Tractor
Safety and Quiet Cabs
In the 1970s, Government legislated to make
safety cabs and roll bars mandatory for new tractors destined for
the U.K. market. In the run-up period, weather cab makers were
encouraged to produce safety cabs or roll bars for pre-existing
tractors. With an estimated 250,000 tractors requiring such
structures, we soon had a strong demand from hillside farming areas
where the risk of the tractor overturning was greatest. Hundreds of
Welsh and West of England hill farmers had been injured or killed
over the preceding decade.
Cab-Craft produced the first safety cab
for International Harvester tractor dealers in the late 1960s. The
frames were tested and approved for several livestock farmers I.H.
tractor models at the N.I.A.E. testing station at Silsoe,
Bedfordshire. The test involved a swinging pendulum weighing up to a
ton striking the cab frame bolted in situ on a tractor. The skill
came from anchoring the cab correctly to the rear axle. The cab
frame had to be fabricated with a frame designed to 'give' up to 12
degrees when struck by the swinging block. Too strong and the fixing
bolts would shear off, too weak and the frame would have too much
distortion.
In the early days, there were several trips to the test
station to finally get a cab passed. One of the first safety cabs we
produced went to a Welsh hill farmer in Newtown. Soon after
delivery, we had an urgent call from the dealer asking for a
replacement. Why? Their customer rolled his tractor 900 foot down a
hillside when the farm track collapsed under the wheel on the
downhill side. The tractor wheels flew off early in the rolling
period but the driver stayed in his seat as instructed on our label.
He was able to walk away from the wreck uninjured, but badly shaken
and went back to work the next day.
The insurance company agreed to
the immediate replacement of the tractor provided it was supplied
complete with a Cab-Craft safety cab. The farmer sent us a
thank you letter, complete with a picture from the local newspaper
with the headline 'Safety Cab saves Newtown farmer's life'. There
were many such anecdotes over the following years, but even today,
tractors overturning remain high on the list of farming fatalities.
|
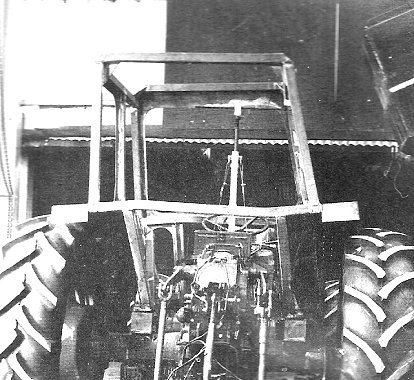 |
Five years on, the legislation was extended to cover
excess noise, and so the era of the safety quiet cab was
born.
This proved to be the biggest problem we ever had to
face. Placing a cab on a tractor not designed for a cab
resulted in often deafening noise levels at the driver's
ear as vibration and transmission tunnel noise was
amplified inside the cab.
To achieve the maximum 75 decibel test limit, not
only had the cab roof and walls to be well insulated,
but so had the mounting brackets, which had to be rubber
cushioned. All the tractor surfaces insulated.
Later, the maximum was reduced to 70 decibels. |
Today, tractor cabs have isolated flat floors. In
the beginning, to keep the height down for entering the
low doorways on the farm buildings in those days, we had
to fit thick moulded polyethylene over some very
intricate surfaces on the tractor below the seat. This
proved to be a huge headache for tractor makers like
Massey Ferguson in Coventry. They were making 80,000
tractors per year, but only selling 5,000 in the UK.
Cab-Craft negotiated a multi-million pound contract to
supply all UK models of their 40 and 60 hp. tractors
complete with safety quite cabs, including the supply
and fitting of the noise deadening material, and noise
testing each tractor within our own factory before
shipment to the dealer.
