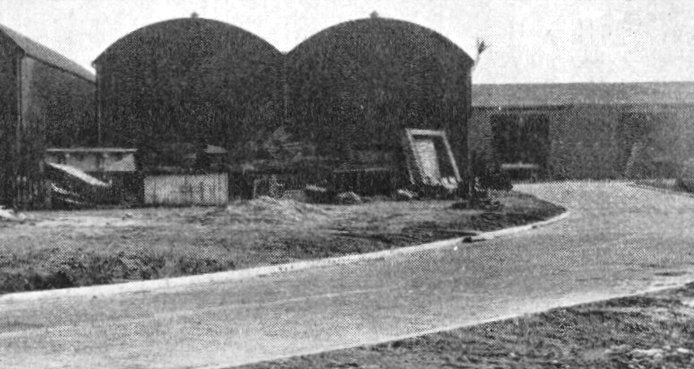
Another view of the new road.
From 'The Steel Casting', courtesy of Wendy Marston. |
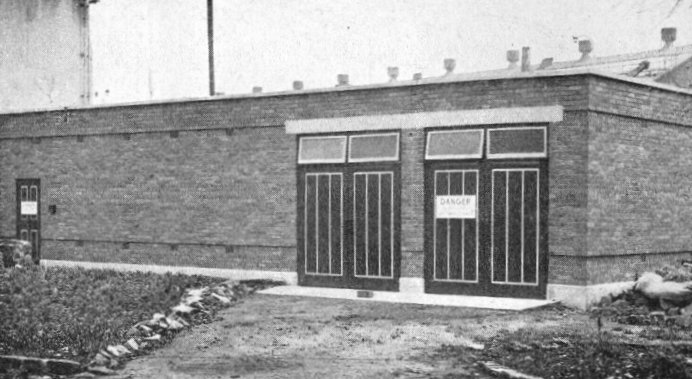
The new electricity sub
station built in 1952 that supplied electricity to
the whole of the site. From 'The Steel Casting',
courtesy of Wendy Marston. |
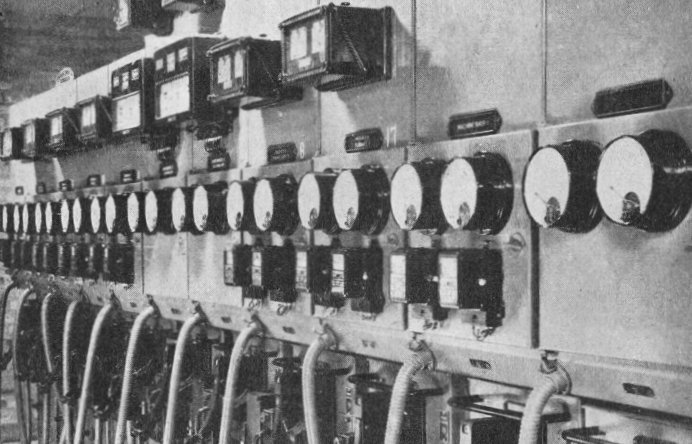
Some of the electrical
equipment in the new sub station. From 'The Steel
Casting', courtesy of Wendy Marston. |
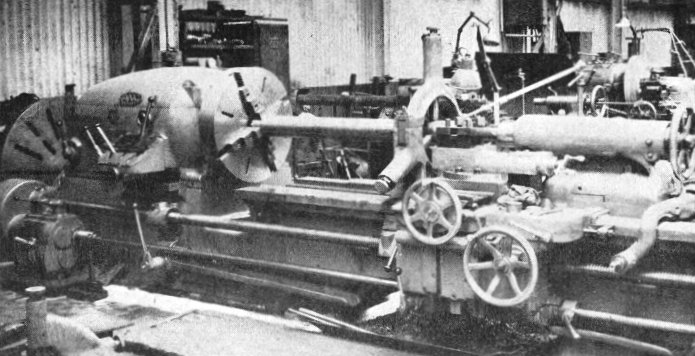
The Lang lathe that was
installed in the Machine Shop in 1952. From 'The
Steel Casting', courtesy of Wendy Marston. |
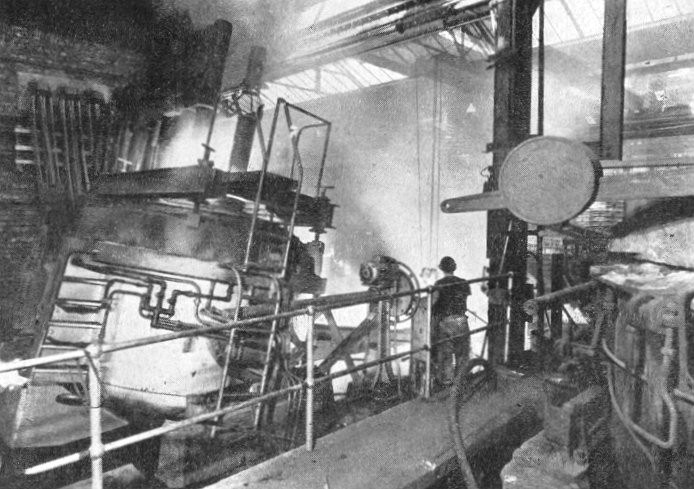
A new 3½
ton electric melting furnace installed in 1952.
