Combine
Harvester Cabs, and The Fight Against 'Harvest Lung'
By 1970, our farm machinery dealers were
starting to ask us to develop cabs for combine harvesters. Initially
demand was to prevent drivers being catapulted into the auger should
the reel dig into the soil, particularly when working downhill, often stopping the combine dead in its tracks.
Surprisingly, working
on a combine at night during the autumn could be quite cold
especially with a wind blowing, farmers wanted a cab with a heater
to keep them warm in these conditions.
|
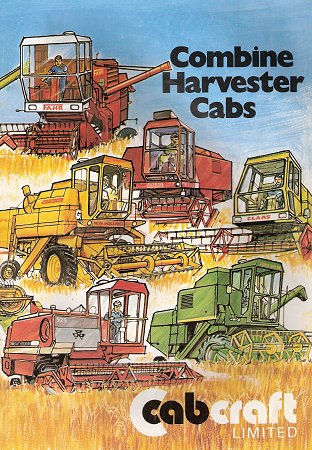 |
We sold a lot of cabs in N.E.
Scotland, as up there they often harvest spring sown malting barley
and oats in zero temperatures, in the late autumn/early winter often
with snow on the ground.
Drivers needed a warm working environment
to avoid hypothermia setting in! This proved quite a challenge as
the combines all had flimsy driving platforms and grain tank walls
quite unsuitable for taking the extra weight of a half ton cab.
Nevertheless, we felt combine cabs could be a growth sector and
commenced designing and developing cabs for most makes and models of
combines, new and old. This required strengthening and sound/dust
insulating the harvesters very substantially and the provision of
detailed illustrated fitting instructions. At this time, I also
recognised the need for specialist help in promoting this wonderful
business opportunity to generate a very strong demand needed to
cover our substantial development costs. My son John Barker was
running a technical Marketing Consultancy company at the time and
provided valuable guidance on providing potential market size,
export opportunities and effective sales promotion. His team also
produced some very effective brochures. |
We advertised the product heavily in the farming
press and sales soon took off in a substantial way,
after two years we had over 30 cab variations to suit
most combine harvesters.
Export enquiries were received and distribution
networks formed in several North European countries. We
soon received demands for improved visibility to the
ends of the cutting reel. My earlier work in steel
rolling mills enabled me to develop intricate section
cold rolled tube to enable very slim corner glazing
pillars to be utilised. This improved the annoying
blindspot areas down from 26cms to just under 4cms. |
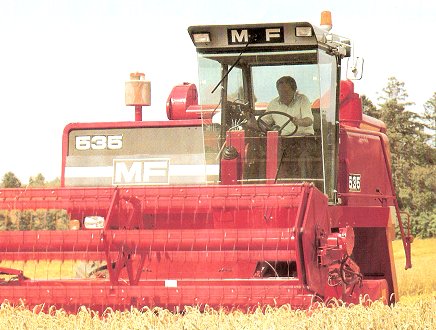 |
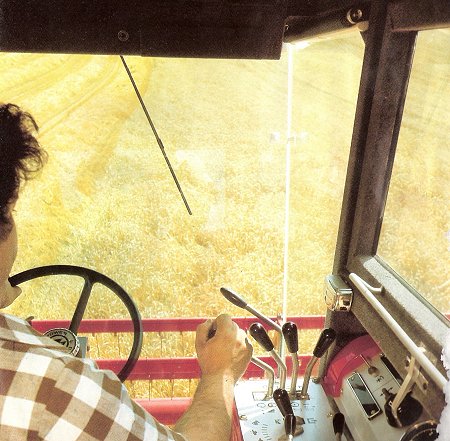 |
The safety glass windows were glued into the
rolled-in glazing indents on the vertical tubes
eliminating sheet metal cladding and rubber glazing
mounts, a huge and very popular step forward for our
customers. The investment in the rolls to form these
unusual patented section tubes was very substantial but
was soon recovered as demand for the new 'full vision'
cabs took off. As time progressed, we produced a more
advanced design with the first glass to glass front
corner joints for Massey Ferguson and New Holland
combines to reduce the blind spot to only 1cm.
High strength adhesives held together three very
large sheets of toughened or laminated glass, with only
four small brackets at the top and bottom to
provide back-up security. |
This technology is still in use today, 30 years on.
Now they even use curved corners to provide zero blind
spots! In the early 70's, Sheffield Hospital's Dr. Darke, a
consultant specialising in industrial respiratory diseases, was becoming increasingly concerned by the poor lung condition of
many retired farmers and farm workers. He discovered that tiny
microscopic fungal spores often present on maturing cereal crops in
damp weather conditions were being inhaled by combine harvester
drivers at harvest time. He had noted our advertising campaign for
combine cabs in 'Farmer's Weekly' and wanted to know if we could
develop combine cabs with air conditioning systems capable of
preventing these spores being sucked into the cab.
Commercial air
conditioning units were unsuitable for off road vehicles at the
time, so we worked with our cooling fan supplier Temperate
Filtration to develop a cab roof mounted unit with filters which
would prevent spores down to 1 micron from entering. Within 6-months
an electrically powered forced air cab ventilator with a combination
of water mist chambers and filters was developed to supply cool
cleaned air to the operator. Dr. Darke was very pleased with the
test results and agreed to promote the health improvement benefits
of the product in the farming press to overcome this major health
hazard for those involved with cereal growing.
