F. H. Lloyd & Company
Limited - The Later Years
|
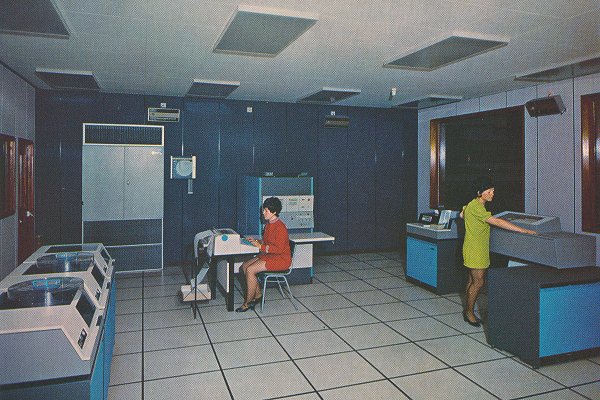
The company's first computer. |
In 1970 an IBM System 360, Model 25 computer was
installed at James Bridge Works. The machine, which cost
£150,000 helped to rationalise production by monitoring
the progress of each order from the initial enquiry to
despatch. It also improved production control, and
assisted with the provision of management information.
Once it had proved itself, it handled the payroll for
most of the group's workforce of 7,000, took over stores
control, handled purchases, and provided sales analysis
and cost accounting data.
It had a CPU with 24,576 bytes of core storage, three
IBM 2311, 7.25 MB hard disc drives, a printer with a
keyboard, a line printer, and a card reader. Although
very high tech for 1970, it is extremely basic by modern
standards. |
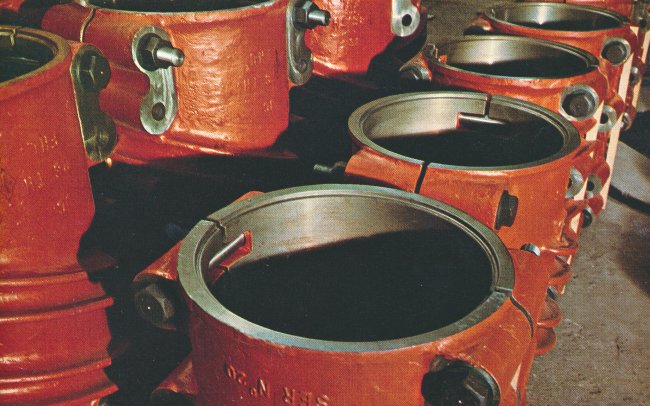
Lloyds produced almost an infinite variety of steel
castings including the ones above, which were produced in
the late 1960s at James Bridge. They were cable glands
for the Pierre Laporte parallel-wire suspension bridge
at Quebec, the first of its kind in Canada. 174 of them
were produced, all with an internal diameter of 24½
inches. The order was valued at £70,000. |
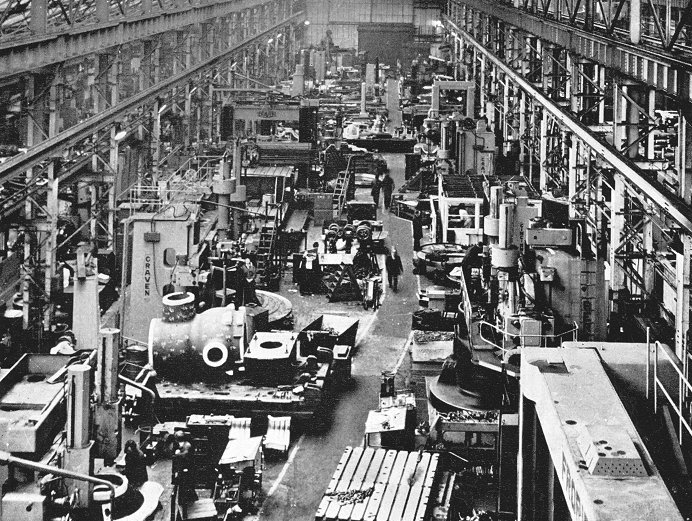
A view of the Machine Shop
from 1970. From 'The Steel Casting', courtesy of
Wendy Marston. |
An
important department at James Bridge was the F.H.L.
Medical Centre which had extensive facilities to deal
with all kinds of injuries sustained in the James Bridge
factory. It was also used by some of the local factories, and
Wednesbury Technical College, thanks to various
agreements.
The centre could cope with a wide range injuries from
a piece of grit in the eye, to molten metal burns,
welding flash, alkaline burns, lime burns, and acid
burns. Every employee had an X-ray on joining the
company, and every 12 months had to have a check-up in
the medical centre. Weight, height, teeth, and eyesight
were checked, and medical records were kept.
Inoculations and vaccinations of all kinds were given,
particularly to members of staff about to travel abroad
on company business.
The centre had its own chiropodist in the form of
Joyce Treadwell, and later Miss Kidney. Surgery was
carried out on three afternoons each week by Dr. Baker,
or Dr. Pollett. There was also a well-equipped
physiotherapy room complete with sunray lamps, infra-red
lamps, massage equipment, and a variety of home nursing
equipment that could be loaned to employees.
Some employees had to wear respirator masks as part
of their job. There were four women in the centre who
were kept busy cleaning the masks so that a clean supply
was always available. There were two masks for each
employee, one for wearing, and one for cleaning. Sister
Powell was in charge of the centre for around 30 years. |
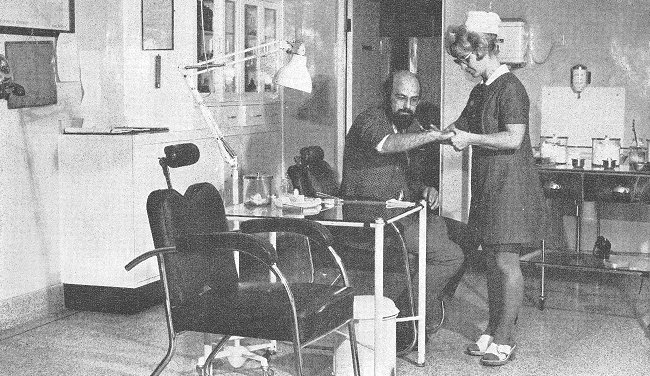
Sister Chin treating a patient in
the men's general surgery. |
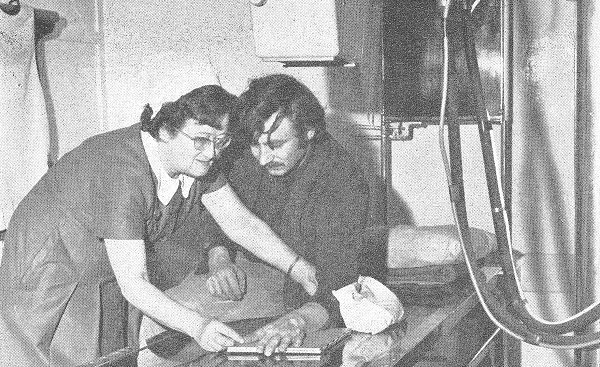 |
Sister Powell prepares a
patient for an X-ray. |
Sister Powell applies eye
drops to a patient. |
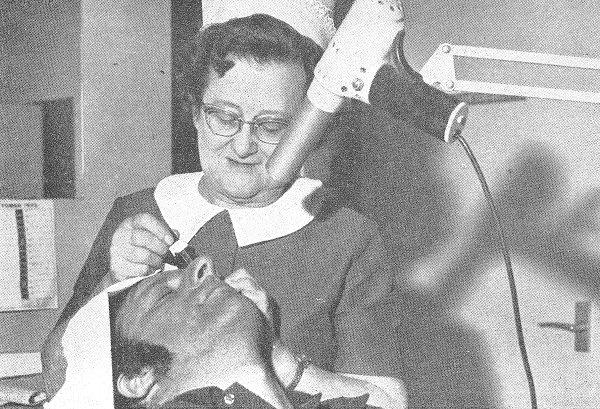 |
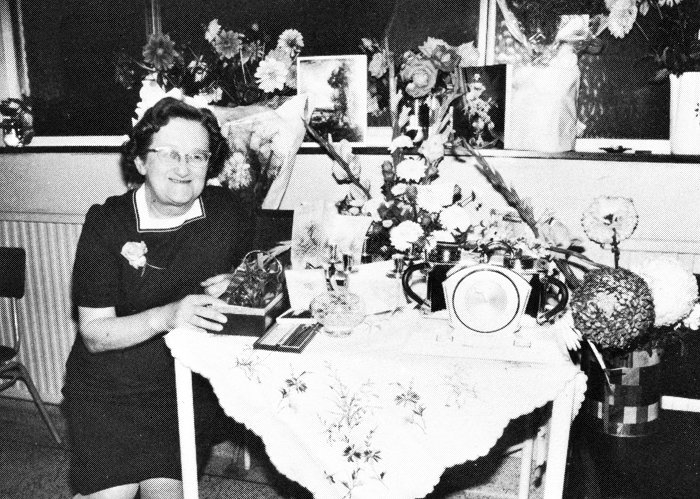
Sister Powell with her
retirement presents in 1974. From 'The Steel
Casting', courtesy of Wendy Marston. |
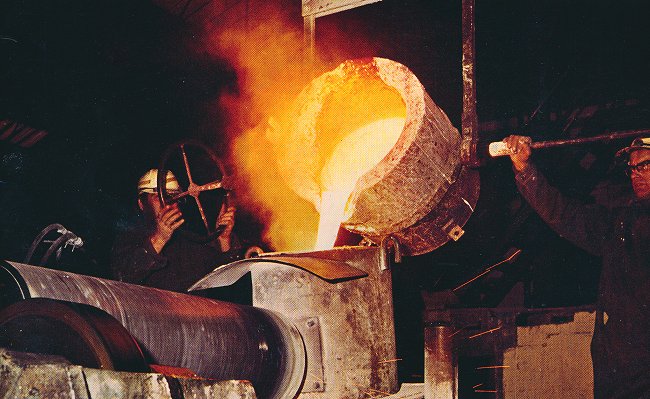
Casting a 'Supertherm' heat resisting steel alloy tube
at Lloyds (Burton) Limited. Part of an order worth
£100,000 for a Japanese company. |
A new company in the Lloyds group was created on 5th
April, 1971 as the result of a merger between two
members of the John Bagnall sub-group. It was called
Lloyds (Brierley Hill) Limited and came about when The
British Tayco Chain Company Limited merged with W. G.
