At the beginning of the 19th century, Darlaston's
industry consisted of many
small workshops in back yards behind people's houses,
that were ideal for small family businesses
producing tools, nails, gunlocks, and gun barrels etc.
The first large factories were the ironworks that were built after the opening of the
canal, which provided an easy way of transporting heavy
items over long distances. After the Napoleonic Wars the
gun trade collapsed and so Darlaston's skilled craftsman
began to produce other products in their small
workshops. As the century progressed, the workshops
grew into small factories employing larger numbers of
people, which was possible because of the increase in
the local population. The next step forward, the
development of larger manufacturing firms happened when
the railways arrived, and brought a new form of fast and
reliable transport to much of the country, including
shipping ports such as Liverpool. By the late part of the nineteenth
century large factories had appeared, employing large
numbers of people.
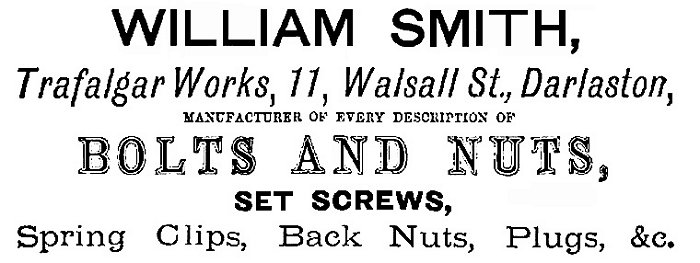
An advert from 1876.
One of the first companies in the town to have large
workshops was S & R Carter of King's Hill Works, which
was located off Birmingham Street, on a site later
occupied by Darlaston Tram Depot. |
|
|
|
|
|
Read about S & R Carter,
King's Hill Works |
 |
|
Read about the Darlaston Iron
Bridge and Roofing Company |
 |
|
|
|
|
|
|
|
Read about some of the larger
companies: |
 |
|
Charles Richards and Sons Limited |
 |
|
David Etchells &
Son Limited |
 |
|
Rubery Owen &
Company Limited |
 |
|
Guest, Keen and
Nettlefolds |
 |
|
Garringtons
Limited |
 |
|
Wilkins and
Mitchell Limited |
 |
|
The Steel Nut &
Joseph Hampton Limited |
 |
|
The
Darlaston Bolt & Nut Company |
 |
|
The Wellman Smith
Owen Engineering Corporation Limited |
 |
|
E. C. & J. Keay Limited |
 |
|
Samuel Platt
Limited |
 |
|
F. H. Lloyd and
Company Limited |
W. Martin Winn Limited
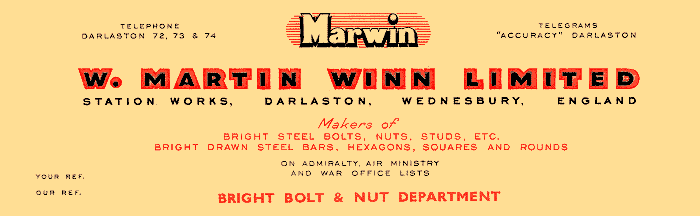
W. Martin Winn Ltd. opened their factory at Heath Road
in 1907. It was a family business that started by making
wrought iron nuts and bolts. They quickly realised the
advantages of steel and produced some of the first steel
nuts and bolts in Darlaston. The business quickly grew
and many of the company's products were produced from
bright drawn steel. Between 1920 and 1930 the cold
heading process was introduced which led to the
production of high tensile steel bolts. Heat treatment
was later introduced for the production of high tensile
carbon steel bolts, and alloy steel bolts. They also
produced extra large bolts weighing two or three
hundredweights each.
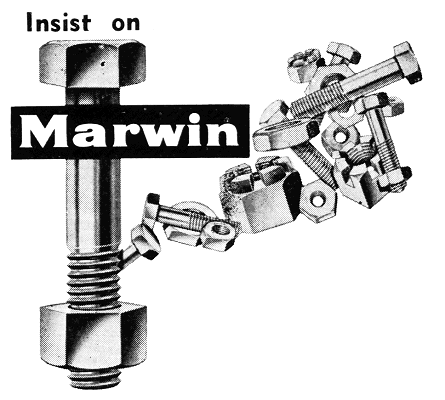 |
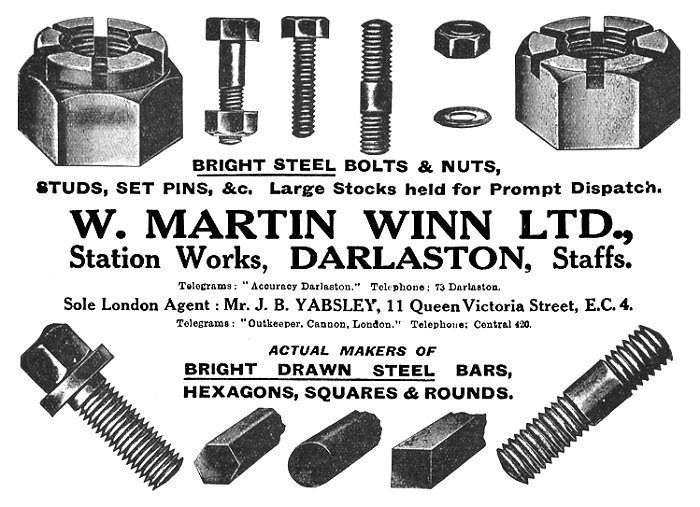
An advert from the 1920s.
The company's founder, Mr. W. Martin Winn died in 1941.
The company was then managed by Mr. W. Norris Winn, Mrs
Martin Winn, and Mr. J. E. A. Jones. In the 1950s the firm began to produce bolts and studs
that were suitable for high temperature installations.
Large numbers of them were sold to oil refineries, and
to manufacturers of steam raising equipment.
In later
years the company benefitted from the decision to
introduce a unified thread to make British and American
screws interchangeable. Large numbers of the firm's
unified nuts and bolts were produced.