From 'The Steel Casting', courtesy of Wendy
Marston. |
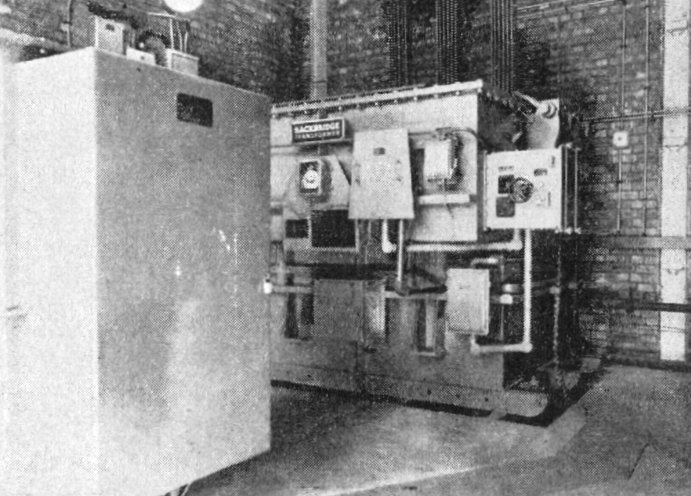
The transformer
for the new 3½
ton electric melting furnace. From 'The
Steel Casting', courtesy of Wendy
Marston. |
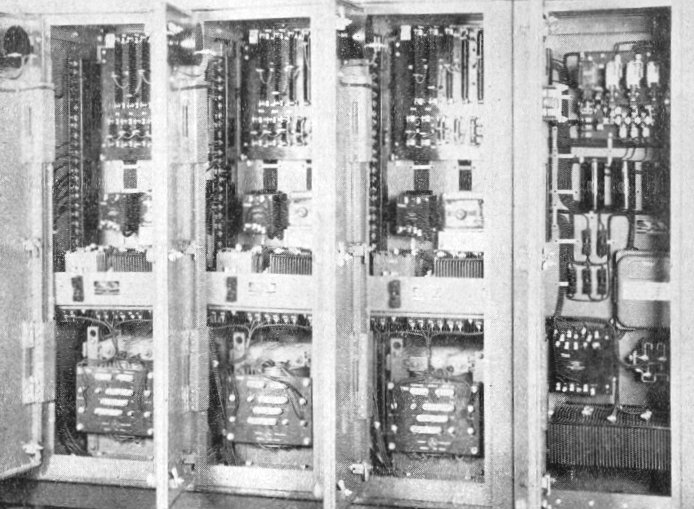
The Amplidyne control
gear that controlled the electrodes in the
new new 3½
ton electric melting furnace. From 'The
Steel Casting', courtesy of Wendy Marston. |
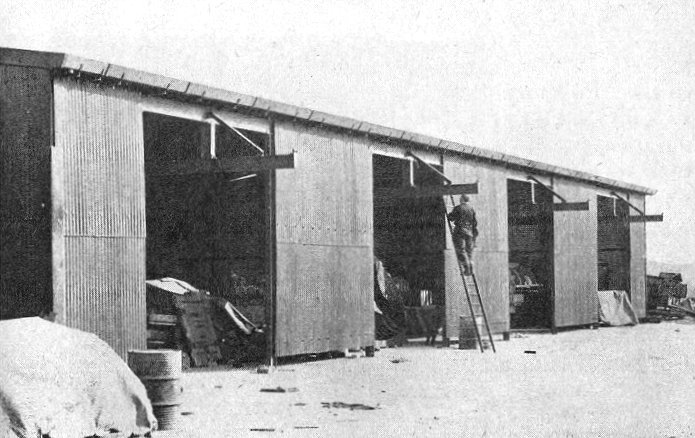
The new 96 feet by 70 feet
pattern storage barn built in 1952. From 'The Steel
Casting', courtesy of Wendy Marston. |
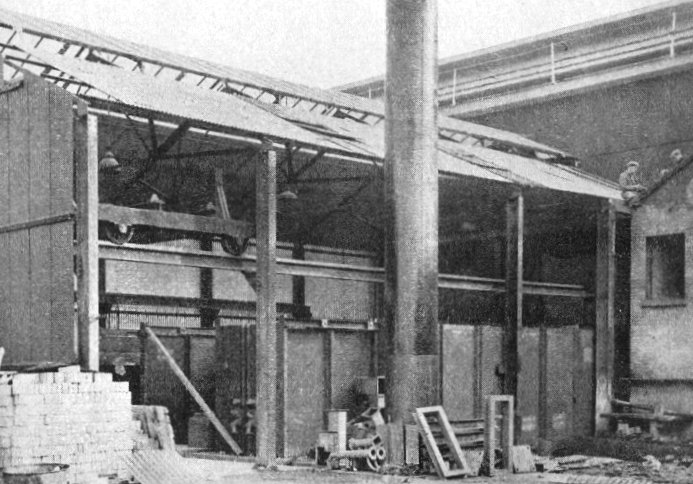
The building housing two mould
stoves, erected in 1952. From 'The Steel Casting',
courtesy of Wendy Marston. |
By 1952 when the company's last
open hearth furnace was scrapped, Lloyds had 6 electric
arc furnaces with a capacity ranging from 2½
to 12 tons.