Electrical Welding & Engineering Company Limited. Tayco
steel chain cable had been made for many years, but
production ceased due to lack of demand. The new company
would concentrate on the production of 'Blaco' stud
steel chain cable, and open link chain, suitable for
marine moorings, heavy industrial slings, and railway
couplings. |
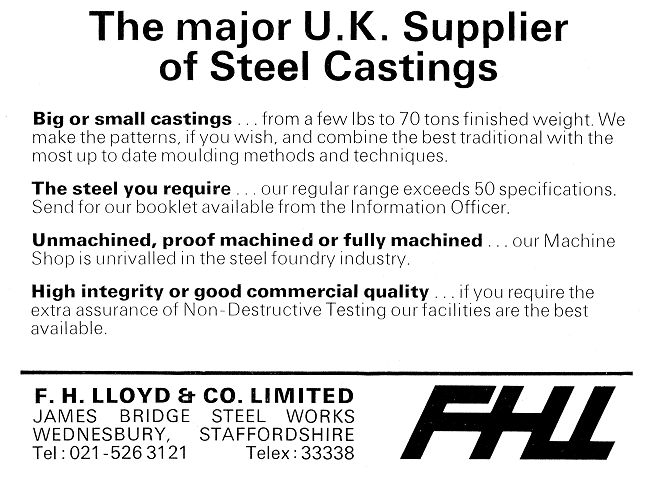
An advert from 1974. |
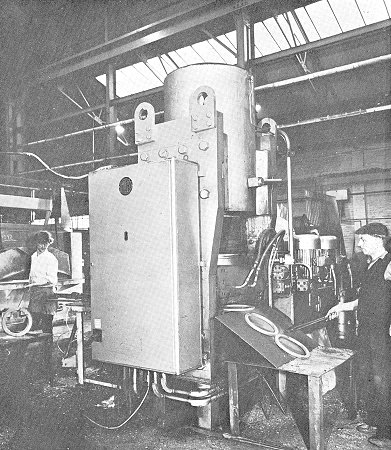
The 500 ton hydraulic press
installed at Brierley Hill to produce engine-starter
rings for commercial vehicles. |
A new plant was installed at
Brierley Hill to produce commercial vehicle starter
rings.
Around 22,000 rings could be
produced per week. 15 percent of them were fully
machined, gear cut, and induction hardened. |
In 1973 orders included a number of turbine
castings for the CEGBs 500MW Ince power station at
Ellesmere port. The order for £118,000 of castings
included a pair of intermediate pressure outer
casings and three pairs of lower pressure casings.
In 1972 the Directors decided to restructure the
company to bring about more effective coordination
of marketing programmes, production techniques,
research technology, and to improve inter-company
communications. In order to achieve this the
companies were grouped into three divisions;
engineering, foundry, and steel. The restructuring
was announced in December 1972 by Mr. M. C. Lloyd.
|
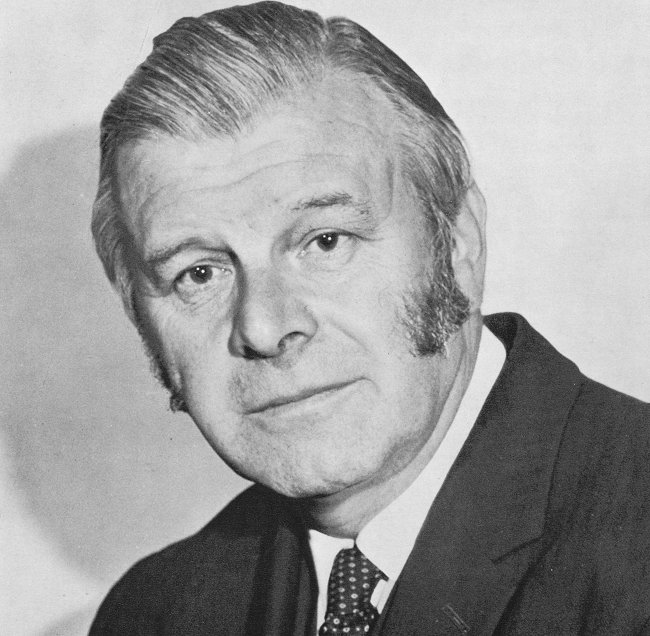
Mr. Michael Charles Lloyd,
1909 to 1973. From 'The Steel Casting', courtesy of
Wendy Marston. |
Michael Charles Lloyd – A Tribute. From
the 'Steel Casting' February, 1973.
Michael Charles
Lloyd was a man whose objective was to
serve his community, his business and
his industry to the best of his
abilities. That he served well will be
immediately acknowledged by all who knew
him. Such acknowledgement perhaps
provides an epitaph which he would have
considered fitting.
He succeeded his
brother Frank as Chairman of F. H. Lloyd
Holdings Limited in 1971. From the date
of his appointment he was concerned to
reinforce the executive management of
the Group and to provide for succession
of management against the time, in 1975
when he was due to retire. He
relinquished the position of Group
Managing Director and set up a Group
Executive Committee to undertake the
functions of corporate planning, policy
initiative and co-ordination of company
activities.
Under Mr. Lloyd's
Chairmanship, this Committee has made
substantial progress in streamlining and
re-organising the F. H. Lloyd Group,
particularly in re-structuring its 21
operating companies into three main
Divisions: Foundry, Steel and
Engineering. This restructuring marks a
watershed in the development of the
Group, and Michael Lloyd's role in
bringing it about was central.
His contribution to
industry in general and to the steel
foundry industry in particular, was
considerable. Over the years he held
various offices with the Steel Castings
Research and Trade Association, was a
member of the Council of the Production
Engineering Research Association and a
member of the Council of the
Confederation of British Industry.