The factory closed during the
recession in the 1970s, but a small tool making
business called Winn Tools remained in the original
office building until a few years ago. Winn Tools was
founded in 1964, and survived until June 2009. |
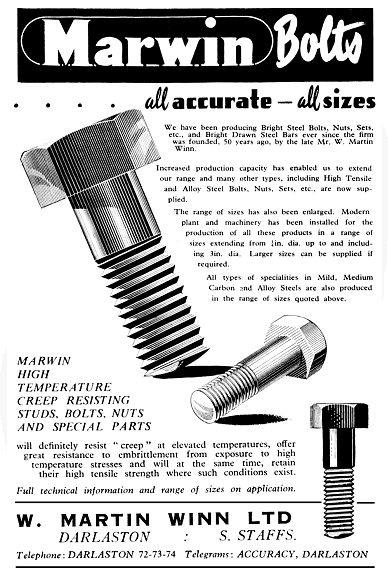
An advert from the mid 1950s. Courtesy of
Christine and John Ashmore. |
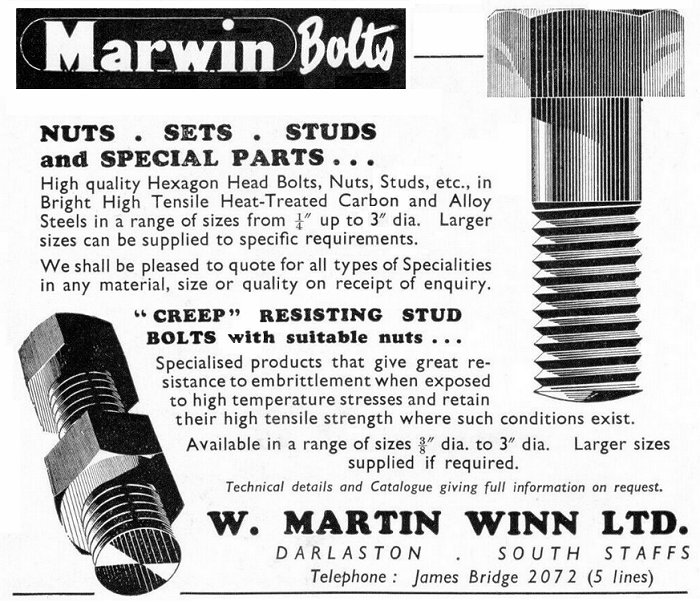
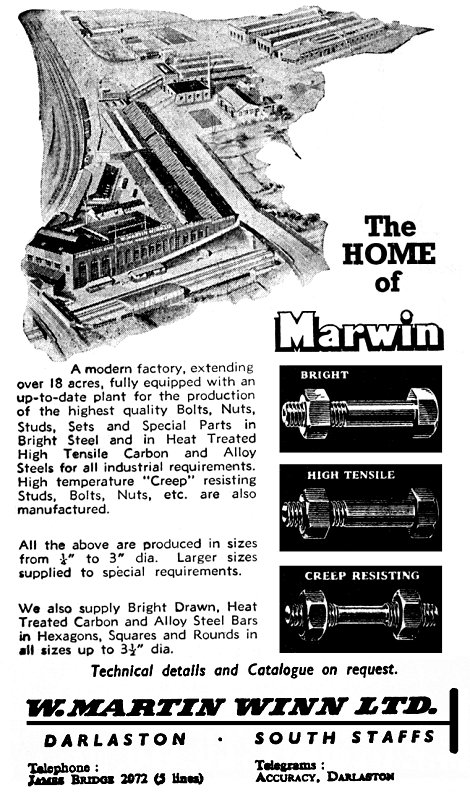
An advert from 1960.
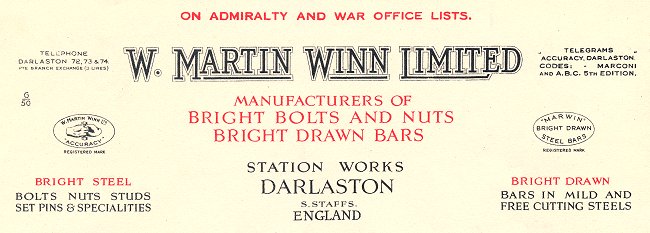
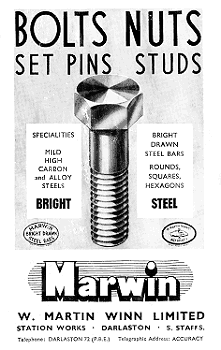
An advert from 1946. |
|
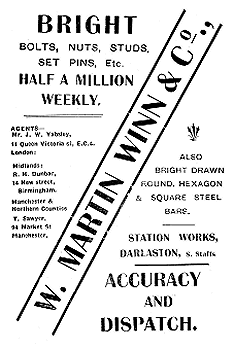
An advert from 1921. |
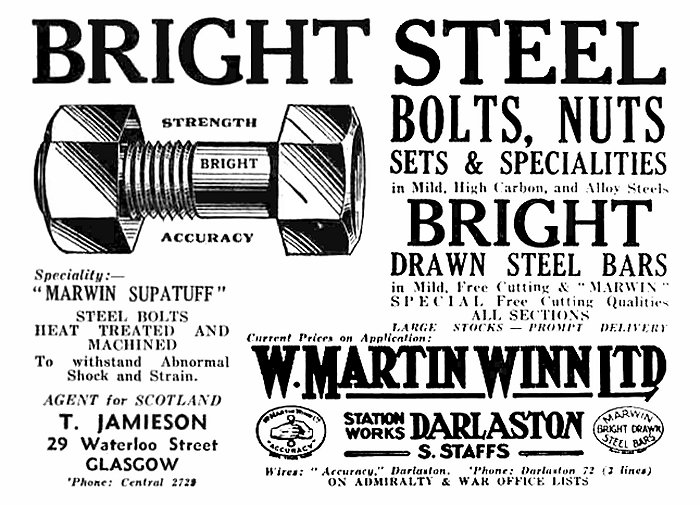
An advert from 1938.