The
foundry could turn out very large castings, and
machine them to individual customer's requirements
in an
up-to-date machine shop.
Around
this time large machines such as tyre presses were produced
in the factory.
|
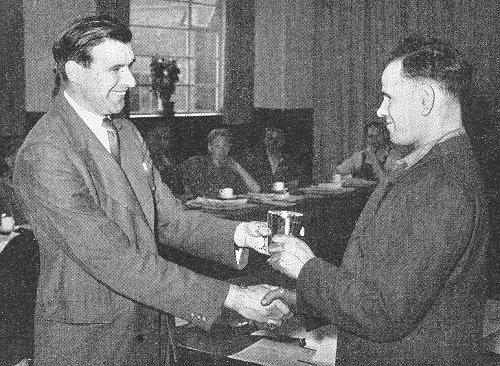
Mr. A. B. Lloyd (on the left)
presents a silver tankard to Robert Thynne. |
During the financial year ending on the 31st March, 1952,
Lloyds produced more than 23,000 tons of black or
un-machined castings, consisting of over 650,000 single
castings. Large numbers of machined castings, patterns,
and ingots were also were
produced. Some of the largest castings produced were
steam chests for the electricity generating industry. They
weighed up to 60 tons. Two cranes would be linked
together with a lifting beam to take them out of the
casting pit. When freshly cast with the pouring heads
still attached, they weighed around 70 tons. |
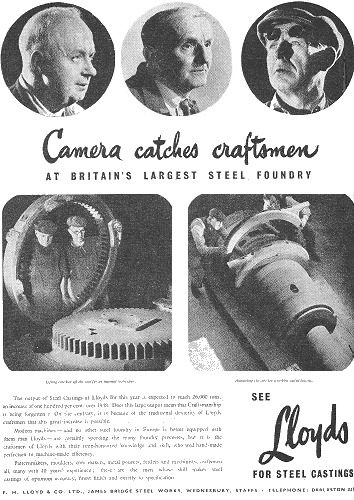
An advert from 1952. |
The advert on the left is
worded as follows:
The output for steel castings at Lloyds for this
year is expected to reach 26,000 tons, an
increase of one hundred percent over 1948. Does
this large output mean that craftsmanship is
being forgotten? On the contrary, it is because
of the traditional dexterity of Lloyds craftsmen
that this great increase is possible.Modern
machines - and no other steel foundry in Europe
is better equipped with them than Lloyds - are
certainly speeding the many foundry processes,
but it is the craftsmen of Lloyds with their
time-honoured knowledge and skill, who wed
hand-made perfection to machine-made efficiency.
Patternmakers, moulders, core makers, metal pourers,
fettlers, and machinists, craftsmen all, many with 40
years' experience; these are the men whose skill makes
steel castings of optimum accuracy, finest finish and
exactly to specification. |
|
|
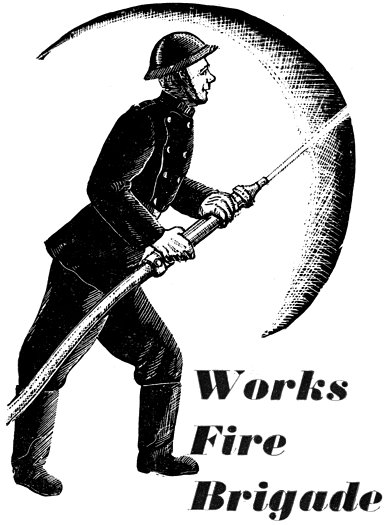 |
From the spring 1953
edition of 'The Steel
Casting':
The year 1952 showed a
marked increase in the
number of fires which
occurred in the works
compared with the previous
two years:
1950 - 15, 1951 - 22, 1952 -
26
Fire fighting materials used
in the extinction of some of
these fires included carbon
tetrachloride foam, carbon
dioxide, hose branches etc.
After each fire a full
survey and inspection was
carried out to find the
cause whenever possible, so
that improvement could be made
to eliminate any further
outbreaks.
I found that seven fires out
of the total number during
1952 should never have
happened if precautions had
been taken by workmen
concerned.
May I advise everyone,
whether at home or work, not
to take any risks that will
start or cause an outbreak
of fire. |
|
|
Fire extinguishers are
checked at regular intervals
by the Fire Dept., but there
are still one or two cases
where extinguishers are
being used and left empty.