Appointments of this kind were important
to Michael Lloyd only in terms of the
contribution he could make: he was never
a man to accept a position for the
status such acceptance might provide.
Where he felt he knew his subject well
enough to enter into public debate he
did so with a vigour and clarity of
expression that made his a voice to be
listened to.
His work in this
area was recognised in 1960 when he
became a Member of the Order of the
British Empire, specifically for work on
the Midlands Industrial Advisory
Committee to the Chairman of NEDDY. At
his home in Hilton House, Bridgnorth,
Shropshire, he lived a quiet family life
with his wife Priscilla Mary, son Dan
and daughter Penelope. His other
daughter, Charlotte lives in South
Africa.
The grounds of
Hilton House contain one of the two most
important (after his family) of his
non-business interests, the Hilton
Valley Railway, famous among miniature
railway enthusiasts both in this country
and abroad. This railway gave, as it
continues to give pleasure to thousands
of visitors, many of whom were driven by
Mr. Lloyd. He was the drive behind the
success of the railway and the proceeds
of that success were invariably donated
to local charities. The railway,
however. was a hobby: the part he played
as a member of the congregation at
Worfield Parish Church was the bedrock
of his life. He was organist at the
Church for many years, and a good one.
It can truly be said that he was a
pillar of the church and his community.
Mr. Lloyd was born
in Wolverhampton on August 6th 1909. He
was educated at Lambrook Preparatory
School, at Charterhouse School and at
Birmingham University. His life was long
and full; his death was tragic and
premature. |
|
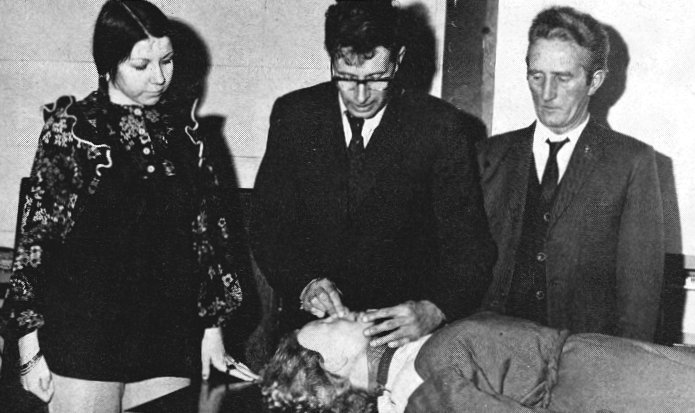
Members of the first first aid
course. Left to right: Lynne Marsh, Buying Dept; Dr.
Lester, and Jack Casey, Pattern Shop. From 'The
Steel Casting', courtesy of Wendy Marston. |
First Aid Course
After discussions
in the Management/Joint Works Committee
a first aid course was arranged by the
company for employees wishing to qualify
for a first aid certificate. Thirty
employees started the course on
Wednesday, 21st February, 1973, and 23
completed the course and took the
examination in April, which they all
passed, and received a certificate from
the St. John Ambulance Association.
The course
consisted of eight, two-hour lectures
with two one hour revision sessions. Dr.
J. P. Lester gave six lectures on the
theory of first aid which included the
principles and practice of first aid
structure and the functions of the body,
resuscitation, shock, injury to bones,
poisoning and the nervous system.
There were eight
practical sessions given by two of the
employees, George Sterry of the
Inspection Department and Jack Casey of
the pattern shop. George is divisional
superintendent of the Coseley and
Bilston Brigade and Jack Casey is a
qualified instructor. The practical
instruction consisted of the method of
bandaging various injuries from a
fractured spine to minor bleeding,
resuscitation, control of bleeding,
transporting injured persons, and
general welfare of the patient.
The names of first-aiders
were posted in each department so that
they could be called on in emergencies. |
|
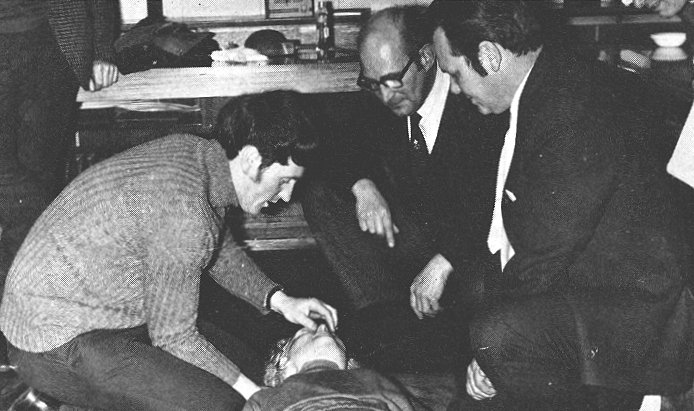
George Sterry, centre,
instructing Ken Liddington, left, from the Drawing
Office, on resuscitation, with Harry Bowdler looking
on. From 'The Steel Casting', courtesy of Wendy
Marston. |
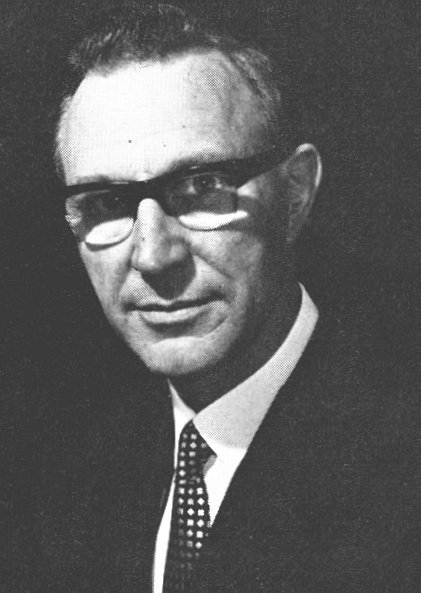 |
Mr. D. L. Carrier who
became Chairman of F. H. Lloyd Holdings Limited
after the death of Mr. M. C. Lloyd.
From 'The Steel Casting',
courtesy of Wendy Marston. |
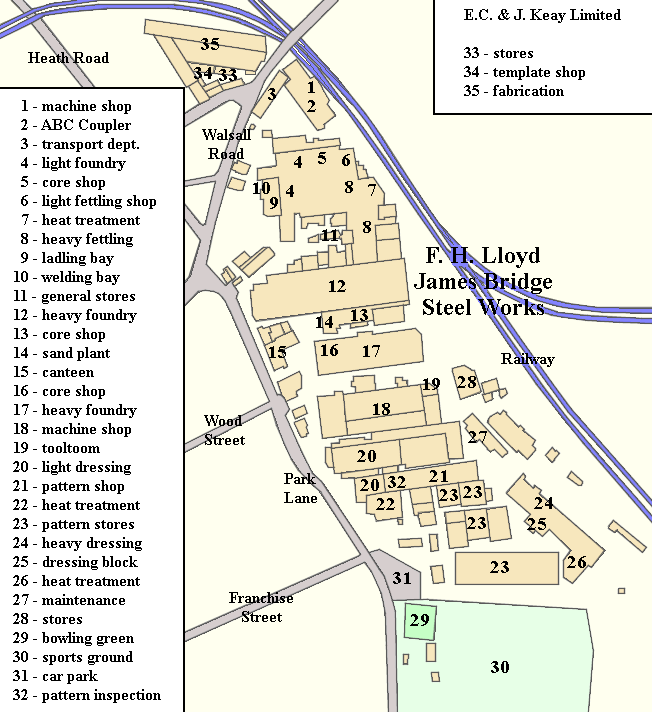
A plan of the Wednesbury site in November
1972.
In 1971 a trial
order worth £18,000 was placed by Brown Boveri for two
turbine castings weighing ten tons each.