We rented a new factory in Shaw Lane, Wolverhampton
and set-up a dedicated production line for this
contract. Each week, lorry loads of tractors came from
Massey's Banner Lane plant along with lorry loads of
cabs from our Four Ashes factory to the Shaw Road
factory, where we employed 35 people for the fitting
operation. The contract was to last 3 years, until new
models were brought on stream, developed with an
integral quiet cab. It was at this time that Massey
ceased UK tractor manufacture, eventually transferring
all production to their factory in France. |
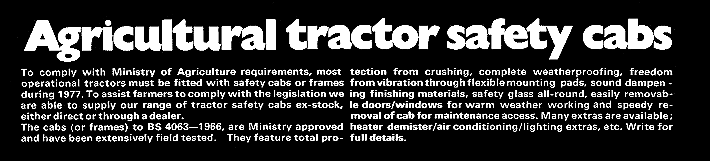
A Same Saturno 80. |
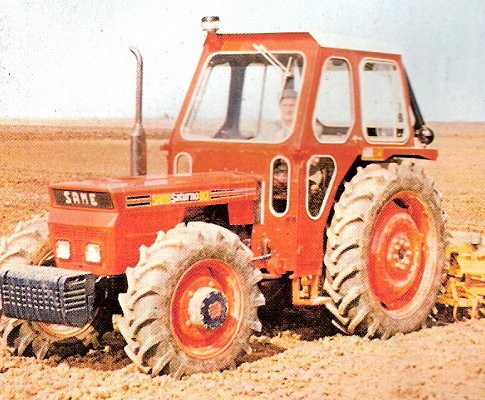 |
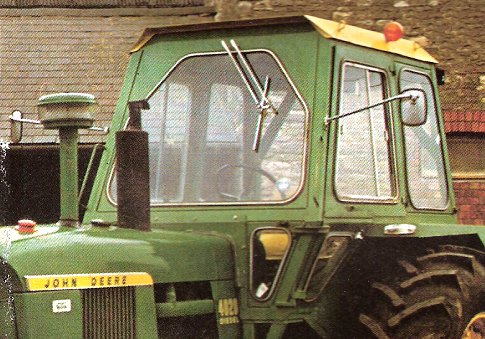 |
A John Deere 40/20. |
An International Harvester
434. |
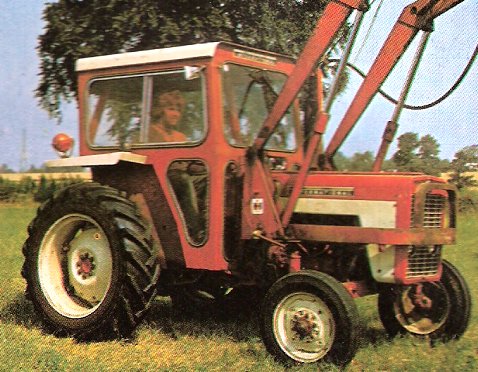 |
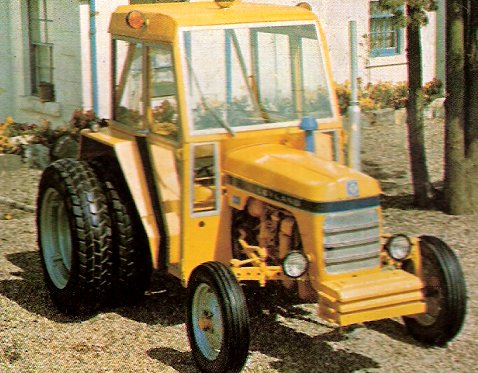 |
A British Leyland 154. |
A Massey Ferguson 1200. |
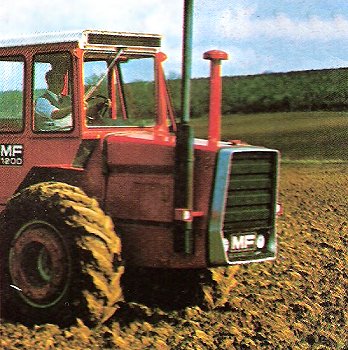 |
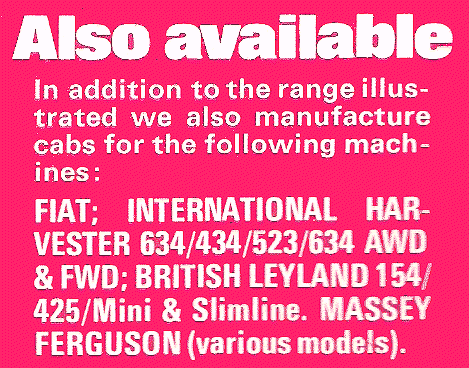
Fork Lift Truck
Cabs with Falling Object Roof Protection/ROPS
We enjoyed a substantial amount of business
making safety cabs for fork lift trucks. The safety legislation
introduced for these vehicles was called FOPS/ROPS (falling object
protective structures with roll over protection). We developed,
tested and made FOPS cabs for Coventry Climax, Henley, Lansing
Bagnall and others, with roof structures capable of protecting the
operator from death or injury when unstable loads dropped off the
raised forks whilst removing materials from high racking.