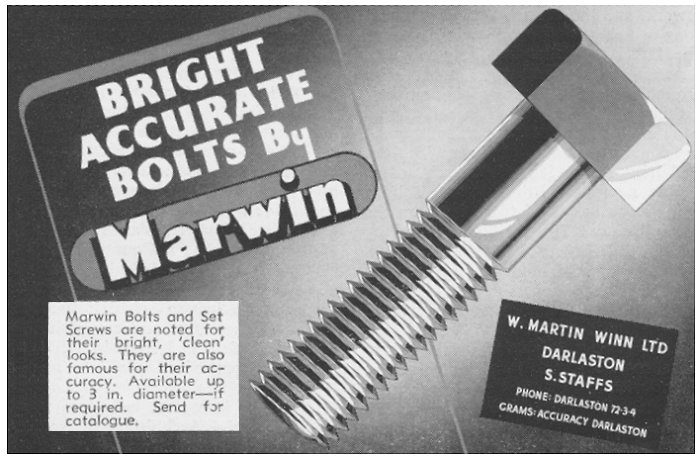
An advert from 1954.
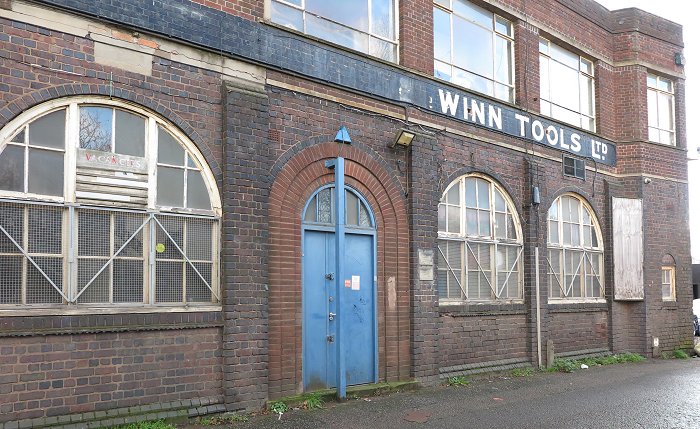
Winn Tools Limited in Kendricks Road.
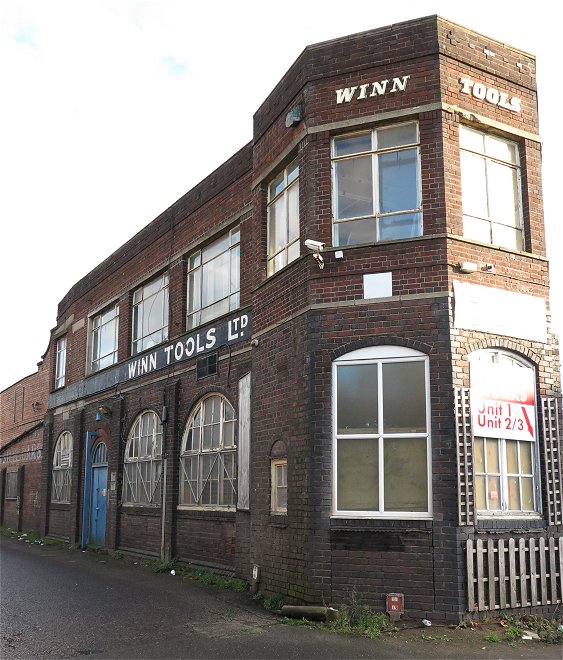
Another view of the old factory.
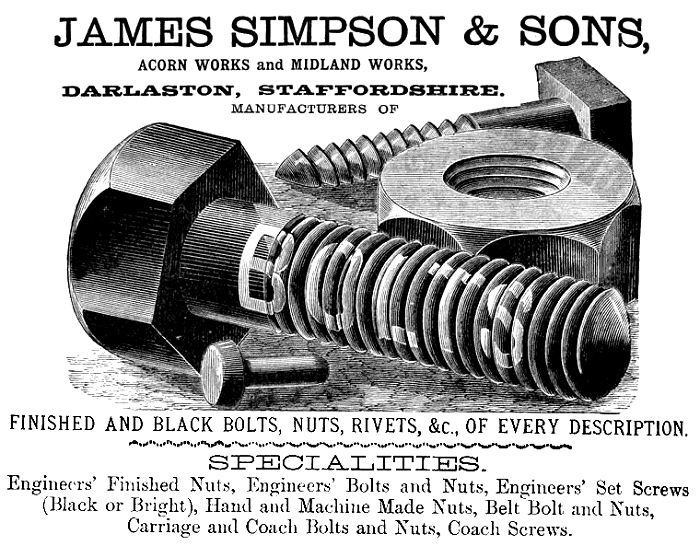
An advert from 1884. |
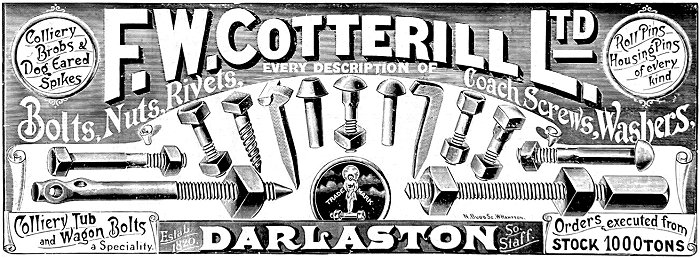
An advert from 1908.
|
|
Read about Wilkes Limited,
Grand Junction Works |
 |
|
|
Read about John Golcher
Limited of Bright Street,
King's Hill. |
 |
|
|
Read about Longmore
Brothers Limited |
 |
|
|
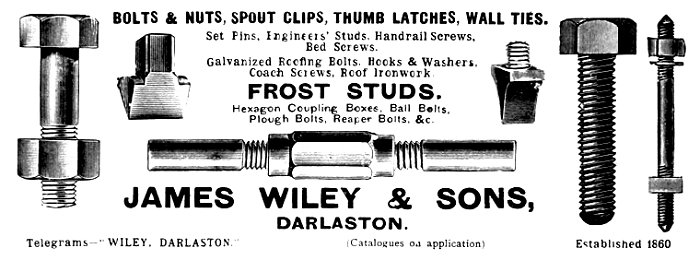
An advert from 1908.