The photo on the right shows the
turbine pattern being inspected for Brown Boveri. |
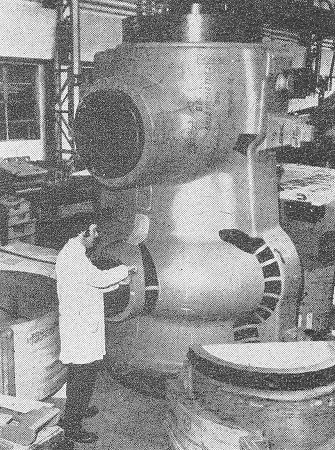 |
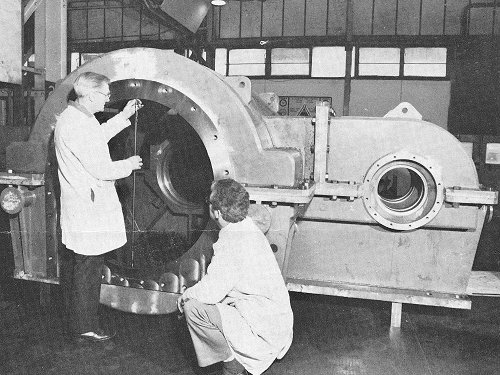 |
Inspecting a turbine gear
housing produced at Lloyds for 43,000 ton bulk
ocean-going carriers that were built in Australia.
The unit would house an epicyclic
gear train that carried power from a gas turbine to the
propeller. |
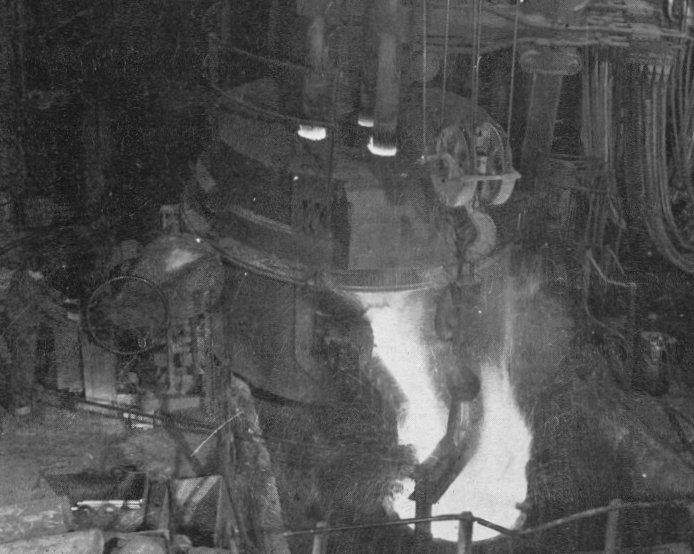
Tapping a ten ton furnace. Courtesy of Wendy Marston. |
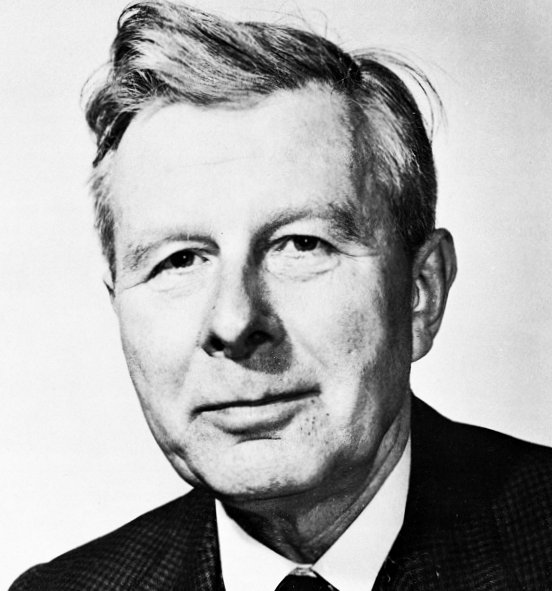 |
Mr. Francis Nelson
Lloyd, 1907 to 1974.
From 'The Steel
Casting', courtesy of Wendy Marston. |
A tribute to Mr. F
.N. Lloyd
Mr. Francis
Nelson Lloyd, former Group Chairman
and Managing Director, died at his
home in Tettenhall, Wolverhampton,
after a period of uncertain health,
on 27th June, 1974, at the age of
66. He retired at the end of 1971,
and so only had a short retirement.
Mr. F. N. Lloyd
was born on 13th August, 1907 and
educated at Charterhouse, and
Trinity College, Oxford. He was a
grandson of Francis Henry Lloyd, the
founder of the company, which he
joined in 1929, becoming a director
in September 1931 and Managing
Director in November 1941 on the
death of Mr. F. J. Hemming. In June
1949 he became Chairman and held
that office until he resigned on
account of ill-health in September
1970.
At the outbreak
of the Second World War he joined
the R.A.O.C. but was soon recalled,
as his presence at the factory was
considered essential to the vital
part which FHL played in the
country's war effort. Towards the
end of the war the company provided
the management and technical knowhow
to operate the new Ministry Steel
Foundry at Burton-on-Trent. Shortly
afterwards F. H. Lloyd acquired that
Foundry and formed it into Lloyds
(Burton) Limited, the firm’s first
subsidiary company and the beginning
of the F. H. Lloyd Group.
In addition to
his involvement with the Lloyd
Group, Mr. Lloyd was a director of
N. Hingley & Sons from June 1953 and
became chairman of that Group in
January 1959. He was instrumental in
the merging of the Lloyd and Hingley
Groups in July 1966. He was a
director of Lloyds Bank from 1956
and also served on its Birmingham
Committee. He was also a member of
the Management Board of the West
Midlands Engineering Employers'
Association from 1941 until 1971
being President in 1964 and 1965.
Throughout his
career Mr. Lloyd was a leading
member of the Steel Founding
Industry and its representative
associations. He became associated
with the General Steel Casting
Association in the late 1930s when
he served on its Council and was a
member of the Townsend Committee. He
became a member of the Council of
the British Steel Founders'
Association on the formation of that
body, and held office virtually
without interruption until the
B.S.F.A. was wound up in 1967
becoming chairman of the Steel
Castings Association on its
formation in that year. Mr. Lloyd
was the first chairman of the
British Steel Castings Research
Association in 1953 and was largely
responsible for effecting the merger
of B.S.C.R.A. with S.C.A. in 1968
when S.C.R.A.T.A. was formed, and
again he became its first chairman.
He was awarded
the CBE in 1970 for his services to
exports. More recently, in 1973, he
was honoured by the foundry industry
when he was awarded the E. J. Fox
medal by the Institute of British
Foundrymen. |
|
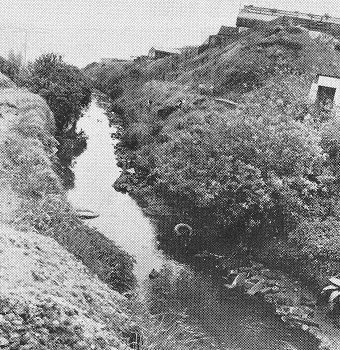 |
|
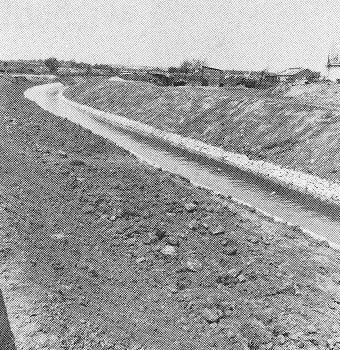 |
In 1975
the Severn Trent River Authority decided to
carry out work on the nearby River Tame which
had long been known for flooding, particularly
at the Railway Tavern pub which was sometimes
three feet deep in water. The river was used by
F. H. Lloyd as a source of water for the cooling
and process plant. The work involved
straightening the river and deepening the river
bed. The company decided to to carry out some
work on the river while the alterations were
taking place. A large diameter pipe was
installed from the river to the work's pumping
plant to ensure an adequate supply of water.
When the work was completed, the river was
expected to flood only once every fifty years.