He sent out an
educational press release and we ran a series oh half page
advertisements in 'Farmers Weekly'. Our marketing Consultants
succeeded in persuading the TV farming programme to feature this
development. We had a full half hour programme made by Tyne Tees
Television who then syndicated it to all the Sunday Farming
programmes in other ITV regions. Dr Darke was interviewed, and I
gave interviews sat on top of one of our combine cabs.
As a result, the business grew strongly and expanded to
eventually generate some two thirds of our income.
All our cabs had our distinctive orange and black
logo on each side of the roof panel, and Doug Barker
(soon to be known as Mr. Cab-Craft) recalls many emotive
meetings at agricultural shows with farmer's wives who
had lost their husband to harvest lung and who wanted a
cab to prevent their sons from running the risk of a
similar early death. Later on, activated carbon filters
were introduced to provide even greater protection from
breathing-in chemical mist for self-propelled sprayer
operators. Enclosed helmets complete with battery
powered fans and filters were also developed by
competitors for combines and sprayers, but proved
unpopular with drivers due to their weight. |

A close-up view of the Sperry
New Holland 1500 series cab, clearly illustrating the
ultra-slim corner pillars and the double-skinned roof
arrangement. |
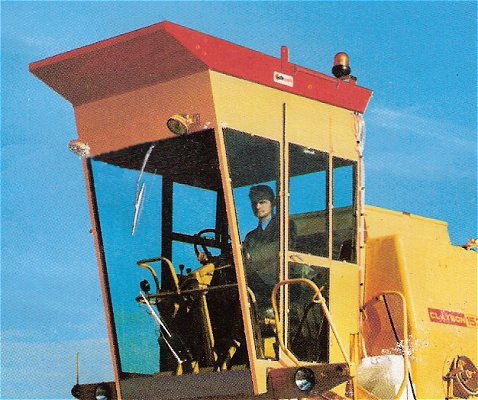 |
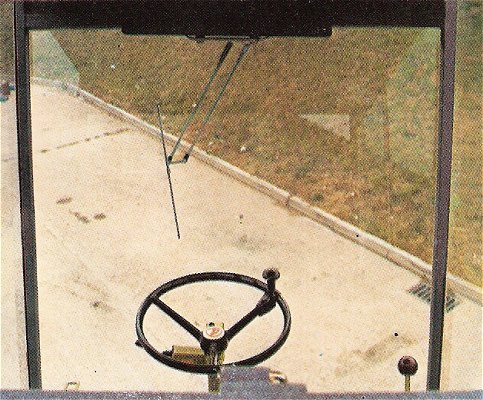 |
A view from inside the cab,
taken from the rear window, indicating the panoramic
visibility afforded by the method of glass fixation.
This view from the driving seat
(impractical to photograph), gives uninterrupted
visibility of reel and auger. |
The view from on top of the
cab roof illustrating the TF300 air filter/cooler
installed in the roof space of the de-luxe cab.
The access hatch is gas spring
assisted for easy opening and closure. |
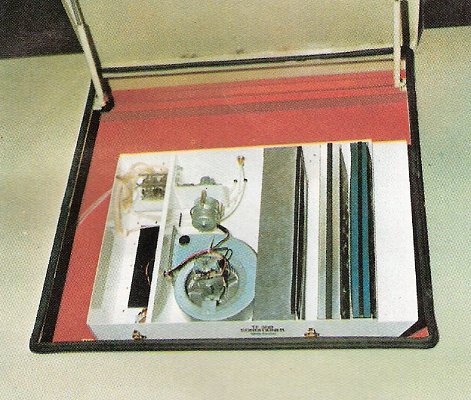 |
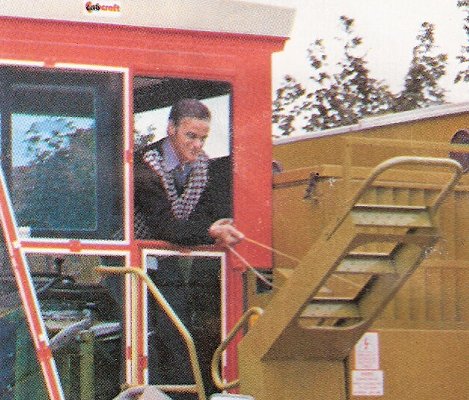 |
This photograph shows a
practical demonstration of the purpose of the two-part
‘stable’ type door. The
driver is shown lowering the raised footsteps to enable
him to leave the combine.
The alternative is a sliding
door which may not provide an adequate dust seal. |
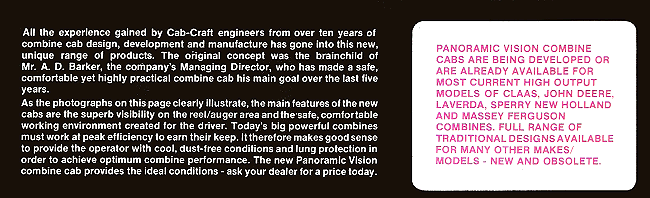
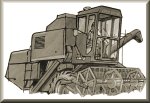 |
|
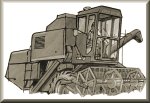 |
Return to the
previous page |
|
Proceed to Safety
and Quiet Cabs |
|