Please inform the fire
station or your foreman.
During the past year members
of the Brigade carried out
drills and maintenance work
as well as attending water
exercises, lectures and
competitions, which had been
arranged by the Darlaston
and Wednesbury Works Fire
Brigades Group.
Special duties covered by
the Works Brigade included
the gala and sports day and
children's Christmas
parties.
The F.H.L. Brigade will take
part alongside other works
brigades in the district
during the coming year and
some of the items planned
are:
Jan. 18th films and quiz
Feb. 8th lecture; "pumps and
water"
Mar. 22nd large scale
exercise.
Chief Officer J. S. REA, F.
H. LIoyd & Co. Ltd. Fire
Brigade.
|
|
|
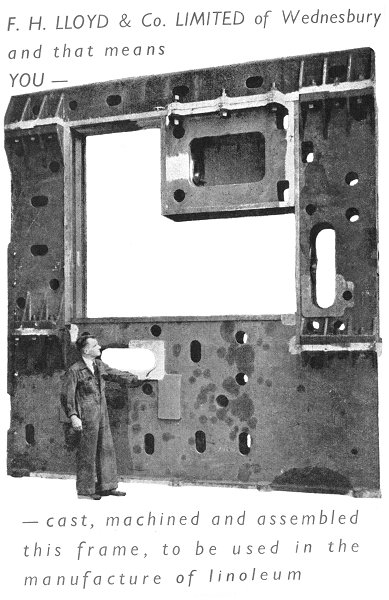
An advert from 1953. From 'The
Steel Casting', courtesy of Wendy Marston. |
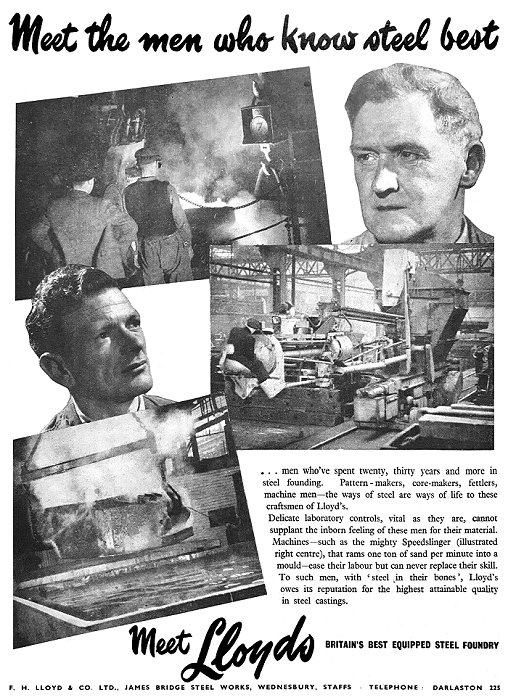 |
An advert from The
Engineer, 15th May, 1953. |
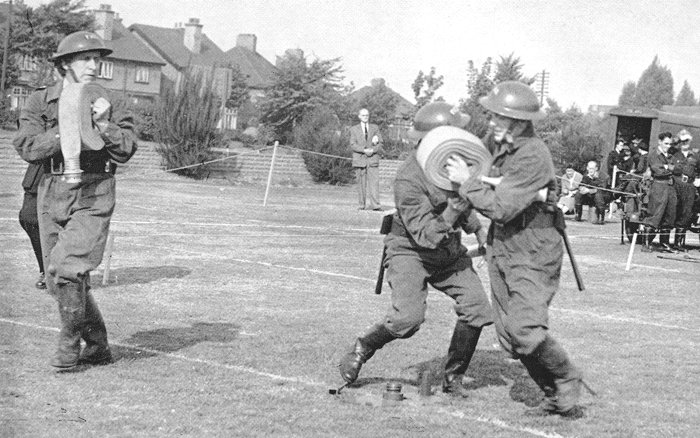
Three members of the four
man team competing in the hydrant drill at the
sports ground on Sunday 20th September, 1959.
Left to right: G. Wilkinson, E. Danks, and W.