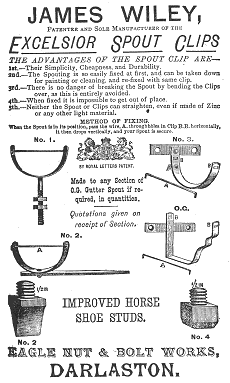
An advert from 1902 |
|
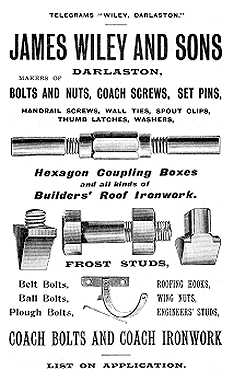
An advert from 1909. |
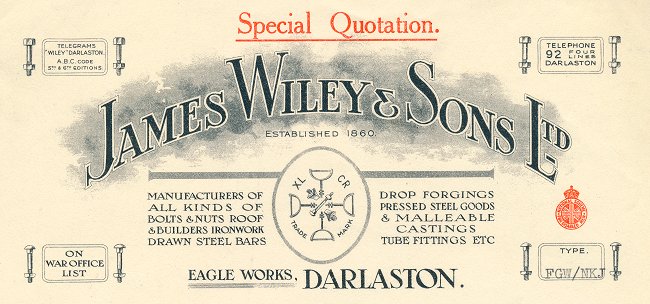
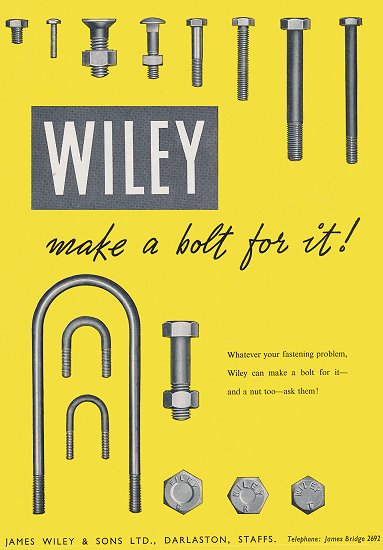
An advert from 1958. |
Wiley James & Sons Limited was established in
1860. The offices and factory were at Eagle Works,
The Green, Darlaston. The firm manufactured all
kinds of black and bright bolts & nuts, made by hand
and machine in iron or steel. Other products
included set screws, engineers' studs, coupling
boxes, builders’ roof iron work, bed screws,
handrail screws, Excelsior spout clips, horseshoe
frost studs, also Norfolk, Suffolk and other
latches.
The firm had a large export market. |
The location of Eagle Works.
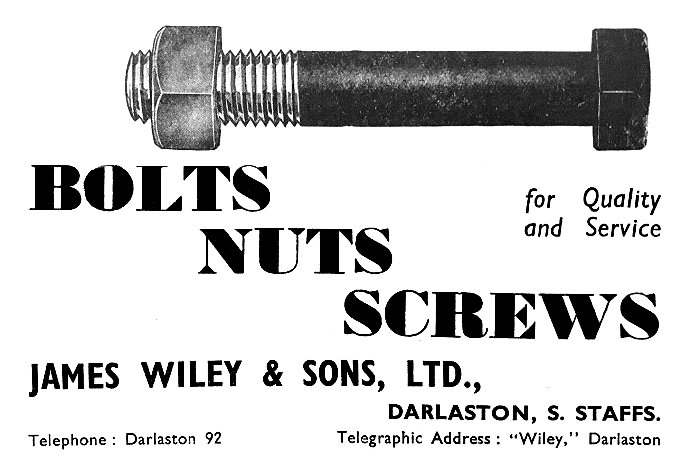
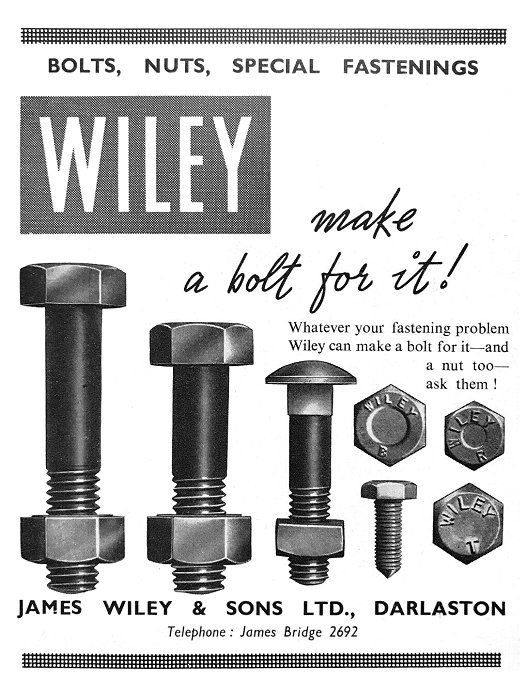
An advert from 1961.