The photographs show the river before and after
the work had been completed. |
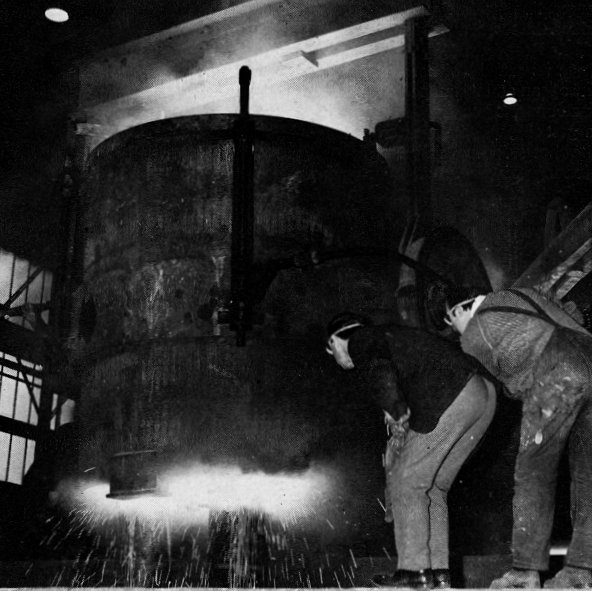
Teeming a
multi-ladle job in the Heavy Foundry,
the largest foundry bay in the country.
From 'The Steel Casting', courtesy of
Wendy Marston. |
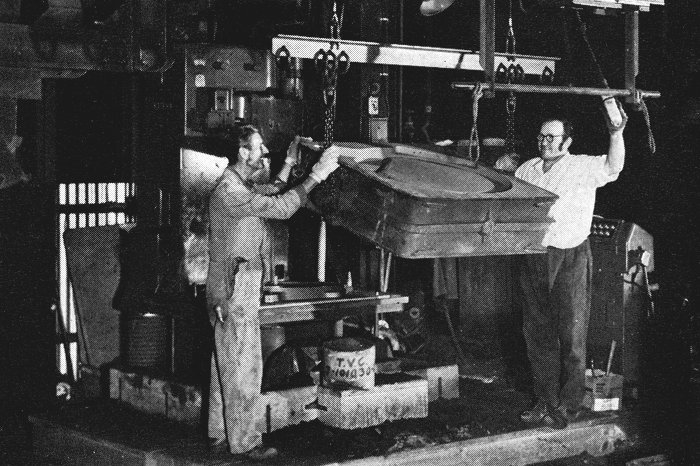
One of the latest
type of squeeze-jolt moulding machines
at work in the foundry. From 'The Steel
Casting', courtesy of Wendy Marston. |
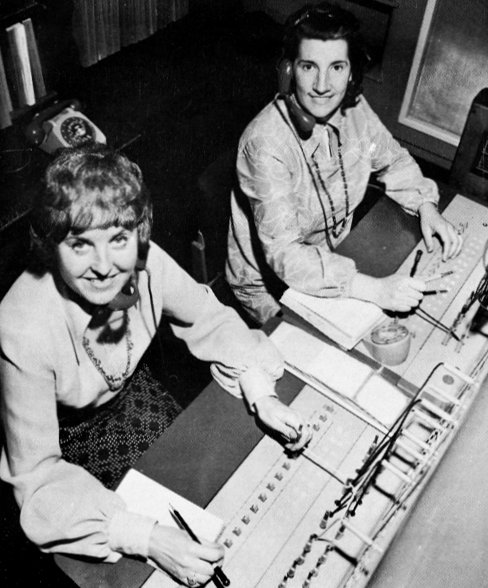 |
The FHL
switchboard ladies, Dot Davies and Ruby
Johnson.
Dot joined the firm in 1959, and Ruby
joined in 1972.
In 1974 they
moved into a new a new switchboard room
containing some of the latest equipment.
Every year they handled about 200,000
incoming and outgoing calls.
From 'The Steel
Casting', courtesy of Wendy Marston. |
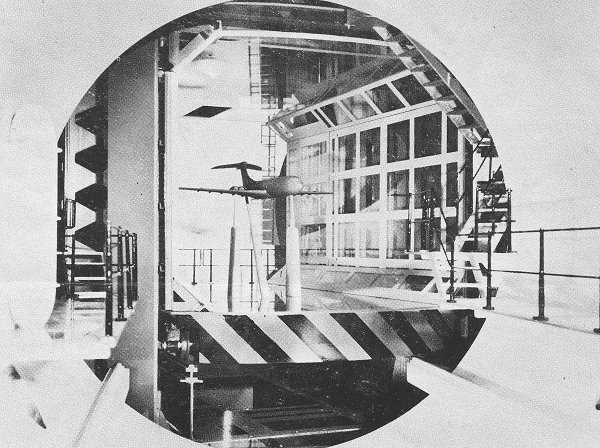
F. H. Lloyd undertook
an unusual and interesting casting job in
1975 for R.A.E. Farnborough. It involved the
production and machining of two large
castings for a low speed wind tunnel. The
two castings, one 22 ft. long, the other 10
ft. long, formed a massive arc upon which
the model aircraft could be mounted within
the tunnel. |
|
The exploration for North Sea
oil involved the building of large oil rigs, each with
27 wellhead assemblies, all needing large valve
castings. Each assembly was 17 ft. high and had three
heads, all of which had to be cast and machined.
In 1975 F. H. Lloyd received an
order for castings for 54 wellhead assemblies for use in
the Forties Field, consisting of nearly 180 tons
of castings.
|
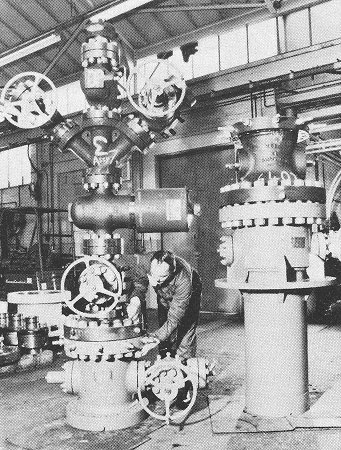 |
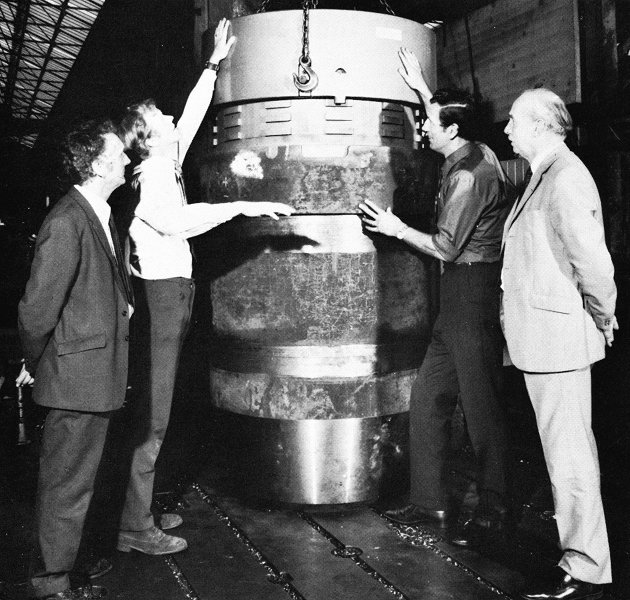
F. H. Lloyds received many
orders from the North Sea Oil companies including
the breach locks that locked together the 70 ft.