Langley. From 'The Steel Casting', courtesy of
Wendy Marston. |
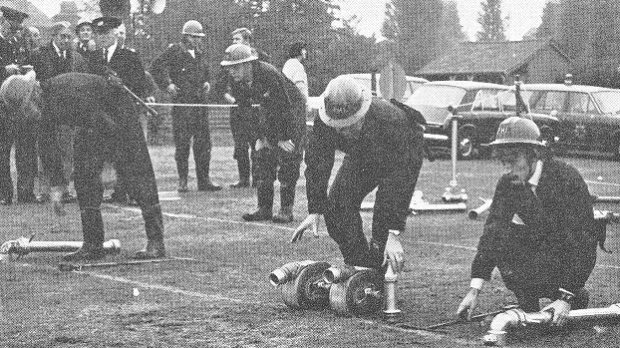
The F. H. Lloyd Fire Brigade in
action during the 21st Annual Fire Brigade Competition
that was held at the work's sports ground on Sunday, 8th
October, 1972. The event was won by the Rubery Owen
team. The four-man F. H. Lloyd team shown in the
photograph are left to right: Trevor Baker, Alan
Bytheway, Basil Reed, and John Lloyd. |
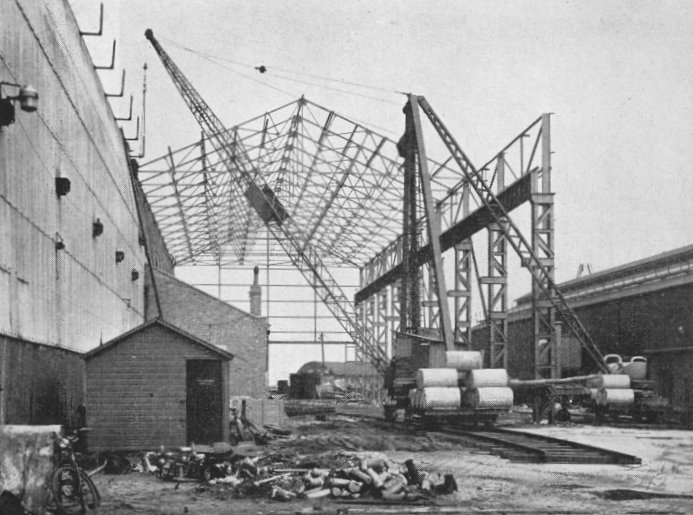
The Machine Shop Heavy Bay
during erection in 1954. From 'The Steel Casting',
courtesy of Wendy Marston. |
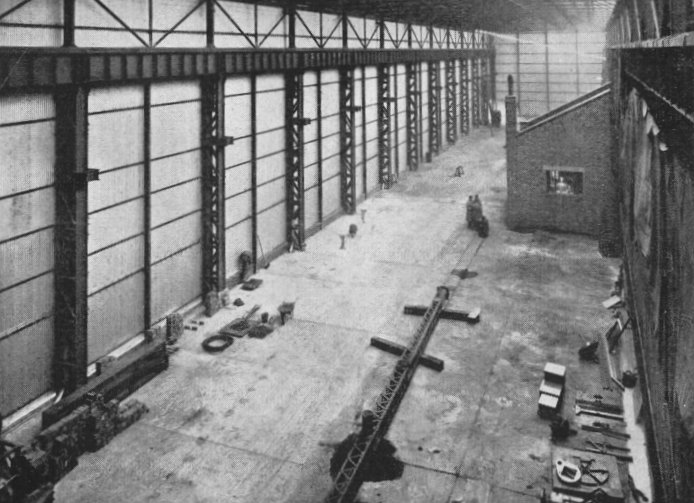
The Heavy Bay nearing
completion. From 'The Steel Casting', courtesy of
Wendy Marston. |
An advert from 1953.
From 'The Steel Casting',
courtesy of Wendy Marston. |
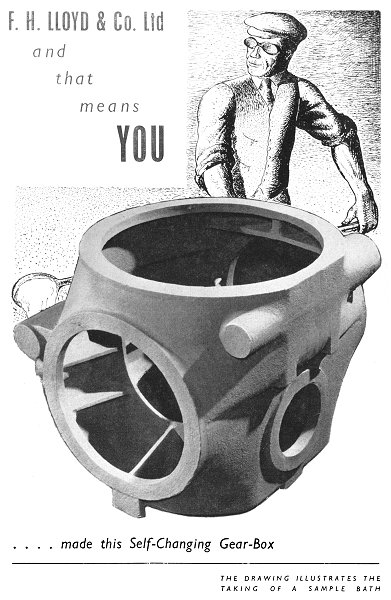 |
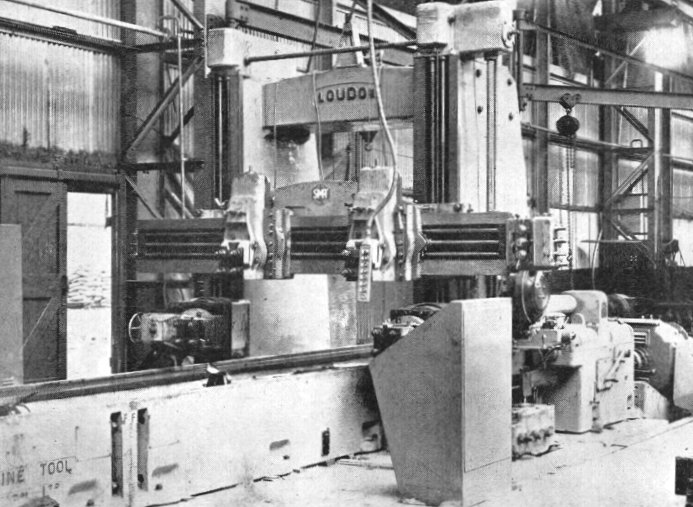
The Loudon planing machine
that was installed in the Machine Shop in 1954. It
was manufactured by the Scottish Machine Tool
Company, and had a maximum capacity of 5ft. by 5ft.