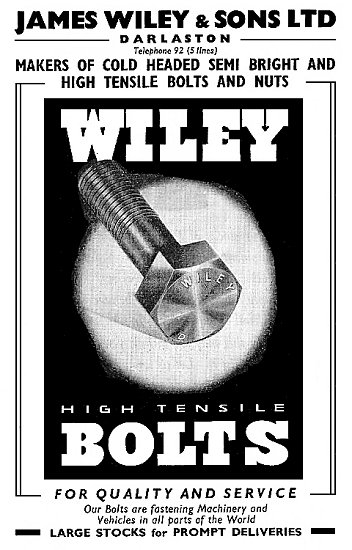
An advert from 1954. |
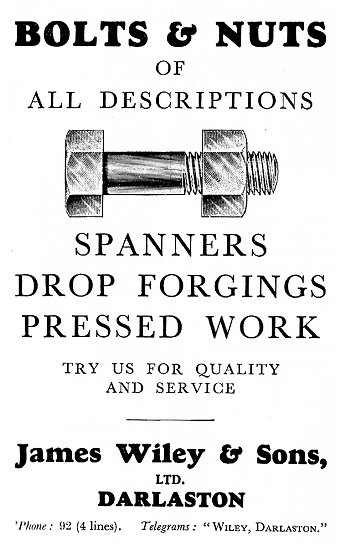
An advert from 1941. |
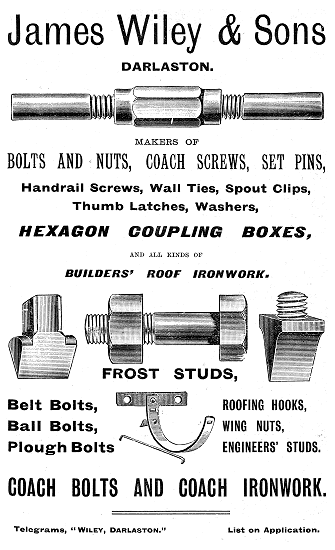 |
|
 |
Two
adverts from 1900. |
|
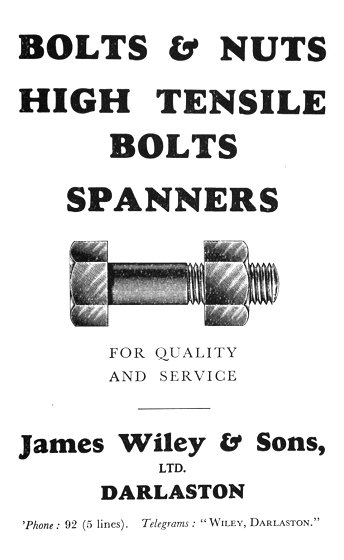
An advert from 1943. |
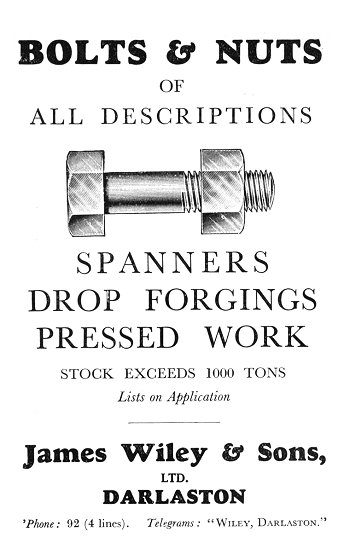
An advert from 1936. |
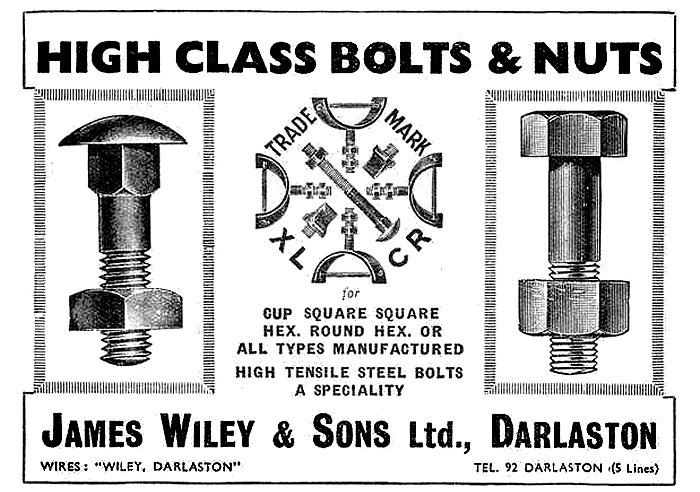
An advert from 1953.
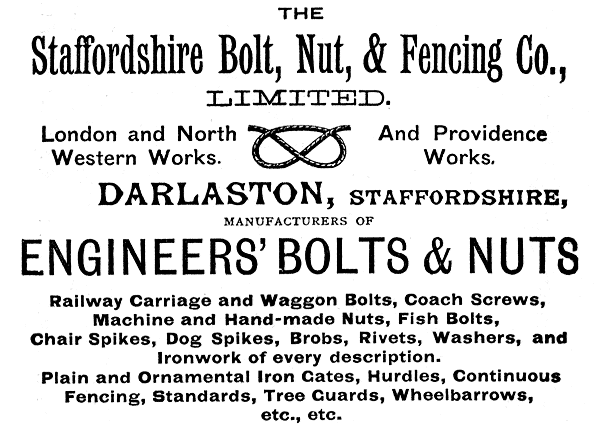
The Staffordshire Bolt, Nut, and
Fencing Company's factory, London and North Western
Works, stood near Bentley Road South, in between the
Walsall Canal and the London & North Western Railway. It
was connected to the railway by a siding which also
served the nearby canal interchange goods station. The
importance of the railway to the company can be seen
from the name given to the works. This advert is from
1884. |
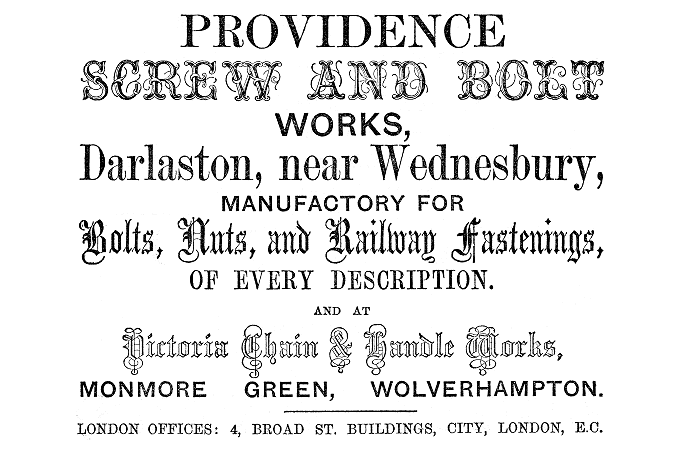
An advert from 1861.