sections to form the oil platform legs. The
photograph above shows the final inspection of a
breach block connector and chaser head by the Chief
Inspector of McEvoy Oilfield Equipment Limited. From
'The Steel Casting', courtesy of Wendy Marston. |
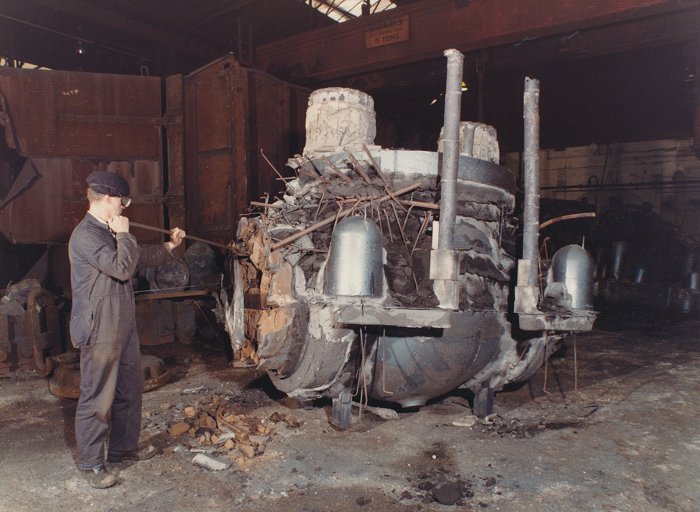
A large valve body casting
after being 'knocked-out' from the mould. Courtesy of Wendy Marston. |
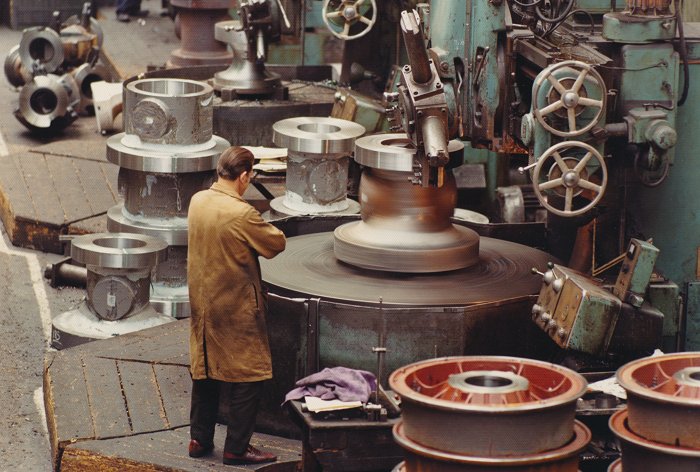
Valve castings for the oil
industry being machined. Courtesy of Wendy Marston. |
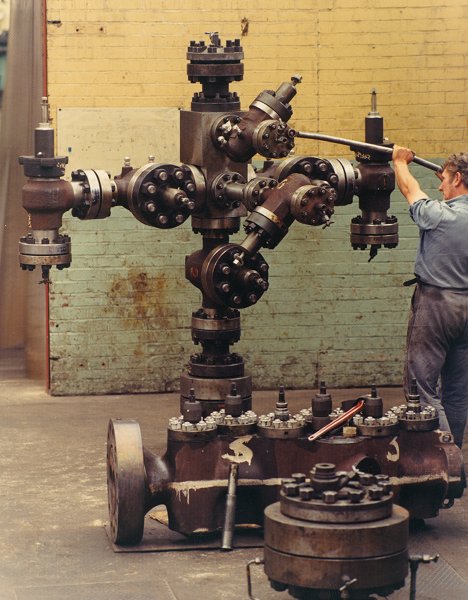 |
One of the North
Sea oil field valve arrangements being
assembled. Courtesy of Wendy Marston. |

Some of the castings for
excavators that were produced at James Bridge
for Ruston-Bucyrus Limited, one of Lloyd's
largest customers. Courtesy of Wendy Marston. |
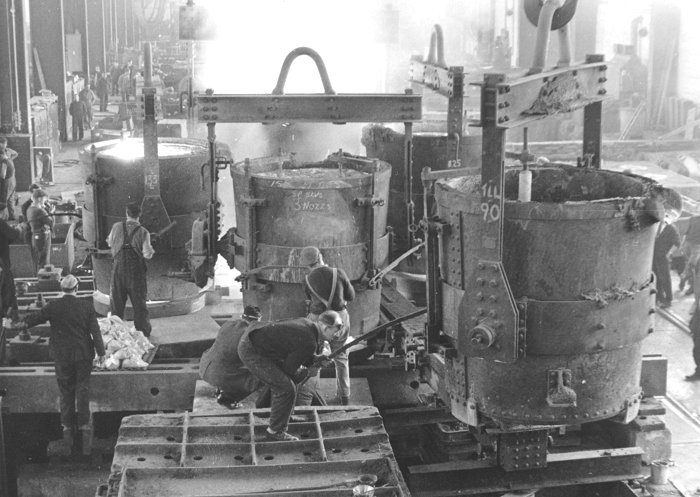
Hard at work on a
multi-ladle casting job in the foundry. Courtesy
of Wendy Marston. |
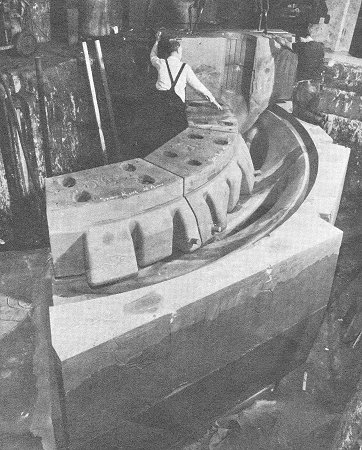
A giant mould for a Dinorwic
Casting. |
F. H. Lloyd supplied many huge
castings for electricity power stations throughout the
world, and made it possible to build some of the largest
power generation units.
One project that relied heavily on Lloyd's castings was
the building of Dinorwic Power Station in North Wales.
|
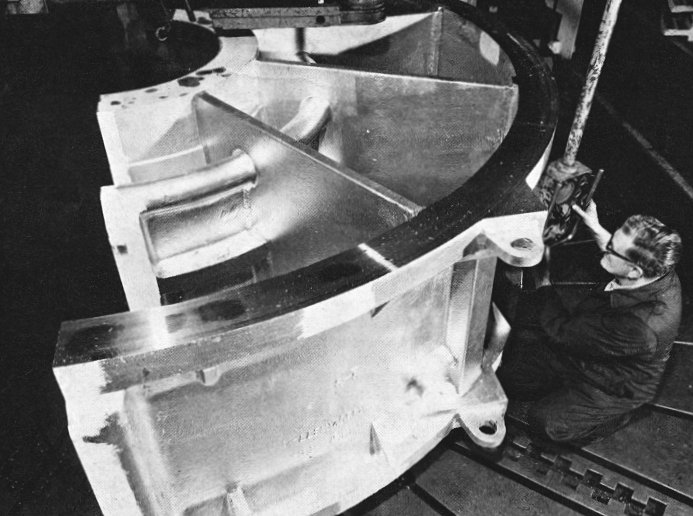
The top half of a GEC 50MW gas
turbine main casing. From 'The Steel Casting',
courtesy of Wendy Marston. |
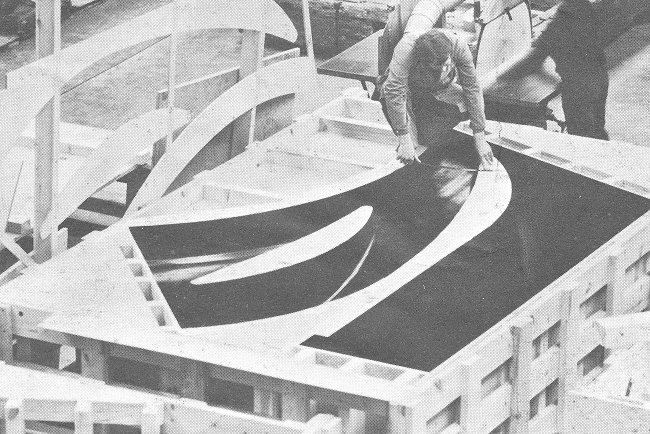
A patternmaker at work on the corebox for
a stayring for Dinorwic Power Station.
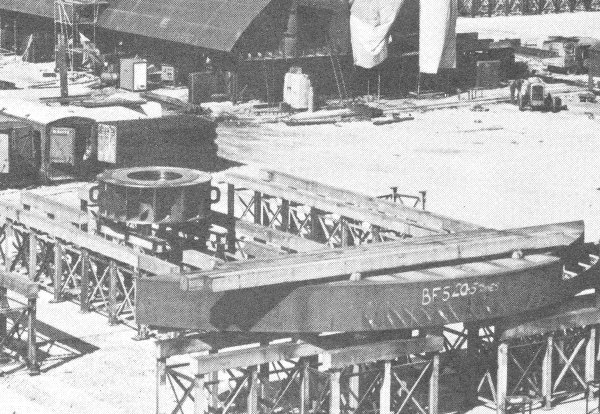
One of the eight massive pivot
bearing castings that were produced by Lloyds for the
Thames Barrier, each weighing nearly 54 tons, with a
diameter of 16 feet. The company produced many castings
for the project including the steel barriers which alone
amounted to castings of over 1,000 tons. |
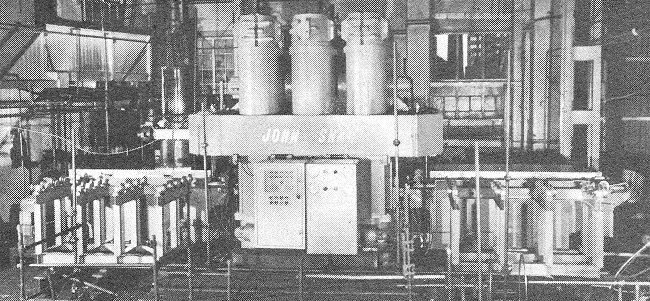
This 71,400 ton rubber die press
built by John Shaw & Sons (Salford) Limited, included
three large castings for the main press head and three
cylinder base castings, all of which were produced by F. H.