by 14 ft. From 'The Steel Casting', courtesy of
Wendy Marston. |
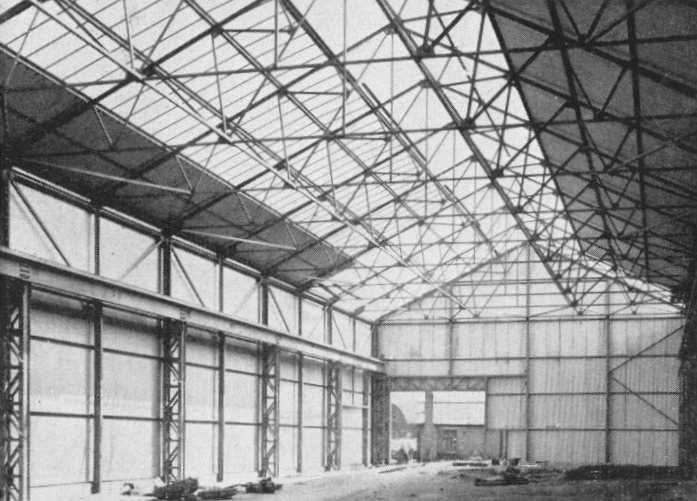
The 182ft. extension to the
New Dressing Shop nears completion in 1954. From
'The Steel Casting', courtesy of Wendy Marston. |
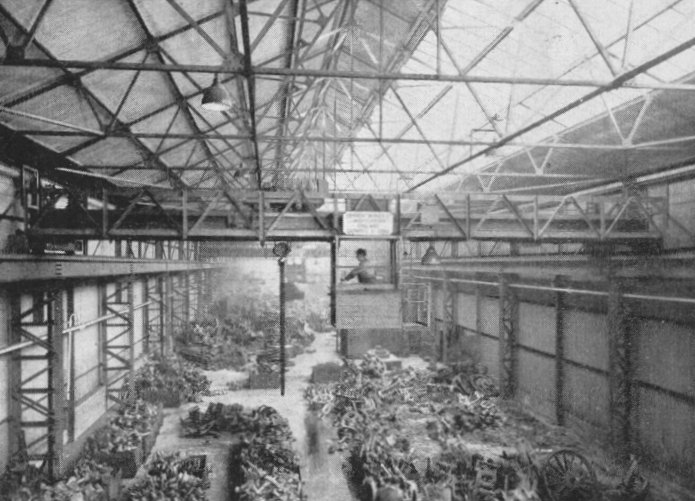
The completed extension to
the New Dressing Shop with its new 5 ton
overhead crane. From 'The Steel Casting',
courtesy of Wendy Marston. |
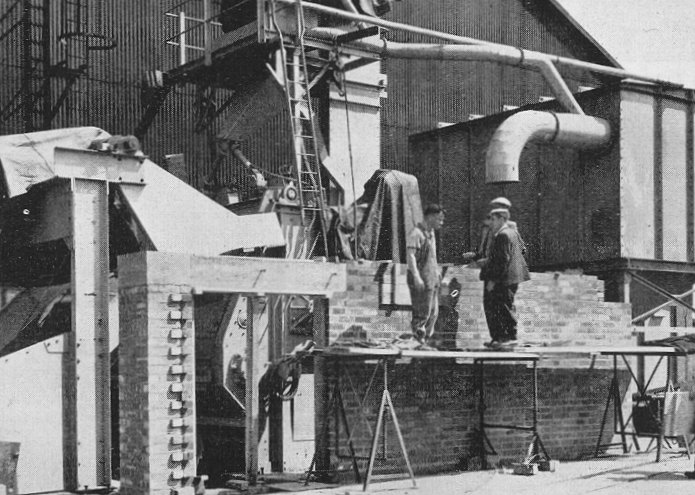
The new building for the
Tumblast Wheelabrator in 1954. From 'The Steel
Casting', courtesy of Wendy Marston. |
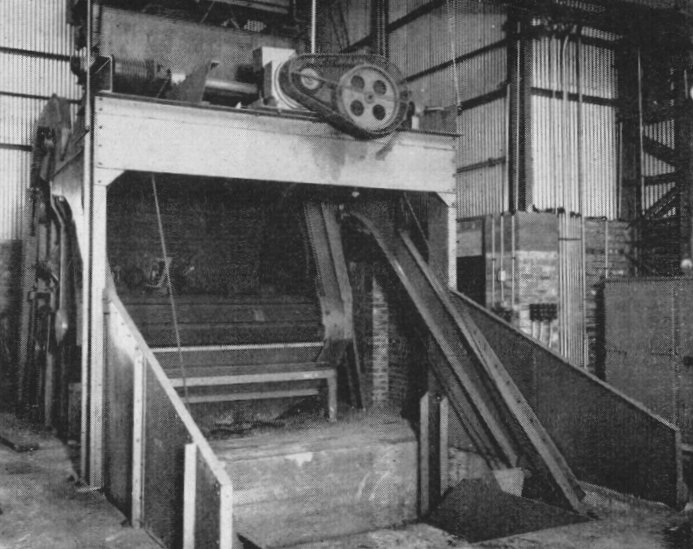
The Tumblast Wheelabrator,
the largest in the country. From 'The Steel
Casting', courtesy of Wendy Marston. |
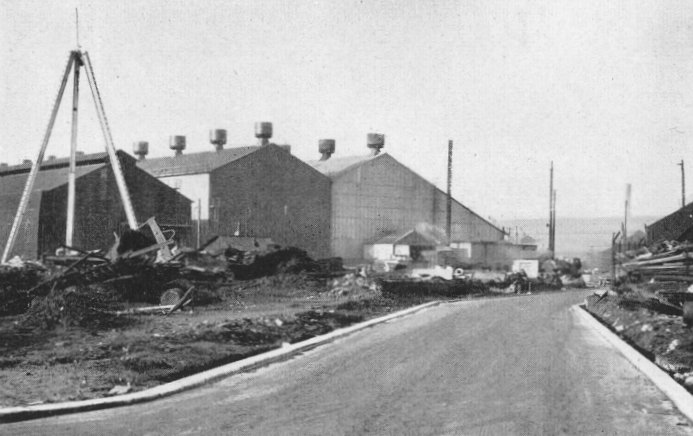
Another view of the new road.