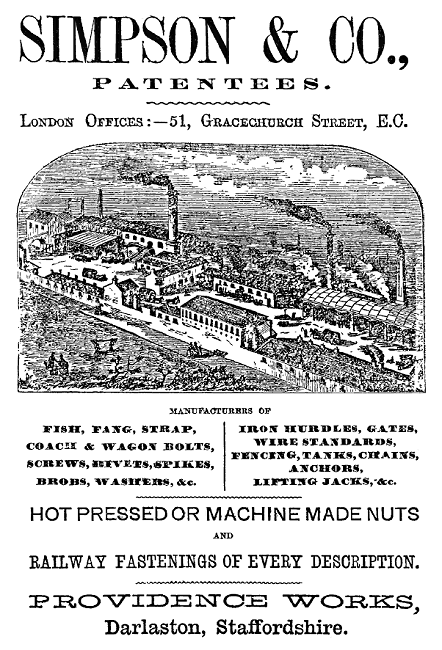
An advert from 1865. |
Providence Works at The Green was run by Simpson
& Company, and later Simeon
Archer and Thomas Harper. The firm went into
liquidation in the autumn of 1878 and was acquired
by The Staffordshire Bolt, Nut, and Fencing Company,
which had purchased Providence Works in the mid
1870s. |
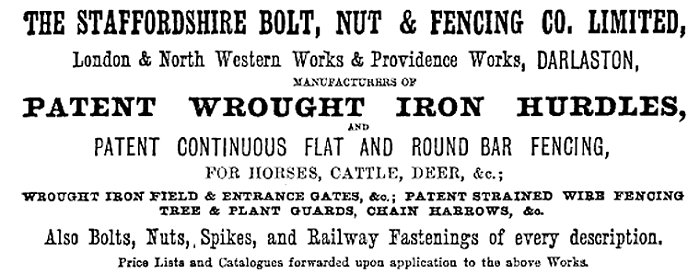
An advert from 1876. |
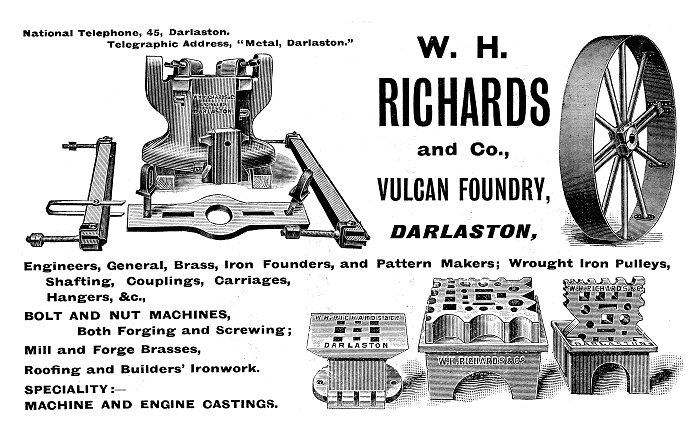
An advert from 1905. Vulcan
Foundry was at the western end of Heath Road, opposite
Charles Richards' Imperial Works. |
Partridge & Company
Sometime before 1850, Simeon Partridge, a grocer, began
to make tallow candles for sale in his shop at 28 Pinfold
Street, which he produced in a small backyard workshop. He soon opened a small factory behind Slater &
Company (solicitors) in Walsall Road, not far from the
Bull Stake. Unfortunately the building burned down in
1900 and manufacturing ceased. His son Alfred soon
opened another factory on the southern side of Heath
Road next to several old flooded mine shafts, one of
which supplied the works with water. Products included
tallow candles, yellow and carbolic soap.
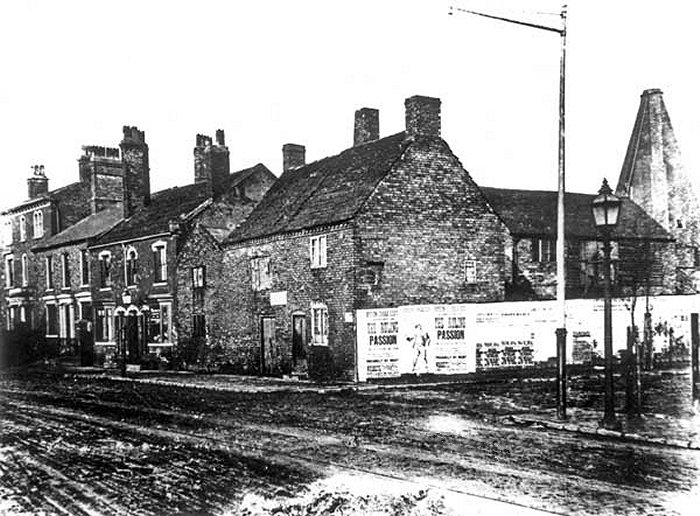
The factory on the
corner of Walsall Road and Crescent Road.
From the collection of the late Howard
Madeley. |
The candles were made by repeatedly dipping candle
wicks, suspended from a frame, into molten tallow, until
the required thickness was obtained. After each dipping
the tallow was allowed to cool. One ton of tallow made
around 25,000 candles, and in a record year in the 1930s
the company made 4,000 tons of candles of various kinds.
In 1910 Gilbert Partridge took over at the works
which were sold to ESSO Limited in 1957. Within a few
years the factory closed.
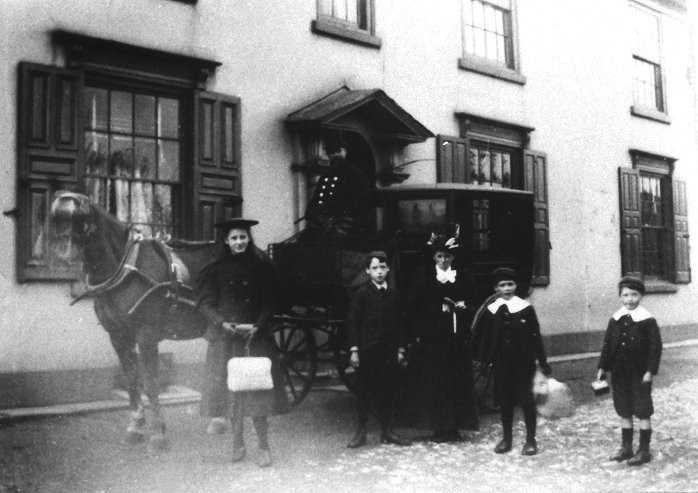
The Partridge family
outside their home, Mill House, in Dorsett
Road. From the collection of the late Howard
Madeley. |
|
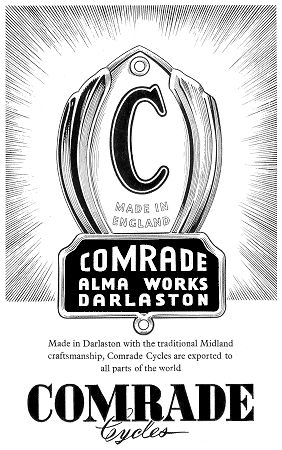
An advert from 1963. |
The Taylor family lived upstairs above the shop and
had several children. Simeon built a workshop and
started to assemble bicycles.