Lloyd. In total the castings weighed 61½
tons. |
A gigantic gear wheel cast by
Lloyds for a cement plant ball mill in Brazil. It had a
diameter of 18 feet and a depth of 2 ft. 6 inches. It
weighed 32 tons. |
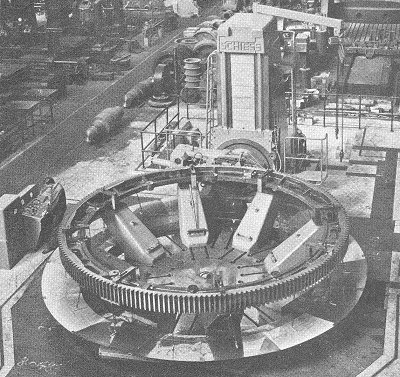 |
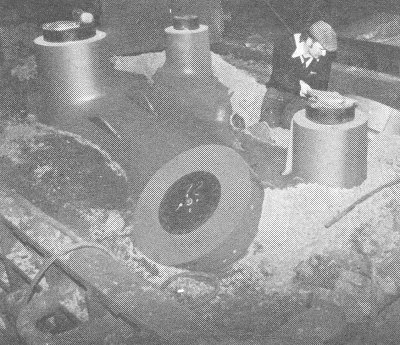 |
Producing the mould for one of
a series of castings made for Canadian power stations.
In the mid 1970s, Lloyds received orders for over 890
tons of such castings from Canada.
Similar castings were made for
power stations in New Zealand, South Africa, and India. |
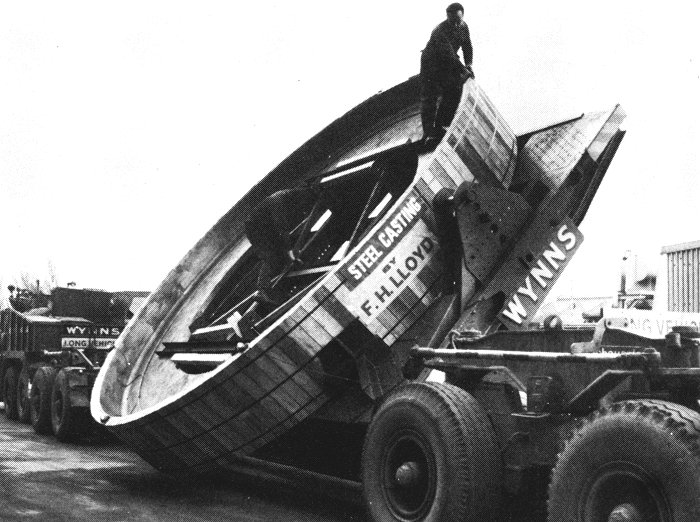
The largest cast steel ring
made at James Bridge, left the factory in 1975 to
make its way to Stockton-on-Tees. It was over 18
feet in diameter, weighed over 20 tons, and was
carried on a special tilting trailer, designed for
the purpose. From 'The Steel Casting', courtesy of
Wendy Marston. |
Lloyds were a major supplier of steel castings to
the large armaments industry, including over one
thousand castings for Chieftain tank turrets. Another,
and very different product produced by the Lloyd Group
was cast steel chain for giant draglines using a
specially developed system of patternmaking, which
resulted in interlocking moulds. The steel could be
poured virtually simultaneously for each link so that
the whole length of chain is cast from the same ladle of
molten steel. Lloyds were one of only a handful of
manufacturers in the world, capable of producing chain
of such a high quality. |
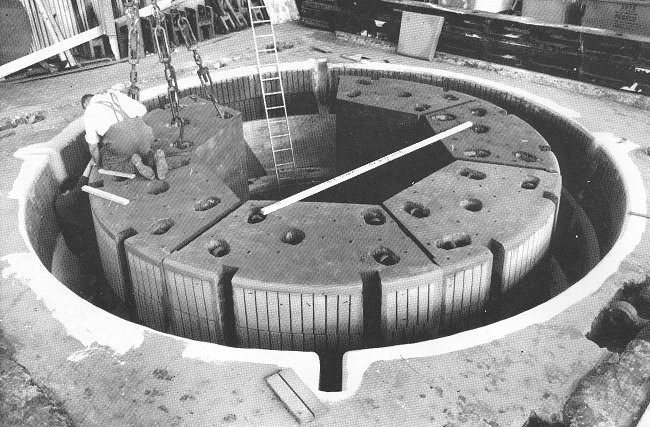
Preparing a mould for a tyre for a
cement kiln, for Head Wrightson Limited,
Stockton-on-Tees. Four tyres were produced and fully
machined, along with one bevel, three straight sides.
Each tyre casting weighed over 96 tons. |
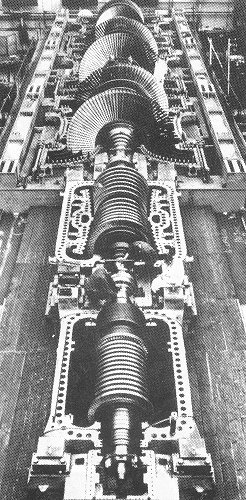 |
Part of the Drax 'B' power
station built by C. A. Parsons Limited,
Newcastle-on-Tyne. F. H.
Lloyd produced the low pressure castings for thee such
turbines, six for each machine. The total weight of six
castings was 214 tons. |
In 1976 Mr. D. C. Lloyd
became Sales Manager at F. H. Lloyd & Company
Limited. His responsibilities included developing
the ever important export market.
From 'The Steel Casting',
courtesy of Wendy Marston. |
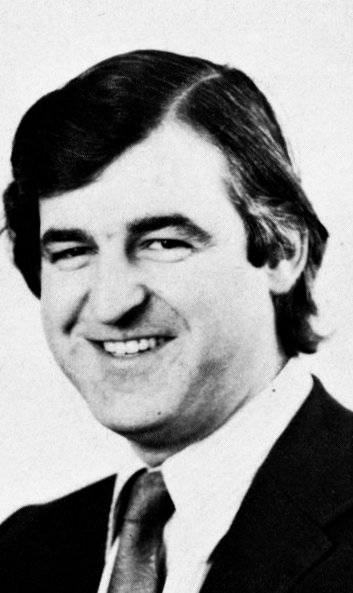 |
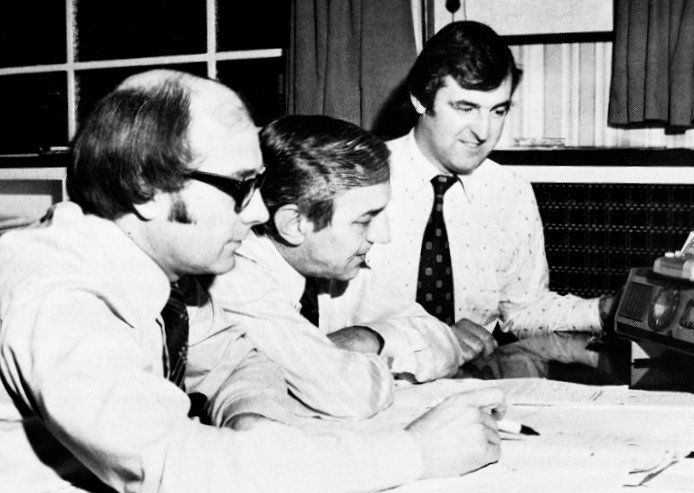
The team in the Sales
Office. Left to right: Terry Gaden, Keith Lort.
and Dan Lloyd. From 'The Steel Casting',
courtesy of Wendy Marston. |
In 1977 a
reorganisation scheme began at James Bridge
to create larger production areas, improve
the overall efficiency of the plant, and
provide better working conditions.