From 'The Steel Casting', courtesy of Wendy Marston. |
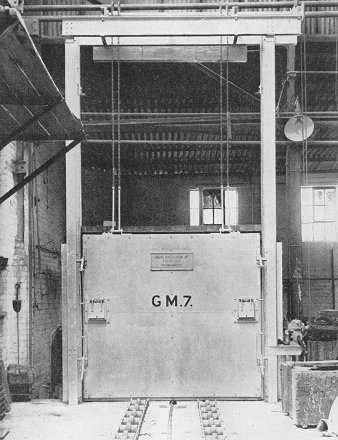 |
|
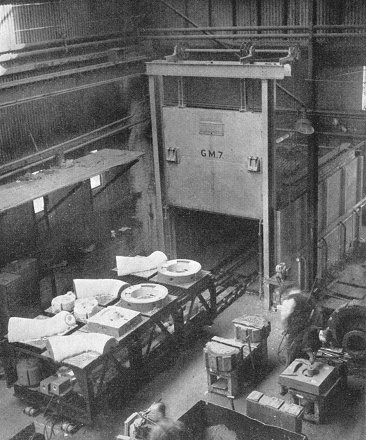 |
The 16ft. by 8ft. Mond gas-fired drying
stove, installed in 1954. From 'The
Steel Casting', courtesy of Wendy
Marston. |
|
Another view of the Mond gas-fired
drying stove with the
double-tier bogey. From 'The Steel
Casting', courtesy of Wendy Marston. |
|
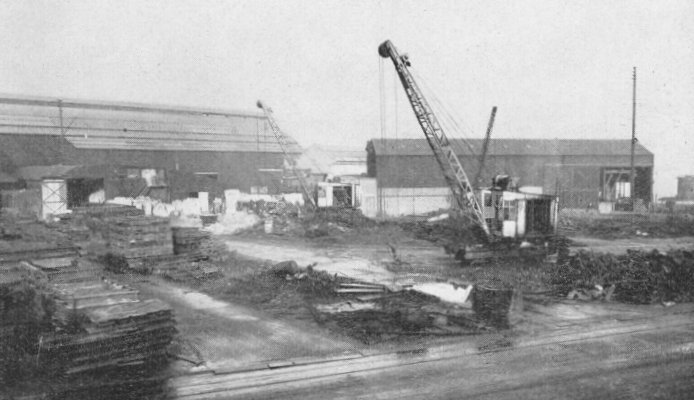
Preparing the ground for the
new road/rail weighbridge and the extension to the
railway, as seen in 1954. From 'The Steel Casting',
courtesy of Wendy Marston. |
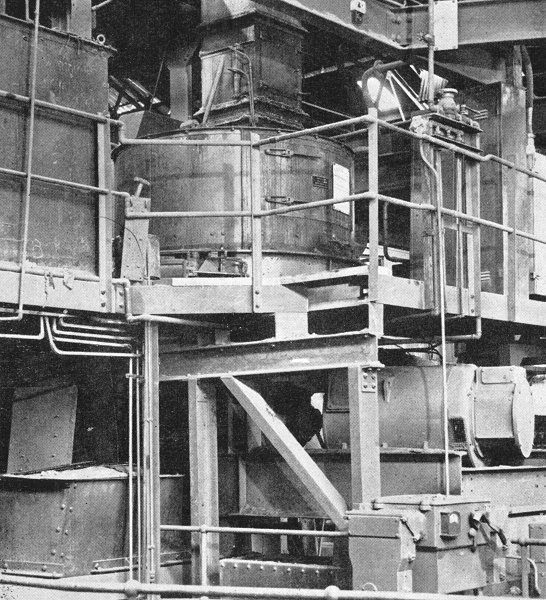
The model 70 Speed Muller sand
milling plant installed in 1954. From 'The Steel
Casting', courtesy of Wendy Marston. |
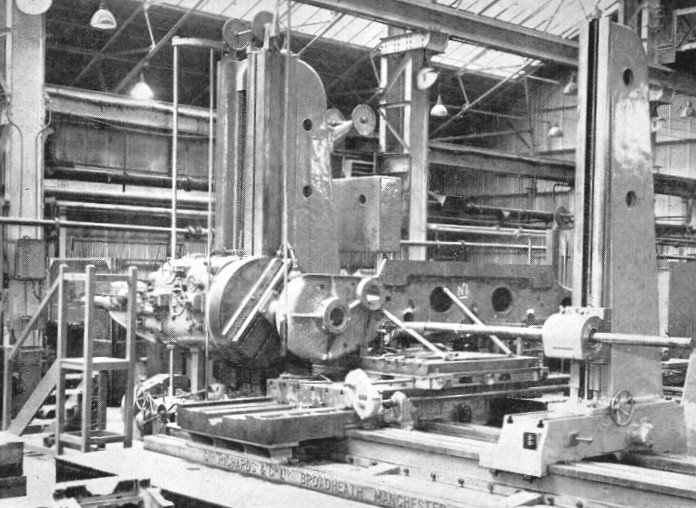
The number 6 horizontal boring
machine manufactured by George Richards Limited that
was installed in the Machine Shop in 1954. From 'The
Steel Casting', courtesy of Wendy Marston. |