Sometime later Simeon purchased an old nut and bolt
factory on The Leys, in between Alma Street and Stafford
Road, in which to manufacture bicycles and tricycles.
The factory was previously occupied by David Harper &
Sons
It became a family business. Simeon's daughter
Florence, sons Jack and Richard, grandsons John and
Philip, and granddaughter Lynda also worked at the
factory.
They became well known for their high standard of
craftsmanship. Simeon died in 1960 after a long illness. By this
time half of the company's products were exported, and
many competitors had ceased to trade because of cheap
foreign competition. Comrade went on to become the
largest independent cycle manufacturer in the country.
The company was hit by the recession in the late 1970s
and 1980s, and moved to new premises near the Bull
Stake. Unfortunately it all came to an end in 1987
because of the continuing recession, and the large
number of cheap foreign imports that flooded the market.
|
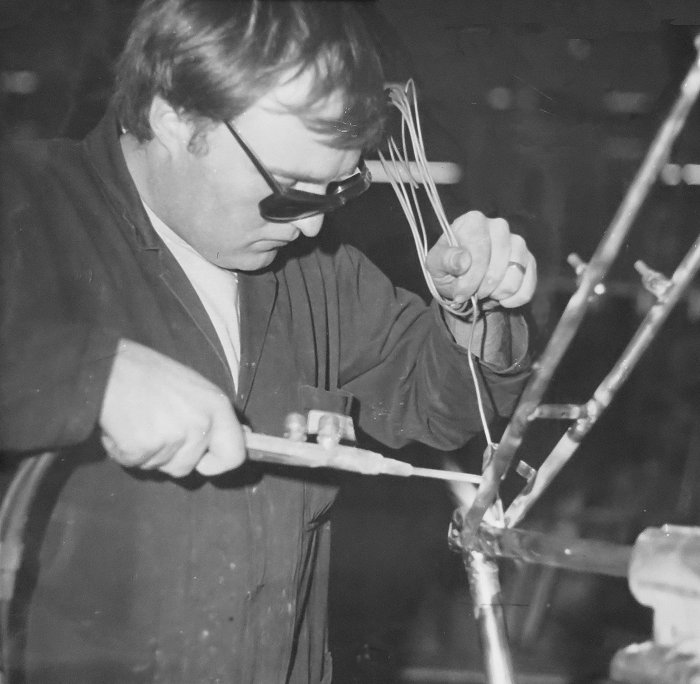
My late cousin Stephen Flavell,
brazing a frame at Comrade Cycles. He greatly
enjoyed working there. |
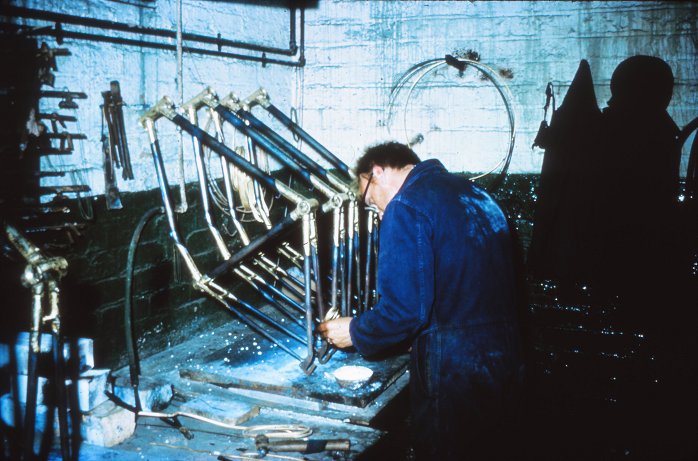
Working on Comrade cycle frames in the mid
1960s.
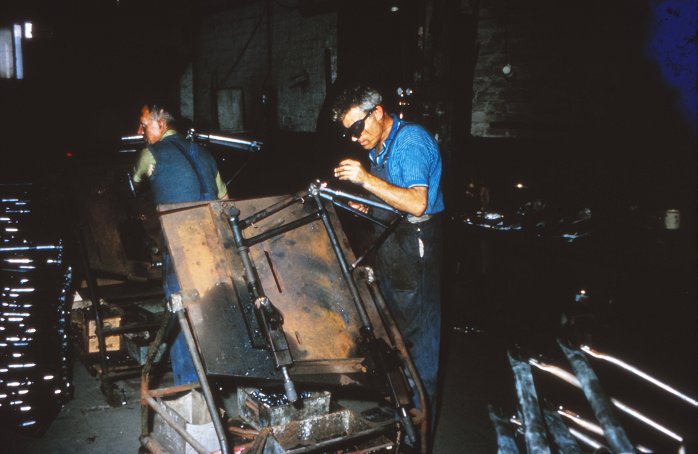
Brazing Comrade cycle frames in the mid
1960s.
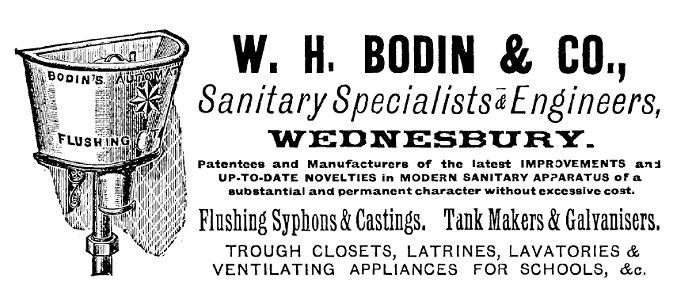
An advert from 1896.