The cabs
also had ROPS structures as fork lift trucks were prone to turning
over when manoeuvring on slight slopes outside of the
warehouse, particularly when the loaded forks were
raised above head height. Again, we were pleased and
proud to place our expertise at the disposal of
manufacturers when it became politically correct to save
lives and prevent injury.
Rollover Protective Structures for Large Crawler
Tractors and Wheeled Loaders
Soon after farm tractor rollover protection
became law, we started receiving enquiries from earthmoving vehicle
manufacturers and distributors for similar cabs for crawlers and
wheeled loaders. The move was led by insurance companies who were
insisting on similar levels of protection for drivers.
This would
prove a very difficult task as there was no standard in the U.K. or
Europe, for ROPS for heavy earthmovers, some weighing in excess of
45 tons. John Barker reached an agreement with a USA manufacturer of ROPS
cabs for Komatsu and Caterpillar earthmovers, covering a
wide range of models used in the U.K. These were built
to S.A.E. standards and satisfied our customer's needs. |
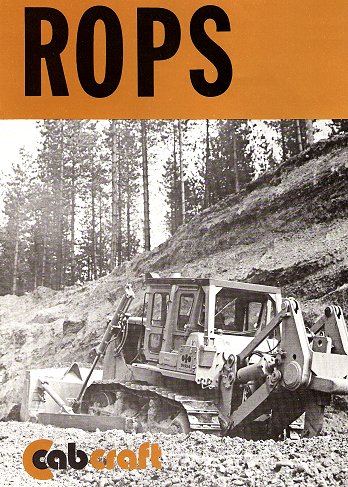 |
John and I visited the
Medford Company in Oregon and negotiated a licence agreement
covering the whole of the U.K. and Europe. We promoted the
availability of ROPS cabs for earthmovers, and with the agreement of
Mitchell Cotts, set-up production facilities in a new unit adjacent
to our Penkridge works.
The ROPS frames were made of large,
thick-walled tube and the finished product could weigh upwards of 2
tonnes. The mounting points were a critical dimension so we
developed assembly jigs to ensure each cab would exactly fit the
machine. We purchased rotating welded assembly positioners to enable
our Lloyds Class 1 certificated welders to place thick welds laid at
the correct level.
In the U.K. we started supplying ROPS cabs to
quarrying and mining groups, and soon saw examples of how our cabs
saved lives when these giant machines either overturned or had a
large boulder drop on the cab roof. We were the only European
company with this capability and were soon exporting to Germany,
Scandinavia and other northern european countries. Komatsu, the
Japanese market leader who competed head-on with Caterpillar, had
long been one of our major customers for weather protection cabs.
|
Komatsu Europe asked us to provide technical
information to their headquarters, so they could design new
earthmovers which were more compatible with our cabs. Within a year we had a contract to supply all their ROPS
cabs for fitment at their dealers premises across
Europe. Numbers were relatively small because there was
no legislation demanding these structures. As with
tractor cabs, within months, we were being asked to
provide quiet cabs, and were able to use our farm
tractor noise suppression know-how to achieve this. One
of the techniques we employed was the coating of the
internal metal surfaces with nylon flock, producing a
velvet-like surface. These particles were applied after
coating the surface with resin, and applying an
electrostatic charge to the cab. This made each 2.5mm
long nylon particle adhere at a ninety degree angle to
the surface. In addition to deadening the sound, it also
gave quite a luxurious appearance. We went on to offer
this product in all our cabs, and set-up a separate cab
flocking area in the paint shop, to avoid contamination. |
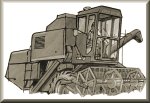 |
|
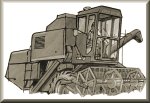 |
|
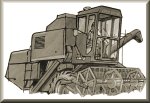 |
Return to Combine
Harvester Cabs |
|
Return to
the beginning |
|
Proceed to
Overview |
|