Improvements were made to the Sand
Preparation Plants, and a new sand slinger
rollover circuit was introduced in the Heavy
Foundry.
A new melting plant
with a £250,000 electric furnace was
installed, and the Pattern Shop was moved to
Keay's old building in Station Street. In
order to ease the movement of patterns from
the new stores to the main foundry area, the
old railway line which ran under the Walsall
Road was converted into a private roadway.
The old Pattern Shop became an additional
fettling area providing an additional 24,000
sq. ft. to the existing facility. Similarly
the Scrap Stores was moved from the Heavy
Foundry Bay to increase the working area. |
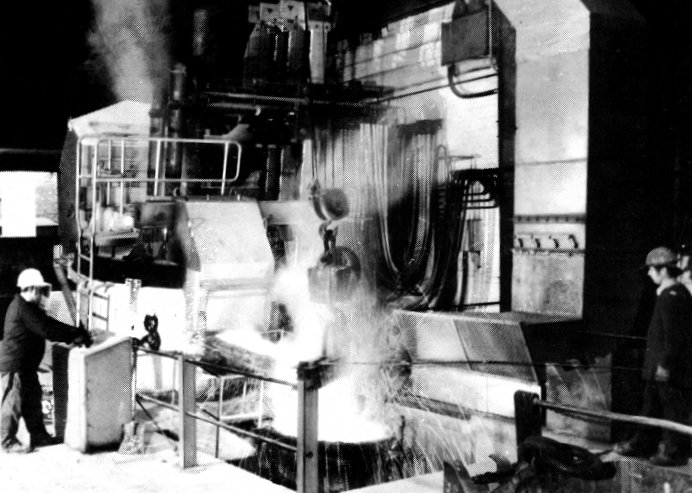
The new melting
plant. From 'The Steel Casting',
courtesy of Wendy Marston. |
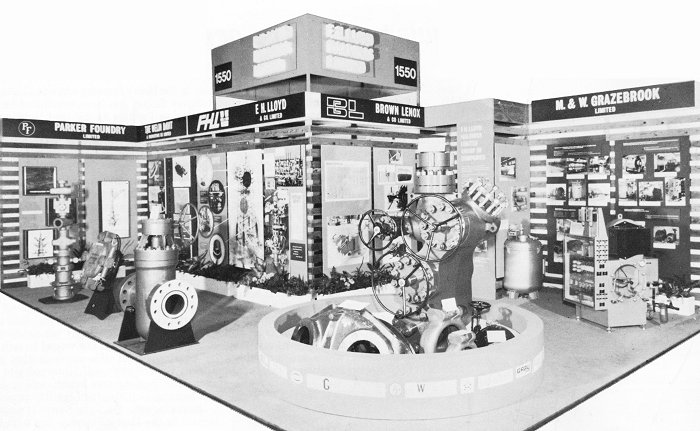
The company's stand at
the Offshore International Exhibition.
Lloyds hoped to increase the number of
ever-important orders for castings from the
offshore oil industry. From 'The Steel
Casting', courtesy of Wendy Marston. |
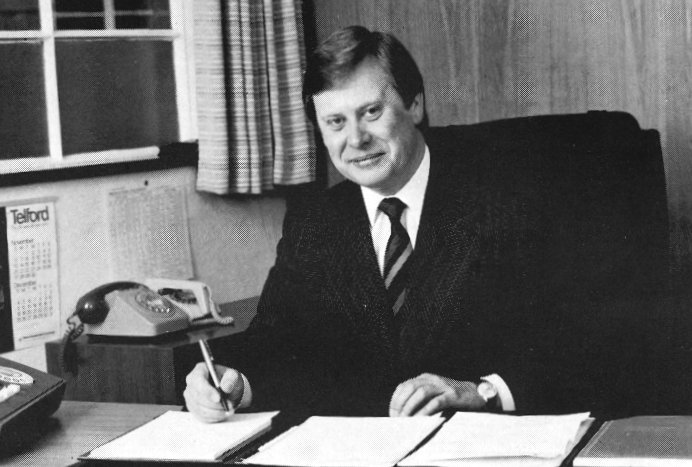
The new Managing
Director of F. H. Lloyd & Company Limited,
appointed in 1977 was Allan Harris who had
joined the company as an apprentice in 1953.
From 'The Steel Casting', courtesy of Wendy
Marston. |
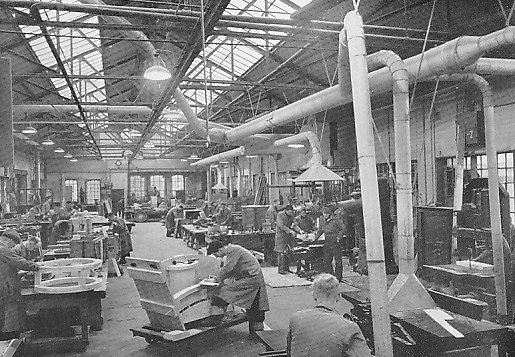
The pattern shop. |
F. H. Lloyd & Company had the largest steel foundry
business in Europe, but it fell into a severe decline in
the 1980s, which resulted in the closure of the
Wednesbury foundry in 1982.The Parker Foundry Limited
at Derby survived until 1987 leaving Lloyds (Burton)
Limited as the sole survivor.
|
Shortly before the closure of
The Parker Foundry Limited, F. H. Lloyd was acquired
by Triplex plc to form Triplex Lloyd plc.
Although Lloyds (Burton) Limited was trading
profitably, it became irrelevant to Triplex Lloyd
which had other plans for the future. It was sold in
1989 to William Cook plc. At the time it was the
second largest producer of steel castings in the
country. |
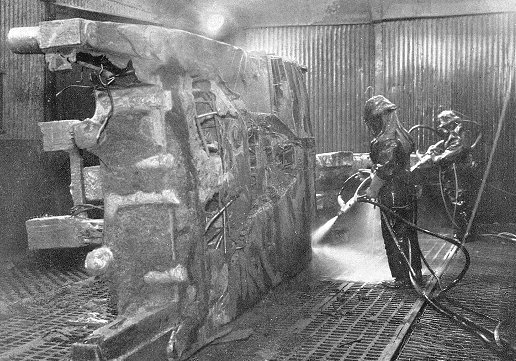
Using the hydroblast system to clean steel
castings. |
F. H. Lloyd Holdings Limited became part of United
Engineering Steels Limited, and the James Bridge site
became F. H. Lloyd Engineering Steels Limited, producing
a range of cast and rolled billets for other companies
in the group. In the 1989 Annual Report, the Directors
of United Engineering Steels Limited announced the
closure of the James Bridge site and the relocation of
its activities to the company's plants in South
Yorkshire. This must have come a terrible shock to the
loyal James Bridge workforce, who had worked hard and
achieved so much for the company. This was a sad loss
for the steel industry, particularly in the West
Midlands. |
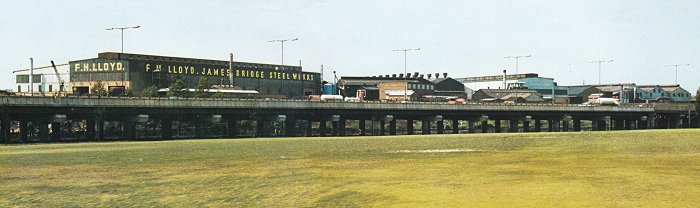
A final view of the James
Bridge factory, seen from across the motorway.
Courtesy of Wendy Marston. |
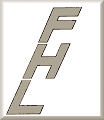 |
|
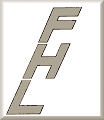 |
|
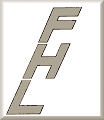 |
Return to
the 1960s |
|
Return to
the contents |
|
Proceed to
personalities |
|