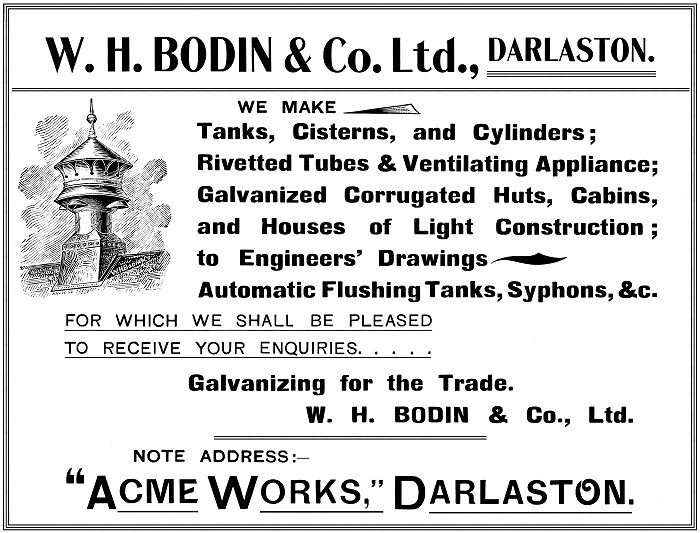
An advert from 1905.
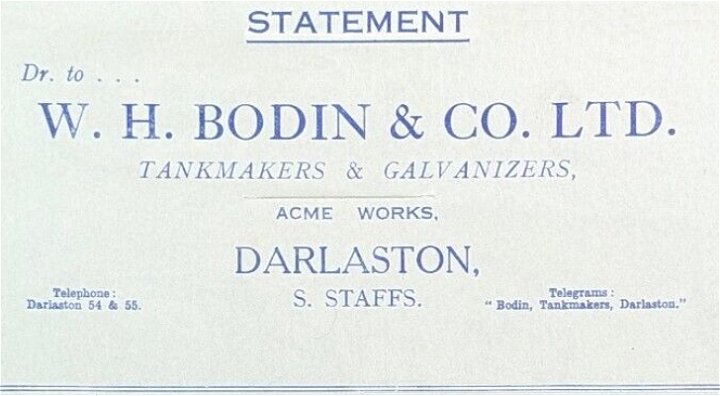
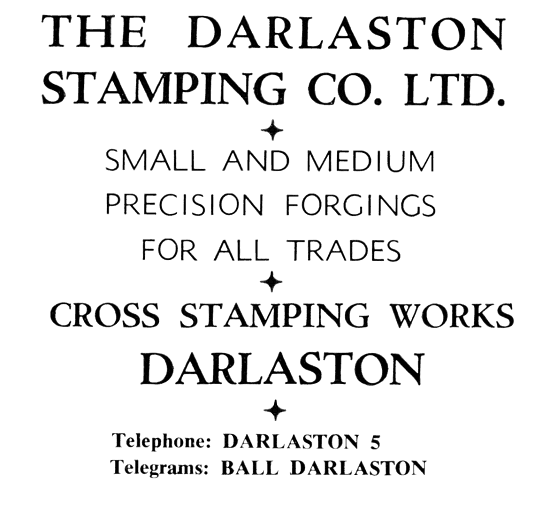
An advert from the mid 1950s. Courtesy of
Christine and John Ashmore.
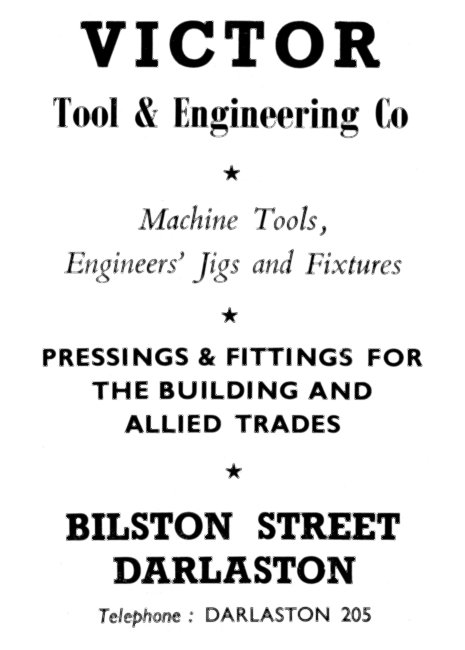
An advert from 1954.
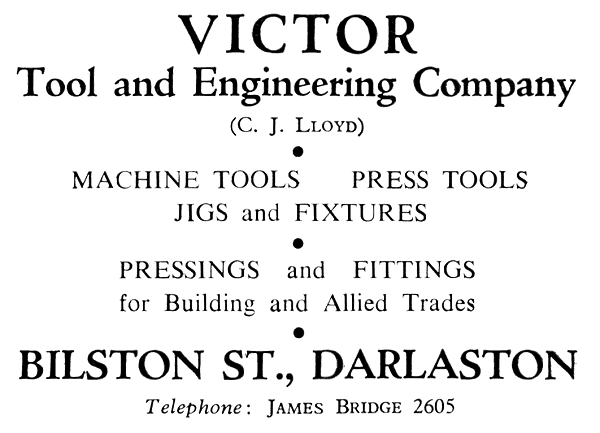
An advert from the mid 1950s. Courtesy of
Christine and John Ashmore.
|
|
Read the story of Samuel
Rubery & Son Limited, Iron and Steel merchants |
 |
|
|
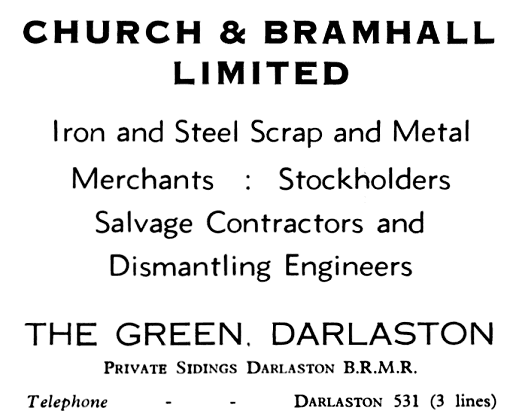
An advert from the mid 1950s. Courtesy of
Christine and John Ashmore.
 |
 |
 |
Return to Years
of Growth |
Return to
Contents |
Proceed to
Local Government |
|