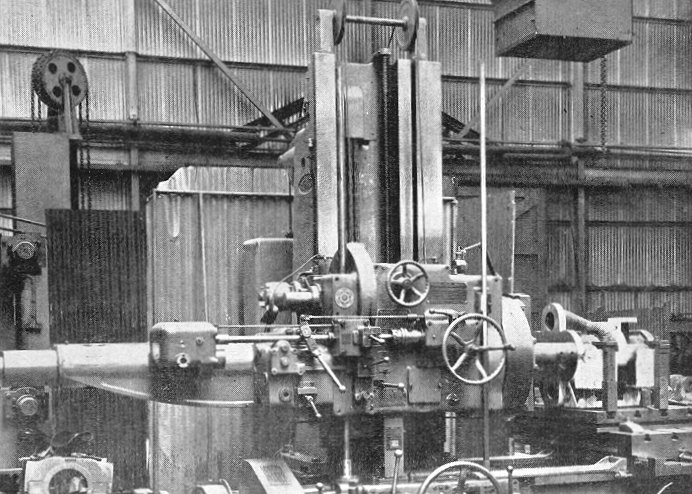
The number 3 horizontal boring
machine manufactured by George Richards Limited that
was installed in the Machine Shop in 1954. From 'The
Steel Casting', courtesy of Wendy Marston. |
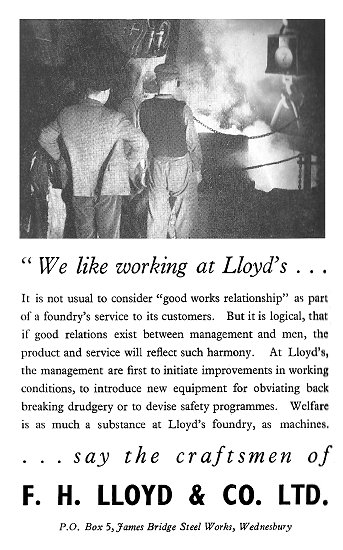
An advert from the mid 1950s. Courtesy of
Christine and John Ashmore. |
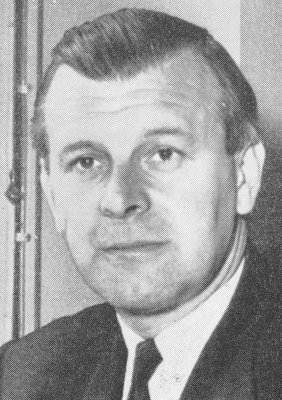
Mr. M. C, Lloyd, M.B.E.,
A.I.Loco.E. |
In January 1954 Mr. Michael Charles Lloyd was invited
to join the business as Works Director, by his elder
brother Francis Nelson Lloyd, Chief Executive. At the
time, the factory produced around 30,000 tons of castings
a year, with about 2,700 staff. |
 |
Casting in the
foundry. From a 1954 works photo.
Courtesy of Wendy Marston. |
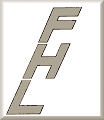 |
|
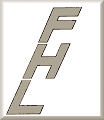 |
|
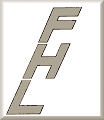 |
Return to the
early 1930s |
|
Return to
the contents |
|
Proceed to the
late 1950s |
|